Laser welding, with its advantages of high-speed welding, low deformation, and beautiful weld seams, demonstrates immense potential in sheet metal manufacturing. Many customers in welding workshops have opted for flexible robot arms equipped with laser welding systems to automate welding tasks. Especially in high-volume, highly repetitive welding scenarios, CNC robot welding machine can significantly enhance production efficiency and welding consistency.
Laser welding robots are transforming modern manufacturing by improving efficiency, precision, and productivity. These robotic welding systems combine laser welding technology with automation to deliver fast, consistent, and high-quality welds. In this article, we’ll explore how laser welding robotic boost production 2025.
Robotic welding machines are generally classified into two main categories: arc welding robots and laser welding robots. Arc welding robots primarily rely on an electric arc as the heat source while using shielding gas to prevent oxygen and water vapor in the air from affecting the weld seam during the process. They are suitable for thick plate welding and structural component manufacturing. In contrast, laser welding robots utilize high-energy laser beams to achieve higher precision and a smaller heat-affected zone, making them ideal for applications in the mechanical and precision manufacturing industries.
How Robotic Welding Machines Work?
A laser automated welding machine consists of a laser generator, beam transmission system, robot body, and control system. The laser beam is focused on the workpiece, rapidly melting the material to form a weld seam. The robot precisely controls the laser position and movement path to ensure welding stability. Meanwhile, the control system dynamically adjusts laser power and welding speed in real-time to optimize welding quality.
Sensing Systems
Robotic welding machines may be equipped with various sensors, such as seam tracking sensors, vision systems, and torque sensors. These sensors monitor welding conditions, workpiece position, and orientation in real time, enabling automatic correction and adaptive welding.
Human-Machine Interface (HMI)
Through a touchscreen or other visual operation panels, operators can set and monitor welding programs, view real-time data, adjust parameters, and receive fault alerts.

Advantages of Laser Welding Robots
High-Precision Positioning for Consistent Welding
Equipped with precise positioning and motion control capabilities, laser welding robots achieve micron-level welding accuracy, minimizing deviations and ensuring superior product quality and consistency. This makes them ideal for high-precision industries such as automotive component manufacturing.
Superior Welding Quality with No Need for Secondary Processing
Laser welding produces smooth, aesthetically pleasing welds with a stable and consistent process. This reduces welding defects and eliminates the need for extensive post-weld grinding, enhancing both product reliability and appearance.
High Automation, Minimal Human Intervention
With simple programming, the robot can execute welding tasks autonomously, enabling continuous operation with minimal manual input. This reduces labor intensity, eliminates human errors, and significantly boosts production efficiency.
Intelligent Monitoring for Precise Parameter Adjustments
Advanced monitoring systems detect welding conditions in real time, automatically optimizing parameters such as laser power and speed. This ensures consistently high welding quality and enhances production reliability.
Ultra-Fast Welding Speeds for Shorter Production Cycles
Laser welding enables rapid mass production, accelerating manufacturing processes and allowing businesses to respond quickly to market demands while shortening delivery times.
Multi-Station Collaboration for Increased Efficiency
With optimized programming and layout, a single robot can manage multiple welding stations simultaneously. This parallel welding capability is especially valuable in large-scale machinery manufacturing, significantly improving production efficiency.
Reduced Labor Costs
By replacing manual welding tasks, robotic welding minimizes reliance on skilled welders, reducing labor costs and mitigating workforce shortages, ultimately helping businesses lower expenses and improve profitability.
High Flexibility for Diverse Production Needs
The robotic welding system supports quick task switching, adapting to various product specifications and welding requirements. This provides manufacturers with a more flexible and scalable production solution.

Collaborative Robot Welding: Empowering Smart Manufacturing
Lightweight & Flexible for Complex Production
Weighing only 18kg, the collaborative robot is easy to transport by a single person to any location in the welding workshop. With no complicated installation required, it can be deployed immediately. Its lightweight design allows for flexible integration into complex production environments, adapting seamlessly to diverse welding needs.
User-Friendly Operation & Exceptional Welding Precision
The robot supports drag-and-teach programming and graphical programming interfaces, eliminating the need for specialized coding skills. With a repeatability accuracy of ±0.02mm, it is equipped with a vision positioning system and motion trajectory optimization algorithm, increasing welding speed by over 30% while maintaining a product yield rate of 99.5% or higher.
Open Platform for Deep Customization
To accommodate customers’ secondary development needs, the collaborative robot features a highly open platform, supporting extensive communication interfaces, SDK development, and ROS system compatibility. This enables seamless upper-level communication control, allowing businesses to optimize welding workflows and achieve intelligent production management.
Smart Manufacturing Solution Driving Welding Automation
With its lightweight design, ease of use, precise welding capabilities, flexible deployment, and proprietary core technology, the collaborative robot is an industry leader in transitioning from manual to automated welding. It helps enterprises enhance production efficiency and achieve smart manufacturing upgrades. For example, in new energy vehicle battery module welding, Dapeng Laser’s solution can complete continuous welding of 20 electrode groups in a single process, reducing cycle time by 40%.
Laser Welding Advantages & Wide Industry Applications
Dapeng Laser’s automated welding robot integrates a laser source, wobble welding head, galvanometer system, and control system, featuring high-level in-house development. It supports weld seam tracking, external axis collaboration, and PLC interactive control, meeting the demands of high-precision, complex trajectory welding. This solution is widely used in industries such as machinery and hardware, 3C electronics, and new energy, making it an ideal choice for automated welding.

Customer Real Case: Laser Welding Solution for Stainless Steel Enclosures
In traditional welding processes, stainless steel enclosures often require post-weld grinding and polishing. This not only complicates the workflow and increases processing time but also poses risks such as welding deformation or burn-through. To improve welding quality and streamline production, our customer implemented a cobot laser welding. This solution significantly enhanced weld seam uniformity and fullness, reducing the need for secondary processing and dramatically shortening post-weld finishing time.
With high repeatability accuracy, stable operation, efficiency, flexibility, and ease of use, the collaborative robot has proven to be highly effective for welding box-shaped components. Today, this laser welding solution is in full-scale production at the customer’s facility, successfully reducing manufacturing costs and significantly boosting overall production efficiency.

The robot welding machine price varies based on several key factors, including functionality, automation level, and brand.
Factors Affecting the Price of Welding Machine Robotic
Welding Technology & Features – Basic arc welding robots are generally more affordable, while high-precision laser welding robots with advanced features, such as real-time seam tracking and AI-powered optimization, tend to be more expensive.
Payload Capacity & Reach – Larger robots with higher payload capacities and extended reach are priced higher due to their ability to handle bigger and more complex welding tasks.
Degree of Automation & Integration – Standalone robotic welders cost less than fully integrated automated welding systems that include sensors, external axes, and AI-driven monitoring tools.
Brand & Support Services – Well-established brands with proven reliability and comprehensive after-sales support often command higher prices compared to lesser-known manufacturers.
New vs. Used Machines – New robotic welders come with the latest technology and warranties, while used or refurbished models offer a more budget-friendly alternative with some trade-offs in performance and lifespan.
Ready to enhance your production efficiency with state-of-the-art laser welding solutions? The price of laser welding robots varies significantly due to multiple factors, making it difficult to provide a fixed cost upfront. To ensure the best solution for your production needs, we offer customized robotic welding systems tailored to your specific requirements. Contact us with your project details, and our team will provide you with a personalized system design and pricing plan to optimize your manufacturing process.
DP Laser is a leading manufacturer of laser welding robots, redefining the future of automated welding with cutting-edge technology and intelligent solutions. By seamlessly integrating laser precision with robotic flexibility, we empower industries to push the boundaries of efficiency, accuracy, and scalability. From automotive, metal fabrication, electronics part to new energy, our innovative welding systems are transforming production lines, helping businesses stay ahead in an era of manufacturing.
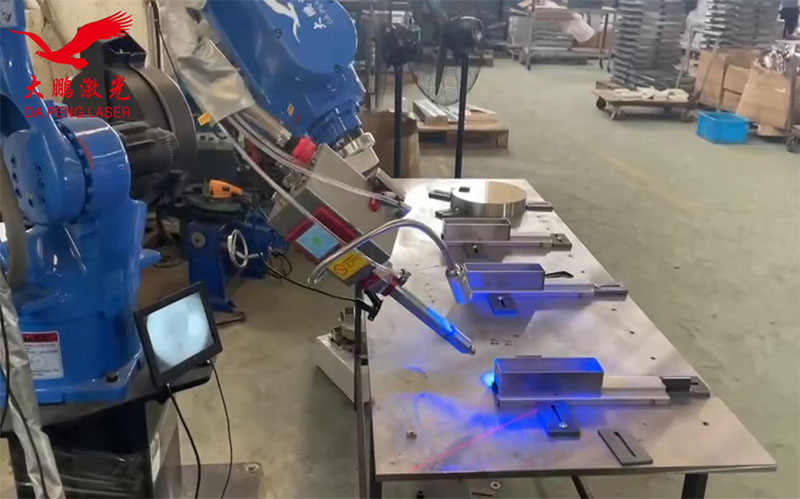
How Robot Laser Welding Machines Help Production 2025?
In 2025, robotic laser welding will continue to drive industrial upgrades with its intelligence, precision, and efficiency. It will help businesses enhance productivity, reduce costs, and ensure product quality while supporting the shift toward smart manufacturing.
1. Increased Production Efficiency & Shorter Manufacturing Cycles
With high-speed welding capabilities, robotic laser welding significantly reduces processing time. Industries such as automotive manufacturing and sheet metal processing will benefit from shorter production cycles and increased overall factory capacity.
2. Superior Welding Quality & Lower Rework Costs
With precise laser control, robots achieve micron-level welding accuracy, minimizing weld defects and reducing rework or scrap rates. This results in optimized production costs and improved product reliability.
3. Reduced Dependence on Skilled Labor & Higher Automation
As smart manufacturing evolves in 2025, robotic welding will replace traditional manual welding, reducing reliance on skilled welders. Through automated production line integration, it enables unmanned operations, ensuring continuous workflow and higher efficiency.
4. Adaptability to Complex Welding Needs & Enhanced Flexible Manufacturing
With intelligent programming and AI-powered trajectory optimization, robots can handle various materials, shapes, and sizes, making them ideal for customized and small-batch production. This flexibility enhances businesses’ ability to respond to market demands more effectively.
In the Industry 4.0 era, smart manufacturing is not just a technological upgrade but a revolution in production models. As a key component of intelligent factories, robotic welding machine is redefining the manufacturing value chain.