In this article we will share a professional laser cutting machine maintenance checklist and practical advice to help you maximize the life of your equipment and ensure that it operates at peak performance levels. Whether you are a user of a fiber laser cutting machine or a maintenance professional, this article will provide you with the critical knowledge you need to keep your equipment working efficiently and providing solid production support.
The Laser Cutting Machine Maintenance Guide
During the use of the laser cutting machine, dust and debris will be generated. With the accumulation of the use of time, the parts will also appear loss. So when we use the laser cutting machine, we should pay attention to the daily laser cutter maintenance to ensure that the accuracy of laser cutting is maintained at a high level.
- Cleaning the Laser Cutting Machine
Regularly clean the exterior of the laser cutting machine to keep it free from dust and debris, preventing any interference with its normal operation. Pay special attention not to wipe the area near the laser cutting head during cleaning to maintain cutting quality.
- Machine Bed and Rails Maintenance
Maintain machining accuracy by ensuring the linear guides of the machine bed have high guiding precision and smooth motion. Periodically check if the X, Y, Z axes can return to the origin and inspect the rails’ straightness and the machine’s perpendicularity. If there’s an issue with axis return, check the origin switch position and perform timely maintenance and debugging. Clean oil stains and foreign objects on the rack and rails by opening the dust cover. Use diesel for cleaning, then move the machine bed to flush out debris inside the slider. After cleaning, wipe off excess diesel and apply a layer of gear lubricating oil.

- Inspection of the Transmission System
Regularly inspect the transmission system, including motors and gearboxes, to ensure proper functioning. Keep the transmission system clean to prevent foreign particles from entering. Check the coupling between the motor
- Cleaning the Exhaust Fan
The exhaust fan on your laser engraver helps prevent dust and debris from building up inside the machine. To clean it, you will need to remove the fan cover and carefully remove any carbon or dust from the fan blades with a brush or compressed air.
- Routine Check of the Laser Source
The laser generator should undergo maintenance before daily startup:
- Check the cooling water pressure daily to keep it between 3.5 and 5 Bar.
- Check the temperature of the cooling water daily to the temperature of the water required by the selected laser.
- Regularly check the filter of the chiller for impurities.
- Check the laser cooling water circuit for impurities.
- Regularly check whether there is corrosion in the cooling water circuit of the laser head of the laser, if there is, then treat or replace the tube in time.

- Laser Cutting Head
The laser cutting head is a critical component of the laser cutting machine, requiring regular checks to ensure its proper functioning.
- Before each startup, verify the accuracy of the cutting head’s position to ensure precise data for the starting point, height, etc. This helps prevent collisions and accidents during the working process.
- Periodically inspect the wear and tear of the cutting head’s nozzle, promptly replacing severely worn nozzles.
- Check the clarity of the lenses at various parts of the cutting head and clean them regularly.
- Inspect all the fixed screws of the cutting head for any signs of loosening.
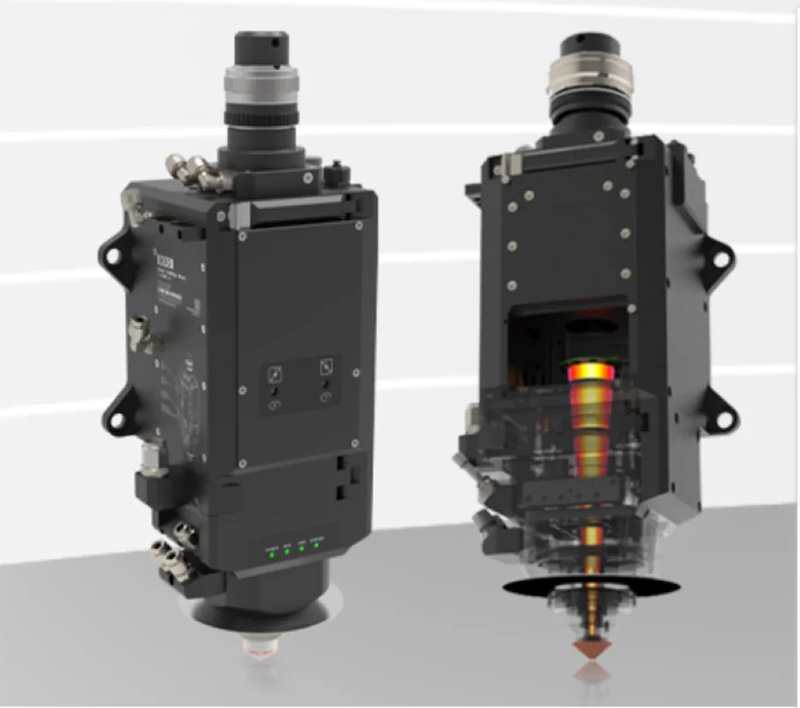
- Nozzle Maintenance
Regular maintenance is essential for laser cutting nozzles. Clean the laser cutting nozzle approximately every hour of operation, and replace it every 2-3 months.
- Focusing Lens
The focusing lens is a precision optical component directly impacting the processing performance and quality of the laser cutting machine. Regular maintenance of the focusing lens is crucial. Keep the lens clean and free from residues. As the focusing lens is a consumable, replace it every 2-3 months to ensure the laser cutting machine’s processing efficiency.
Maintenance Guide for Laser Cutting Machine Focusing Lens
Before cleaning, make sure the equipment is powered off.
Step 1: Remove the focusing lens from the mirror frame of the laser cutting machine. Loosen the securing screws and sequentially take off the nozzle and lens tube. Use an air blower to blow away the dust from the surface of the lens.
Step 2: If cleaning the lens is necessary, use laboratory-grade paper cotton balls dipped in an appropriate amount of acetone or high-purity alcohol. Gently rotate the cotton ball in a clockwise direction from the center of the lens towards the edges. If needed, clean both sides of the lens, ensuring a careful and meticulous cleaning process.
Step 3: Reassemble the lens tube and nozzle, adjust the focal length, tighten the securing screws, and make sure the convex side of the focusing lens is facing downward during installation.
Tips:
1. Gently wipe the lens to avoid damaging the surface coating.
2. Handle the lens with care during the wiping process to prevent drops.
3. Ensure the convex side faces downward when installing the focusing lens.
- Laser Cutter Cooling System Daily Maintenance
The laser cutting machine generates a lot of heat when cutting materials and requires a good cooling system to maintain normal operation. To regularly check the cooling system to ensure that the coolant is unobstructed, no leakage. Laser cutting machine water tank cleaning and replacement of water frequency, it is recommended to clean the water tank and replace the circulating water once a week.
1) Regularly clean the radiator: Carefully clean the surface of the radiator with a brush, then use compressed air to dry and remove dust. If necessary, utilize a specialized air conditioner fin cleaner (commonly known as a dusting agent) for cleaning and flushing.
2) Regularly clean the condenser: Dust removal should be carried out using the same method as cleaning the radiator.
3) Regularly check the water level in the chiller unit’s water tank: Ensure the water level is appropriate. If the water level is too low, promptly add distilled water or deionized water.
4) Regularly inspect electrical wiring terminals and remove dust: After power is disconnected, examine the connections of electrical wiring terminals and remove any dirt.
5) Regularly check the water system: Inspect joints for signs of leakage and check for aging in the pipelines. If there is a leak, promptly replace the relevant components.
6) Regularly check the water quality in the chiller unit’s water tank: If the cooling water quality deteriorates, becomes turbid, or the transparency decreases, promptly replace the entire cooling water.
7) Regularly clean the filter cartridge: Remove impurities from the filter cartridge, and if the filter is damaged, replace it promptly, ensuring the use of the standard filter specified by the manufacturer.
- Scheduling Routine Inspections
Regularly schedule inspections for all machine components, including the fiber laser, cutting head, focusing lens, mirrors, and the cooling system.
Winter Maintenance
Colder temperatures in winter require extra care for your machine.
Temperature Control
Maintain a room temperature above 0°C, where the machine is stored. If available, use the machine’s provided heating system to keep it within the recommended temperature range.
Lubrication Maintenance
In cold winter conditions, prioritize lubrication for the guide rails and drive train. Use low-temperature lubricants to ensure effective lubrication, even in chilly temperatures. Perform regular checks and replace the lubricant to prevent it from hardening and impacting equipment operation in low temperatures.
Dehumidification and Antifreeze
Utilize a dehumidifier in the laser cutter’s working environment to prevent moisture from condensing on surfaces or inside the equipment. Before winter begins, timely replace the water cooler with antifreeze to safeguard against freezing damage to components like the water cooler, laser, and laser head. Ensure uninterrupted operation of the water cooler to prevent freezing if antifreeze replacement is not feasible due to power outages.
Electrical Equipment Protection
Guard electrical equipment against moisture or freezing by applying suitable insulation. Regularly inspect cables and connectors to ensure they remain in good condition, preventing electrical malfunctions.
The risk of breakdowns can be minimized by planned cyclical maintenance measures to ensure that the fiber laser cutting machine operates stably and efficiently during the winter and in any mid. Always refer to the laser cutter manufacturer’s recommendations and manuals before performing any maintenance tasks. Please refer to our documentation area to download the best fiber laser cutting machine maintenance or contact our experts for download links to the documentation.
Periodic Check of Fiber Laser Cutting Machines
Daily Maintenance of Fiber Laser Cutting Machines
– Check the laser and cutting gas pressure before starting the machine daily and replace the insufficient gas in time.
– Check the zero point, limit switches and screws of X-axis, Y-axis and Z-axis to ensure that they are firmly installed and the limit switches are sensitive.
– Check the table sensing switch to make sure it is clean and free of dust to avoid sensing failure.

– Check the circulating water level of the chiller and add it in time if necessary.
– Check the external optical circulating water line and address any leaks to maintain optics life.
– Test X and Y direction manually at low speed after power on, confirm no abnormality and return to home position.
– Clean the metal slag on the laser cutting nozzle every 30 minutes and replace the nozzle regularly.
– Clean up the cutting waste and work site in time after completion of daily work, keep it tidy.
– Clean all parts of the equipment to eliminate debris.
Weekly Maintenance Guide Laser Cutting Machines
– Periodically check air pipe filters to remove water and debris.
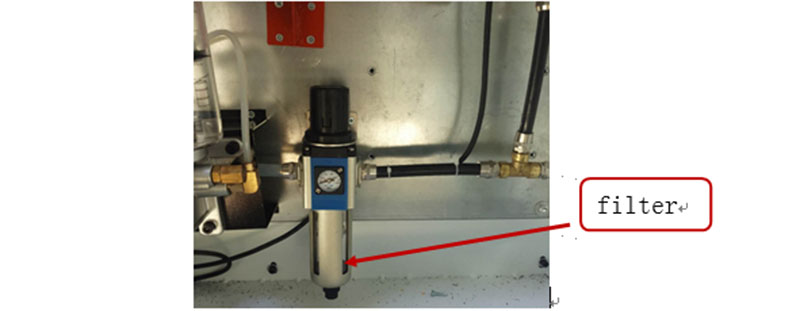
– Regularly check stroke switches and ram bracket screws to ensure secure installation.

– Clean the dust on the electric control cabinet and exhaust fan filter to maintain ventilation and heat dissipation.
– Clean the dust inside the guide rail and rack regularly to avoid damage and prolong service life.
– Check and refill the lubricant of X, Y, Z axis guide rail, rack and screw every week to maintain lubrication and prolong service life.
– Regularly check the discharge of waste oil from guide rails and rack and pinion lubricants, and clean the drain holes to prevent waste oil from overflowing.
Annual maintenance:
– Replace worn parts
Replace optics and other wear parts according to manufacturer’s recommendations.
– System Overhaul
Perform a thorough overhaul of the entire system, including checking solder joints, tightening screws, etc.
– Performance Test
Perform performance tests to ensure that the equipment still meets specifications.
– Operator Training
Provide operators with the necessary training to ensure safe operation of the equipment. Ensure that your employees are properly trained on fiber laser cutting machine maintenance procedures. This ensures that they are able to recognize and resolve problems in a timely and efficient manner.
Professional Laser Equipment Services
As a beginner in laser cutting machine, you may find yourself confused about how to properly maintain your equipment and execute necessary maintenance procedures. Don’t worry—our dedicated after-sales team is here to assist you in becoming familiar with the daily maintenance and operational procedures of the industrial laser cutter. They will provide guidance to ensure that you use the laser cutting machine correctly, enhance production efficiency, and help you maximize the lifespan of your laser metal cutter machine. If you have any questions or need support, we are ready to assist you at any time.
Doing a comprehensive laser cutter maintenance will ensure that the laser cutting machine maintains good performance and reliability over a long period of time. Fiber laser cutting machine manufacturers provide a recommended maintenance program that should be followed by every manufacturer to ensure maximum performance of the machine over its lifetime, effectively extending the life of the laser cutter, reducing the failure rate and increasing productivity.