Laser welding technology has emerged as a standout in modern industrial manufacturing due to its exceptional precision and efficiency. By focusing a high-energy-density laser beam, this process rapidly heats metallic materials to their melting point within a highly localized area, achieving precise and robust welding results. Compared to traditional arc welding methods, laser welding offers superior processing accuracy, faster welding speeds, and a smaller heat-affected zone. Furthermore, it is capable of handling more complex geometries and diverse material combinations, making it widely adopted across various industrial applications. However, despite its numerous advantages, laser welding is not without limitations. This article explores both the advantages and disadvantages of laser welding.

How Does Laser Welding Work
Laser welding operates by utilizing a high-energy-density laser beam to locally heat materials. When the laser beam strikes the surface of the welding material, it is absorbed and rapidly converted into thermal energy, causing the material to heat up to its melting or boiling point within a very small area, forming a molten pool. Due to the laser beams highly concentrated energy, the melting process can be precisely controlled, ensuring exceptional welding accuracy. As the laser beam moves along the predetermined path, the molten material cools and solidifies, creating a strong weld joint.
This innovative welding process is particularly suited for thin-walled products and precision components. It can accommodate various welding techniques, including spot welding, butt welding, overlay welding, and seal welding.
What are the Benefits of Laser Welding?
There are numerous pros and cons of laser welding, making it a versatile yet complex process in modern manufacturing. This technique is known for its precision and ability to handle a variety of materials, but it also comes with certain limitations. The following section will delve into the key benefits of laser welding, highlighting how it improves efficiency, quality, and flexibility in various industrial applications.
High Efficiency and Low Deformation
Laser welding can complete welding tasks at extremely fast speeds. Due to its high energy density and precise energy control, the heat input to the material is minimal, resulting in significantly reduced deformation in the welded area. This makes it ideal for fully automated welding production of mass-produced products.
Simple and User-Friendly
Laser welding systems are equipped with simple configurations and intuitive control systems, making them capable of handling a variety of complex welding needs. From thin sheets to thick plates, and from pipes to corner welds, the process can easily accommodate different forms of welding.
High Power Density
Laser welding offers a high depth-to-width ratio, reaching up to 5:1 or even 10:1, which enables efficient energy use and deeper penetration in the weld.
Capability for Micro Welding
The focused laser beam creates a very small spot size and can be precisely positioned, making it ideal for micro and small components in large-scale automated production.
Precision Positioning & Minimization of Heat-Affected Zone (HAZ)
By focusing the laser beam, laser welding can achieve micron-level spot sizes and extremely precise position control. Additionally, because the thermal effects are confined to a small area, the process effectively minimizes the risk of deformation or other adverse effects caused by heat.
Time and Space Divisible Capability
Laser welding systems can divide the laser beam in both time and space. This means that the same laser can be split into multiple beams at different time points or spatial locations, enabling simultaneous multi-position processing and greatly enhancing production efficiency.
Wide Material Applicability
Laser welding can be used on a wide range of materials, including stainless steel, aluminum alloys, and titanium alloys. Whether welding similar or dissimilar materials, laser welding provides reliable solutions. It can be applied to various metals and non-metals, from thin sheets to thick plates, offering more possibilities in industrial manufacturing.
When discussing advanced laser welding technology, it is important to highlight its significant advantages while also fairly analyzing its drawbacks to provide a comprehensive and balanced evaluation.

What Are the Disadvantages of Laser Welding?
Laser welding, known for its precision and efficiency, is widely used in various industries. However, despite its many advantages, there are certain disadvantages of laser welding. Understanding these disadvantages is crucial for making informed decisions in practical applications, ensuring a balance between welding quality and production efficiency.
High Precision Requirements
Laser welding demands high assembly precision for workpieces. Any misalignment or deviation can compromise the welding quality, affecting the final product. To achieve efficient and stable automated welding, products must meet strict consistency and precision standards.
High Initial Equipment Costs
The upfront investment for laser welding systems is substantial. This includes the cost of the laser source, optical system, control system, and auxiliary equipment. Such high costs increase financial pressure on businesses and may pose an entry barrier for small and medium-sized enterprises.
High Maintenance Costs
Laser welding equipment requires regular inspection, calibration, and part replacement, resulting in higher maintenance expenses compared to traditional welding methods.
Safety Concerns
The laser beam used in welding poses potential risks to human safety, necessitating strict safety measures such as wearing protective goggles, using appropriate ventilation systems, and adhering to safety protocols. Additionally, the process may generate harmful substances, such as splatter and fumes, which require effective protective measures.
Welding Defects and Quality Control
Issues such as splatter, cracks, porosity, and discontinuities in the weld seam can occur. Precise control of welding parameters and processes is necessary to ensure consistent welding quality.
Limited Penetration Depth
Laser welding has limited fusion depth, making it less suitable for thick materials. Welding deeper sections may exceed the capabilities of laser welding machines. Before starting a project, it is crucial to evaluate the materials and consult laser welding experts to determine the most suitable welding method.
Maximum Thickness
Laser welding is typically ideal for thin to medium thickness materials. For components thicker than 6mm (specific maximum thickness depends on the welding process, materials, and equipment), traditional methods like arc welding may be more appropriate.
Limited Material Range
Materials with high reflectivity, such as aluminum and copper, reflect a significant portion of the laser beam, reducing efficiency. Additionally, high thermal conductivity materials dissipate heat quickly, making proper penetration difficult to achieve.
Automation and Customization Needs
For complex and hard-to-reach welding areas, specialized fixtures and jigs are often required to ensure precision and stability. To meet higher automation demands, multi-axis laser welding systems can be employed. These systems offer flexible, multi-degree-of-freedom motion capabilities, enabling the handling of intricate welding tasks with ease.
By considering these limitations, manufacturers can better assess whether laser welding is the most appropriate solution for their specific applications.

How to Solve the Difficulties of Laser Welding Reflective Metal
High-Performance Laser Welding Machine
Choose high-performance laser welding equipment, such as high-power lasers and precision focusing systems, to enhance welding accuracy and stability, ensuring consistent and reliable results.
Surface Pretreatment
Apply appropriate surface pretreatment methods, such as mechanical polishing, chemical etching, or coating with special materials, to improve the laser absorption rate of aluminum alloys, thereby boosting welding efficiency and quality.
Welding Parameter Optimization
Adjust welding parameters, including laser power, waveform, and focal position, to effectively control heat input and minimize the occurrence of porosity and thermal cracking. For pulsed lasers, fine-tune the pulse waveform to precisely regulate heat input, further enhancing welding quality.
Shielding Gas
Use suitable shielding gases (e.g., argon or nitrogen) during the laser welding process to reduce oxidation and the formation of pores.
Filler Wire Welding:
Employ automatic filler wire feeding to improve the composition of the weld metal, lower the risk of thermal cracking, and enhance the strength and reliability of the weld joint.
Monitoring and Control Systems
Utilize modern welding monitoring and control systems to track parameter variations in real time during the welding process. Implement automated adjustments when necessary to ensure process stability and consistent quality control.
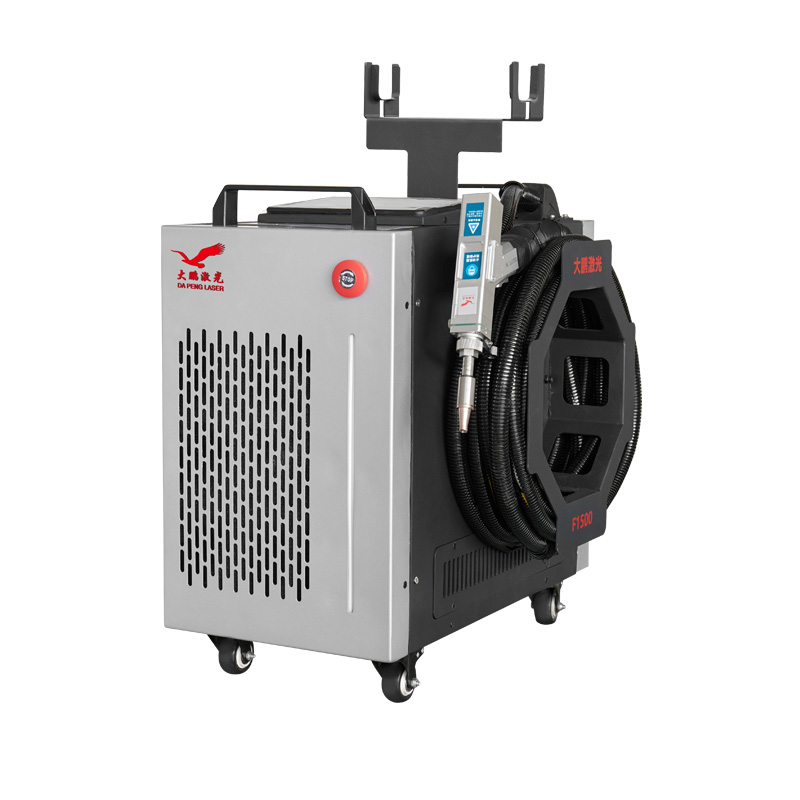
2024 The Best Portable Laser Welding Systems
Portable laser welding systems are designed with an intuitive, user-friendly interface, requiring only two hours of training to master. This significantly reduces labor costs.
Powerful Laser Beam
The laser welding machine delivers highly concentrated beam energy, ensuring efficient welding performance. It achieves precise welds at remarkable speed while maintaining a minimal heat-affected zone, producing smooth, aesthetically pleasing seams and reducing the need for post-processing.
Versatile Material Compatibility
These systems are compatible with various metals, including stainless steel, carbon steel, galvanized steel, and aluminum alloys, making them suitable for a wide range of industrial applications.
Compact and Flexible Design
Handheld welding machines eliminate the need for fixed workstations, offering a compact design that saves space and provides exceptional operational flexibility. The included long fiber-optic cable enables free movement across a wide area, allowing for easy operation in complex or confined spaces.
Built-in Cooling System
An integrated cooling system ensures the laser source operates stably under high-load conditions, maintaining efficiency during extended usage.
Multi-Functionality
Beyond core welding tasks, the handheld device supports rust removal and cutting functions, which can be achieved by simply switching nozzles. The fiber laser source boasts excellent durability with an expected lifespan of up to 30 years, ensuring long-term cost-effectiveness.
Extensive Welding Capabilities
These systems are highly versatile, capable of performing a variety of welding tasks, including spot welding, seam welding, lap welding, T-joint welding, corner welding, groove welding, seal welding, and intricate irregular joint welding. They accommodate diverse material and welding requirements, making them ideal for both precision welding and mass production scenarios.
Broad Range of Applications
Fiber laser welding machines are widely used across various industries. In jewelry processing, they enable the welding of intricate metal components, ensuring precise, aesthetically pleasing, and durable joints. In the electronics industry, they meet the demands for high-precision, low-heat-impact welding, and significantly enhancing product reliability. In mechanical manufacturing, these systems efficiently handle the welding of large structural components and complex parts, improving both production efficiency and weld quality. Additionally, they are extensively applied in the fabrication of signage, doors, windows, cabinets, and construction materials, making them indispensable in the metal manufacturing sector.

How to Choose the Right Laser Welding Machine for Your Business
Before purchasing a laser welding system, there are four key factors you should carefully consider:
- Type of Laser Welding Machine
Depending on your production needs, laser welding machines are generally categorized into automated robotic systems and handheld models. If your production volume is high and efficiency is a priority, a robotic automation laser welding machine would be the ideal choice. For small and medium-sized businesses or customized, low-volume production tasks, a handheld laser welding machine is more practical and cost-effective.
- Laser Power
The power of the laser directly affects the welding depth and efficiency. High-power lasers provide deeper welding capabilities but come at a higher cost. For welding materials with thicknesses between 0.5 mm and 3 mm, a 1000W laser is typically sufficient. For deeper welds or materials requiring higher performance, opt for equipment with a power range between 1500W and 3000W to meet more demanding requirements.
- Laser Configuration Options
The configuration of the laser welding machine should be chosen based on the specific application and industry requirements. For instance, jewelry welding often demands high-precision, small laser systems, while galvo laser welding is suitable for large-scale, high-efficiency tasks. Laser welding machines with different configurations come at varying price points, so you should balance your intended use with your budget.
- Production Costs and Benefits
Although laser welding equipment involves a high initial investment, its efficiency and quality in mass production can significantly reduce long-term per-unit manufacturing costs. If your goal is to enhance production capacity and optimize costs, a handheld laser welding machine offers a cost-effective solution while fulfilling a variety of production needs.
By thoroughly evaluating these factors, you will be able to select the ideal laser welding equipment that not only meets your production demands but also aligns with your budget.
In conclusion, while laser welding offers excellent weld quality and efficiency, it’s important to understand its limitations, such as high equipment costs, restrictions with highly reflective materials, and thickness limitations. This article addresses what is the problem with laser welding and provides insights to help businesses make more informed decisions and adopt the right solutions to enhance their manufacturing capabilities.