In the manufacturing industry, metal fiber laser cutting machines have become crucial tools for improving production efficiency and quality. How to choose a laser cutter has become a key challenge for manufacturers. This article will take you through this process, covering considerations from material adaptability to cutting dimensions, providing you with wise purchasing advice to help your manufacturing business stand out in the competition.
There are several points to consider when buying a fiber laser cutting machine:
- First, consider factors such as cutting width, machine power, materials that can be cut, and repeat positioning accuracy. These depend on the production requirements and the type of material being processed.
- Second, focus on the quality of the samples when purchasing, assessing the accuracy and smoothness of the cut section by examining the cut out sample. This helps to ensure that the chosen machine will meet quality standards and production requirements.
- Finally, the brand and price of the metal laser cutting machine need to be analyzed in depth. Different brands of machines may have different performance, durability and quality of after-sales service. While understanding the brand reputation, it is also important to consider the budget to ensure that you get the best value for money.
- Choosing a reliable industrial laser cutting machine manufacturer is quite important, laser cutting machine belongs to the new laser technology equipment, the acquisition of a machine put into use is the need to consider the long term, choose a large scale, experienced brand, the quality of the product and equipment is more guaranteed, and the strength of the manufacturer can provide efficient and timely after-sales service and perfect product training.
What to Consider When Purchasing a Laser Cutter?
What Materials Do You Need To Cut?
When choosing a fiber laser cutting machine, the primary consideration is the material to be cut. Fiber laser cutting machines can cut various types of metals, including carbon steel, stainless steel, galvanized sheet, aluminum, titanium, copper, and brass, among others. Non-metallic materials should be processed using a CO2 laser cutting machine.
What is the size of your workpiece?
The larger the working area of the laser cutting machine, the larger the size of the workpiece it can accommodate. This is crucial for applications that require processing large-sized materials. Factors such as the size, structure, and material of the worktable affect the cutting results. Note that with an increase in the size of the worktable, the size and price of the cutting machine will also correspondingly increase.
Cutting Thickness
The power of the cutting machine limits the depth of cut, so you need to choose the right model, tool, etc. according to the actual needs. As the thickness of the material increases, a more powerful machine is needed, and accordingly, the price of the machine will increase.
Cutting Accuracy
Cutting accuracy is a key consideration, which determines the error in the size of the parts cut out. The cutting accuracy of the laser cutting machine mainly depends on the quality of the laser source, the stability of the optical system, the stability of the table, the CNC system and other components and parameter configuration. According to the actual needs and cost considerations, choose the appropriate model of cutting machine. Roc laser has a variety of models of fiber laser cutting machine, different cutting machine models corresponding to different configurations, customers can match the machine model according to the processing accuracy requirements.

Control System
The control system is directly related to the operability and stability of the CNC laser cutting machine. Mainstream control system brands such as CypCut, Lantek, etc., when choosing the need to consider the ease of use, functionality and compatibility with other equipment.
Higher Power Provides Greater Flexibility
The choice of laser power is based on the needs of the material and content to be cut. Different power levels are required for different materials and processes. For example, cutting acrylic and plastics, glass may not require excessive power, while cutting metal materials may require a laser power of at least 1000W. Thicker materials typically require higher power levels to ensure effective perforation and cutting. The most popular choices today are in the 6-12KW range, and the higher KW used does not necessarily mean greater thickness cutting capability, but rather higher linear cutting speeds. DP Laser can provide high power industrial laser cutting machines from 20kw~30kw.
The cutting parameters of the metal laser cutting machine can be found on this page, however, due to space constraints we have not been able to present all material and machine parameters. If you do not find the information you need on this page, please feel free to contact us and we will provide you with more detailed parameter information. We are committed to providing you with comprehensive and accurate cutting machine parameters and data.
Optical Components
To improve the cutting accuracy and effectiveness of a laser cutting head, it is necessary to consider factors such as wavelength, semi-reflective mirrors, fully reflective mirrors, refractive mirrors, etc., and to select high-quality optics suitable for the laser cutter. The combination of these key considerations ensures that the selected laser cutter meets real-world needs and delivers superior performance.
Lens Focal Length
Depth of cutting and speed: The choice of lens focal length directly affects the laser’s focal position on the surface of the workpiece. The right focal length ensures that the laser produces enough energy inside the workpiece to increase the depth of cut. However, a focal length that is too long or too short may result in insufficient energy or over focusing, affecting the cutting effect.
Cutting quality: Proper selection of the focal length improves the quality of the cut and avoids problems of excessive melting, burning or non-smooth cutting edges. By adjusting the focal length, the distribution of laser energy on the workpiece can be optimized to achieve a more precise and smooth cutting effect. The quality of the cut is directly related to the appearance and performance of the final product and is therefore another key factor in focal length selection. When cutting materials of different thicknesses, the laser lenses can be replaced with different focal lengths accordingly.
Safety Protection Devices
Be sure that the cutting machine you purchase is equipped with the necessary safety protection devices, such as safety guards and emergency stops. These devices are essential for maintaining staff safety. In addition, consider optional auxiliary production systems such as automatic loading and unloading systems and robots to improve productivity.

Cutting Type of CNC Laser Cutting System
Sheet Metal Laser Cutter has cutting classifications such as vaporization, melting, and oxidation. The choice of cutting method usually depends on the material and thickness of the workpiece, as well as the processing requirements. Different cutting methods have some differences in terms of accuracy, speed, and applicability. Different cutting methods can be selected based on different materials.
1. Laser vaporization cutting.
The use of high-energy, high-density laser beam to heat the workpiece, increase the temperature, so that the material in a short period of time vaporized into water vapor. Since the heat of vaporization is generally greater for materials, a high-power laser beam is required. Laser vaporization cutting is generally used for very thin metallic and non-metallic materials.
2. Laser melting cutting.
The material is heated to a certain temperature so that it melts, and then a non-oxidizing gas is blown through a nozzle coaxial to the beam, using the pressure of the gas to expel the liquid metal and form a kerf. The energy required is only 1/10th that of vapor cutting, and it is not necessary to vaporize the metal completely. Materials generally suitable for laser fusion cutting include stainless steel, titanium, aluminum and its alloys, which are not easily oxidized materials or active metals.
3. Laser Oxygen Cutting.
The laser is used as a preheating heat source, and oxygen and other active gases are used as cutting auxiliary gases. After the gas is ejected, an oxidizing reaction occurs with the metal, releasing a large amount of oxidizing heat and forming a cut. Materials generally suitable for laser oxygen cutting include carbon steel, titanium steel, heat-treated steel and other easily oxidized metal materials.
Reliability and quality of service
Before purchasing a laser cutting machine, in addition to the type of cutting, you should also pay attention to the manufacturer’s after-sales service. Experienced cutter manufacturers usually provide a perfect after-sales service system, it is recommended to visit the factory before purchase to ensure that the selected cutter can meet the actual needs. Customers from all over the world are welcome to come to the Roc Laser factory to learn and guide, we are ready to provide you with services.
On-site installation and training
Whether you have never invested in a fiber laser cutting system or are a seasoned professional, on-site installation and training will be completed by our experienced team of professionals. We will help you install and learn how to operate your new machine free of charge.

How to Choose a Fiber Laser Metal Cutting Machine?
Choosing the right fiber laser metal cutting machine involves considering multiple factors that encompass the characteristics of different machine models. The decision should be driven by a careful evaluation of your specific production applications and industry requirements.
1. Metal Plate Fiber Laser Cutting Machine
Specialized in cutting metal sheets, widely used in metal processing industry, such as metal structural parts, kitchen utensils, electrical shells, construction materials, etc.
- Power and Speed: Choose the appropriate power and cutting speed according to your production needs. High-power laser cutters are suitable for fast cutting of thick plates, while low-power models are suitable for thin plates.
- Table size: Consider the size of the plate you need to cut and make sure the table size of the machine meets your production requirements.
- Automation: Automatic loading and unloading and automatic seam tracking can increase productivity, especially for high volume production.
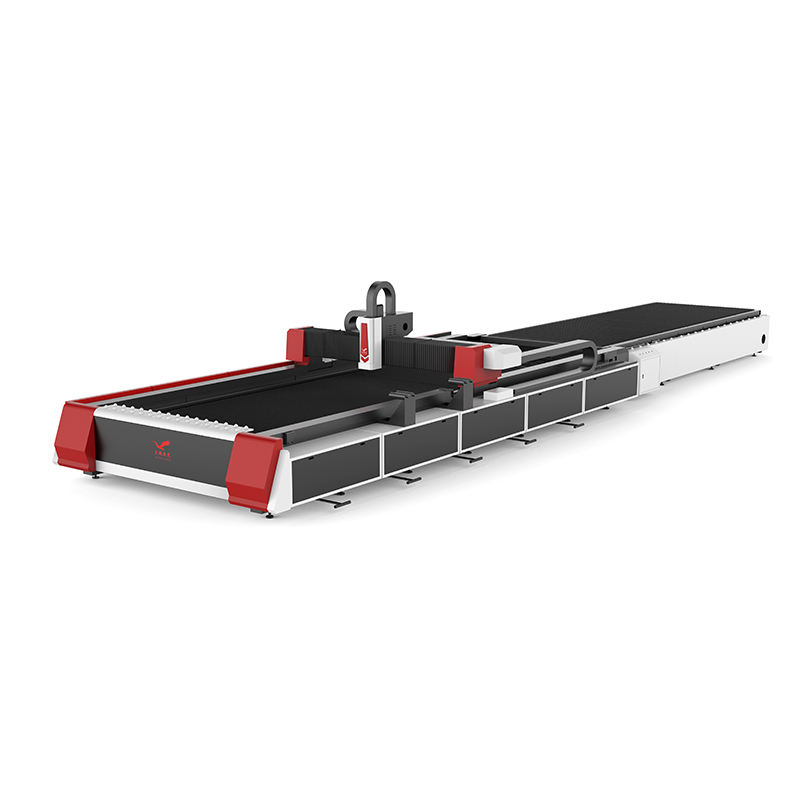
2. Fiber Laser Cutting Machine for Metal Pipes
Designed for cutting metal pipes, suitable for pipe manufacturing, furniture manufacturing and other fields.
- Pipe Diameter Range: Ensure that the machine is suitable for the range of pipe diameters you need to cut. Some models may specialize in small diameter tubes, while others are suitable for large diameter tubes.
- Cutting Length: Consider the length of the pipe you need to cut and make sure the machine is able to accommodate the size of your production.
- Multi-functional cutting: Some advanced laser tube cutters have multi-axis cutting capabilities that allow for a variety of angles and shapes, increasing cutting flexibility.
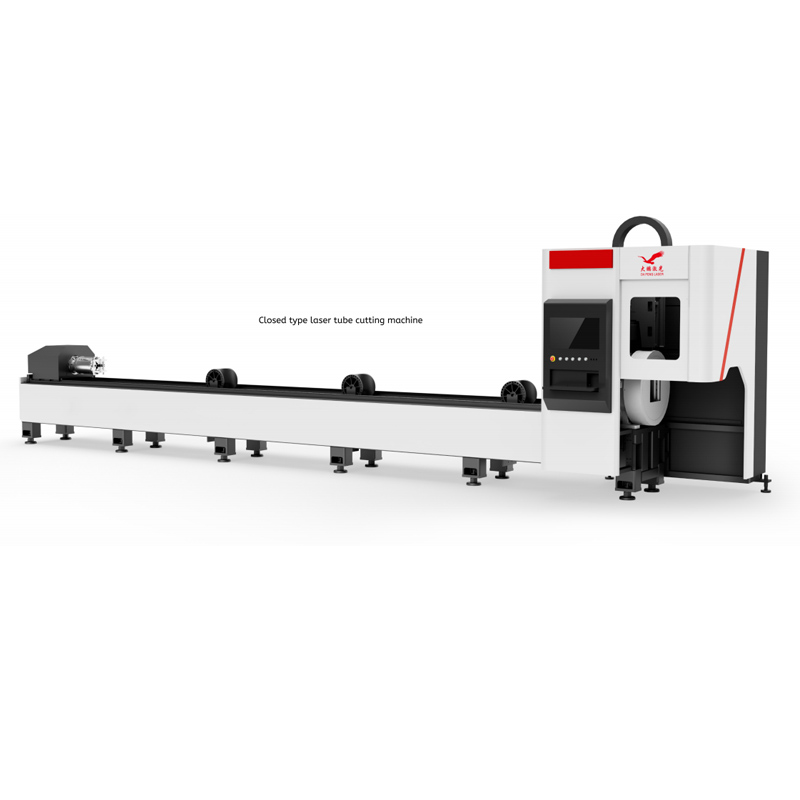
3. Metal Sheet and Tube Laser Cutting Machine
Combining sheet and tube cutting functions provides versatility for application scenarios where different types of materials need to be processed at the same time.
- Versatility: This all-in-one model is able to handle both sheet metal and pipe cutting needs, making it suitable for companies that need to diversify their production.
- Productivity: By integrating sheet and tube cutting functions, the machine reduces equipment switching and floor space, thus increasing productivity.

4. Automatic Loading and Unloading Fiber Laser Cutting Machine
Equipped with an automated loading and unloading system, the machine improves productivity and is suitable for mass production and continuous processing.
- All-in-one design: Consider whether you need one machine to accomplish both sheet and tube cutting tasks. An integrated design reduces the footprint of the machine and improves overall productivity.
- Cutting Quality: Ensure that the under feeder maintains high quality cutting edges when cutting sheet and tube to avoid secondary processing costs.
- Software Support: Choose a machine with a user-friendly software interface and advanced control system for easier program settings and adjustments.
5. Automatic Coil Fed Laser Cutting Machine
For the cutting needs of coiled materials, the machine can automatically roll up the materials and cut them efficiently for the coil processing industry.
- Integrated Coil Leveling: The coil leveling system that flattens and levels the metal coil before it undergoes laser cutting. This ensures that the material is uniformly flat and free from distortions.
- Diameter and weight of the coilsmaterial: According to your production needs, select the appropriate diameter and weight range of the rolled material to ensure that the machine can work continuously and stably.
- Automatic feeding system: This model is usually equipped with an automatic feeding system, which allows for a continuous supply of rolls and reduces downtime during production.
- Material Savings: Automatic winding systems allow for more efficient use of material, reducing scrap rates and providing advantages for cost control and sustainable production.

6. Fiber Laser Exchange Platform
With the function of switching working platforms, it can be flexibly switched in different working environments to improve production flexibility.
- Quick table change: Reduces downtime between cutting tasks and improves production efficiency.
- Adaptation to different materials: Considering whether or not you need to work with a wide range of metals, this model’s quick-change system makes cutting different materials more flexible.
- Automation: Fiber laser exchange platforms often feature intelligent automation systems that streamline operations and improve production stability and consistency.
We are committed to providing you with professional after-sales service to ensure that you receive timely support during the use of your machine. We have a professional service team composed of excellent engineers and sales staff who can help you choose the fiber laser cutting machine that best suits your needs. If you have any questions or need further information, feel free to communicate with us, we will be happy to serve you.

Conclusion:
We explored essential factors in selecting the appropriate CNC Fiber Laser Cutting Machine, emphasizing material adaptability, cutting dimensions, precision, and other configurations tailored to processing needs. In the highly competitive manufacturing landscape, the strategic acquisition of a suitable fiber laser metal cutting machine stands as a pivotal measure for ensuring business success. This article serves as a guide, addressing the query “what should I consider in a laser cutting machine,” to assist you in identifying the most fitting partner from the diverse range of laser cutting machine models available.