Starting a 3d robot laser cutting machine 2025 requires careful planning and the right technology to maximize efficiency and quality. As industries increasingly adopt automation, robotic laser cutting systems have become a game-changer for handling complex 3D cutting tasks, improving production speed, and reducing material waste.
Why Start Your Robot Laser Cutting Project 2025?
The traditional processes in the automotive sheet metal industry involve 3D cutting of various auto parts, such as hoods, doors, and bumpers. Common methods include die stamping, plasma cutting, and five-axis laser cutting. However, these methods come with high costs, long production cycles, poor flexibility, and subpar cutting quality. The manufacturing and trimming of complex molds require advanced technology and equipment, often leading to material waste and increased costs. Additionally, plasma cutting requires post-processing, such as grinding, which is inefficient and harmful to health.
To address these issues, a new process integrates industrial robots with fiber lasers for 3D cutting. This combination reduces costs, minimizes system footprint, and lowers energy consumption and maintenance expenses. While robotic system positioning accuracy is slightly lower than that of five-axis CNC cutting machines, it still meets the precision requirements of automotive sheet metal components, offering a more economical and efficient solution.
In traditional manufacturing, the process involves measuring workpiece data, drawing designs, developing molds, fabricating molds, trial production, and mold adjustments—taking at least 15 days before mass production can begin. In contrast, 3D robot laser cutting machine requires only a single forming mold to complete the cutting process, significantly shortening the development cycle and reducing production costs. It also allows for timely identification of design issues, lowering overall R&D expenses while improving processing efficiency and workpiece precision.
Six-Axis Robotic Laser Cutting System
The six-axis robotic laser cutting system consists of a robotic arm system, laser cutting system, vision system, and auxiliary tooling system. It is an integrated system that combines robot motion control, laser processing, tooling coordination, and visual algorithms to achieve precise and efficient cutting.
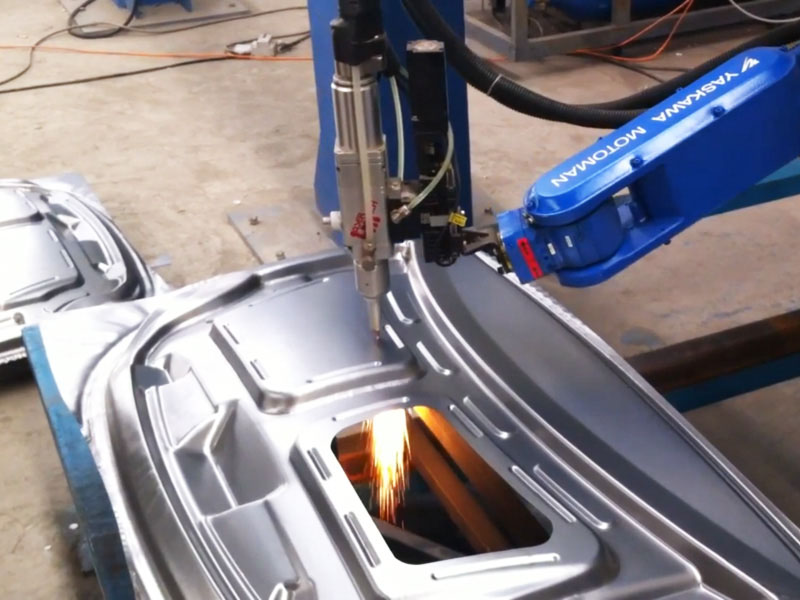
How 3D Laser Cutting Robots Boost Manufacturing?
3D laser cutting robots integrate robotics and laser cutting technology to achieve high-precision motion and efficient material processing across various industries.
1. Flexible Cutting Paths
Unlike traditional machines that operate on a fixed plane, robotic systems can position the laser cutting head at almost any point and angle within their workspace. This flexibility allows for intricate and precise cuts on complex 3D surfaces.
2. High Efficiency & Speed
The combination of rapid robotic movement and advanced laser cutting significantly boosts processing efficiency. This not only reduces production time and costs but also makes it ideal for both mass production and customized manufacturing.
3. Versatility & Adaptability
3D laser cutting robot systems can be adjusted to accommodate different product shapes, sizes, and materials—including both metals and non-metals. With proper programming, they can autonomously handle both flat and complex geometric cuts with ease.
4. Wide Industry Applications
These robots are widely used in industries such as aerospace, automotive, shipbuilding, machinery manufacturing, elevator production, advertising, home appliances, medical devices, hardware, and metal construction. In particular, they offer unparalleled advantages in automotive component manufacturing, reducing mold development costs and minimizing investment risks in body design and production.
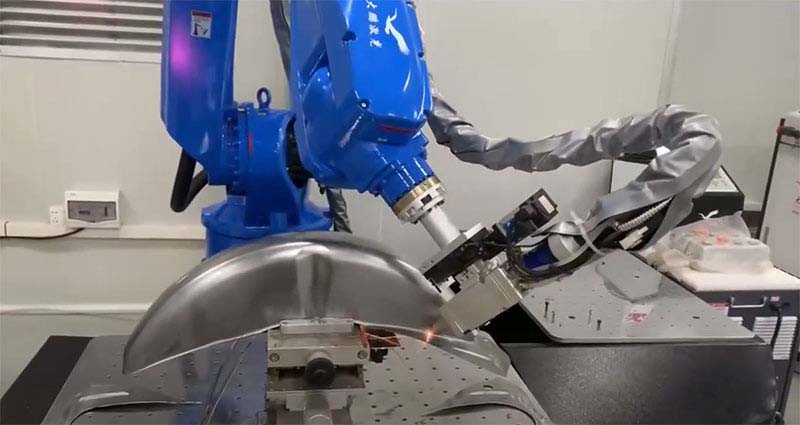
What should you consider when purchasing a 3D robot laser cutting system?
- Product Dimensions – Define the length, width, height, or diameter of the workpieces to ensure the system can accommodate the required cutting area.
- Material Type & Thickness – Identify the material (e.g., steel, aluminum, plastic) and its thickness to determine the appropriate laser power and cutting settings.
- Processing Requirements – Specify the intended operations, such as cutting, welding, cleaning, or marking, to ensure the system meets your production needs.
- Additional Requirements – Consider performance factors like pressure resistance, airtightness, tensile strength, and required production capacity per hour.
- Pre-Processing – Assess existing cutting or welding techniques and their precision levels to determine integration or replacement needs.
- Other Considerations – Evaluate automation compatibility, tooling responsibilities (customer or supplier), and the need for training or after-sales support.
By carefully analyzing these aspects, you can ensure the selected system enhances efficiency, reduces costs, and meets production goals.
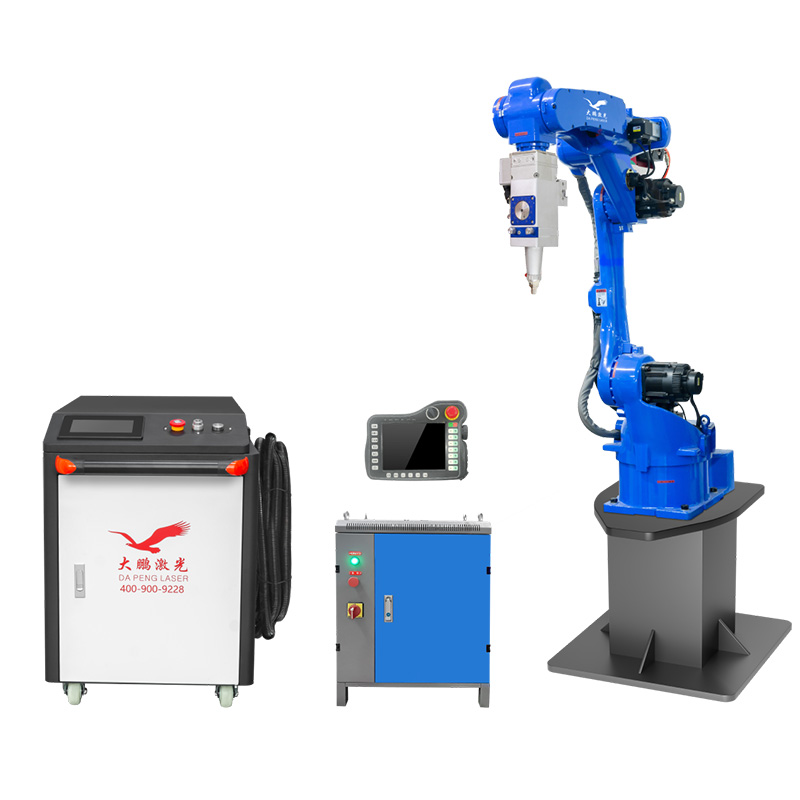
How to Choose the Best Robotic Laser Cutting Machine 2025
1. Arm Reach – The arm reach determines how far the robot can extend to access cutting positions. A longer reach allows for processing larger workpieces, while a shorter reach limits the size of products that can be handled.
2. Payload Capacity – The payload refers to the weight the robotic arm can carry. A higher payload can support heavier cutting or welding heads. The required payload is determined by:
- Cutting head weight
- Mounting plate weight
- Vision system weight
- Distance from the 6th axis center (lever principle: the farther from the center, the higher the required payload)
3. Repeatability Accuracy – This measures the deviation when the robot repeatedly reaches the same point.
- Standard brands: ±0.08mm repeatability, suitable for cutting circles larger than 20mm (requires a robot with a payload above 20kg).
- High-end brands: ±0.02mm to ±0.06mm repeatability, capable of cutting circles larger than 8mm with higher precision.
4. Absolute Positioning Accuracy – This refers to the deviation between the programmed position and the actual stopping point of the robot. The smaller the deviation, the higher the accuracy of the machine in following programmed cutting paths.
Robotic 3D Laser Cutting Machine VS. CNC Cutting Machines
Equipment | Traditional Hardware Mold Cutting Equipment | Robotic Laser Cutting Machine |
Process | Requires forming, punching, blanking, trimming, and matching press machines with corresponding molds. | After blank forming, a single 3D machine can independently complete production. |
Cost | High cost of press machines. | Lower equipment costs compared to traditional methods. |
Extremely high mold costs. | Simple process, easy to learn and operate. | |
Different products require the development of separate molds. | Minimal preparation time required. | |
New mold development takes 3 to 6 months. | Fast production launch with quick setup. | |
Complex debugging and stamping processes. | Easy adjustments for different products. | |
Requires multiple operators. | Operable by a single person, reducing labor costs. | |
Applicability | Suitable for single-product, large-scale mass production. | Ideal for new product development and small to medium batch production of multiple varieties. |
Laser Cutting Robot vs. Five-Axis Laser Cutting Machine: Which One is Right for You?
🔧 Structure & Workspace
A multi-robot 3D laser cutting system consists of multiple robotic arms and laser cutting heads, enabling simultaneous operation for higher efficiency and processing capacity. It provides a larger workspace, making it ideal for cutting and processing large-sized workpieces or handling multiple workpieces across different cutting zones.
🔧 Flexibility
Multi-robot systems allow robotic arms to collaborate and divide tasks, making them highly adaptable to complex cutting operations. In contrast, a five-axis laser cutting machine, despite having multiple axes for control, remains a single unit, offering relatively lower flexibility.
🔧 Production Efficiency
Since multiple robots can work simultaneously, multi-robot 3D laser cutting systems achieve higher production efficiency. Through coordinated operations and task distribution, they can process multiple workpieces or cutting zones at the same time, making them ideal for high-volume production and fast-cutting applications.
🔧 Application Scenarios
The choice between a multi-robot 3D laser cutting system and a five-axis laser cutting machine depends on specific production needs:
If you require high output, flexibility, and adaptability for large-scale production, a multi-robot laser cutting system is the better choice.
If precision and intricate shapes are the priority, a five-axis laser cutting machine may be more suitable.
Application Examples
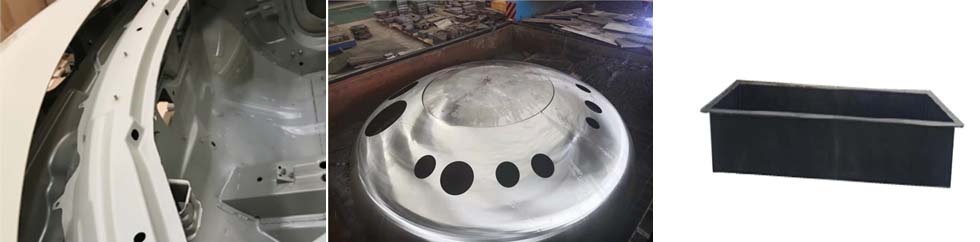
3D cutting of automotive parts | Pressure vessel covers & tubes | Carbon fiber 3D cutting |
Accessory Selection
Positioner
Suitable for double-sided processing and continuous 24/7 operation, significantly improving work efficiency.
Enables left-right cyclic operation for uninterrupted production.
Selection should be based on product size, weight, and fixture dimensions to ensure the appropriate load capacity and size.
Available options include single-station and dual-station positioners.

Rotary Platform
Designed to accommodate cutting at different angles and orientations for various workpieces.

Rotary Positioner

Ground Rail
When the robotic arm’s reach is insufficient to cover the required welding length, a ground rail or gantry system can be used. The ground rail allows the robot to move along the track and stop at a fixed position before performing operations.
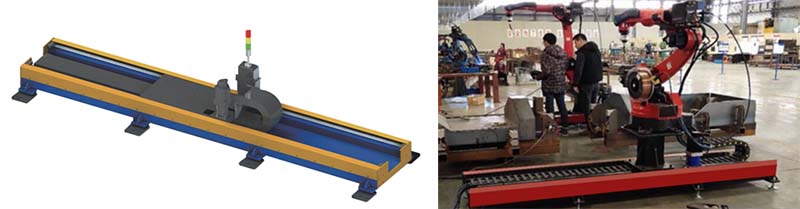
Workbench
Single, double or triple workbench can be matched according to products.
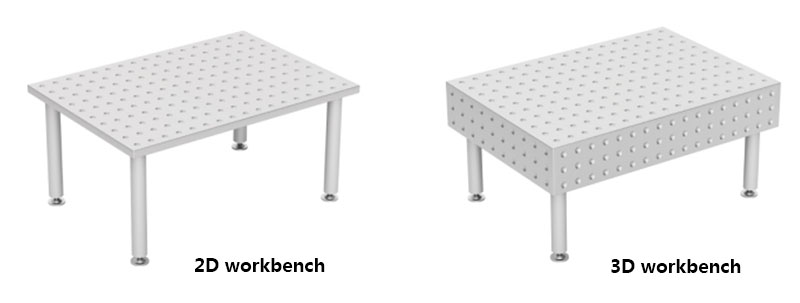
Visual tracking system
According to product selection, it can solve product assembly errors and correct them during welding.
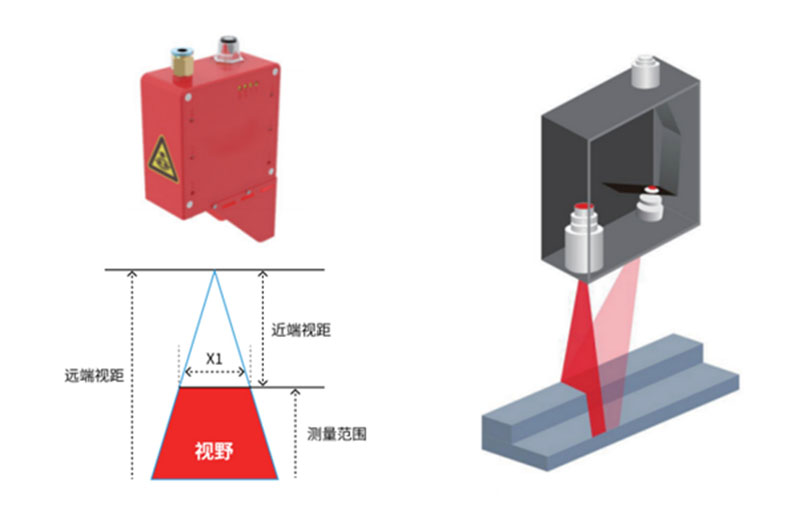
Safety Fence
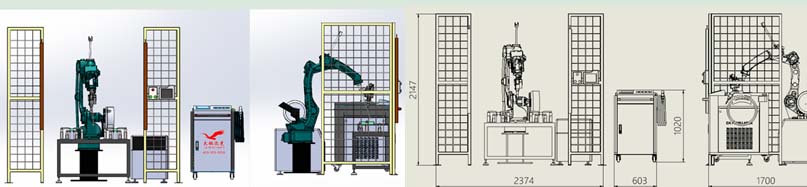
Workstation and Control System
The control system uses a PLC for integrated control, with human-machine interaction through an HMI. The PLC centrally manages the control systems for the laser, robot, welding head, fixture, chiller, laser protection, smoke purifier, welding room access control, safety circuit, and sound and light alarm systems.
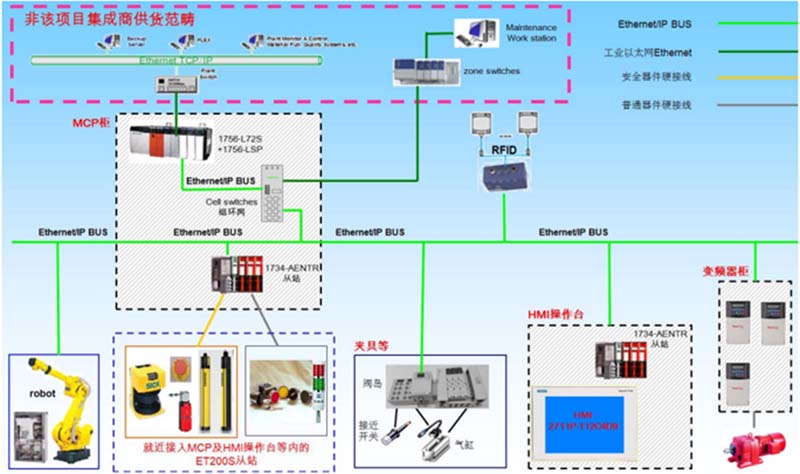
Smoke and Dust Purification System
The smoke and dust purification system uses a high-efficiency industrial dust collector produced by a well-known environmental protection company. The product features high energy efficiency, high negative pressure, and cost-effectiveness. It adopts an integrated cabinet structure with an attractive design, specifically designed for laser processing fumes, plasma cutting fumes, and other floating dust. It includes a customized high-efficiency impeller, imported polyester fiber filter cartridges, PTFE coating, and H13-grade filtration precision and efficiency.
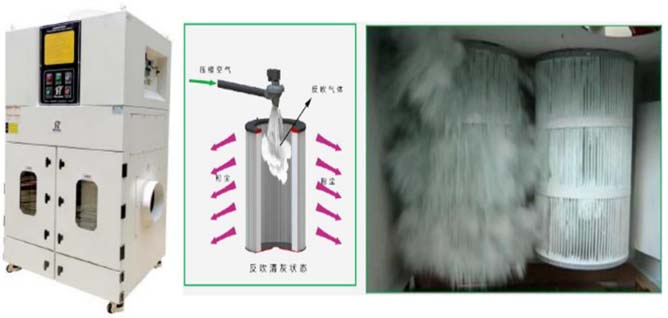
Voltage Stabilizer
When fluctuations in the external power supply voltage or load changes cause voltage instability, the voltage regulator can automatically maintain a stable output voltage. Compared to other types of voltage regulators, it offers advantages such as large capacity, high efficiency, no waveform distortion, and smooth voltage regulation. It also includes protection functions for over-voltage, under-voltage, overload, overcurrent, short circuit, and bypass, providing strong assurance for the stable operation of the laser and control systems.
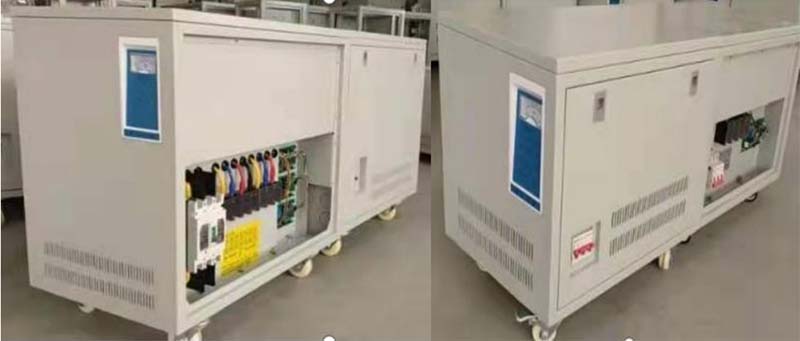
Top Manufacturers of Industrial Robot Systems
FANUC is a global leader in industrial automation and robot manufacturing, renowned for its high-precision, high-reliability laser cutting robots. Its integrated control systems and intelligent features (such as AI servo adjustment) enable automated, high-efficiency production, making it particularly suitable for large-volume, high-precision automotive component cutting. FANUC’s laser cutting robots are capable of handling complex 3D laser cutting and welding tasks.
ABB
ABB is a giant in the industrial robotics field, offering advanced laser cutting solutions. Known for its robots’ high speed, precision, and flexibility, ABB’s robots are ideal for complex cutting tasks and are widely used in metal processing and manufacturing. Their robots support modular design, making them easy to integrate into existing production lines. They are particularly well-suited for customized production with small batches and multiple varieties.
KUKA
KUKA, a well-known German industrial robot manufacturer, specializes in high-performance laser cutting robots. Its products are known for high dynamic performance and stability, making them ideal for high-precision, demanding cutting applications, widely used in automotive and heavy industries. KUKA’s laser cutting robots have high payload capacity, large working ranges, and advanced control systems, enabling precise and flexible laser cutting. Their robots are capable of handling complex 3D laser cutting, welding, and surface treatment applications.
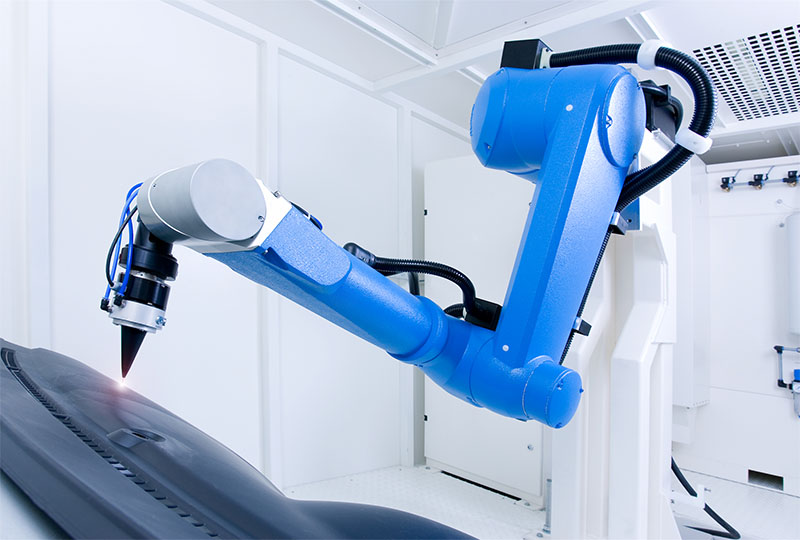
Conclusion: The above information is intended to give you a preliminary understanding of how to choose the most suitable laser cutting robot for your project. If you need more in-depth information or would like to receive free samples, please feel free to contact us through any of the options on our website to discuss your needs with our laser equipment manufacturing engineers. DPLaser is a professional robot laser cutting machine manufacturer, and we’re confident you’ll find a satisfying laser production solution here.