Bevel laser cutting is a specialized laser cutting technique designed to create angled edges on materials, enhancing both the versatility and precision of traditional laser cutting. This process allows for the production of complex shapes and beveled surfaces, making it highly suitable for industries such as automotive, aerospace, and metal manufacturing. In this guide, we’ll explore the unique advantages of bevel laser cutting, its applications across industries, and how bevel tube laser cutting machine achieve precise beveling. Discover why bevel laser cutting is increasingly popular in industrial processing applications.
What is Bevel Laser Cutting?
Laser cutting bevel is a specialized laser cutting technique used to create angled or beveled edges on materials, typically at angles like 15, 30, or 45 degrees. Unlike standard vertical cuts, bevel cuts are designed to add an angled edge, where parts often need to fit together with specific angles for welding, assembly, or fabrication.
In industries such as shipbuilding, construction machinery, and oil pipelines, bevel cutting for thick steel plates is an essential part of the manufacturing process. To ensure the strength and reliability of welded structures, specific geometrical bevels often need to be processed on components awaiting welding. Custom bevels, such as U-shaped, Y-shaped, W-shaped, X-shaped, and V-shaped, are designed to enhance subsequent processes like welding and assembly, meeting the diverse demands of various industries. Traditional bevel cutting methods include machining, flame cutting, and plasma cutting, each of which has its drawbacks—machining is slow and heavily reliant on manual labor.
Can You Cut Bevels On a Laser Cutter?
Laser cutters, known for their high precision and efficiency, are widely used for processing various sheets and tubes. They demonstrate excellent performance, especially in standard right-angle cuts.
However, when it comes to bevel cutting applications, several variables must be considered, such as cutting angle, tilt, and angle accuracy. These factors are crucial for achieving high-quality cutting results and directly impact the performance and durability of the final welded components.

How to Laser Achieve Bevel Cutting?
- 3D Laser Cutting Head: When performing bevel cuts, the laser cutting head needs to be rotated to a specific angle to achieve precise tilting of the cutting surface. Supported by a CNC control system, the angle of the cutting head can be accurately adjusted to flexibly meet diverse cutting requirements.
- Bevel Laser Cutting Control System: Specialized bevel cutting software provides precise cutting paths and angle control, automatically optimizing cutting parameters based on the material and bevel type. This ensures high-precision bevel cutting results.
- Intelligent Chuck System: The tube chuck system is used to securely hold and rotate the material, ensuring stability and accurate positioning during the cutting process. Particularly in tube bevel cutting, the chuck system helps achieve complex angles and paths, ensuring cutting quality.
Advantages of Bevel Laser Cutting for Metal
- Enhanced Efficiency: The use of laser bevel cutting technology significantly simplifies the processing workflow, allowing for the precise formation of bevels at angles ranging from 1°~45° in a single operation. This eliminates the need for multiple processes, such as traditional cutting and milling, greatly improving efficiency, ensuring quality, and saving resources while producing high-quality cut parts with excellent dimensional accuracy.
- Improved Surface Quality: Laser cutting provides extremely smooth cutting edges, significantly enhancing the quality of bevel surfaces. Since laser cutting is a non-contact process, it reduces deformation or damage to the workpiece caused by mechanical forces, ensuring clean and smooth cutting surfaces. This contributes to better welding quality and increased durability of the structure.
- Consistent Quality in Mass Production: Laser bevel cutting technology achieves a high degree of consistency in cutting results, particularly in large-scale production environments. By precisely controlling cutting parameters such as power, speed, and gas flow, complex shapes can be cut easily and accurately, ensuring that each product’s bevel dimensions and shapes meet design requirements, thus maintaining overall processing quality stability.
- Reduced Bevel Processing Costs: The integrated cutting process of laser bevel cutting reduces the multiple machining steps required by traditional methods, such as secondary cutting and grinding. This not only saves time and labor costs but also lowers material waste caused by repeated processing.

Application of Laser Bevel Cutting
Laser bevel cutting is a processing method that shapes materials into inclined or beveled edges. This technique has a wide range of applications:
- Metal Fabrication: Commonly used in the manufacturing of parts that require precise angles, such as brackets and frames. The bevel cuts facilitate better welding and assembly processes.
- Bevel Preparation for Welding: To enhance the stability and quality of welded joints, laser cutting technology is often employed to accurately create the required bevel profiles before welding operations begin. This adaptability meets various welding requirements.
- Processing of Steel Structures in Construction: Laser cutting technology is also suitable for creating bevels on steel structural components, such as bridges, building frames, and beams. This helps achieve optimal component fitting while ensuring the overall safety and reliability of the structure.
- Application in Pipe Production: Bevel cutting is an essential step in pipe production, facilitating seamless connections and precise joints between pipe sections. Laser cutting provides precise bevel designs suitable for pipe connections, thereby improving the overall performance and production efficiency of the pipes.
- Automotive and Marine Components: Laser bevel cutting is commonly used to cut bevels in automotive and ship hull plates, enabling effective connections and sealing of joint structures in hull materials.
The Best Bevel Fiber Laser Cutting Machine
This bevel laser tube cutting machine features an advanced metal tube clamping system, ensuring stable material delivery and achieving high-precision, high-quality cutting results. It is equipped with top-tier laser sources from Raycus or Max, delivering high-quality laser beams that produce smooth, burr-free cutting edges for precision machining.
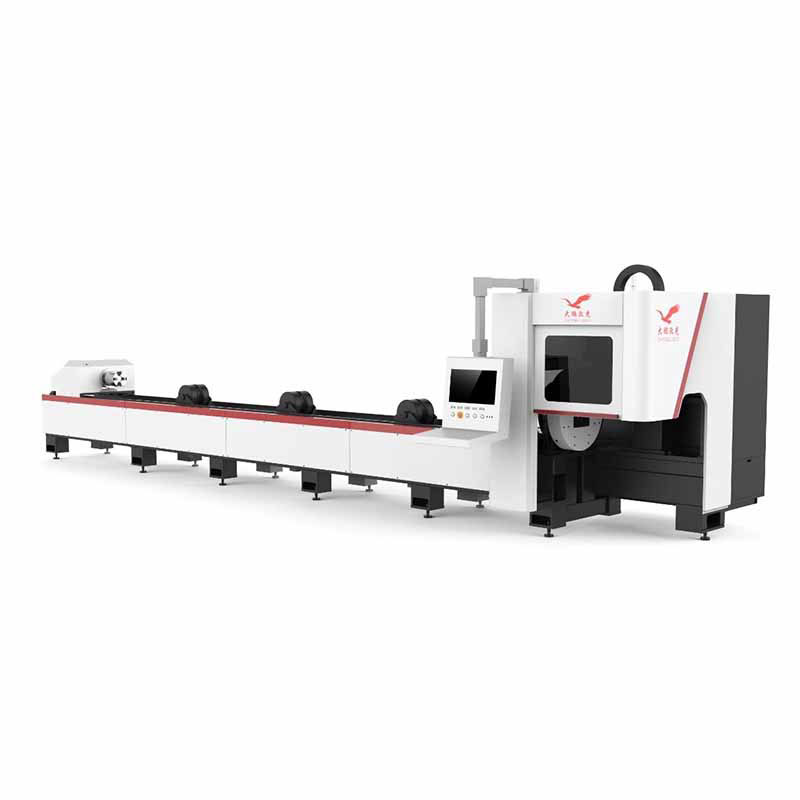
The machine structure employs aerospace-grade aluminum in a gantry design, providing both high accuracy and excellent toughness, enabling faster processing speeds suitable for extended, efficient operation. The equipment supports various 3D processing methods, including punching, arc cutting, engraving, and grooving, accommodating a wide range of irregular metal tubes such as rectangular, oval, square, round, triangular, D-shaped, and hexagonal tubes.
With optional automatic feeding and rapid high-quality cutting functions, this machine offers reliable performance and superior quality, backed by professional after-sales support.
Features:
- 3D Laser Head for Specialized 3D Cutting: This machine employs a branded 3D laser head specifically for 3D cutting, with auto-focusing capabilities. During bevel cutting, it adjusts the focal point based on the thickness and angle of the cutting material, ensuring cutting process precision. It efficiently processes various tubes, including round and square, delivering superior bevel cutting results.
- Single-Run Formation of Multiple Bevel Shapes: This machine can produce complex bevel shapes like Y, V, and X in a single run. It is equipped with practical functions, such as automatic obstacle avoidance, edge detection, rapid piercing, and visual calibration, which enhance operational safety while maintaining stable, high-quality cutting.
- Bevel Laser Cutting Benefits: This machine’s bevel cutting capabilities are marked by high precision, fast cutting speeds, unrestricted pattern versatility, and smooth cuts, along with low processing costs. It also offers automatic nesting to save materials, enabling rapid product iterations to meet market demand. As a result, high-power bevel laser cutting machines have become widely adopted in the market.
- Wide Bevel Angle Cutting Range (±45°): With a maximum cutting angle of ±45°, the machine’s intelligent control system automatically adjusts for optimal cutting paths, making the entire process both smart and convenient.
- 360° Unrestricted Rotation: Featuring a proprietary design, the machine’s cutting head can rotate without limitations. Paired with intelligent cutting software, this enables precise control over any bevel cutting path, ensuring consistent angle and precision. It supports 360° all-around bevel cutting.
- Single-Pass Angle Cutting Formation: This cutting machine efficiently performs various bevel types in a single pass, including K, X, positive Y, negative Y, A, and V, and it also supports 90° straight cuts. This single-pass capability greatly reduces the need for subsequent processing and significantly boosts material processing efficiency.

With its bevel cutting head, this CNC bevel tube laser cutting machine can perform precise bevel cuts up to ±45°, offering specialized solutions for heavy pipe bevel cutting, ensuring excellent results. For a custom 3D bevel laser cutting machine price, contact us with your processing requirements, and we’ll provide a quote right away. Don’t hesitate—start enhancing your metal fabrication today!
Summary:
In today’s manufacturing, bevel tube laser cutting stands out as a versatile and essential technique, providing precision and efficiency for metal processing. As industries increasingly demand high-quality finishes, laser cutting machines that handle bevel cuts deliver both accuracy and efficient. With advanced features and tailored functions, DPLASER bevel fiber laser cutting machine is designed to elevate your production, enhancing both speed and cutting quality to meet diverse needs across sectors. Explore the future of metal processing and take advantage of the innovative benefits that laser technology brings to your projects.