When we talk about metal processing, bending is often a crucial step. Whether it’s manufacturing sheet metal components for cars, metal parts for electronic products, or casings for distribution boxes, metal bending is one of the key processes for transforming flat metal materials into the desired shapes and angles. To accomplish this, industrial metal bending machine have become indispensable tools for modern metal fabrication industry.
What is a Metal Bender?
Automated laser bending machine is a mechanical device used for processing metal sheets or tubes by bending them to create the desired shapes or angles for metal processing and manufacturing. It primarily consists of a frame, a worktable, and a clamping beam.
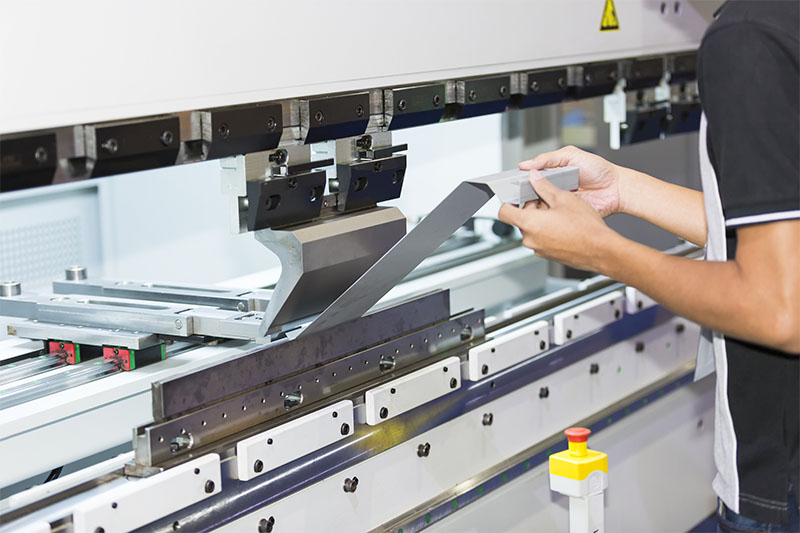
Frame: The frame of the bending machine serves as the machine’s skeleton, providing a stable foundation that supports and secures all other components. Frames are typically constructed from sturdy steel materials to ensure stability and durability.
Worktable: The worktable is a flat platform where the metal workpiece to be bent is placed. It is positioned above the frame and has sufficient strength and flatness to ensure the workpiece remains stable during the bending process.
Clamping Beam: The clamping beam is a movable component located above the worktable, and it is used to clamp the metal workpiece and apply bending force. The clamping beam usually consists of a base and a pressure plate.
Base (Die Holder): The base is the lower part of the clamping beam, often connected to the worktable. It typically features various bending dies of different shapes (also known as die holders or dies) to accommodate metal workpieces of varying shapes and sizes.
Pressure Plate (Punch): The pressure plate is the upper part of the clamping beam, connected to the base through a hinge to facilitate up-and-down movement. The pressure plate applies pressure to bend the metal workpiece, and its shape and size determine the final shape and angle of the bend.
Components of the Base:
Bearing Housing: The bearing housing is located inside the base, providing support and allowing smooth movement of the pressure plate on the hinge.
Coil: The coil is a component placed in a recess within the bearing housing and is typically used to control the operation of the bending machine. It can be an electromagnetic coil used to control the up-and-down movement of the machine.
Cover Plate: The cover plate covers the upper part of the bearing housing and coil, protecting the internal components from external environmental influences and ensuring the safe and reliable operation of the machine.
How does a Metal Bending Machine Work?
The working principle of cnc laser bending machine involves placing the metal workpiece on the worktable, then clamping it and applying pressure to achieve the bending of the metal. Different shapes and sizes of dies can be used to produce various bending shapes, making the bending machine an indispensable tool in metal processing and manufacturing.
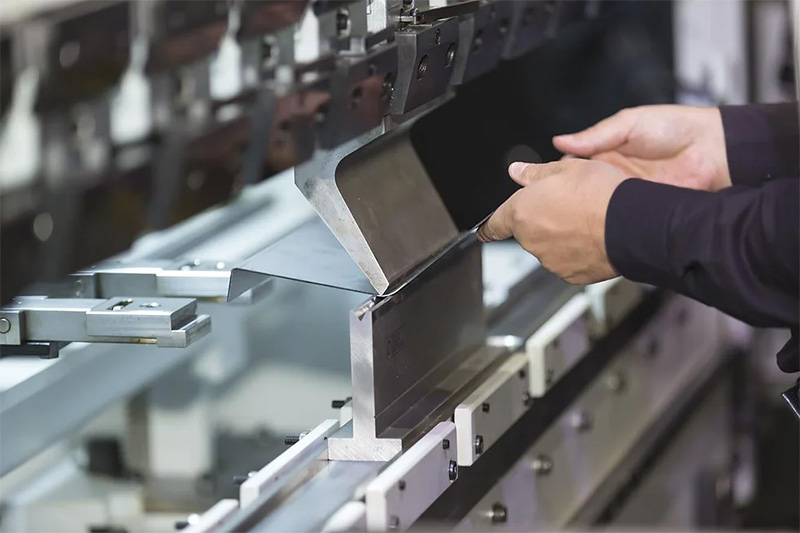
What are the Different Types of Sheet Metal Bending Machines?
CNC bending machine for metal come in several types, including electric CNC bending machines, hydraulic CNC bending machines, mechanical CNC bending machines, Oil-Electric Hybrid CNC Bending Machine, and electro hydraulic CNC bending machines.
Electric CNC Bending Machine:
This type of CNC bending machine uses an electric motor to drive the mechanical structure and controls the angle and position during the bending process through a CNC system. It is known for its high precision, fast speed, and user-friendly operation, making it suitable for precise bending of thin sheets.
Advantages: Energy-efficient, high precision, suitable for precision bending work, lower maintenance costs.
Applications: Typically used for precision-controlled bending of thin sheets.
Hydraulic CNC Bending Machine:
Hydraulic CNC bending machines use a hydraulic system as the power source and control the movement of the mechanical structure using hydraulic cylinders to achieve sheet metal bending. They offer flexibility, high force, and are suitable for processing large-sized sheets.
Advantages: Suitable for large workpieces, high bending force, high stability.
Applications: Widely used in automotive manufacturing, shipbuilding, and heavy metal processing industries.
Mechanical CNC Bending Machine:
Mechanical CNC bending machines use traditional mechanical structures for bending and control the movement of mechanical dies precisely through a CNC system. They are suitable for bending small batches of various sheet metal types.
Advantages: Simple and reliable, cost-effective.
Applications: Smaller metal processing shops and light-duty bending tasks.
Hybrid Oil-Electric Bending Machine:
A hybrid oil-electric bending machine combines both electric and hydraulic driving methods to achieve precise bending during operation. It combines the advantages of electric and hydraulic bending machines, offering speed and precision along with high force and versatility.
Advantages: Precise control, high bending force, energy-efficient.
Applications: Suitable for tasks requiring precise control and higher bending force.
Electro-Hydraulic CNC Bending Machine:
An electro-hydraulic CNC bending machine uses an electric motor to drive a hydraulic pump and precisely controls the movement of hydraulic cylinders through a CNC system for bending operations. It can accurately control angles and positions based on different bending requirements and is suitable for various sheet metal bending tasks.
Advantages: High precision, high bending force, suitable for a variety of workpieces.
Applications: Widely used in metal manufacturing, aerospace, shipbuilding, and industries requiring high precision and bending force.
Applications of Bending Machine for Tube and Sheet Forming
Laser cutting bending machine is used to manufacture various metal components and structures to meet the needs of different industries. These machines assist in processing metal materials and bending them into the desired shapes and angles, enabling complex and precise engineering and design.

Metal Products: Metal sheet and tube bending machines can bend metal sheets and tubes into various shapes and angles, allowing the production of metal components. Examples include metal enclosures, metal frames, display racks, metal fixtures, and more.
Automotive Manufacturing: In the automotive manufacturing process. By bending metal sheets into the required shapes, the car body and chassis components can be achieved. Metal tube bending machines are used to manufacture exhaust pipes, oil lines, cooling system pipes, and more.
Construction and Building Materials: Metal tube sheet bending machines are used to manufacture metal components for construction, such as metal roofs, steel structural frames, elevators, door and window frames, and more. Additionally, they can be used to produce metal pipes and fittings used in construction.
Furniture Manufacturing: Metal tube bending machines are used to produce components for furniture, such as metal frames for tables, chairs, cabinets, and other furniture pieces.
Manufacturing Equipment: Metal sheet bending machines are used in the production of components for chemical equipment, including tank bodies, pipelines, and troughs.
Pipe Manufacturing: Tube pipe bending benders are employed to manufacture various components of piping systems, including elbows, bent pipes, pipe supports, and more.
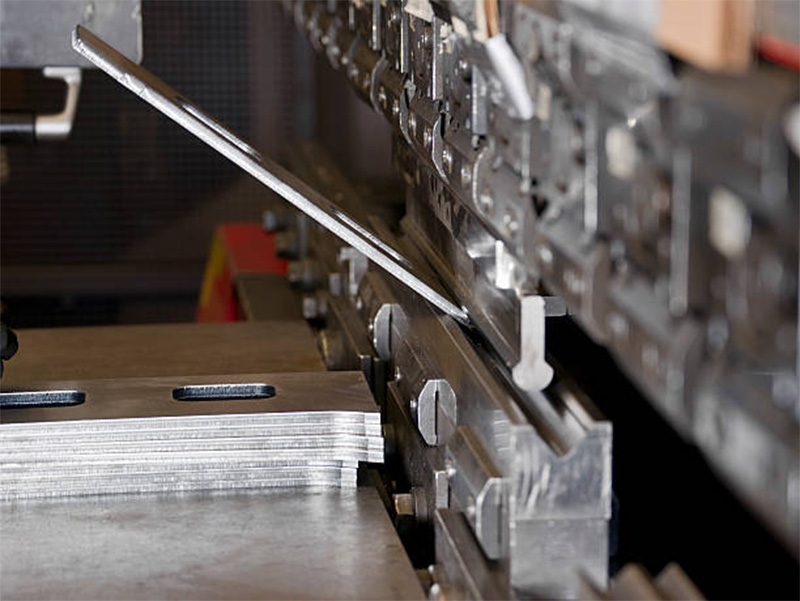
How to Use a Metal Bender?
Using a bender, whether it’s a metal sheet bender or a pipe bending machine, requires proper techniques and safety precautions.
1. First, ensure that the power supply is connected and turn on the main power switch on the control panel. Then start the oil pump, and you will hear the sound of the pump starting.
2. Perform stroke adjustment, carefully adjust the stroke settings, and conduct a test before bending. Make sure there is a thickness of one plate between the upper die and the bottom when the upper die is lowered to the bottom to avoid damaging the dies and the machine. Stroke adjustment is typically done through electric rapid adjustment.
3. Choose the appropriate bending groove, which is usually around 8 times the width of the plate thickness. For example, if you are bending a 4-millimeter-thick plate, select a groove of approximately 32.
4. Adjust the backgauge, usually with two methods: electric rapid adjustment and manual fine adjustment, similar to the operation of a shearing machine.
5. Step on the foot pedal switch to start bending. Unlike a shearing machine, the dies of a CNC bending machine can be released at any time. When the foot pedal switch is released, the machine stops descending, and pressing it again resumes the descent.
6. Strictly follow the machine tool operating procedures and wear appropriate personal protective equipment.
7. Before starting the operation, check for foreign objects on the front material support, backgauge, and slider. If any foreign objects are found, arrange and clean them to avoid safety hazards.
8. Check the alignment and stability of the upper and lower dies. Also, inspect whether all positioning devices meet the workpiece processing requirements. Before starting, ensure that the upper and lower dies are clean and free of debris in the grooves to avoid damage to the dies or affecting the accuracy of the workpiece. Carefully inspect the motor, switches, wiring, and grounding for normality and firmness before starting, making sure that all operating components and buttons are in the correct positions.
9. If the upper slide and various positioning axes are not at their original positions, execute the home position program.
10. After starting the equipment, run it empty for 1-2 minutes, allowing the upper slide to travel 2-3 times at full stroke. If you notice any unusual sounds or malfunctions, stop immediately, troubleshoot, and then continue working.
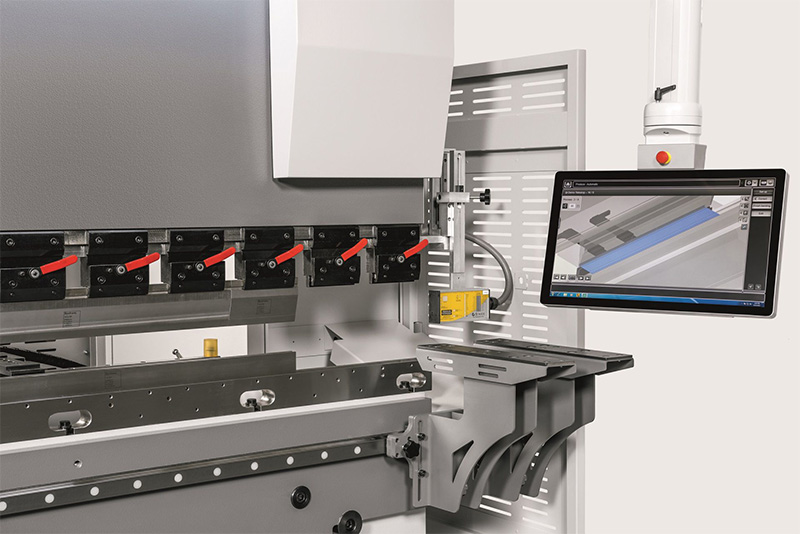
What are the Features of DPLASER Sheet Metal Bending?
DPLASER possesses extensive experience and professional knowledge to assist you in selecting the type of CNC press brake bending machine that suits your production and budget.
Robust Structural Design: Our metal bending tools are manufactured with heavy-duty cast iron frames, ensuring the stability and durability of the tools. The cast iron frame provides a solid foundation, enabling our bending machines to perform precise and uniform bending operations on various metal materials.
Bending Precision: Our metal bending tools exhibit exceptional bending precision, catering to a wide range of complex sheet metal bending requirements. Whether for small components or large assemblies, our bending machines help ensure the accuracy of the final products, meet customer demands, and enhance work efficiency.

Features:
1. Fast speed, high efficiency, and low energy consumption.
2. Batch processing of workpieces with high product consistency.
3. Simple daily maintenance with low maintenance costs.
4. High level of automation, user-friendly operation, and minimal requirements for manual labor and specialized skills.
5. Ability to shape complex forms in a single operation, including both upward and downward bends, non-right angle bends, arcs, and polygonal bends.
6. Supports various loading and unloading methods, including manual loading, gantry robots, and mechanical arms.
7. High scalability, allowing the addition of mechanical arms for loading and connection to fully automated production lines.
8. Closed-loop control system with dual servo motors ensures coordination error within ±0.02mm.
If you are interested in laser cutting bending fabrication, please contact us. We can provide you with further information and offer a free sample testing service. Regardless of the industry you are in, we can provide you with suitable metal bending solutions.