Precision micro laser drilling offers advantages such as extremely high peak energy, exceptional precision, and minimal thermal impact. Its processing capabilities include etching, cutting, drilling, engraving, and photolithography for integrated circuits. This technology is widely used in advanced manufacturing applications, including silicon wafer dicing, precision drilling of ceramics, and glass cutting.
Laser micro cutting has become a cornerstone of precision manufacturing, enabling highly accurate and intricate processing at the micron scale. As the demand for miniaturized components grows, a deep understanding of ultrafast laser micro-cutting and its strengths is essential for selecting the optimal solution for high-end applications.
How Does a Laser Micro Cutting Machine Works?
Laser micro cutting uses a highly focused laser beam as a processing tool to perform precision cutting and drilling at the micro- and even nano size. Due to its high energy density, excellent beam directionality, and monochromatic nature, the laser can rapidly convert light energy into thermal, mechanical, or chemical energy within an extremely short time. This enables precise material removal, modification, or deposition.
The exceptional accuracy of micro- and nanofabrication is made possible by advanced positioning and focusing technologies. High-precision mechanical systems and optical components allow the laser beam to be tightly focused to micrometer or nanometer dimensions, enabling ultra-fine machining of small material areas. Additionally, when combined with state-of-the-art scanning systems and image processing technologies, laser micro cutting machines can produce complex patterns and intricate 3D structures with outstanding precision.

Application of Laser Micro-Cutting
Compared to continuous wave and long-pulse laser systems, ultrashort pulse lasers offer a key advantage: their extremely short pulse durations result in virtually no thermal impact on the material being processed. Laser micro-cutting is ideal for applications requiring high-precision features, typically on materials less than 2 mm thick, where tight tolerances are critical.
Wafer Dicing
In semiconductor manufacturing, precise wafer dicing is essential. Traditional methods such as diamond blade cutting or plasma dicing often suffer from limited accuracy, higher costs, or the generation of hazardous byproducts. In contrast, laser cutting offers superior precision, efficiency, lower operational costs, and a clean, non-contact process—making it an ideal solution for chip-level wafer dicing.
Ultraviolet (UV) picosecond laser cutting, in particular, focuses a high-energy beam onto the wafer surface, achieving cutting precision as fine as 2.5μm. This significantly enhances chip quality and production yield.
Thin Film Removal
During chip fabrication, specific material layers must be precisely removed to enable subsequent processing. Laser micro- and nanofabrication techniques allow for highly accurate, non-destructive thin film removal, providing a superior alternative to conventional methods.
For instance, in flexible electronics manufacturing, metal films often need to be selectively peeled off. Traditional removal techniques can damage the material or compromise surface quality. Laser processing, however, can cleanly remove metal films without harming the underlying substrate, preserving both device performance and manufacturing accuracy.
Chip Cutting
Before packaging, individual chips must be separated from the wafer. Laser cutting enables ultra-fine dicing of materials such as silicon (Si), gallium arsenide (GaAs), and silicon carbide (SiC), with benefits including non-contact operation, high-speed processing, and independence from material hardness. This makes laser micro-cutting especially suitable for handling ultra-thin chips and hard materials in advanced semiconductor applications.
Cover Glass Cutting
In consumer electronics such as smartphones, tablets, and wearable devices, cover glass (e.g., Gorilla Glass or sapphire glass) requires high-precision cutting. Laser micro-cutting enables smooth, burr-free, and crack-free processing, significantly improving the appearance and durability of end products. It also supports complex shapes and ultra-thin glass, offering flexible solutions for advanced design requirements.
FPC/PCB Cutting and Drilling
In the flexible electronics industry, flexible printed circuit boards (FPCs) demand precise contour cutting and micro-hole drilling. Traditional mechanical methods often lead to burrs or material deformation. Laser micro-cutting, by contrast, offers high-precision, non-contact cutting with minimal thermal impact, and supports intricate, arbitrary shapes without damaging delicate materials.
Micro-Casting of Alloys
Laser micro-cutting is especially suitable for processing micro-components, precision parts, and high-performance materials. In fields such as precision engineering and biomedical devices, alloy micro-casting demands extremely tight dimensional control and material integrity—standards often beyond the reach of conventional machining. With its non-contact nature, exceptional accuracy, and low thermal impact, laser micro-cutting enables fine trimming, intricate shaping, and the creation of complex microstructures, ensuring the quality and performance of micro-cast alloy parts.
Precision Micro-Hole Drilling
Industries such as semiconductors, medical devices, and fluidic systems require micro-holes with strict control over diameter, geometry, and spatial distribution. Mechanical drilling and chemical etching often fall short in precision or cause material damage. Laser micro-cutting technology allows for micron- to submicron-scale drilling in a wide range of materials—including metals, ceramics, and glass—while maintaining hole uniformity and smoothness. Applications include inkjet printheads, implantable medical devices, and microfluidic chips, where high-precision micro-holes enhance device functionality and reliability.
Electrode Structure Fabrication
In the electronics and energy sectors, laser micro-cutting is widely used in the fabrication of precision electrode structures, such as fuel cell electrodes, lithium battery current collectors, and microelectrodes for semiconductor devices. Compared to traditional methods like chemical etching or mechanical machining, laser micro-cutting enables high-precision processing on ultra-thin metal foils, composite materials, and conductive films without causing material damage. This enhances conductivity and preserves structural integrity.
For example, in the production of flexible electronic devices, laser micro-cutting can create high-precision, multilayer microelectrode structures that significantly improve device performance and stability.
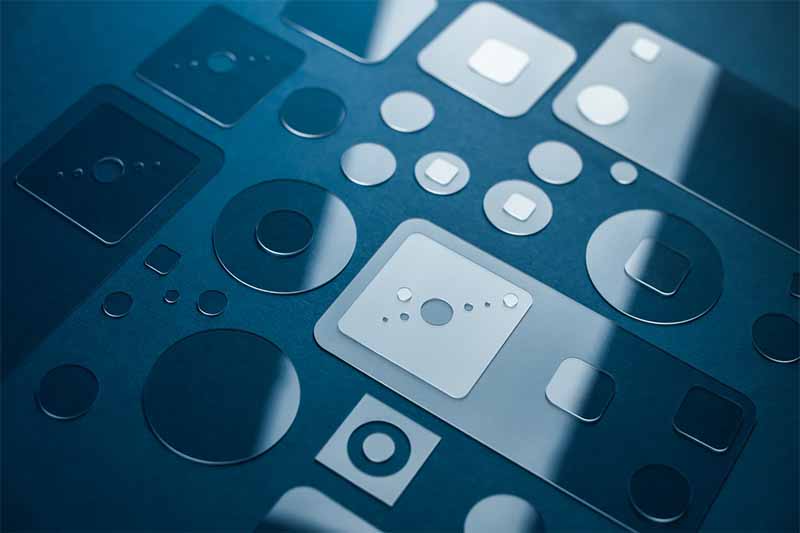
Advantages of Laser Micro Drilling
Laser micro-drilling is a non-traditional drilling technique that uses a focused laser beam to precisely target specific surface areas. By converting optical energy into thermal energy, it enables the removal of material and the formation of microstructures such as pits, grooves, and holes. Ultrafast pulses laser—typically in the femtosecond or picosecond range—can create holes with diameters between 20~500 µm, depending on the specific process parameters. This highly adaptable, multifunctional, and reliable microfabrication method is widely used across industries.
High Precision
Laser micro-drilling enables the fabrication of micro- and submicron-scale holes with exceptional accuracy. It ensures consistent hole diameters and clean edges, meeting the stringent requirements of industries such as semiconductors, electronics, and medical devices. Tiny holes can be arranged in complex patterns without burrs or debris, minimizing the risk of clogging and ensuring top-tier precision.
Non-Contact Processing
As a non-contact method, laser drilling exerts no mechanical stress on the workpiece and avoids deformation. This is especially advantageous for delicate materials like thin films, brittle substrates, and high-precision components, making it ideal for sensitive micro-hole applications.
High Speed and Efficiency
With extremely short pulse durations, laser micro-drilling achieves rapid material removal while maintaining accuracy. This makes it well-suited for high-throughput manufacturing and large-scale industrial production.
Wide Material Compatibility
Laser micro-drilling is compatible with a broad range of materials, including metals (such as stainless steel and titanium alloys), ceramics, glass, polymers, and composite materials. It delivers consistently high accuracy across all substrates.
Capability for Complex Structures
Laser micro-drilling can handle irregular surfaces, thin layers, and miniature components with ease. Whether the requirement is for standard or non-standard hole geometries, the process delivers precise results, fulfilling the needs of advanced and customized fabrication processes.
Minimal Heat-Affected Zone
Particularly with ultrafast lasers (femtosecond or picosecond), energy is highly localized, resulting in negligible thermal diffusion. This minimizes heat-affected zones, effectively avoiding thermal damage, melting, or micro-cracks. The result is consistently high-quality, reliable micro-holes.
Machining | Laser Processing | |
Processing Efficiency | Good | Perfect |
Quality | Good | Perfect |
Degree Of Precision | Poor | Perfect |
Processing Materials (low-temperature plastics, glass, ceramics, etc.) | Poor | Perfect |
Post-Processing | Poor | Good |
Consistency (No Abrasion) | Poor | Perfect |
Environmentally Friendly | Poor | Good |
Initial Costs | Perfect | Poor |

Applications of Laser Drilling Micro Holes
1. Glass Wafer Drilling
Glass wafers are widely used in semiconductor packaging, MEMS (Micro-Electro-Mechanical Systems), and optoelectronic devices. Traditional mechanical drilling often causes microcracks and edge chipping. Laser micro-drilling offers a non-contact, high-precision solution that eliminates microcracks, making it ideal for processing ultra-thin and large-diameter glass wafers efficiently and reliably.
2. Precision Glass Drilling
In industries such as consumer electronics, optics, and medical devices, glass drilling requires extremely high accuracy. Laser micro-drilling can create micron-scale holes in optical glass, quartz glass, and microfluidic chip substrates—delivering stress-free, crack-free results and improving product durability and quality.
3. Sapphire Drilling
Sapphire is known for its extreme hardness and high optical transparency, making it a popular material for LED substrates, smart device cover lenses, and optical windows. However, its hardness makes conventional drilling difficult and damaging. Ultrafast lasers (picosecond or femtosecond) enable high-quality micro-holes in sapphire, free from cracks or molten debris.
4. Silicon Drilling
Silicon is essential in semiconductors, photovoltaics, and MEMS sensors. Laser micro-drilling is well-suited for processing silicon wafers, through-silicon vias (TSVs), and microfluidic channels. It offers high speed, precision, and minimal thermal impact, particularly for ultra-thin silicon substrates.
5. Ceramic Drilling
Ceramics are valued for their high temperature resistance, corrosion resistance, and excellent electrical insulation. They are widely used in electronic packaging, aerospace, and medical devices. Laser micro-drilling enables precise micro-hole formation in ceramics such as alumina (Al₂O₃), silicon nitride (Si₃N₄), and silicon carbide (SiC), avoiding common mechanical issues like cracking and edge chipping.
6. Metal Drilling
There is a growing demand for micron-scale holes in metals used in precision manufacturing and medical implants. Laser micro-drilling can precisely drill stainless steel, titanium alloys, aluminum alloys, and superalloys, offering non-contact, burr-free processing with excellent dimensional control.
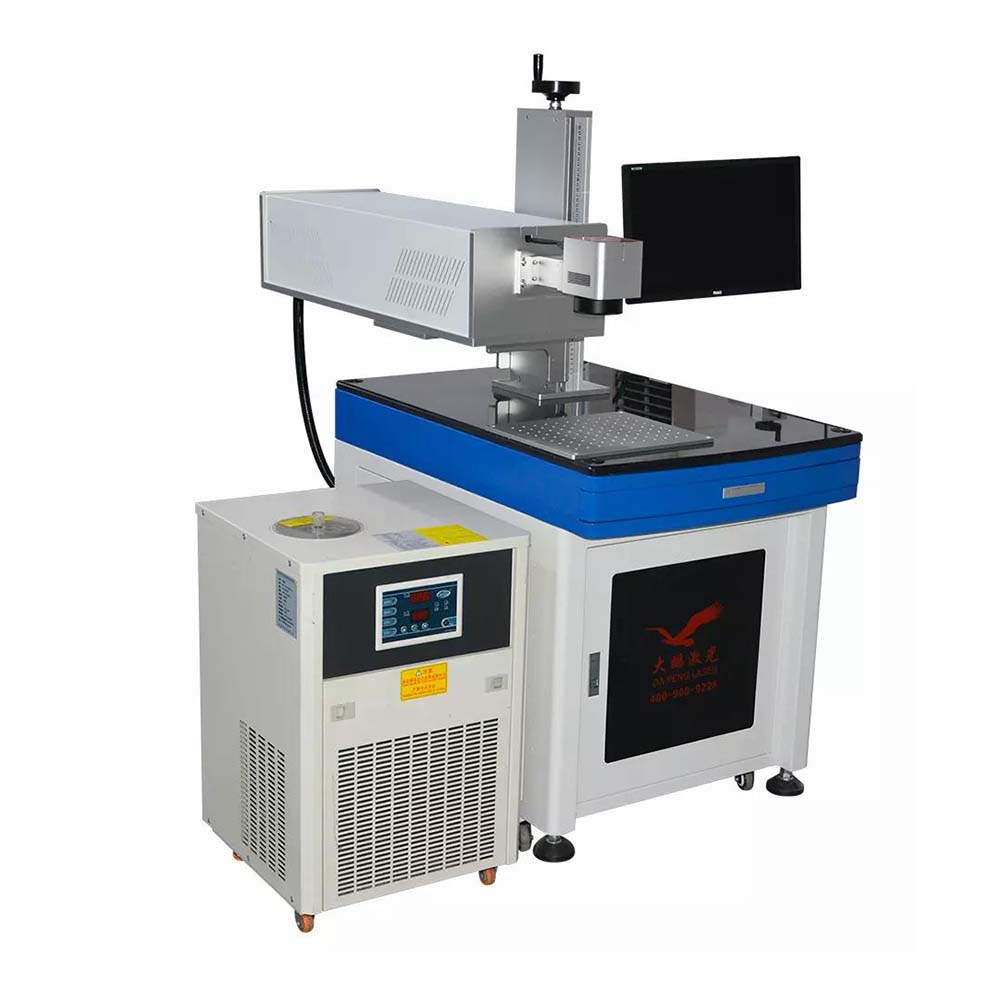
Why Choose Our Laser Micro Cutting and Drilling Machine?
Our laser micro cutting machine delivers micron-level tolerance and intricate features without causing thermal damage or material distortion. It is designed to handle everything from ultra-thin films to materials several millimeters thick—cutting thousands of holes quickly, consistently, and with high repeatability.
Depending on the material, we tailor the laser source for optimal results:
For transparent films or glass, UV laser sources provide superior precision and edge quality.
For metals or ceramics, infrared fiber lasers are ideal due to their high energy absorption and processing efficiency.
Whether you’re working with delicate substrates or high-strength materials, our ultrafast laser micro cutting system ensures clean, burr-free, and high-precision results—making it the perfect choice for manufacturing applications across electronics, medical devices, semiconductors, and new energy manufacturing.