As manufacturing continues to advance, the integration of automatic laser welding technology has become integral to the contemporary industrial landscape. Among the plethora of laser welding equipment options, automatic laser welding machines have risen to prominence due to their efficiency, precision, and versatility in tackling even the most intricate welding tasks. In this context, this article delves into choosing the platform fiber laser welding machine that best suits needs.
What is Platform Laser Welder?
Automatic laser welding machine is a kind of CNC laser welding machine, which can carry out automatic or semi-automatic butt welding, sealing welding, spot welding, continuous welding, and realize the welding of complex plane straight line, circular arc and arbitrary trajectory. The automated laser welding machine is configured by software to weld automatically according to a set program. It usually consists of a laser source, a welding head, a welding platform, an automated control system and possibly auxiliary equipment. Automatic laser welder can be applied to a wide range of welding tasks, from small parts to large workpiece, and in different materials from metals to plastics.
Handheld vs Automatic Laser Welding Machines
Automatic laser welding machine for stainless steel carbon steel emphasize consistent production efficiency and welding quality, while handheld laser welding machines prioritize flexibility and adaptability, particularly suitable for scenarios that require more manual intervention and operational skills.
Usage:
Automatic Laser Welding Machine: Integrated into production lines or workstations, the welding process is controlled by an automated control system, requiring minimal manual intervention.
Handheld Laser Welding Machine: Operated by a technician, the welding process involves manually controlling the position and parameters of the welding head.
Application Scenarios:
Automatic Laser Welding Machine: Suited for mass production scenarios where welding requires high consistency, efficiency, and precision, such as automotive component manufacturing.
Handheld Laser Welding Machine: Appropriate for small quantity production, repairs, intricate-shaped workpieces, and situations demanding greater flexibility.
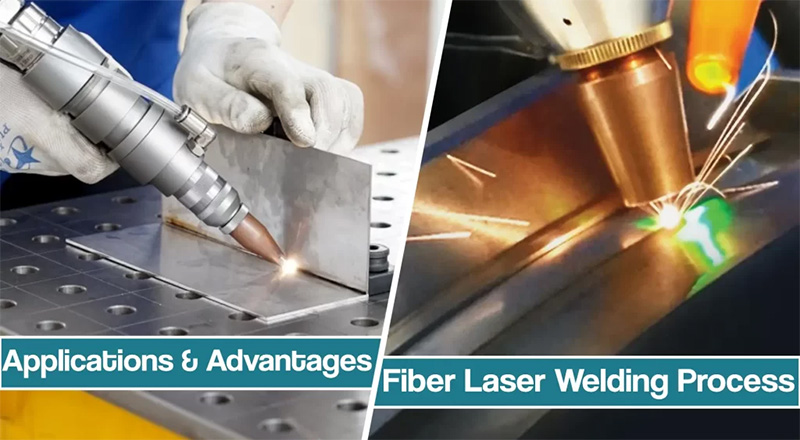
Key Features:
Automatic Laser Welding Machine: Highly automated, welding parameters and paths are pre-set, facilitating continuous and repetitive welding tasks.
Handheld Laser Welding Machine: Technicians manually control welding head position, speed, and parameters, offering more hands-on operation.
Welding Quality Control:
Automatic Laser Welding Machine: Due to automated control, welding quality remains stable and is less susceptible to human factors.
Handheld Laser Welding Machine: Welding quality is influenced by operator skills and experience, potentially resulting in some variability.
Production Efficiency:
Automatic Laser Welding Machine: Highly efficient for large-scale production, capable of continuous operation to enhance overall efficiency.
Handheld Laser Welding Machine: Generally more flexible, suitable for small-batch and intricate welding, but may be slower compared to automated equipment.
What are the Benefits of Using Automated Laser for Welding?
Enhancing Quality: Automated systems can precisely control welding parameters, achieving a high level of consistent welding quality. Compared to manual welding, this significantly reduces variations between parts, especially when part design makes proximity challenging.

Increasing Efficiency: Automated welding can operate 24/7 for continuous, high-speed welding operations, significantly boosting welding production efficiency. Robots or automated systems can work continuously without rest or fatigue, thereby reducing production cycles and delivery times.
Reducing Human Error: Manual welding can be influenced by factors such as operator skill levels, fatigue, and attention, leading to inconsistent welding quality. Automated welding diminishes human errors, ensuring the consistency of the welding process.
Lowering Costs: Shorter cycle times and extended operating hours can decrease the cost per weld, but that’s not the sole cost-saving factor. Automated welding reduces costs associated with waste and consumables. Waste drops as errors due to fatigue are eliminated. As robots use only the minimum filler material required each time, consumable usage decreases.
Flexibility and Diversity: Automated welding systems can be programmatically adjusted as needed, accommodating various welding tasks and components. This enables production lines to flexibly adapt to diverse production requirements.
Recording and Tracking: Automated welding systems can record welding parameters, process data, and quality metrics, providing robust support for quality control and tracking. This aids in promptly identifying issues and making adjustments.
Safer Working: Welders are protected from arc flash and weld heat. Automated welding keeps workers away from these dangers, creating a safer and more enjoyable work environment.
How to Use Shielding Gas Correctly In Laser Welding?
Why Use Protective Gas during Laser Welding?
Auxiliary gases play a crucial role in the laser welding process, with their impact on welding quality, weld seam formation, and metallurgical properties being of paramount significance.
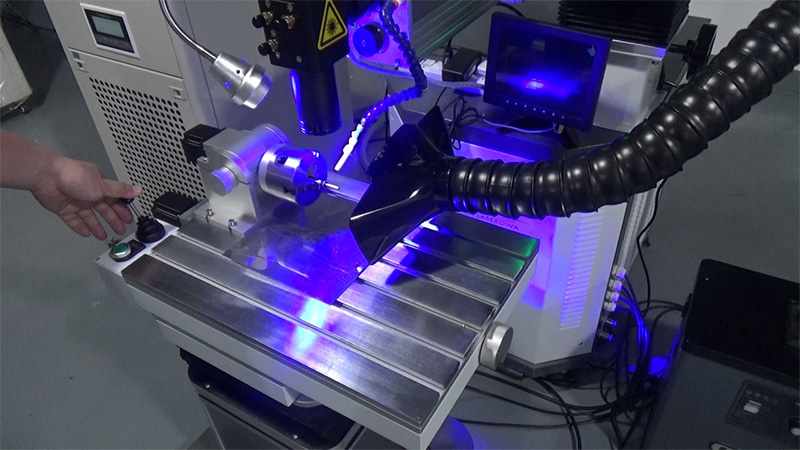
Preventing Oxidation and Contamination:
In the high-temperature molten pool of the laser welding process, metals are prone to reacting with oxygen from the surrounding air, resulting in oxidation and diminishing weld quality. Protective gases create an inert atmosphere in the welding zone, isolating oxygen from the air and thus preventing oxidation and contamination.
Reducing Porosity Formation:
Introducing protective gases into the welding zone helps prevent the formation of pores. Pores can weaken the strength and sealing of weld seams, hence using protective gases reduces pore formation and ensures a good welding effect.
Providing Cooling Effect:
Protective gases can act as coolants during welding, controlling the temperature of the welding zone and aiding in regulating the flow of the molten pool.
Preserving Focusing Lens:
High-powered lasers are employed in laser welding, generating smoke, vapor, dust, and spatter during welding. The use of protective gases effectively shields the focusing lens from contamination and spatter, thereby minimizing wear and tear.
Protecting Copper Nozzles:
The use of protective gases can moderately lower the temperature of the welding gun, serving as a heat dissipate for copper nozzles and consequently prolonging their lifespan.
Choosing the Right Shielding Gases for Automatic Laser Welding
Common protective gases used in laser welding are primarily N2 (nitrogen) and Ar (argon). Their differing physical and chemical properties result in varying effects on welding quality, weld seam formation, and material properties.
Nitrogen (N2):
Cooling Effect: Nitrogen possesses excellent cooling capabilities, allowing for rapid cooling of the welding zone, thereby controlling the geometric shape and size of the weld seam.
Welding Impact: Nitrogen primarily functions as a coolant during laser welding. It reduces the temperature of the welding zone, decreases the size of the molten pool, aiding in controlling weld depth and geometric shape. Moreover, nitrogen prevents the reaction of oxygen and moisture in the air with the molten metal, thus reducing the formation of pores and oxides.
Application Scenarios: Nitrogen is commonly used for welding stainless steel, aluminum alloys, and other materials to minimize oxidation and enhance welding quality.
Argon (Ar):
Inert Protection: Argon is an inert gas that effectively isolates oxygen and moisture from the air, preventing metal oxidation and pore formation.
Welding Impact: Argon is primarily employed as a shielding gas. It isolates oxygen and nitrogen from the air during welding, preventing metal oxidation and pore formation. Additionally, argon stabilizes the arc and provides ample cooling. In certain applications, such as deep penetration laser welding, argon can serve as an auxiliary gas to help control the shape and temperature distribution of the molten pool.
Application Scenarios: Argon is widely used for welding steel, aluminum, copper, and other materials, particularly in cases with high demands for welding quality and appearance.
Nitrogen (N2) and argon (Ar) as auxiliary gases in welding are mainly utilized to control factors like temperature, molten pool shape, and oxidation during the welding process. The choice between nitrogen and argon as a shielding gas depends on the welding material, process, and desired welding quality.
How to Add Auxiliary Gas in Laser Welding?
In laser welding, the blowing method of auxiliary gases is of paramount importance as it can influence weld quality, molten pool shape, and the formation of pores.
Localized blowing involves directing auxiliary gas through a nozzle to a specific area within the welding zone, typically above or alongside the weld seam. This helps stabilize the arc, protect the molten pool, prevent oxidation, and hinder pore formation. It is suitable for situations where precise control over weld seam shape and molten pool size is necessary, such as in fine welding applications.
Global blowing entails uniformly directing auxiliary gas from multiple directions across the entire welding zone. This effectively removes oxygen from the welding area, ensuring the entire welding process takes place within an inert atmosphere. This method is applicable in cases where welding quality requirements are not particularly stringent, providing comprehensive atmospheric protection.
Auxiliary gas is blown from one side of the weld seam to alter the airflow dynamics within the welding zone and adjust the shape and size of the molten pool. Side blowing can alter the flow characteristics of the molten pool and is occasionally employed to manipulate the geometric shape of the weld seam.
5-Axis Linked Laser Welding Machine
The 5-axis automatic laser welding machine laser welding head can be moved and oriented in five different directions. This horizontal multi-axis motion provides greater flexibility and precision in the welding process, allowing for more complex welding geometries and intricate parts.
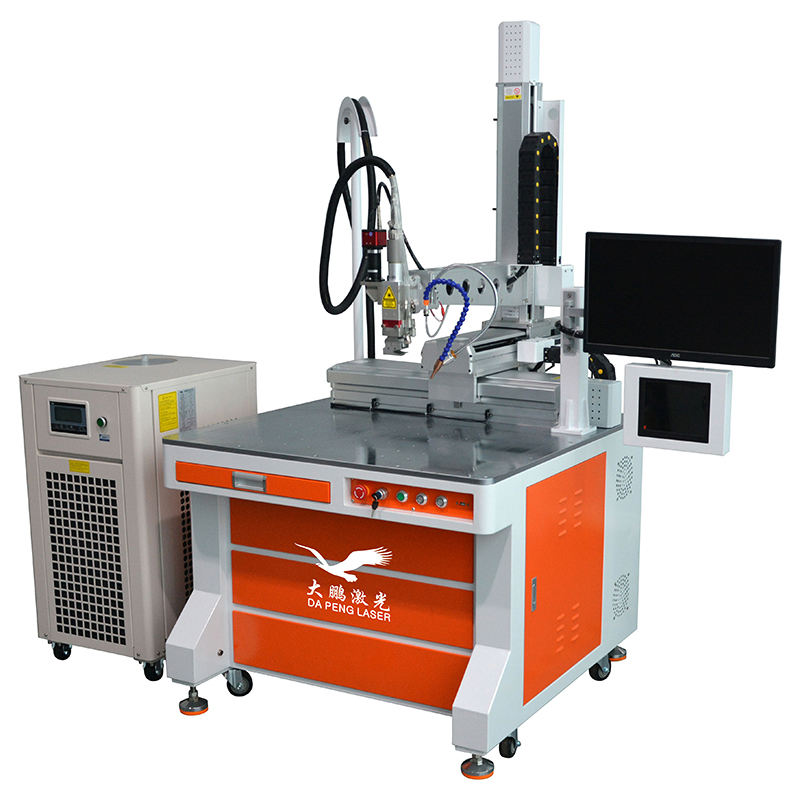
- Equipped with an automatic control system, it can automatically perform welding tasks without frequent manual intervention.
- High photoelectric conversion rate, rapid welding speed, low energy consumption, no consumables, and low operating costs.
- Excellent laser beam quality, stable energy output, and superior welding results.
- Narrow weld seams, significant depth, high precision, and a smooth, flat, and aesthetically pleasing appearance.
- Equipped with swing welding heads and the option to incorporate wire feeding devices to compensate for larger gaps in products.
- CCD sensor and observation system enable clear positioning and welding effect observation based on red light indicators.
- Professional welding software, user-friendly operation, equipped with a multi-axis motion platform, capable of welding products on any plane.
- Primarily used for continuous welding of various metal sheets (stainless steel, carbon steel, galvanized sheet, copper, aluminum alloy, etc.).
Laser Source:
Utilizes Raycus/MAX/JPT/RECI/IPG fiber laser sources for stable laser output, high photoelectric conversion efficiency, and maintenance-free operation.
Welding Head:
1. Drawer-style protective lens installation allows easy replacement of protective lenses.
2. Equipped with an infrared beam module and CCD camera module, with a high-definition CCD display screen ensuring better observation of the welding process.
3. Swing welding head suitable for a wider range of products.
4. The laser welding head can be adjusted in height, allowing convenient height adjustment as needed.
Workstation:
The entire machine features a compact and robust steel plate polished worktable structure, offering adjustable and flexible machining directions for precise control.
Multi-Axis Servo Welding Worktable:
Equipped with X/Y/Z/A/B motion axes, providing high positioning accuracy, responsive movement, and anti-vibration design, eliminating the need for manual product movement. Welding takes place through automatic movement, and an optional rotary chuck can be added to achieve 360° automatic welding.
Chiller:
Incorporates a well-known brand Hanli chiller system, featuring high flow rate, and effective cooling.
Rotary Fixture:
Enables automatic welding and user-friendly operation, enhancing work efficiency.
Optional Automatic Wire Feeding Device:
An automatic wire feeding machine that can adjust wire diameter and feed speed according to product requirements.
Professional Laser Welding Motion Control System
1. Utilizing mature solutions from industrial motion control, integrating laser welding machine and motion control into the computer interface.
2. Controlled by a PC, supported by dedicated software, easy to learn and operate. Workpieces can move along flat trajectories, welding arbitrary points, lines, circles, squares, or any flat shape composed of lines and arcs.
3. The software employs an integrated development environment (IDE) approach, with the main interface integrating graphic editing, run monitoring, programming acquisition, and motion control. The layout is clean and professional, effectively enhancing work efficiency.
4. Real-time control welding.
5. High-performance motion control for up to 5 axes, enabling spatial welding path teaching programming.
6. Offers multi-language display (Simplified Chinese, English, etc.) for international applications.
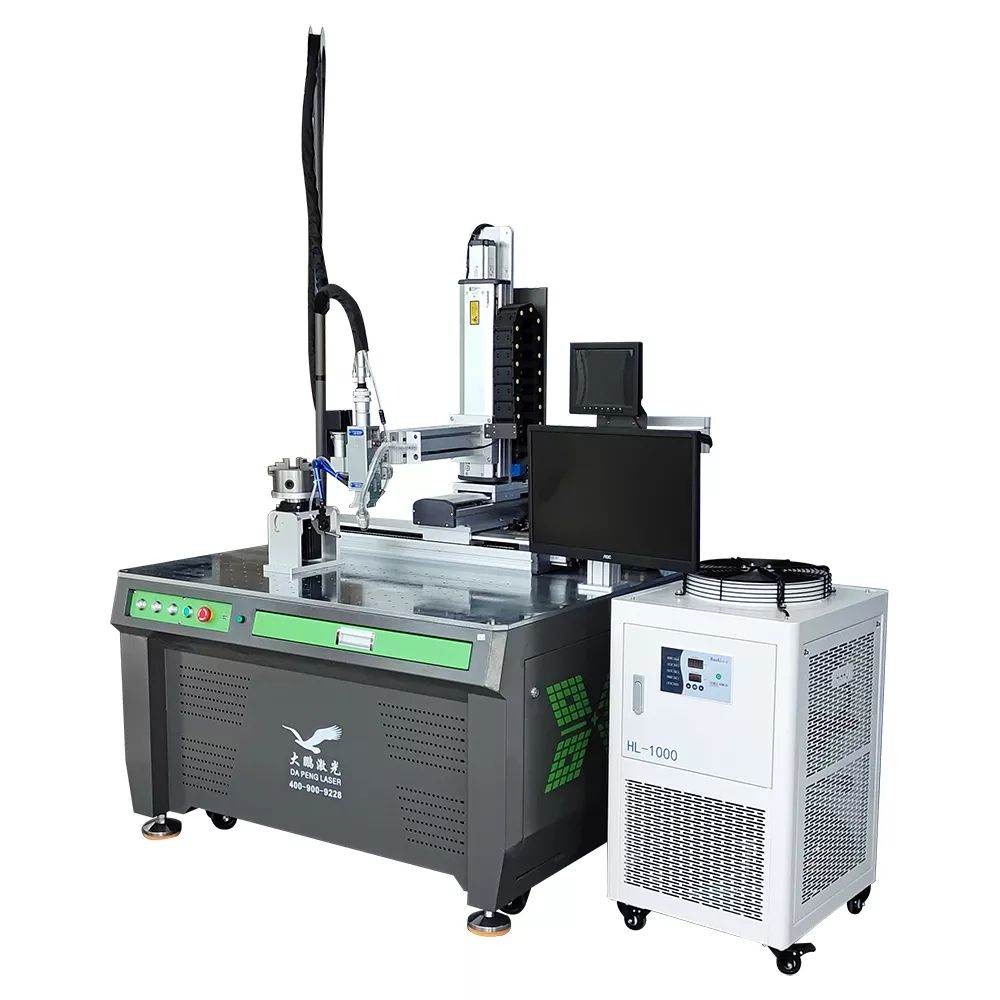
Three Axis Automatic Laser Welding Machine
Three-axis platform automatic laser welding machine is used for traditional hardware, electronic equipment, batteries and other industries laser welding equipment.
alt: 3 axis 4 axis fiber automatic laser welding machine
It possesses advantages such as high peak power, excellent beam quality, small spot size, and flexible installation.
The laser beam can achieve various spot shapes and simultaneously perform contour beam processing to meet the requirements of hybrid welding and other high-demand welding effects, achieving precise and efficient welding.
The automatic platform welding machine adopts an integrated welding module and targeting combination design, equipped with visual CCD acquisition and infrared sensors, enabling precise positioning.
The multi-axis servo welding table offers high positioning accuracy and responsive movement, incorporating anti-vibration design and eliminating the need for manual product movement, allowing for automated movement during welding.
The laser welding head can perform operations like spot welding, butt welding, overlay welding, and sealing welding on thin-walled materials and precision components.
Features:
- The welding head structure frame is customizable, effectively meeting diverse requirements based on customer costs and site conditions.
- The X, Y, and Z axis guides are equipped with vertical movement capabilities, enabling welding of irregularly shaped products. The design is customizable, detachable, and adaptable, allowing for seamless integration with production lines.
- The system employs computer-based human-machine interaction, ensuring simple and reliable operation that is easy to control.
- The welding head can swing: by deflecting the angle of the lens, it can achieve various types of optical paths.
- The equipment boasts low operational costs, minimal consumables, straightforward routine maintenance, and reduced downtime for debugging costs.
- It enables non-contact long-distance welding for areas that are difficult to approach using traditional welding methods.
- It can be applied to a wide range of materials: stainless steel, carbon steel, galvanized sheet, brass, aluminum alloy sheet, and other metals.
How to Choose Automatic Laser Welding Machine?
Choosing automated continuous fiber laser welding machine need consider several crucial factors.
Firstly, focus on the specific needs of your application. Determine the types of materials you’ll be working with and the complexity of the welding tasks.
Secondly, assess the level of automation required. Automatic laser welding machines can vary in terms of their integration into production lines and their ability to operate independently. Choose a machine that aligns with your production volume and workflow.
Thirdly, evaluate the maintenance requirements and operational costs. A machine with low consumable usage and minimal downtime for maintenance will lead to higher productivity and lower overall expenses.
Lastly, factor in customer support and training. A reputable manufacturer should offer adequate technical support and training to ensure you can maximize the machine’s capabilities.
By carefully analyzing these points, you can select an automatic continuous laser welding machine that aligns with your specific needs, enhances efficiency, and delivers high-quality welding results.
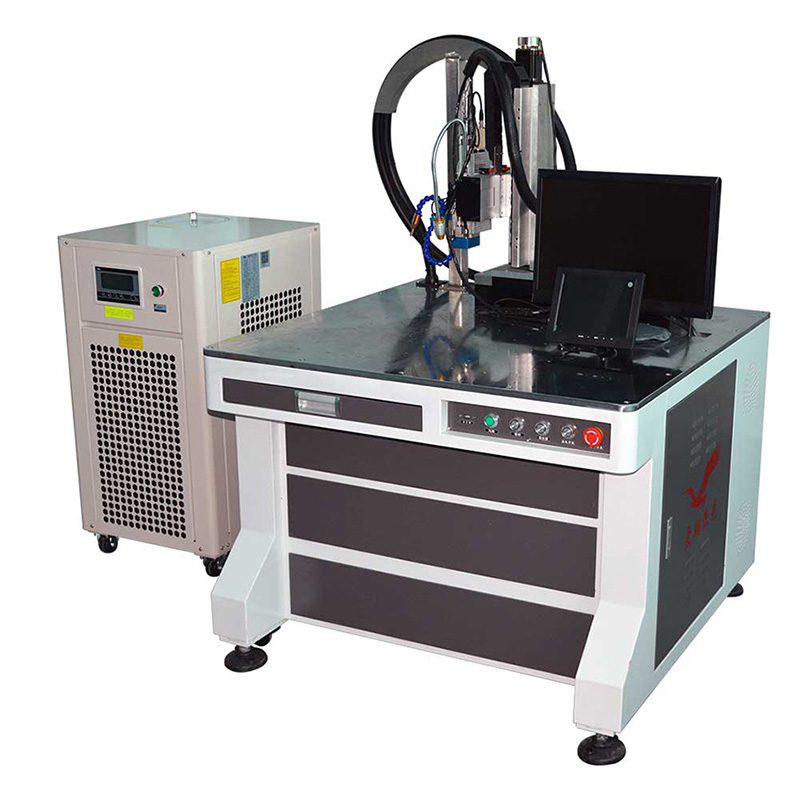
More Non-Standard Laser Welding Solutions Can Be Customized On Demand
The 5 axis platform automatic laser welding machine can be customized as laser welding machine for automotive parts, laser welding machine for lighting parts, laser welding machine for aluminum frames, laser welding machine for lithium batteries, and laser welding machine for billboards. In order to meet the needs of different application scenarios, DPLASER has created a full range of laser welding equipment, including handheld laser welding machine, automatic laser welding machine, robot laser welding machine, CW/QCW laser welding machine, jewelry laser welding machine and so on. It can be adapted to different materials for targeted operations, with a high degree of refined application.