Manual loading and unloading of laser cutting machines leads to low efficiency and high labor intensity, while irregular layout also causes waste of raw materials. This article focuses on the impact of laser cutting machine with loading and unloading on efficiency and labor intensity in metal sheet and tube processing, as well as the effect of optimizing layout on improving material utilization.
What is the Automatic Loading and Unloading Systems?
The automated loading and unloading system is capable of automatically feeding raw materials such as sheet metal and tubing into the laser cutting machine for processing, including storage and intelligent handling. Once processing is complete, the system automatically unloads finished products and scrap without human intervention.
This laser loading unloading system operates efficiently, is suitable for handling large numbers of production tasks, and supports unattended operation for long periods of time. The sheet metal loading and unloading system is highly flexible and compatible, and can be used not only for laser cutting, but also seamlessly connected with other sheet metal processing equipment such as bending machines, Coil Fed, and forming machines, thus enhancing overall production efficiency.
Benefit of Loading and Unloading System for Laser Cutting
Full Automation Production Line
This system covers the entire process from production planning, programming and layout, material management, automatic loading and unloading, cutting processing to handling of finished products and waste materials, ensuring efficient execution according to the plan and enhancing production efficiency.
Heavy Plate Handling Capability
With the ability to handle materials with a thickness of up to 110mm, the system achieves centralized storage of thick plates after cutting, meeting diverse processing requirements.
Intelligent Handling Equipment
Utilizing automated tools such as vacuum suction cups and forks, precise loading and unloading of materials is achieved, seamlessly integrating with the production system to enhance control and flexibility in the production process.
Efficient Sorting and Storage
Equipped with movable high-low double-layer sorting tables, capable of stacking up to 5 tons of sheet metal, effectively dispersing offloading pressure, improving sorting efficiency, and reducing waiting time.
High Utilization Rate and Long Running Time
Ensuring laser cutting machine uptime exceeds 85%, with daily cutting time of over 20 hours, maximizing equipment capacity.
Safety Assurance
Integrated with safety protection facilities and interlocking devices to ensure worry-free operation; even in the event of a single machine failure, the system can continue to provide loading and unloading services for other equipment, ensuring production continuity.
Flexible Control Modes
Supports automatic and manual mode switching, with automatic mode enabling features such as automatic worktable exchange, edge finding, and continuous cutting cycles, while manual mode caters to specific operational needs, ensuring flexibility and precision in operations.
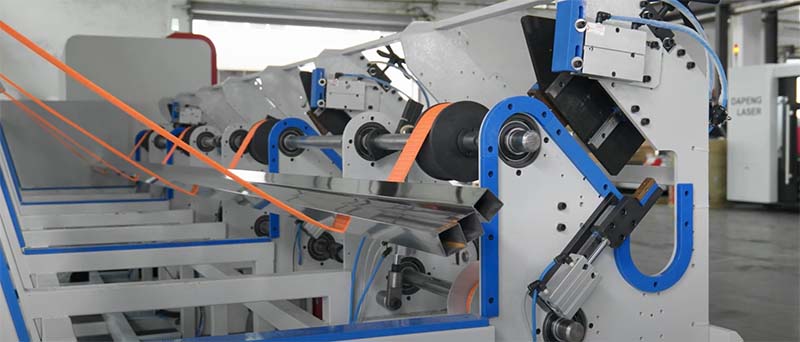
Cons.
Small batch production may not have enough budget to invest.
Laser cutting machines with loading and unloading system may require more factory space.
May be limited to specific raw material sizes or thicknesses.
Two Types of CNC Loading and Unloading Systems
Cantilever Loading and Unloading
- Cantilever loading and unloading systems typically employ one or more extendable mechanical arms installed on the side or above the laser cutting machine. These arms can flexibly extend and rotate to grab, transport, and place materials.
- Advantages: Occupies relatively small space, suitable for production environments with limited space. High flexibility to adapt to various sizes and shapes of workpieces.
- Applications: Suitable for efficiently handling materials in limited spaces or processing small to medium-sized sheet metal.
Gantry Loading and Unloading:
- Gantry loading and unloading systems utilize a gantry structure spanning above the working area of the laser cutting machine, with linear guide rails on the X and Y axes for moving and carrying devices to transport materials.
- Advantages: Large coverage area, strong stability, suitable for handling large-sized or heavy-duty sheet metal. Due to its robust structure, it can carry heavier loads.
- Applications: Particularly suitable for large-scale, continuous production environments, especially in industries requiring the processing of large metal sheets, such as shipbuilding and heavy machinery manufacturing.
The choice between these two loading and unloading methods depends on various factors such as production requirements, workpiece sizes, workshop layout, and budget.
The automatic loading and unloading laser cutting system combines the motion flexibility and high degree of flexibility of robots and the advantages of high speed, high quality and narrow slit of laser cutting, which perfectly meets the needs of modern manufacturing industry. It not only technically meets the requirements of complex three-dimensional cutting and improves the quality level of industrial products, but also reduces production costs and brings considerable economic benefits to enterprises.
Laser cutting as a method of thermal cutting, equipped with semi or fully automated loading and unloading machines can significantly improve productivity and simplify the production process. It is mainly used for high-speed cutting and processing of carbon steel, stainless steel, aluminum, copper, brass and other medium-thin metal plates, and is widely used in the industries of machinery manufacturing, elevator, sheet metal, kitchen equipment, chassis and cabinets, machine tools and equipment, electrical equipment, lighting hardware, advertising signs, automotive parts, display equipment, all kinds of metal products, as well as sheet metal cutting and processing.
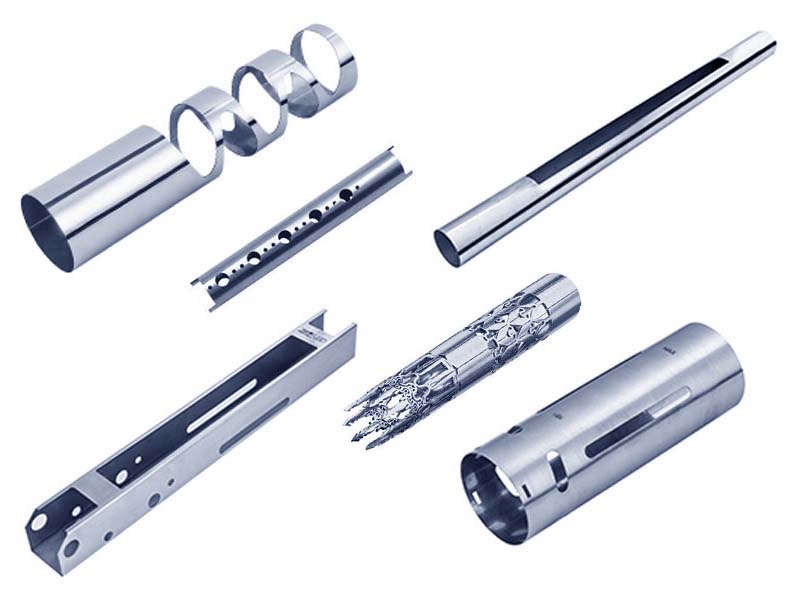
How to Use an Auto Loading and Unloading Laser Cutting Machines?
Safety and Inspection (Preparatory Steps)
Prior to initiating any operation, the primary task is to conduct a comprehensive safety check and equipment maintenance to ensure operational safety and efficiency. This includes but is not limited to inspecting the laser, guide rails, control systems, and the automatic loading and unloading system to ensure all components are functioning properly and undamaged.
Pre-Preparation
Material Preparation: Select and clean the metal sheets to be processed, removing surface stains, oil residues, and rust to ensure cutting accuracy and quality.
Tool Assembly: Confirm that hooks, suction cups, or other specialized loading and unloading tools are properly installed in the automatic loading and unloading system and in working condition.
Automatic Loading
Material Loading: Utilize a forklift or hoisting equipment to place the metal sheets flat on the loading platform, ensuring the material is flat and securely fastened.
Activate Loading: Initiate the automatic loading program through the control panel, where the system will precisely grab and transport the material to the cutting area using suction cups or robotic arms, without manual intervention.
Monitor Cutting: During the laser cutting process, operators should track the cutting progress and quality through the monitoring system, ready to adjust parameters as needed for any anomalies.
Automatic Unloading
Completion of Cutting: After the cutting operation is complete, the system automatically moves the finished products to the unloading area.
Unload Parts: The automatic unloading mechanism gently places the cut parts onto the unloading platform, again without direct manual operation.
Quality Inspection: Conduct a detailed inspection of the unloaded parts to verify dimensional accuracy and cutting quality, performing any necessary post-processing or rework if required.
Iterative Cycle
Once unloading is completed and the parts are confirmed to be qualified, the process of loading to unloading can be repeated, allowing for continuous batch production. Throughout the entire operation cycle, maintain vigilance over equipment status, conducting timely maintenance to ensure optimal work efficiency.
The fully automated laser loading and unloading solution combines the laser cutting machine with a CNC system to realize the automatic separation of sheet metal from automatic loading to unloading and even finished forming and separation from waste material. This not only significantly enhances the economy and safety of the production process, but also greatly improves the automation level of sheet metal processing, accelerates the material transfer and loading/unloading steps, and directly contributes to the rapid growth of metal processing efficiency, while effectively reducing production costs.
The operating efficiency of automatic laser loading and unloading machine is about 4~5 times that of manual labor under ideal full load condition, and its advantages become more and more obvious with the increase in the number of laser cutting machines. Therefore, equipped with loading and unloading system has incomparable advantages in saving labor, safe production and improve operational efficiency.
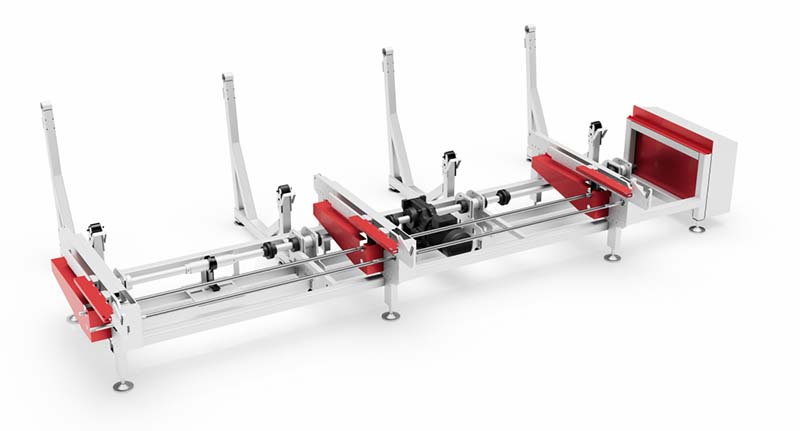
Why Choose DPLASER Automatic Loading and Unloading Laser Cutting Machine
DPLASER loading and unloading laser cutting machine adopts exquisite modular construction and compact design to maximize the use of space and reduce the additional cost caused by the equipment footprint. This series of machines has a high degree of flexibility, not only with a variety of laser cutting systems can be perfectly coordinated to meet the needs of different specifications of metal pipe and plate precision processing, but also according to the customer’s processing requirements for customized.

The loading and unloading laser cutting machines price depends on configurations and systems. Please provide us the details of your sheet material, maximum thickness and processing requirements. We have our own team of engineers to design your sheet metal loading and unloading system solution. In addition, it is best to provide us with your factory space and we will try our best to design the most suitable technical solution for you.