Handheld fiber laser welding machine has gained immense popularity in various industries due to its precision and efficiency. However, like any other welding technique, it is not immune to challenges and issues that may arise during the welding process. This comprehensive laser welding troubleshooting aims to address common problems encountered with handheld laser welding machines, welding-related complications, and issues concerning the quality of welds.
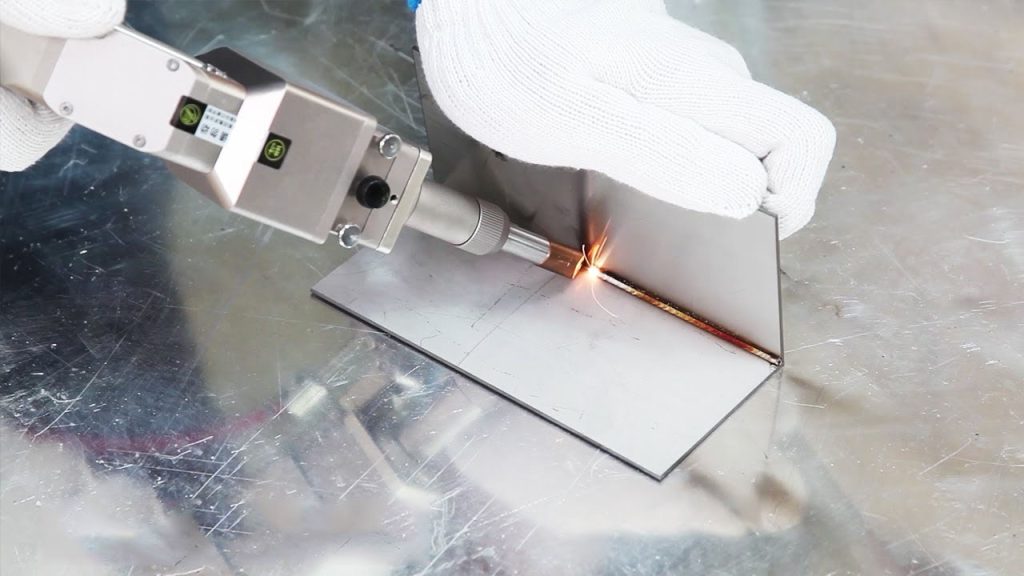
Advantages of Handheld Laser Welding
Laser welding is highly efficient
The laser can be concentrated in a small area to produce high energy density, so the welding process can be completed in a short period of time. Laser welding is faster and more productive than traditional welding methods.
Laser welding offers precision
The laser beam can be highly concentrated, and the small size of the focal point enables fine welding, which is especially suitable for parts that require high welding quality and appearance. Moreover, laser welding has a small heat-affected area on the material, which reduces distortion and heat effects.
Handheld laser welding machine is easy to use
Compared with other welding methods, laser welding does not require contact with the weld material and avoids contamination and damage that may occur in conventional welding. The operator only needs to control the parameters of the laser to complete the welding process.
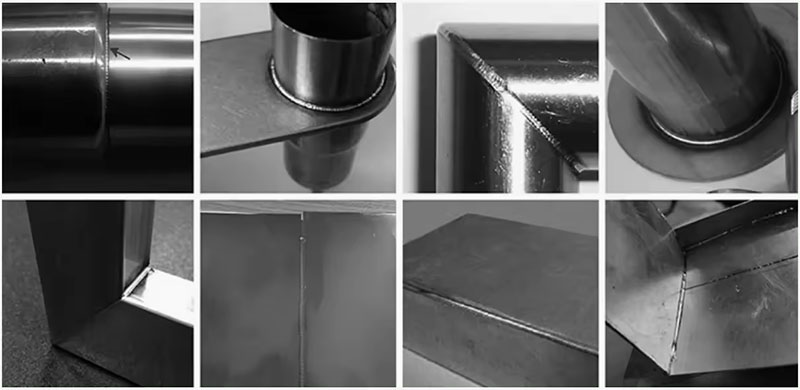
Laser welding is a technique of welding based on a high energy density laser beam. It has many advantages that make it widely used in various industries. In electronic parts manufacturing, laser welding enables assembly and joining of tiny sizes. In automotive manufacturing, laser welding can be used for body welding, parts assembly and other processes. In the aerospace field, laser welding can realize the welding of high-strength and lightweight materials.
In the process of using the laser welding machine, sometimes the operation or parameter settings and other reasons, resulting in some failures. Of course, in order to make the laser welding machine work better, reduce the number of failures and improve work efficiency, understanding these failures and their processing methods can help you better solve the laser welding machine problems and improve work efficiency.
Process Parameters Affecting the Laser Welding Quality
Laser welding process parameters have an important impact on the welding quality, by reasonably adjusting these parameters and combining with the actual application requirements, the laser welding process can be optimized to improve welding quality and efficiency.
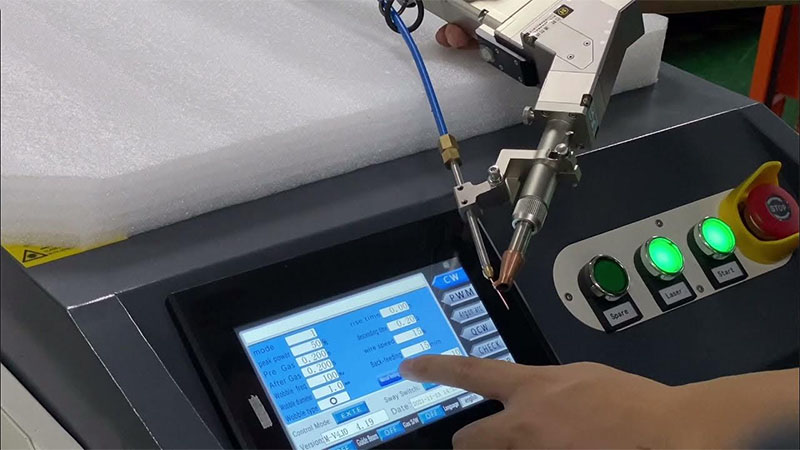
1. Power Density
Power density in laser welding refers to the energy distribution of the laser beam per unit area in the welding area. Higher power density can heat the material to the boiling point in a very short time, generating a large amount of vapor, suitable for material removal processing, such as punching, cutting and engraving. The lower power density, the heating time is relatively long, the bottom temperature may have reached the melting point, in favor of the formation of a good melt welding.
2. Laser Pulse Waveform
Laser pulse waveform refers to the pattern of change of laser intensity with time. In the laser welding process, the reflectivity of the metal surface will change with the temperature changes, resulting in the loss of laser energy. This is especially important for thin-film welding, as higher reflectivity may lead to welding defects. Therefore, designing the right laser pulse waveform can improve weld quality.
3. Laser Pulse Width
The laser pulse width is the time duration length of the laser pulse. It affects the melting and vaporization of the material during the welding process on the one hand, and determines the cost and size of the laser welding equipment on the other. Selecting the appropriate pulse width can realize the desired processing effect and meet the actual application requirements of the equipment.
4. Laser Focus
The position of the laser focus has a great influence on the quality of the weld. In the vicinity of the focal point, the power density of the laser beam is very high, which can lead to porosity in the material. Therefore, it is common to move the focal point slightly out of focus to obtain an area of even power density distribution. The amount of defocusing should be optimized for the specific welding material and requirements to achieve the best weld quality.
5. Focus Position
The focus position is the position of the laser beam focus point relative to the weld surface. By adjusting the focus position, the weld depth and weld width can be controlled. In general, the focus position should be properly moved away from the weld surface to obtain a uniform weld and a lower risk of porosity.
6. Scanning Speed
Scanning speed refers to the speed at which the laser welding head moves during the welding process, usually expressed in millimeters per second (mm/s). The selection of scanning speed should take into account factors such as the thermal conductivity of the welding material, the welding depth and the quality requirements of the weld.
By reasonably adjusting these parameters and combining them with practical application requirements, the laser welding process can be optimized to improve welding quality and efficiency. Of course, in practice, there may be more parameters to consider, so comprehensive consideration of various factors to achieve the best welding results.
How to Solve the Laser Welding Issue?
Common problems and solutions for handheld welding machines we will divide into three parts, equipment startup problems, common equipment problems and weld quality problems. By examining each problem category, we will explore the underlying causes and present effective solutions to overcome these issues. Furthermore, practical tips and best practices will be provided to ensure a smooth welding experience and achieve optimal results.
Part 1: Laser Welding Machine Common Faults & Solutions Before Starting
1. Equipment cannot start (power)
Solution: Check whether the power cord switch is powered.
2. Lights cannot be lit
Solution: Check the pre-fire board with or without 220V voltage, check the light board; 3A fuse, xenon lamp.
3. The light has been lit, no laser
Solution: Observe the handheld laser welding machine part of the display out of the light is normal. First of all, check the CNC part of the laser button is closed, if closed, then open the laser button. If the laser button is normal, open the numerical control display interface to see whether the setting for continuous light, if not, then change to continuous light.
Part 2: Laser Welding Machine Common Problems and Solutions When Welding
1. Unstable laser power
If the laser power is unstable, it may be caused by high temperature of the laser or contamination of the optical components.
Solution: clean the optical components, check the cooling system and the power supply, etc.
2. Poor weld quality
If the quality of the weld seam is poor, it may be caused by incorrect setting of parameters such as welding speed, focal length and laser power.
Solution: Adjust the welding parameters, check the quality of the welding head, etc.
3. Inaccurate beam focusing
If the beam is not focused accurately, it may be caused by incorrect positioning or damage to the optics.
Solution: recalibrating the optics, replacing damaged components, etc.
4. Cooling system failure
If the cooling system malfunctions, it may be due to insufficient cooling water flow, excessive cooling water temperature, etc.
Solution: Check the cooling system piping, clean the cooling system, adjust the water flow, etc.
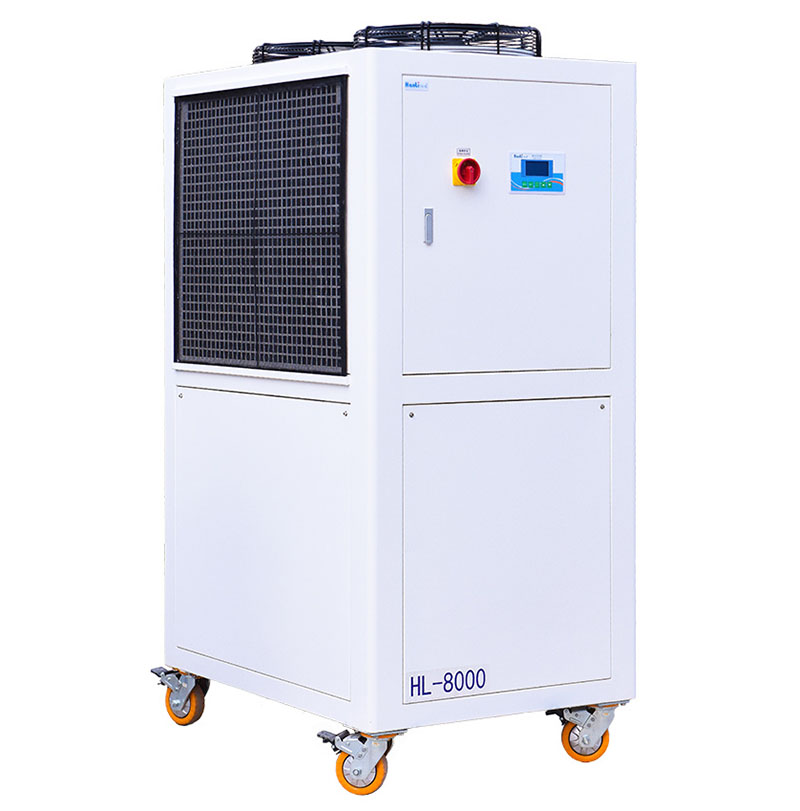
5. The weld seam is black
1) The protective gas is not open, as long as the nitrogen gas is opened, it can be solved.
2) The airflow direction of the protective gas is wrong, the airflow direction of the protective gas should be made opposite to the movement direction of the work piece.
6. Lack of penetration in welding
1) Lack of laser energy can improve the pulse width and current.
2) The focusing lens is not the correct amount, to adjust the focusing amount close to the focusing position.
7. Weakening of the laser beam
1) If the cooling water is contaminated or has not been replaced for a long time, it can be solved by replacing the cooling water and cleaning the UV glass tube and xenon lamp.
2) The focusing lens or resonant cavity diaphragm of the laser is damaged or polluted, it should be replaced or cleaned in time.
3) Move the laser in the main optical path, adjust the total reflection and semi-reflection diaphragm in the main optical path, check and round the spot with image paper.
4) The laser does not output from the copper nozzle below the focusing head. Adjust the 45-degree reflective diaphragm so that the laser is output from the center of the gas nozzle.
8. Welder suddenly does not output laser
Check whether the pre-fire plate fuse is damaged; check whether there is a power failure; whether the laser cavity is leaking, etc.
Part 3: Laser Welding Quality Problems and Solutions
1. Welding spatter
After laser welding is completed, many metal particles appear on the surface of the material or work piece, attached to the surface of the material or work piece
Reason for spattering: the surface of the processed material or work piece is not clean, there is oil or pollutants, it may also be caused by the volatilization of the galvanized layer.
1) Pay attention to cleaning the material or work piece before laser welding;
2) Spatter is directly related to power density. Appropriate reduction of welding energy can reduce spatter.
2. Cracks during welding
1. If the cooling speed of the workpiece is too fast, the temperature of the cooling water should be adjusted on the fixture to increase the water temperature.
2. When the workpiece fit gap is too large or there is burr, the machining precision of the workpiece should be improved.
3. The workpiece has not been cleaned. In this case, the workpiece needs to be cleaned again.
4. The flow rate of protective gas is too large, which can be solved by reducing the flow rate of protective gas.
3. Pore on the weld surface
Reasons for the generation of porosity:
1) The laser welding molten pool is deep and narrow, and the cooling rate is very fast. The gas generated in the molten pool is too late to overflow, which can easily lead to the formation of porosity.
2) The surface of the weld is not cleaned, or the zinc vapor of the galvanized sheet is volatilized.
Clean the surface of the workpiece and the surface of the weld before welding to improve the volatilization of zinc when heated.
4. Poor bonding of the weld to the base material and beveling
Reason:
1) If the welding speed is too fast, the liquid metal in the weld will not be redistributed on the backside of the hole, and biting edges will form on both sides of the weld.
2) If the joint assembly gap is too large, the molten metal in the joint filler will be reduced, and edge biting will also occur easily.
3) At the end of laser welding, if the energy drop time is too fast, the hole will be easy to collapse, which will also cause localized biting edges.
Solution:
1) Control the matching of laser welding machine processing power and speed to avoid biting edges.
2) Weld biting edges found in the inspection can be polished, cleaned and repaired to meet the requirements of the acceptance criteria.
5. Weld buildup
The weld is obviously overfilled, and the weld is too high when filling the weld.
Reason for weld buildup: welding wire feeding speed is too fast or welding speed is too slow.
Solution: Increase the welding speed or reduce the wire feeding speed or reduce the laser power.
6. Insufficient penetration of laser welding machine
1. Insufficient laser energy can improve the pulse width and current.
2. The focusing lens is not the correct amount of focusing, should adjust the amount of focusing too close to the focusing position.
7. Welding deviation
The weld metal will not solidify in the center of the joint structure.
Reason for deviation: Inaccurate positioning during welding, or inaccurate filling time and wire alignment.
Solution: Adjust the welding position, or filler time and wire position, as well as the position of the lamp, wire and weld.
8. Denting appear on the weld metal surface
Reason for denting: When brazing, the center of the weld spot is bad. The center of the spot is close to the lower plate and deviates from the center of the weld, causing some of the base metal to melt.
Solution: Adjust the light wire matching.
9. Poor weld molding
Bad weld ripple, uneven and untidy weld, uneven transition between weld and base material, bad weld, uneven weld.
The reason for this situation: Weld brazing, wire feeding is not stable, or light is not continuous, etc..
Solution: Adjust the stability of the equipment.
10. Weld channel
When the trajectory of the weld varies greatly, the corners are prone to weld channel or uneven molding.
Reason: The weld trajectory varies greatly and is uneven.
Solution: Weld under the best parameters, adjust the angle of view to make the corners coherent.
11. Surface slag entrapment, which mainly appears between layers
Surface slag entrapment causes:
1) When multi-layer multi-pass welding, the coating between layers is not clean; or the surface of the previous weld is not flat or the surface of the weld does not meet the requirements.
2) Improper welding operation techniques, such as low welding input energy, welding speed is too fast.
Solution:
1) Choose reasonable welding current and welding speed, and the interlayer coating must be cleaned when multi-layer multi-pass welding.
2) Grind and remove the weld with slag on the surface, and make up the weld if necessary.
Part 4: Other Accessories – Handheld Laser Welder Common Problems and Solutions
1. Failure of safety protection device
The safety protection devices of the laser welding machine include the welding chamber door, gas flow sensor, temperature sensor and so on. If these protective devices fail, it will affect the normal use of equipment, and even cause injury to the operator.
For the safety protection device error, you should stop operation immediately and notify the professionals for overhaul and replacement.
2. Wire feeder jamming
If there is a wire feeder jam this situation, the first thing we need to do is to check whether the gun nozzle is clogged, the second step is to check whether the wire feeder is clogged and there is the silk disk rotation is normal.

To gain a proper understanding of the defects in the laser welding process and comprehend the reasons behind different defect occurrences. When dealing with laser welding machine malfunctions, it is recommended to first carefully read the user manual and strictly follow the operating procedures. If faced with complex malfunctions or unresolved problems, it is advisable to contact the supplier or professional technicians of the laser welding machine for consultation and repair.
Laser Welder Troubleshooting Video Guide
DPLASER is a leading industrial laser equipment manufacturer in China. We are dedicated to providing comprehensive laser equipment solutions to our customers, including design, research and development, sales, and service. If you encounter any difficulties while using the handheld laser welder, please feel free to leave a message on the website or contact us via whatsapp.
DP LASER YouTube channel is a valuable resource for obtaining knowledge about laser welding equipment. Here, you can find a wealth of content related to laser welding equipment, including troubleshooting, usage tips, recommendations, how-to’s and user guides.
Whether you are a beginner or an experienced professional, our videos can help you understand the latest laser welding technology, solve common issues, and even master advanced techniques.
Stay tuned as we dive into the various troubleshooting for handheld Laser welding machine and empower you to tackle challenges head-on, resulting in improved welding performance and exceptional weld quality.