Laser cutting and plasma cutting are two commonly used technologies in manufacturing and fabrication, each offering unique advantages based on the specific needs of the project. But what exactly is a laser cutting machine, and how does it compare to a plasma cutter? In this article, we’ll explore the difference between laser cutting and plasma cutting, helping you determine which technology is best suited for your cutting requirements.
Laser Cutter vs. Plasma Cutter
What is a Laser Cutting Machine? A laser cutting machine uses a laser beam emitted from a laser source, which is focused through an optical system into a high-density, high-power laser beam. This beam is directed onto the surface of the workpiece, heating it to its melting or boiling point. Meanwhile, a high-pressure gas, aligned with the laser beam, blows away the molten or vaporized metal. As the beam moves relative to the workpiece, it creates a cut seam, achieving the cutting process.

What is a Plasma Cutter? A plasma cutter is a machine that uses plasma cutting technology to process metal materials. Plasma cutting involves using the heat generated by a high-temperature plasma arc to melt and evaporate the metal at the workpiece’s cutting edge. The high-speed plasma flow then removes the molten metal, forming the cut. This cutting method is widely used for cutting thick metals.
Comparing Laser Cutting vs. Plasma Cutting
Laser cutting is distinguished by its high precision, speed, and quality, making it ideal for fine and intricate work. Plasma cutting, on the other hand, excels in cutting thicker materials due to its fast cutting speeds and versatility with various metals.
Cutting Speed
Generally, laser cutters offer higher cutting speeds than plasma cutters. This is because the laser beam has a significantly higher power density, allowing rapid and extensive heating of the material for quick cuts.
However, for thicker materials, plasma cutters tend to perform faster. In thick materials, laser energy dissipates as it penetrates deeper, slowing the cutting process. Plasma cutters, which are designed primarily for medium to thick materials, can cut up to 50 mm thick and maintain effective speed.
Cutting Quality
Laser cutters typically produce higher cutting quality than plasma cutters. With high precision and dense energy, laser beams enable clean, smooth cuts with minimal need for post-processing, achieving tolerances within ±0.1 mm.
Plasma cutting, while fast, often results in a rougher surface, particularly on thicker materials. The high temperature and speed of plasma create a wider heat-affected zone, impacting edge quality and often leaving burrs that require further finishing. Plasma cutting kerf widths are around 3 mm.

Heat-Affected Zone (HAZ)
Laser cutting introduces less heat, resulting in a smaller heat-affected zone. This minimizes thermal distortion, making it a superior choice for heat-sensitive materials or applications where precision is essential.
In contrast, plasma cutting generates a larger heat-affected zone, which can cause deformation and alter the internal structure of the material.
Automation Level
Laser cutters achieve high automation through programmed control, allowing precise cutting of complex shapes and greatly improving production efficiency and product consistency. Their advanced automation capabilities integrate seamlessly with computer numerical control (CNC) systems, enabling highly automated workflows. This reduces human error, labor costs, and overall production expenses.
In comparison, plasma cutters have lower automation capabilities and typically require more manual intervention and adjustments.
Applications
Laser cutters are suitable for cutting a wide range of metals, such as stainless steel, aluminum, and copper alloys. They can also cut non-metal materials like plastic, leather, and paper. Laser cutting is ideal for applications that require precision, intricate details, and high-quality surface finishes. This makes it valuable in industries like aerospace, automotive, electronics, and medical device manufacturing, where clean, precise edges are essential.
Limited Effectiveness on Reflective Materials: Laser cutting has limitations with high-reflectivity materials, such as aluminum, as they reflect the laser beam, reducing cutting efficiency.

Plasma cutters, using various working gases, can cut metals that are challenging for traditional oxygen-based cutting, especially non-ferrous metals like stainless steel, aluminum, copper, titanium, and nickel. Plasma cutting is well-suited for heavy-duty applications that require fast, efficient cutting of thicker materials. Industries like construction, shipbuilding, and metal fabrication benefit from plasma cutting’s speed and cost-effectiveness, especially where high precision is not critical.
Restricted to Conductive Materials: Plasma cutting is limited to conductive materials, making it unsuitable for cutting non-metals like plastic or wood.
All in all, when discussing laser cutting vs plasma cutting for metal, the applications of each technology highlight their respective strengths. Laser cutting offers superior edge quality, making it ideal for industries that require intricate, high-quality cuts on both metal and non-metal materials. On the other hand, plasma cutting is better suited for heavy-duty tasks, such as cutting thicker metals and non-ferrous materials. Its speed and cost-effectiveness make it the preferred choice in industries like construction, shipbuilding, and metal fabrication.
Cost and Maintenance
Laser cutting machines typically have a higher initial purchase cost than plasma cutters, but their operating costs are lower. The high power density of the laser beam allows for faster cutting, reducing production time and minimizing material waste.
On the other hand, plasma cutting machines have a lower initial cost but require regular replacement of components such as the torch and nozzle. Plasma cutters are well-suited for businesses focused on cutting thicker materials where high precision is not a primary concern.
Safety
As with any high-energy process, safety is a top priority. Both laser and plasma cutting involve the use of intense heat and energy to cut materials, which can lead to molten metal or other materials splattering, sparks flying, and smoke generated by burning materials in the air. Proper safety measures and equipment are essential when operating either system.
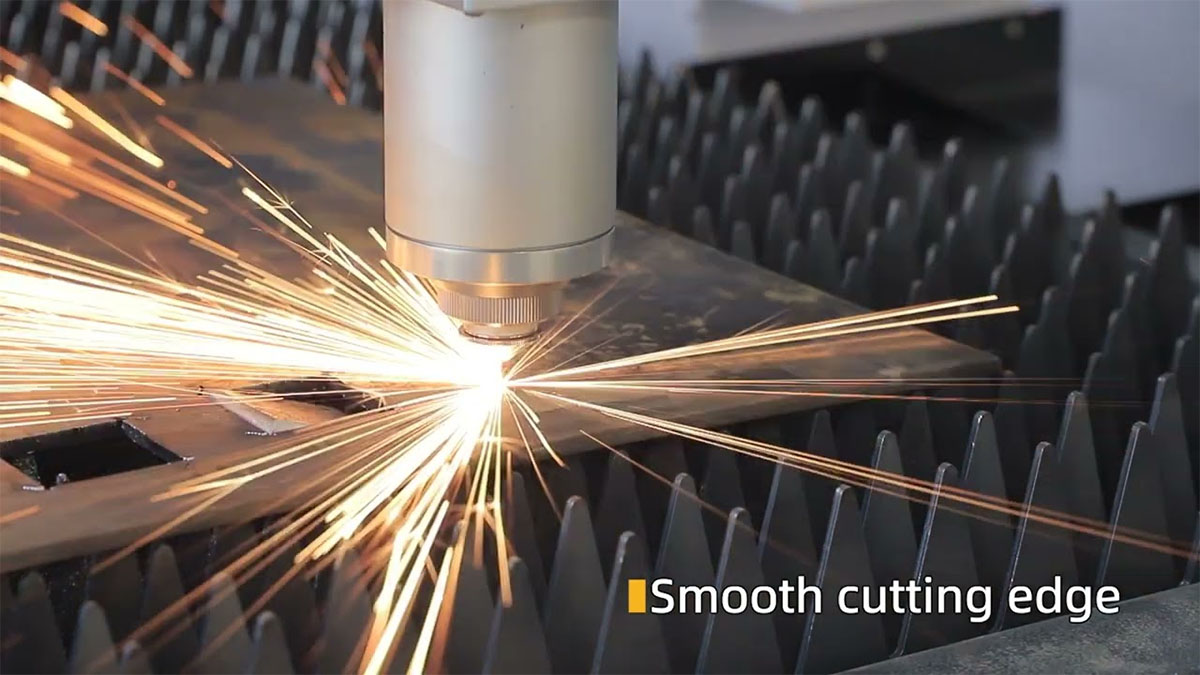
How to Choose Between a CNC Laser Cutting Machine and Plasma Cutter?
Choosing between a CNC laser cutting machine and a plasma cutter depends largely on the type and thickness of the material you’re cutting, as well as the precision requirements of your project.
If your work involves cutting parts with strict tolerances, high precision, or materials ranging from thin to medium thickness, a laser cutting machine is the better choice. It offers superior accuracy, consistency, and clean edges, making it ideal for intricate designs and demanding applications.
On the other hand, if you’re working with highly reflective metals, thicker materials, or simpler shapes, a plasma cutter might be more suitable. Plasma cutters offer versatility, can cut through thicker metals more quickly, and require a lower initial investment compared to laser cutting machines.
Fiber Laser Cutting Machine for Metal
A fiber laser cutting machine uses a high-energy density laser beam to achieve fast and precise material cutting. Laser cutting is characterized by high speed, accuracy (cut width of 0.1–0.2mm, precision of 0.01–0.02mm), excellent cut surface quality (roughness Ra 6.5–12.5μm), narrow kerf, minimal heat-affected zone, and negligible deformation. The cutting process is clean, safe, and pollution-free, making it ideal for efficient cutting of thin materials like carbon steel.
Plasma Cutting Machines for Metal
Plasma cutting machines use high-temperature plasma to cut metal materials, making them particularly suitable for cutting thicker metal workpieces. Plasma cutting is fast, especially when cutting thin carbon steel plates, where cutting speeds can be 5 to 6 times faster than oxygen cutting. Plasma cutting can utilize various working gases (such as argon, hydrogen, nitrogen, oxygen, air, and steam), allowing for optimization of cutting performance and improved cutting quality and speed by selecting the right gas.
Characteristics | Laser Cutting | Plasma Cutting |
Cutting Principle | Use of a beam to melt, burn or vaporize materials | Melts and blows away molten metal using a high-temperature plasma arc |
Application Material | Metals, wood, plastics, ceramics | Conductive metals (steel, stainless steel, aluminum, copper, etc.) |
Precision | Very high for complex shapes | Lower for fast cutting of thicker materials |
Speed | Slower speed but higher precision | Faster, especially for thick materials |
Costs | Higher initial investment, suitable for large-scale production | Lower running costs, suitable for medium-thick materials |
Heat affected zone | Smaller | Larger |
How to Choose the Right Laser Cutting Machine?
Laser cutting machines commonly require power levels between 3000W~6000W, though ultra-high-power models are also available. Laser cutting machines price from tens of thousands to over one hundred thousand dollars, depending on equipment size and capabilities.
When selecting a laser cutting machine, consider key production requirements such as material thickness, cutting frequency, width, and budget. It’s also essential to assess the quality of after-sales support—timely, on-site maintenance and troubleshooting can minimize downtime and prevent costly interruptions.
Standard machine sizes include models such as 3015, 4020, 6020, 6025, 8025, 10025, and 12025, with options for single or double worktables. There are also specialized machines, including plate-only, tube-only, and plate-tube integrated laser cutters. Selecting the right model should align with your company’s specific operational needs before setting a budget.
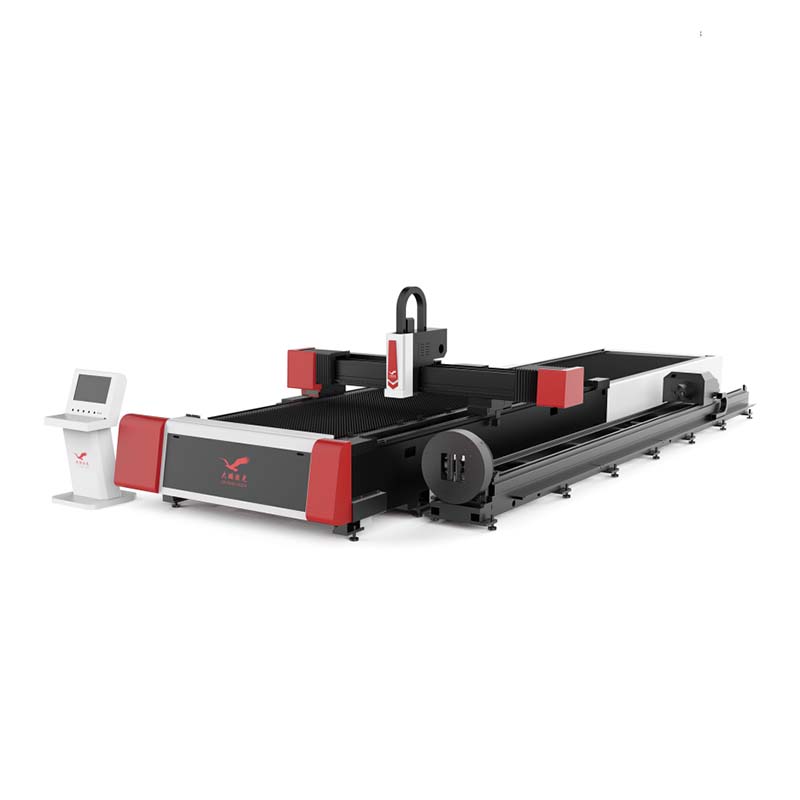
1. Clarify Cutting Requirements
- Define the Usage: Determine whether the machine will be used in-house or for outsourcing.
- Identify Materials and Thickness: Know the types of materials (e.g., steel, aluminum) and the thickness range you need to cut.
- Estimate Workload: Assess the expected cutting volume and required efficiency.
- Choose the Right Laser Power: Select a laser power that matches the thickness and complexity of the material you need to cut.
2. Evaluate Manufacturer Reputation
- Research Brand Reputation: Choose a manufacturer with a solid reputation and a history of technological advancement.
- Market Research: Check online reviews, industry exhibitions, and customer feedback to gauge the market standing of different brands.
- R&D Capabilities: Ensure the manufacturer has its own research and development capabilities and a complete production line.
3. Consider After-Sales Service
- Proximity to Supplier: Consider suppliers who are geographically close to ensure faster, more efficient technical support and service.
- Service Details: Make sure to clarify the scope of after-sales service, including installation, training, maintenance, and troubleshooting.
- Response Time and Spare Parts Availability: Inquire about the supplier’s response times and spare parts availability to minimize machine downtime.
4. Assess Pricing
- Compare Prices: Get quotes from multiple suppliers to avoid inflated or excessively low prices.
- Consider Operating Costs: Beyond the initial purchase cost, account for long-term operational costs such as consumables and energy usage.
- Return on Investment: Evaluate the return on investment (ROI) to ensure that the machine will deliver the expected economic benefits over its lifespan.
In summary, laser cutting is ideal for achieving high precision, fine detail, and minimal heat distortion, especially on thin to medium-thickness materials. Plasma cutting, on the other hand, excels at cutting thicker, conductive metals with high efficiency and speed. When discussing laser cutting vs plasma cutting price, laser cutting machines typically require a higher upfront investment due to their precision and versatility, while plasma cutting machines are generally more budget-friendly for thicker materials and high-volume cutting. Explore our laser cutting solutions to enhance your fabrication process.