Molds are essential tools in modern manufacturing, used to produce a wide range of plastic, metal, and composite products. The lifespan and quality of molds directly impact product quality and production efficiency. During use, molds may suffer from wear, cracks, dents, and other defects, requiring timely repairs. Laser welding for mold repair provides excellent assistance in this regard, as they can quickly repair damaged molds with high precision, even when dealing with hard-to-reach areas.
What is Laser Mold Repair Welding Machine?
Laser welding technology has found remarkable applications in the mold industry. Mold repair laser welding machine is easy to operate and can significantly accelerate the welding process, providing high-quality repairs with exceptional precision. As a result, they are widely used in mold welding applications. The laser welding machine generates an extremely small heat-affected zone, eliminating the need for preheating. After welding, the workpiece will not undergo annealing, preserving its original physical properties.
Laser welding not only effectively repairs mold wear but also allows for precise welding of small and intricate areas, ensuring no deformation or porosity after repair. This helps maintain the mold’s high performance and long lifespan.
Laser mold welding machines are specifically designed for the mold industry and are ideal for precision mold repairs. They are widely used in the manufacturing and molding of molds for digital products, mobile phones, toys, automobiles, motorcycles, and more. By providing precise repairs, molds that would otherwise be discarded can be reused, significantly reducing production costs and improving work efficiency. Additionally, laser mold welding technology also supports fine adjustments to mold designs or dimensions, helping to shorten product development cycles and accelerate the launch of new products.
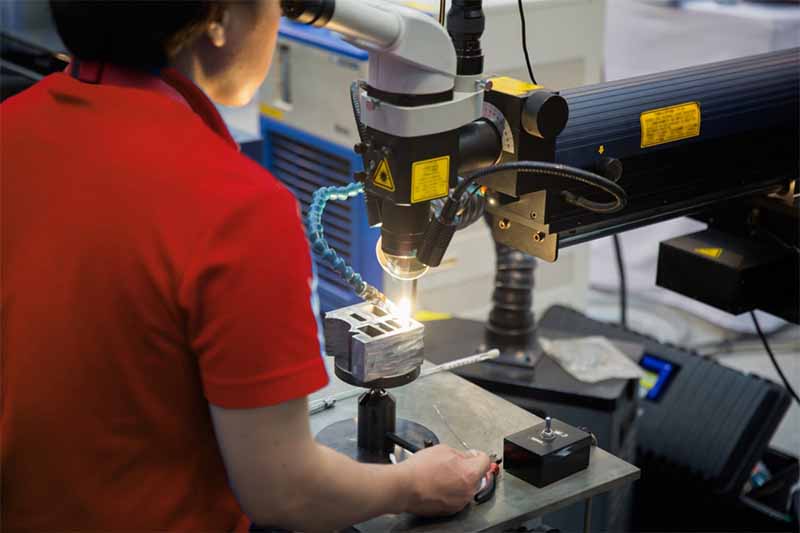
Laser Welding for Mould vs. Traditional Welding
Precision
Laser welding machines offer micron-level precision, making them ideal for the high-accuracy requirements of precision mold repairs. In contrast, traditional welding equipment provides lower precision, often struggling to meet the stringent demands of fine mold restoration.
Heat-Affected Zone
The laser welding process generates an extremely small heat-affected zone, minimizing impact on surrounding materials. This preserves the original properties of the material, preventing mold deformation and strength loss. Traditional welding methods typically create a larger heat-affected zone, which can lead to undesirable changes in the mold’s structure and properties.
Repair Quality
Laser welding does not require direct contact with the mold surface, reducing the risk of damage caused by physical contact and ensuring the integrity of the mold. The repairs made by laser welding machines are durable, with precise energy control that results in a tight molecular bond at the weld site. This allows the mold to withstand higher stress and impact without further damage. In contrast, molds repaired using traditional welding equipment may experience cracking at the weld site under complex stress conditions.
Efficiency
Laser welding is fast, allowing mold repairs to be completed in a short time, which significantly boosts production efficiency.
Flexibility
Laser welding machines offer high flexibility, capable of handling a wide range of complex mold repair needs. Whether its tiny components or large structural parts, laser welding can easily accommodate them, with quick adjustments and programming. Traditional welding equipment has limited flexibility and may require additional tools and complex procedures for welding intricate molds.
Automation
Platform laser welding machines have a high level of automation and can work in tandem with robotic systems and other automated equipment for efficient, streamlined production. In contrast, traditional welding equipment is less automated and relies more on manual operation, leading to lower efficiency and stability in mold repairs.
Cost
While laser welding machines have a higher initial investment cost, their advanced technology and lower maintenance complexity result in lower long-term costs. On the other hand, traditional welding equipment has a lower upfront cost, but it requires frequent electrode replacements and mechanical maintenance, making its long-term maintenance costs higher.
Application
Laser welding machines are especially suited for complex, high-precision mold repair tasks, such as aerospace components and miniature electronic product welding. Traditional welding equipment is better suited for large mold repairs or rough repairs where precision is not as critical.
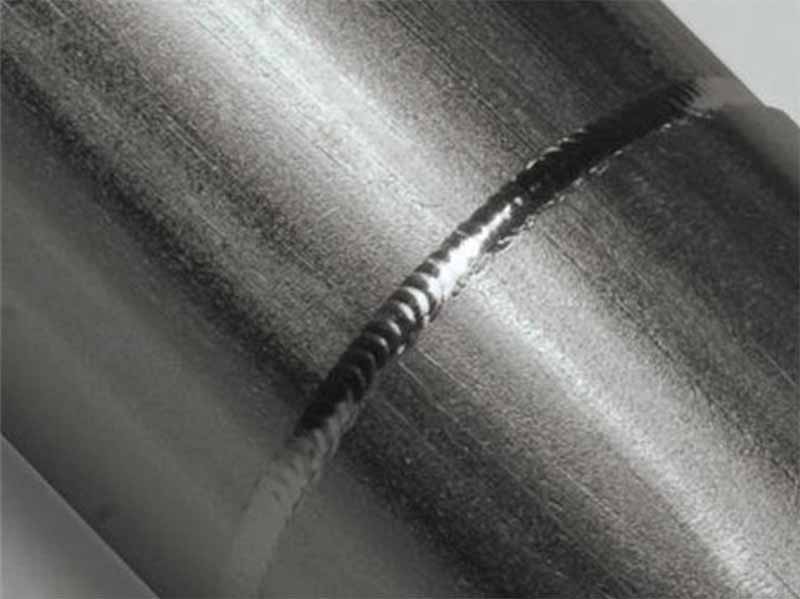
Benefits of Laser Welding for Mould Repair
High Precision
Mould laser welding machine allows for precise control over the heat-affected zone, effectively preventing or minimizing mold deformation caused by heat. This ensures that the repaired mold retains its original geometry after restoration.
Targeted Repair
Laser welder enables repairs to be made on specific damaged areas of the mold, without the need to treat the entire mold. This not only saves repair time and costs but also protects the undamaged parts of the mold from any damaged.
Low Heat Input
Because the laser beam can focus energy on a very small area, it significantly reduces the amount of heat transferred to the mold during the welding process. This results in minimal damage to the mold’s base material.
Wide Material Compatibility
Laser welding provides effective solutions for a wide range of materials, from tool steels to other commonly used mold metals, making it a versatile option for various mold repairs.
Reduced Repair Costs
By offering highly efficient and precise repair capabilities, laser welding helps lower the overall cost of mold repairs, extending the life of molds and reducing the need for complete replacements.
The Best Industrial Mold Laser Welding Machine
The DPLaser mold repair laser welding system is designed for precise mold repair, offering a superior alternative to TIG MIG welding. This machine is easy to operate and use, making it highly accessible. It is widely applied in the repair of precision injection molds, die-casting molds, stamping molds, and hard materials like stainless steel. The mold repairing laser welding machine effectively addresses porosity, slag holes, shrinkage cavities, cracks, edge wear, and seal edges, delivering reliable, high-quality repairs and welding for a variety of mold types.
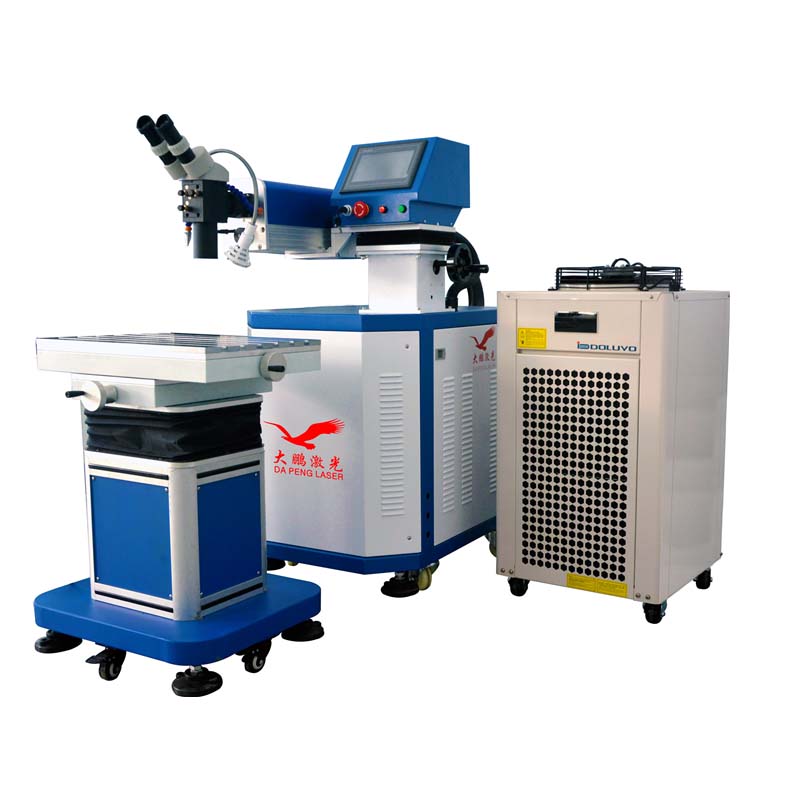
Ergonomic Workbench Design
The system features a convenient workbench for placing workpieces to be welded, allowing for precise laser alignment and seamless execution of welding tasks.
Professional Microscope Observation System
Equipped with a 10x magnification microscope and high-speed electronic filtering protection, this system ensures clear visibility for operators while safeguarding their eyes from direct laser exposure.
Intelligent Auxiliary Gas Protection
An internally controlled argon gas supply, managed by a microprocessor, creates an inert gas environment during welding. This effectively prevents oxidation of the weld area, ensuring the strength and aesthetic quality of the weld joint.
User-Friendly Interface
The large LCD display supports multiple language options and simplifies human-machine interaction, allowing even inexperienced operators to quickly master the system.
Flexible Laser Path Control
Operators can guide the laser path using a manual joystick or buttons, with real-time monitoring via a CCD camera or binocular microscope. This enhances both flexibility and precision during the welding process.
Convenient operating system
In addition to the preset standard welding programs, it allows the user to customize and save specific process parameters and use them when needed.
Efficient Temperature Management System
For robotic laser welding systems, the built-in water cooling unit effectively regulates the equipment’s temperature, ensuring stable operation with continuous cooling for long-term, high-efficiency performance.
Features:
Powerful Welding Capability: The laser welder for mould mold die repair supports a wide range of welding methods, including spot welding, butt welding, overlap welding, and seal welding. It delivers welds with a high depth-to-width ratio, fine width, narrow heat-affected zone, minimal deformation, and fast, efficient welding speed.
Micro Welding: By focusing the laser beam, the mold laser welding system achieves extremely small spot sizes for precise positioning, making it especially suitable for automated large-scale production and assembly welding of small parts, meeting high-precision requirements.
Material Compatibility: The laser welding machine repair mold can weld materials that are difficult to melt, such as aluminum, copper, iron, stainless steel, common metals and titanium and quartz, also enables dissimilar material welding. This versatility results in excellent welding quality for a variety of materials.
Flexibility: It can weld in hard-to-reach areas and supports non-contact, long-distance welding, greatly enhancing the flexibility of welding operations. In recent years, with the application of fiber optic transmission technology in YAG laser processing, the scope of laser welding applications has expanded further.
Wide Applicability: The high-power metal laser welding machine is also capable of handling thicker molds. Whether the welding task is simple or complex, the system is easily capable of managing it, ensuring versatility across a wide range of applications.

Tips for Laser Welding Machine Repairing Industrial Molds
Careful Inspection
Use a microscope to closely examine the mold and welding conditions. It is recommended to use binocular observation for more accurate details of the mold.
Choose the Right Welding Wire
Select the appropriate welding wire diameter (typically between 0.2~0.8 mm) based on the mold repair requirements. Proper material selection is crucial to ensuring the quality of the repair.
Identify Mold Material
Different mold materials (e.g., galvanized, beryllium copper, or aluminum) require adjustments to welding parameters to achieve the best repair results. Always identify the material before setting up the machine.
Gas Protection
Ensure that protective gas is supplied before welding begins to prevent oxidation of the material during the welding process, which can negatively affect the quality of the weld.
Avoid Undercut in Welding
Preheat the area around the welding zone with the laser to prevent undercut in welding at the edges of the weld. This helps maintain the integrity of the mold and prevents damage to surrounding areas.
Use CCD Monitoring System
In addition to direct observation through a microscope, a CCD camera system allows other team members to remotely monitor the welding process via a screen. This aids in team collaboration and ensures better quality control during the repair.
The mold fiber laser welding machine uses a fiber laser source, offering a range of significant advantages, including no material consumption, minimal maintenance, fine welding points, no post-processing required, compact size, low energy consumption, and ease of operation. Even workers with no prior welding experience can quickly learn how to use the machine. We offer a variety of configuration options and tooling fixtures, and we also support custom laser welding machines tailored to your specific production needs.

If you’re considering laser welding for your molds, simply provide us with the following information, and the professional team at DPLaser will tailor the optimal welding solution for you:
- What are the dimensions and processing requirements of your mold? (Providing images would be even better)
- What is the diameter of the welding wire you commonly use? (e.g., 0.5 mm, 0.8 mm, 1 mm, etc.)
- Do you have welding requirements for circular or cylindrical molds? If so, a rotating auxiliary system may be necessary.
In conclusion, mold laser welding machines provide efficient and precise solutions for both welding and repairing molds. With advantages such as superior accuracy and minimal heat distortion, laser welding outperforms traditional methods, ensuring improved mold lifespan, production efficiency, and consistent product quality across various industries. Dapeng Laser’s latest mould laser welding machine is designed to meet diverse industry needs, ensuring enhanced mold maintenance and consistent product quality.