3D laser cutter and engraver for metal tube utilizes state-of-the-art laser technology to precisely cut and engrave metal tubes, opening up a world of possibilities for various industries. In this article, we will delve advantages of 3D tube laser cutting, capabilities, applications, exploring how it has significantly improved efficiency, accuracy, and flexibility in metalworking operations. This laser cutting equipment has made a significant impact on the way metal tubes are processed and enables operators to create more complex metal fittings faster than ever before.
What is a 3D Laser Cutter for Pipe?
3D laser tube cutting is a highly advanced manufacturing process that uses laser technology to cut and shape tubes or cylindrical objects with precision and accuracy in three dimensions. The tube to be cut is placed inside the machine, and the laser beam is directed onto the surface of the tube. By manipulating the laser beam’s intensity and focus, the machine can accurately cut through the material along specific paths and shapes, creating intricate patterns or complex cuts. Our 3D laser tube cutting machines eliminate the need for multiple passes when cutting parts with complex shape.
What are the Different Types of Tube Laser Cutter?
The 3D laser cutting machine for pipe is a device that utilizes laser technology to cut and process three-dimensional tubes. Based on different working methods and characteristics, it can be classified into the following types:
1. Handheld Tube Laser Cutting Machine:
This type of cutter is typically operated by hand, with the operator holding the laser beam to cut the tube. It is suitable for rough cutting or trimming of pipes and offers high flexibility and mobility.
2. Desktop Laser Cutting and Engraving Machine:
This cutter is usually based on a fixed tabletop, with the tube placed on the surface for cutting. It is suitable for cutting tubes with precise dimensions and shape requirements.
3. Automatic Fiber Laser Cutting Machine:
This type of cutter is equipped with automatic features, enabling automatic feeding, positioning, and cutting of tubes through computer control systems. It is ideal for large-scale, high-efficiency tube production and processing.
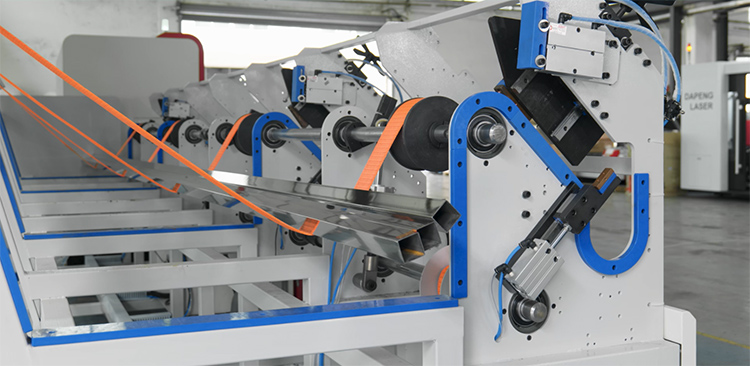
4. Multi-Axis Laser Tube Cutting Machine:
This cutter has multiple working axes, allowing for cutting tubes in three-dimensional space. It is suitable for cutting tubes with special shapes, curves, or complex structures.
These are some common classifications of 3D Laser Tube Cutting Machines, with each type being suitable for different cutting needs and application scenarios.
The Structure of CNC Fiber 3D Tube Laser Cutting Machines
The 3D Fiber Laser Tube Cutting Machine is a device that utilizes fiber laser technology to cut and perforate three-dimensional tubes. It is typically composed of the following main components:
Machine Body:
The machine body serves as the mainframe of the equipment and is usually made of steel or cast iron, providing sufficient strength and rigidity to withstand the pressure and vibrations during the cutting process.
Fiber Laser Source:
It provides the high-intensity laser beam required for cutting operations. The fiber laser source is known for its reliability, efficiency, and ability to deliver precise and consistent cutting performance.
3D Cutting Head:
This cutting head is designed to move in three dimensions (X, Y, and Z axes). It contains mirrors and lenses that guide and focus the laser beam onto the tube’s surface, allowing for accurate and intricate cutting.
Tube Feeding System:
The machine is equipped with a tube feeding system that facilitates the loading and positioning of tubes to be cut. It may include rollers, clamps, or chucks to secure and advance the tube through the cutting process.
CNC Control System:
The CNC controller serves as the machine’s control unit. It receives instructions from CAD/CAM software and translates them into precise movements and cutting paths for the laser and cutting head.
Cooling System:
Laser cutting generates heat, and a cooling system is necessary to maintain the optimal operating temperature of the laser source and other critical components.
Exhaust System:
As cutting generates fumes and smoke, an exhaust system is integrated to extract and filter the emissions, ensuring a clean and safe working environment.
Supporting Device:
Support the metal pipe to be processed, to ensure the stability and accuracy of the pipe processing.
Clamping Device:
Clamping the metal pipe to be processed to ensure that the pipe does not move or slide during processing.
Despite the complexity of the 3D tube cutting machine, it enables efficient and accurate metal tube processing through the synergy of its components. The multi-axis motion system and advanced laser power control technology give it the ability to cut in multiple directions and angles.
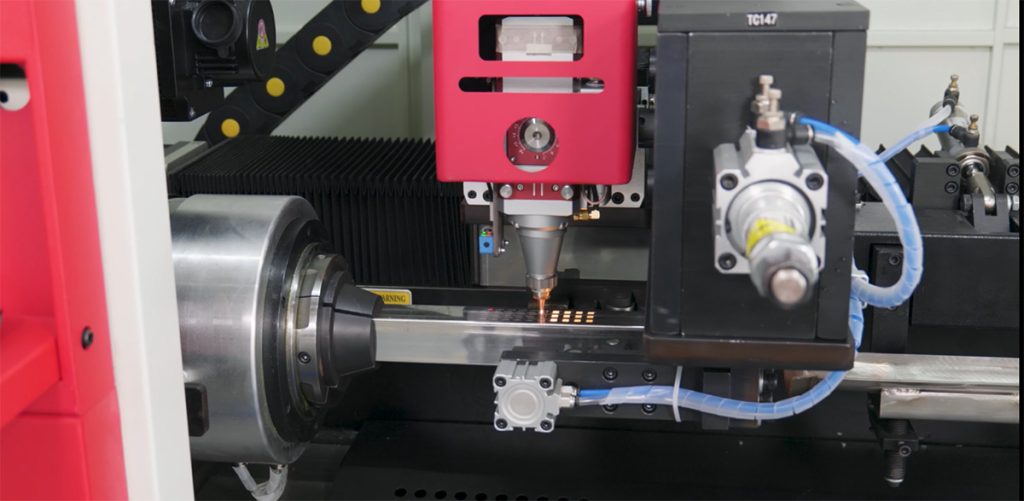
Advantages & Disadvantages of 3D Fiber Lase Cutter
3D laser pipe cutting machine has revolutionized many industries by providing an efficient and accurate method for fabricating Round, Rectangular Tube and Angle, Flats, Square Tubes, H-Tubes, Hex Tubes, Wedge Tubes, R-Tubes. These metal tubes can be cut, bent, welded and other processing techniques to form complex structures according to different material and size requirements, to meet the demand for diversified shapes of tubes in various industries.
1. Precision: Laser cutting is highly precise, allowing for intricate and complex designs with tight tolerances. This precision ensures that the finished components fit together perfectly, reducing the need for additional manual adjustments.
2. Versatility: 3D laser tube cutting machines can work with a wide range of materials, including metals like steel, aluminum, and stainless steel, as well as various plastics.
3. Efficiency: The process is computer-controlled and automated, leading to faster production rates compared to traditional cutting methods. This efficiency helps reduce production time and costs.
4. Minimal waste: Laser cutting is a non-contact process, enabling cutting with greater precision, tighter tolerances, and reduced material damage in the heat-affected zone.
5. Complex geometries: The technology enables the creation of complex pattern that would be challenging or impossible to achieve using conventional cutting methods.
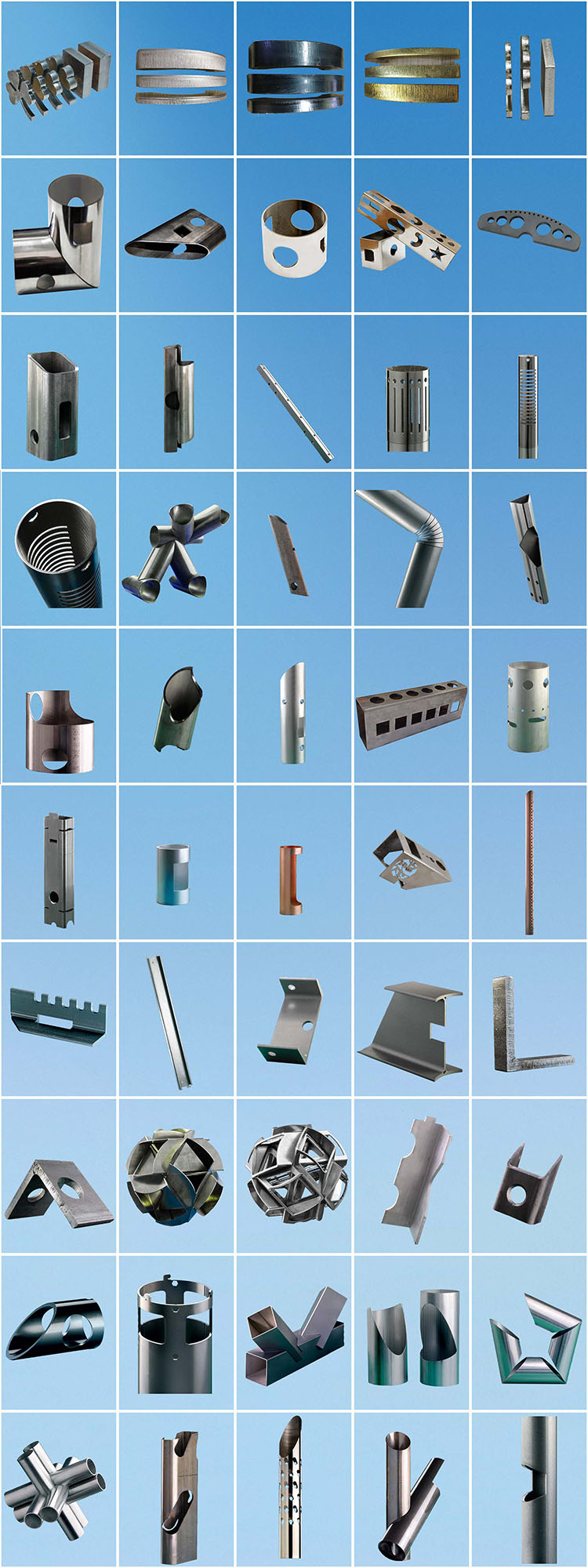
6. Repeatable results: Once a cutting program is established, the laser cutting machine can reproduce the same cuts with consistent quality, ensuring reliable results for mass production.
Tube 3D laser cutting is often used as an alternative to machining as it produces the same precision results at a lower cost.
Cons
1. Initial Investment: The upfront cost of setting up 3D laser tube cutting, which includes acquiring the laser cutting machine and necessary software, can be quite substantial. This initial investment may pose a significant hurdle for small businesses or startups seeking to embrace this advanced technology.
2. Maintenance Costs: Regular maintenance is essential for the optimal functioning of laser cutting machines. Expenses for replacing consumables like lenses and nozzles, as well as periodic servicing of the laser source, can accumulate over time, adding to the overall operational costs.
3. Noise and Fumes: During the cutting process, noise and fumes can be generated, especially when working with certain materials. Adequate ventilation and the use of appropriate protective equipment may be necessary to ensure a safe and healthy working environment for operators.
Despite these drawbacks, 3D laser cutting for tubes remains a highly effective and widely-used manufacturing process. Many of these challenges can be addressed through proper training, prudent equipment selection, and implementing appropriate safety measures in the cutting environment. With the potential for unparalleled precision and versatility, the benefits of 3D laser tube cutting can far outweigh the initial challenges, making it a valuable tool for various industries.
Application of 3D Pipe Cutting Machine
1. Metal Processing:
The metal pipe cutting machine can be used for processing various metal pipes, such as steel pipes, aluminum pipes, copper pipes, etc. It is capable of precise cutting and processing, used in the manufacturing of components for various transportation vehicles such as cars, airplanes, trains, ships, as well as components in fields like construction, machinery, electronics, etc.
2. Furniture Manufacturing:
This cutting machine can process various shaped metal pipes and can be used in the manufacturing of furniture frames, supports, and other components.
3. Instrument Manufacturing:
The metal pipe cutting machine can be used in the production of parts requiring various instrument casings, such as motorcycle supports.
4. Pipeline Fabrication:
This cutting machine can be used in the manufacturing of various pipeline components, such as elbows, expansions, and reductions. Precise cutting and processing of metal pipes ensure the quality and sealing of pipe connections.
Three-Dimensional fiber laser cutting machine is the preferred choice for engineering applications requiring high productivity in the manufacturing of complex parts for industries such as automotive, aerospace, electronics, and others. This equipment is more common in the manufacturing and construction industries, and it is more likely to be needed by metal processing or building material suppliers.
What to Consider Before Purchasing 3D Pipe Cutting Machine
1. Cutting Requirements
Clearly define your cutting needs as the first step in purchasing a pipe cutting machine. Determine the types of pipes you need to process, the size range, maximum cutting thickness, and cutting precision requirements. This will help you choose the appropriate model of pipe cutting machine that suits your needs.
Focus position, nozzle height, mode power, etc., all influence the corresponding cutting process. Additionally, the precision of the 3D laser pipe cutting machine depends on the equipment itself and external factors. So, when using the equipment, it’s necessary to adjust and set the corresponding parameters, including speed, power, etc.
Assist Gas:
During the use of the 3D laser pipe cutting machine, it requires the addition of corresponding assist gas. As the type and pressure of gas can have certain effects on cutting, it is essential to choose assist gas that is suitable for the processed material. The right assist gas not only reduces the heat-affected zone but also cools the focusing lens and the surface of the workpiece. Additionally, it prevents smoke and dust from entering the lens, which could cause overheating. Commonly used gases include air, nitrogen, and oxygen.

2. Equipment Quality and Stability:
Choose a reliable laser equipment manufacturer and brand to ensure that the purchased laser pipe cutting machine has stable performance and excellent durability.
3. After-Sales Service and Maintenance Support:
Understand the supplier’s after-sales service and maintenance support, including equipment usage guidance, maintenance, and response time for repairs. Make sure you can receive timely technical support and maintenance services to ensure the long-term stable operation of the equipment.
4. Price and Cost-Effectiveness:
Consider the balance between the price and performance of the metal pipe cutter create a reasonable purchasing plan based on your budget and research the prices of similar products in the market to ensure that the purchased pipe cutting machine has good cost-effectiveness.
Automatic 3D Tube Laser Cutting Systems
DPLASER’s professional 3D laser pipe cutting machine is suitable for expanding the scope of laser cutting of pipes, tubes, and structural applications, including I-beams, H-beams, C-channels, angle steel, and other user-defined three-dimensional shapes made of carbon steel or stainless steel.
Three-dimensional (3D) laser cutting shares similarities with traditional laser cutting, but its uniqueness lies in the laser’s ability to recognize and process all sides of the substrate, not just the surface. In contrast, two-dimensional (2D) laser cutting mainly handles flat materials. Three-dimensional laser cutting is typically capable of processing cuboids or other large substrate shapes, making it more flexible and versatile.

Features:
Bevel Cutting
Perform bevel cutting at the ends or sides of the pipes. By adjusting the position and angle of the cutting head, as well as controlling the cutting path and parameters, precise bevel cutting of metal pipes can be achieved.
Fast Cutting
When cutting small graphic contours, there is no need to move the pipe; instead, the cutting head swings to enable quick cutting.
Automatic Loading and Unloading
The machine provides a fully automatic loading system that can automatically sort and measure the length of bundled pipes. Thanks to the intelligent unloading system, the finished products and waste are separated from each other. Additionally, remnants and waste materials are collected centrally.
Floating Support System
During cutting, the floating support device automatically adapts to the pipe’s rotational changes without interrupting the production cycle.
Pneumatic Chuck
Equipped with a high-speed pneumatic chuck with a maximum speed of 120r/min. The clamping force is adaptively adjusted, making the operation more intelligent and simplified.
Machine Bed
The metal steel-cast bed welding plate is stable and less prone to deformation. It has a longer service life, enhanced stability, earthquake resistance, and improved accuracy.
Applications:
With 3D technology, a wide variety of shapes can be cut on pipes, allowing for greater flexibility and design possibilities.
1. Curves and Arcs: 3D tube cutting technology enables the creation of smooth curves and arcs along the length of the tube. This can range from gentle bends to more complex and intricate curves.
2. Angle Cuts: Tubes can be precisely cut at various angles, including bevel cuts, chamfer cuts, and mitered cuts. This allows for connections, joints, or specific assembly requirements.
3. Holes and Slots: 3D tube cutting can create different sizes and shapes of holes and slots along the tube surface. These openings can be used for various purposes, including for fittings, connections, or ventilation.
4. Notches and Tabs: Notches and tabs can be cut into tubes to facilitate seamless connections and secure assembly. These features ensure proper alignment and stability when joining multiple tubes together.
5. Intricate Patterns: 3D tube cutting technology enables the creation of intricate and detailed patterns. This can include logos, text, decorative designs, or any custom pattern for branding or aesthetic purposes.
6. Curved or Straight Cuts: The technology allows for precise straight-line cuts as well as complex curved cuts along the length or across the tube. This versatility makes it possible to achieve a wide range of shapes and designs.
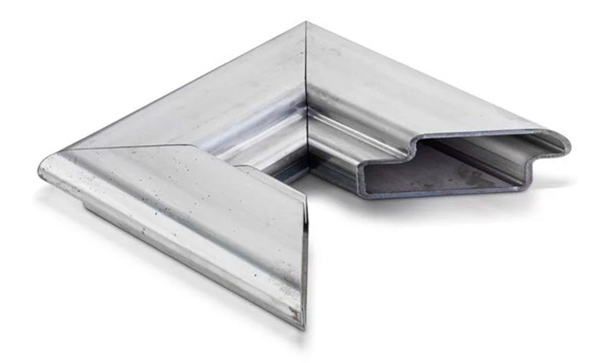
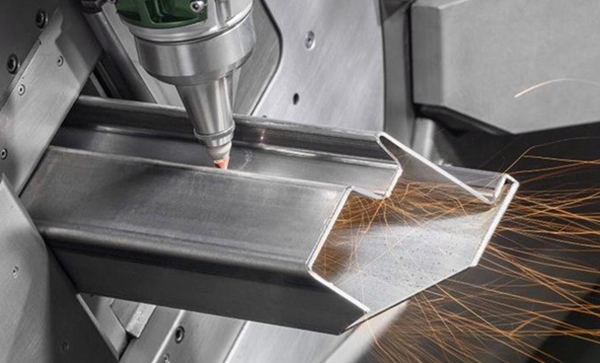


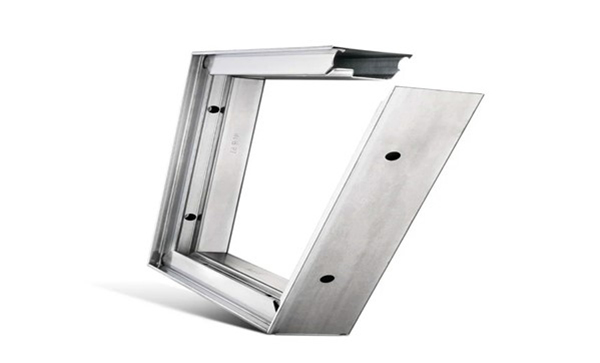
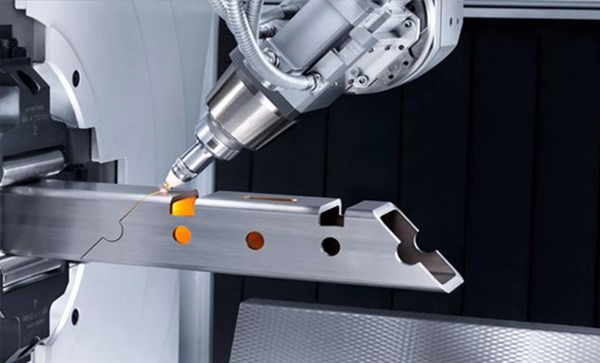
What are 3D cutters used for? From automotive and aerospace industries to construction and art, these cutting-edge machines have found their way into numerous applications. They are used for fabricating intricate components for engines and turbines, creating customized exhaust systems, and even crafting elaborate artistic installations. The future of 3D metal tube cutters appears promising. Continuous research and development efforts are underway to enhance their capabilities further. Our professional laser tube cutting machines greater levels of precision, efficiency, and automation, driving productivity and innovation to new heights.