Laser cutting machines have become indispensable tools in modern industries, enabling precise cutting, welding, and marking of materials through high-energy laser beams. With the continuous advancement of laser technology, the application of these machines has expanded from traditional metal processing to non-metal material handling, making them critical equipment in various industries. However, given the wide variety of laser cutting machines with differing performance and price points, selecting the ideal machine to meet specific needs remains a challenge for many users. This article offer laser cutter buying guide in 2025, helping users make informed decisions.
We will provide an in-depth analysis focusing on key aspects such as material type, material size, material shape, and machine configuration, offering users a comprehensive guide on how to buy a laser cutter in 2025.
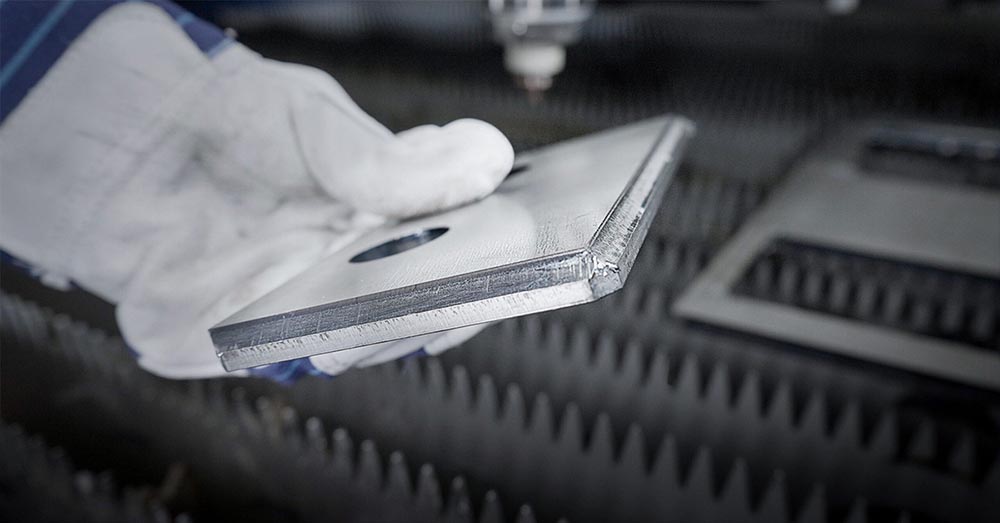
What Material Do You Want to Process?
When purchasing a laser cutter, it’s essential to choose the right type based on the materials to be processed. Fiber laser cutters are ideal for metal materials such as stainless steel, carbon steel, aluminum, and copper, offering highly efficient and precise cutting. On the other hand, CO₂ laser cutters are better suited for non-metal materials like wood, acrylic, plastic, and glass, ensuring excellent processing quality. Choosing the right machine tailored to your specific needs is a critical step in buying a laser cutter in 2025.
Material Dimensions
In addition to determining the material type (metal or non-metal), it’s crucial to define the required cutting thickness and size. These factors directly influence the choice of machine model, working area, and the number of devices needed. Fiber laser cutters can handle almost all metal materials and are commonly used for cutting carbon steel, low-carbon steel, stainless steel, steel alloys, and aluminum. Familiarizing yourself with standard market sizes (such as 3015 and 6025) can help streamline the selection process. Additionally, confirm whether the supplier offers customization options to meet unique processing needs.
The model numbers 3015 and 6025 in laser cutting machines typically refer to the size of the machine’s working table, which indicates the maximum cutting area. These numbers are expressed in millimeters (mm) and represent the dimensions of the cutting bed.
3015
Refers to a working table with a width of 3000mm (3 meters) and a length of 1500mm (1.5 meters).
This size is suitable for medium to small-scale cutting tasks, allowing for the processing of materials up to 3M by 1.5M in size.
6025
Refers to a working table with a width of 6000mm (6 meters) and a length of 2500mm (2.5 meters).
This size is typically used for larger industrial processing, capable of handling larger materials.
These model numbers help users quickly understand the machine’s cutting capacity, and they guide the selection of an appropriate machine based on material dimensions. For example, if you need to cut a 4-meter long sheet, a 6025 or larger model would be required, while a 3015 would not suffice for such a task.
Do You Need to Cut Sheets or Tubes?
1. Sheet Fiber Laser Cutting Machines
These machines are designed for high-precision cutting of flat metal or non-metal sheets. They typically feature larger work tables capable of handling materials in various sizes, offering excellent speed and precision. If your primary business focuses on sheet metal processing, decoration, signage, or similar industries, a flat sheet laser cutting machine would be an ideal choice.
- Confirm Maximum Sheet Size: Ensure the machine’s work table can accommodate the largest sheet size you need to cut.
- Choose the Right Laser Power: Select an appropriate laser power based on the typical thickness of the materials you process to ensure optimal cutting results.
- Consider Automated Loading and Unloading Systems: For improved production efficiency, consider machines equipped with automatic loading and unloading systems.
2. Tube Laser Cutting Machines
These machines are specifically designed for cutting round, square, I-beam, H-beam, or other specialized tube shapes. Tube laser cutters are often equipped with multi-chuck systems that securely clamp various diameters and lengths of tubes, enabling precise 3D cutting. In industries such as furniture manufacturing and steel structure construction, tube laser cutting machines significantly improve processing quality and efficiency.
- Confirm Maximum and Minimum Pipe Diameters: Know the range of pipe sizes the machine can handle to ensure it meets your needs.
- Check for Support for Complex Shapes: Ensure the machine can cut more complex shapes, such as bent pipes.
- Evaluate Equipment Flexibility: Assess whether the machine can quickly switch between different tube types to improve production flexibility.
3. Tube and Sheet Fiber Laser Cutting Machine
The CNC fiber laser cutting machine for tube and pipe combine the advantages of both sheet and tube laser cutting, efficiently processing flat sheets and offering flexibility for tube cutting. This versatility makes them ideal for companies that need to handle both sheet and tube cutting tasks. Opting for a combined sheet and tube laser cutting machine can save space while maintaining functionality, offering greater efficiency without compromising on performance.

Laser Cutting Quality
Cutting quality is a crucial factor when selecting a laser cutting machine, as it impacts processing accuracy, production efficiency, and the ease of subsequent operations. Here are the main factors that influence cutting quality:

1. Cutting Width
The cutting width is an essential indicator of laser cutting precision. Ideally, the cutting width should be between 0.10mm and 0.20mm. A narrower cutting width indicates that the laser cutter can perform more precise cutting, reduce material waste, and ensure that the finished product meets the required accuracy.
2. Cutting Surface Quality (Smoothness and Burrs)
The quality of the cutting surface directly affects the appearance of the product and subsequent processing. An ideal laser cut should have smooth edges and no burrs.
- Thin Material Cutting: For thin sheets, the surface smoothness is more critical, and burrs must be minimized.
- Thick Material Cutting: When cutting thicker materials, the stability of the cutting machine and power control are particularly important to ensure uniform cutting and avoid material warping and burr formation.
3. Impact of Gas Choice on Cutting Quality
The cutting gas plays an important role in the laser cutting process, and choosing the right gas can significantly improve cutting quality. Common cutting gases include:
- Nitrogen: Typically used for high-quality cuts, providing smoother edges, especially for materials like stainless steel, and reducing oxidation and burn marks. Nitrogen cutting also minimizes material deformation and keeps the cut edges clean.
- Oxygen: Used for cutting thicker materials, especially carbon steel. Oxygen cutting provides faster cutting speeds, but may leave oxidation and burrs on the cutting edges, requiring post-processing.
- Air: Compared to nitrogen and oxygen, air is more commonly used and economical but provides somewhat lower-quality cuts. The cut edges may have slight burrs or irregularities.
4. Material Deformation
High-quality laser cutting should minimize material deformation. Since laser cutting concentrates heat at the cutting point, it may cause localized thermal expansion, leading to deformation. A good laser cutting machine should have excellent heat control capabilities, effectively managing the heat-affected zone and reducing material deformation caused by thermal expansion, thus ensuring high-quality cutting results.
Single Platform vs. Exchange Platform: Which One Should You Choose?
A single-platform fiber laser cutter has only one working table, meaning the operator needs to unload finished products and load new materials during cutting, which leads to downtime and reduced production efficiency. This type is more suitable for small-batch production. In contrast, a double-platform fiber laser cutter features two independent working tables, allowing for simultaneous loading and unloading while the machine continues cutting, significantly boosting production efficiency. This setup is ideal for large-scale production but comes with a higher initial cost and requires more space.
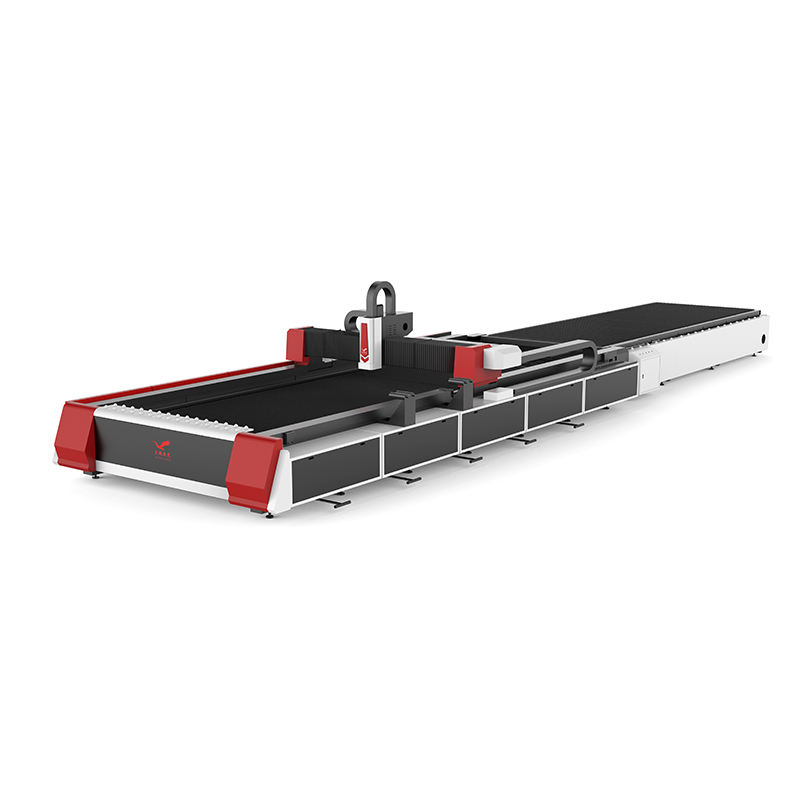
Should You Choose a Full-Closed Fiber Laser Cutting Machine?
Open laser cutters are designed for easy loading and unloading of large or bulky workpieces, offering a larger working area that is ideal for handling oversized metal sheets or complex parts. However, due to the lack of an enclosed space, they offer weaker safety features and environmental control, requiring additional safety measures. The open design may also expose the cutting process to external factors that can affect cutting precision.
In contrast, closed laser cutters have an enclosed design that limits direct access to the cutting area but effectively controls laser radiation, smoke, and debris, improving both safety and environmental control.
Laser Power Configuration
When selecting a metal laser cutting machine, the power level should be determined based on the thickness of the material to be processed. For example, for cutting metal sheets under 6mm in thickness, a machine with a power range of 1500W~3000W is recommended. The cutting speed of a laser cutter is influenced by factors such as laser power, material type, and material thickness. If you anticipate higher efficiency needs or potential changes in cutting requirements in the future, it may be wise to invest in a higher-powered laser cutter.
Key Components
- Laser Source Brand: The brand and quality of the laser source (such as IPG, Raycus, or MAX) can significantly impact the machine’s stability and longevity.
- Motors and Drive Systems: Components like the servo motors, reducers, rails, racks, gears, and ball screws affect the overall cutting precision and smoothness of operation.
- Cooling System: The cooling system’s compatibility and efficiency are crucial for maintaining optimal performance. It is recommended to use industrial-grade water chillers to ensure the best cooling effect, preventing overheating and enhancing machine longevity.

Laser Cutting System
We provide you with the CypCut laser cutting control system, one of the best in the industry. This system integrates CAD, Nesting, and CAM modules, offering features such as automatic drawing optimization, graphic cutting technology settings, production scheduling management, and compatibility with capacitors. Additionally, it supports automatic focusing, ensuring precise and efficient cutting performance.
Should I Buy a Laser Cutter?
If you regularly work with materials like metal, wood, or acrylic and need precise, high-volume cutting, a laser cutter could be a great investment. Consider your budget, available space, and whether the machine fits your business needs before making a decision.
If you’re looking to replace traditional methods like water jet cutting, plasma cutting, or flame cutting, a laser cutter is worth considering. Laser cutting typically offers superior precision, cutting speed, and surface quality compared to these conventional methods, while also reducing the need for post-processing. With continuous advancements in technology, laser cutters have become more efficient and environmentally friendly, making them an excellent modern alternative for a wide range of materials.
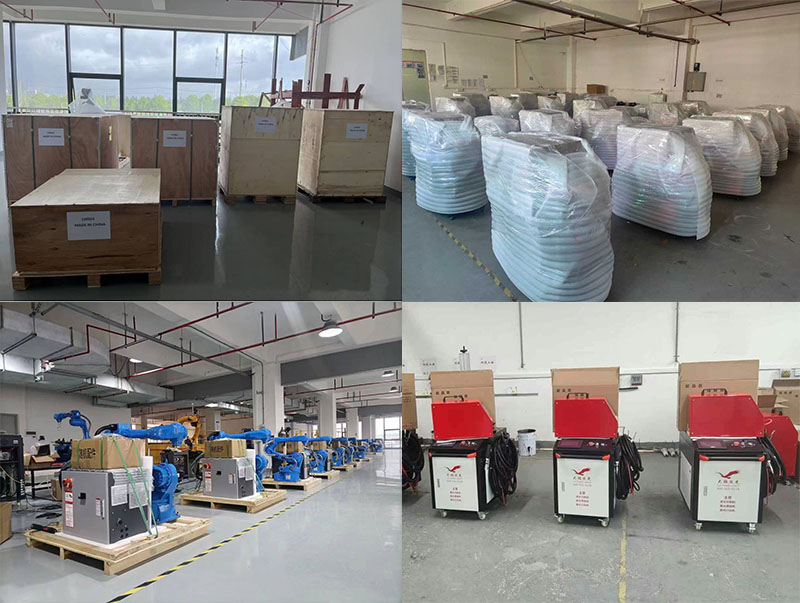
How to Choose a Laser Cutting Machine Manufacturer?
- Sample Testing and Manufacturer Technical Strength
In the initial stages of cooperation, we encourage customers to visit the High Energy Laser factory in person. Through an on-site tour, customers can gain a deeper understanding of our production capabilities and technical strength. During this visit, we will arrange dedicated staff to assist and provide free cutting sample services based on the customer’s processing requirements. This allows customers to directly evaluate our product quality and craftsmanship, ensuring that the final product meets their daily processing needs.
- Installation, Debugging, and Staff Training
From equipment production to successful delivery and commissioning, we strive to offer a seamless process for our customers. We take responsibility for the entire installation and debugging process, ensuring everything runs smoothly. At the same time, we recognize the importance of staff training, so we offer detailed training for the customer’s team, covering equipment operation, maintenance, and safety usage. Along with the equipment, we also provide a comprehensive maintenance manual and user guide to ensure customers can use our equipment reliably and sustainably over the long term.
- After-Sales Support
We place great emphasis on the stability of equipment usage and the prompt response of after-sales service. High Energy Laser is committed to providing comprehensive after-sales support, including, but not limited to, regular follow-up visits, technical support, and fast troubleshooting. These measures are designed to provide customers with a worry-free experience, allowing them to focus on developing their core business without worrying about equipment issues.
- Price
When selecting a laser cutting machine, businesses should base their decision on production needs, material type, and thickness. Generally, the higher the power, the greater the cutting capability and precision, but the price also increases. For instance, a 1000W fiber laser cutting machine is suitable for cutting 10mm carbon steel and 5mm stainless steel, with a price of around $20,000. On the other hand, a 3000W model can process thicker materials, such as 20mm carbon steel and 10mm stainless steel, but comes at a higher price. Therefore, businesses should seek the optimal balance between performance and cost based on their actual needs and budget.
Best Laser Cutting Machine for Metal
The F3015 fiber laser cutting machine for metal is specifically designed for industrial production and is highly efficient in cutting a wide range of materials. Its high-power performance allows for the simultaneous cutting of multiple layers of material, making it especially suitable for industries that require fast metal sheet processing, such as sheet metal fabrication, automotive parts production, and the home appliance industry. With its flexible design and easy-to-operate features, it can quickly adapt to varying production needs, significantly reducing processing time and improving overall production line efficiency. This makes it an ideal tool for enhancing manufacturing capabilities.
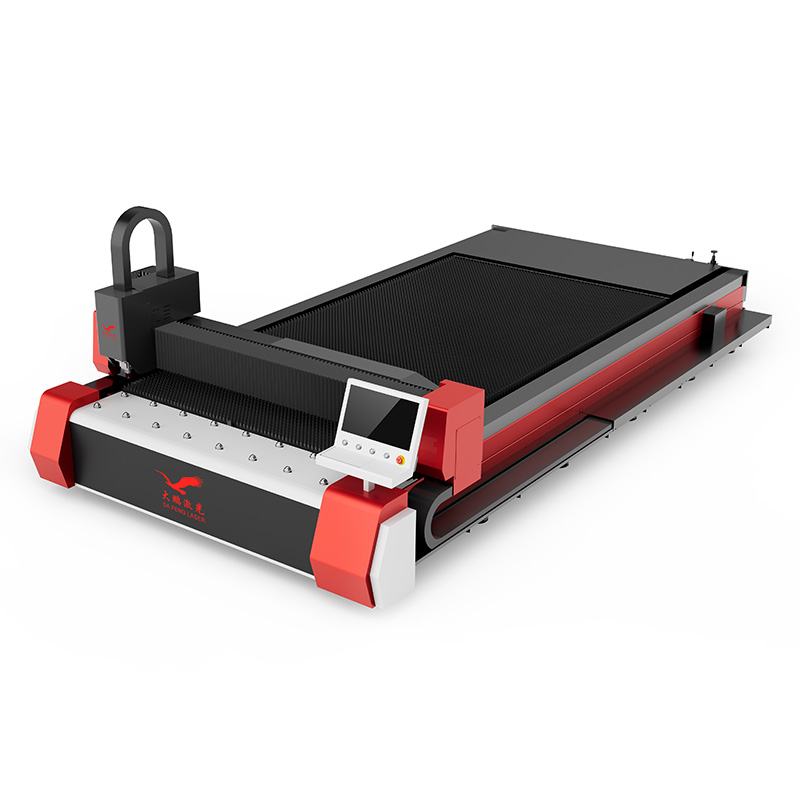
Specifications:
Worktable Size: 3000mm x 1500mm
Power Options: 1000W / 1500W / 3000W
Laser Head: WSX, RAYTOOLS, OSPR
Laser Source: MAX, Raycus
Rated Voltage & Frequency: 220V / 380V, 50Hz / 60Hz
Features:
Excellent Beam Quality: Smaller focus and finer cutting lines.
High Electro-optical Conversion Rate: Low power consumption.
Extremely High Cutting Speed: Twice the speed of comparable CO2 laser cutting machines.
High Stability: Stable performance with key components having a lifespan of up to 100,000 hours.
Low Maintenance Costs: Fiber-optic transmission eliminates the need for mirrors.
Easy Operation & Maintenance: Fiber-optic transmission requires no adjustments to the optical path.
Applications
Fiber laser cutters are highly efficient in metal sheet processing and can handle complex shapes with ease.
In the electronics industry, they are used for the precise processing of small components and enclosure materials, ensuring optimal device performance.
In automotive manufacturing, they are employed for cutting body structure parts and engine components, significantly improving both efficiency and precision.
In machinery manufacturing, they offer versatility in handling various materials and complex part designs.
Additionally, fiber laser cutters are widely used in the home appliance industry for processing enclosures and internal components, as well as in tool manufacturing for cutting blades and tool parts. They provide robust manufacturing support across a variety of industries.
Applicable Materials
Fiber laser cutting machines can cut a wide range of metal materials, including stainless steel, carbon steel, alloy steel, silicon steel, and spring steel. These materials are commonly used in industrial manufacturing, meeting requirements for strength and durability. The machine’s performance in processing light metals is equally impressive, particularly with materials such as aluminum and aluminum alloys, making it ideal for lightweight product manufacturing.
Ultrafast Laser Cutting
In addition to meeting traditional manufacturing needs, fiber laser cutting machines can also be extended to more refined applications. For heat-sensitive or transparent materials, as well as cutting requirements involving extremely small dimensions, ultrafast laser technology is the ideal choice. Ultrafast lasers offer extremely short pulses and low heat impact, ensuring that materials remain undamaged. This makes them well-suited for high-precision micro-machining tasks
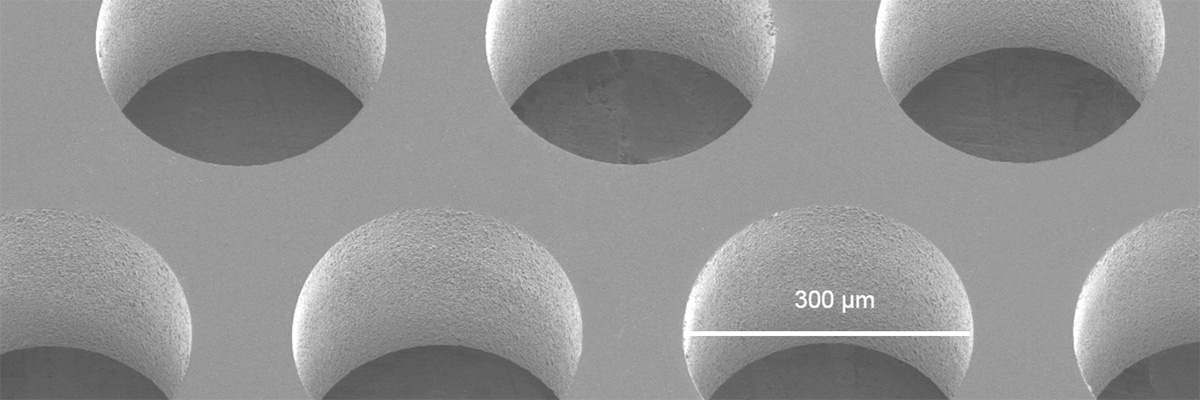
Applications of Ultrafast Lasers
Precision Marking: Laser marking can permanently and accurately mark electronic components, including serial numbers, barcodes, and logos. This is essential for traceability, inventory management, and quality control.
Fine Cutting: Lasers can cut complex shapes and patterns in precision electronic components, while minimizing the heat-affected zone (HAZ) to reduce the risk of damage.
Micro-Machining: Laser technology can create micro-features on electronic components, such as FCB and connectors, which are crucial for high precision applications.
Ultrafast laser technology ensures that even the most delicate materials are processed with high precision, making it ideal for industries requiring extreme accuracy and minimal material distortion, such as electronics and semiconductor manufacturing.
In conclusion, purchasing the best laser cutting machine for metal in 2025 requires careful consideration of various factors, from the materials you plan to process to the specific features you need for your projects. Selecting the right laser cutting machine can be challenging due to the variety of options, but understanding specific needs—such as material type, speed, and precision. Whether you’re focused on material size, the benefits of a single or dual platform, or deciding between an open or enclosed system, making an informed choice will ensure your investment supports your business effectively.