In modern manufacturing, the choice of welding technology has a significant impact on product quality and productivity. Laser spot and seam welding are two common laser welding methods, and their respective characteristics and application scenarios are significantly different. In this article, we will discuss the difference between spot welding and seam welding, and compare the advantages and disadvantages of traditional resistance spot welding and laser welding to help you better understand the performance and advantages of these technologies in practical applications. Whether you are an engineer, a manufacturer, or an enthusiast interested in welding technology, this article will provide you with valuable reference information.
Seam Weld Vs Spot Weld
Laser seam welding and spot welding differ not only in appearance but also in their working principles. Laser welding uses a laser as the heat source, distinguishing it from arc welding, resistance welding, and electron beam welding.
Laser has two modes: continuous welding and pulsed welding, capable of both seam welding and spot welding. Spot welding is a type of welding method, different from seam welding, with resistance spot welding being the most common. Compared to resistance spot welding, laser spot welding does not require pressure, allows for greater penetration depth, and is easier to automate.
Resistance Spot Welding
This welding method utilizes columnar electrodes to form a weld point between the contact surfaces of two overlapping workpieces. During spot welding, pressure is first applied to ensure tight contact between the workpieces, followed by the application of an electric current. The resistance heat generated causes the contact area to melt and, upon cooling, forms a weld point. Spot welding is primarily used for stamping parts of thin sheet components with a thickness of less than 4mm, making it particularly suitable for welding electronic parts, furniture and tools, etc… However, its shortcoming is that it cannot be used for welding containers that require sealing.
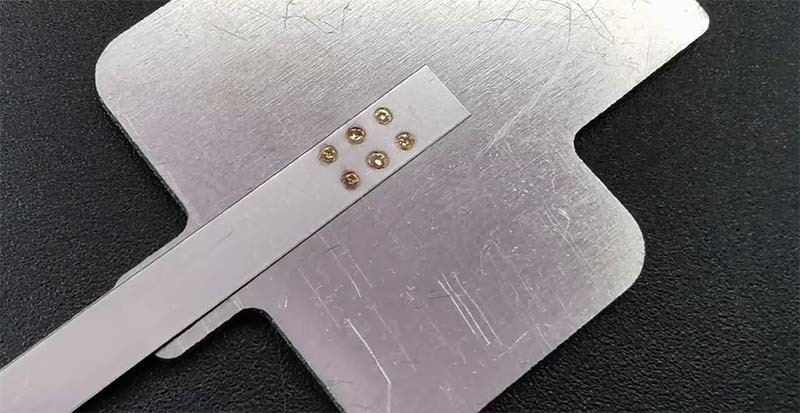
Difference between Spot Welding and Seam Welding
Laser welding utilizes high-energy laser pulses to locally heat a small area of the material. The energy from the laser radiation is conducted into the material, causing it to melt and form a specific weld pool.
Laser Spot Welding
Spot welding is a method of laser welding that confines the laser energy to a small area for instantaneous heating, fusing two contacting metal parts together. This welding method can be continuous or pulsed. It is characterized by high precision and accuracy, making it suitable for welding delicate or small components such as electronic parts, circuit boards, and micro-components. Spot welding creates localized welds or discrete weld points at specific positions on metal sheets. These weld points are typically small, circular, and range in diameter from a few millimeters to a centimeter.
Laser spot welding is widely used across various industries. A common application is coil welding, and it is also employed in the medical field for manufacturing medical devices and implants. The welds produced by spot welding are small and concentrated, with a minimal heat-affected zone, reducing the risk of deformation or damage to the surrounding material and ensuring high weld quality. The non-contact nature of laser spot welding minimizes the potential for contamination or surface marks on the workpiece.
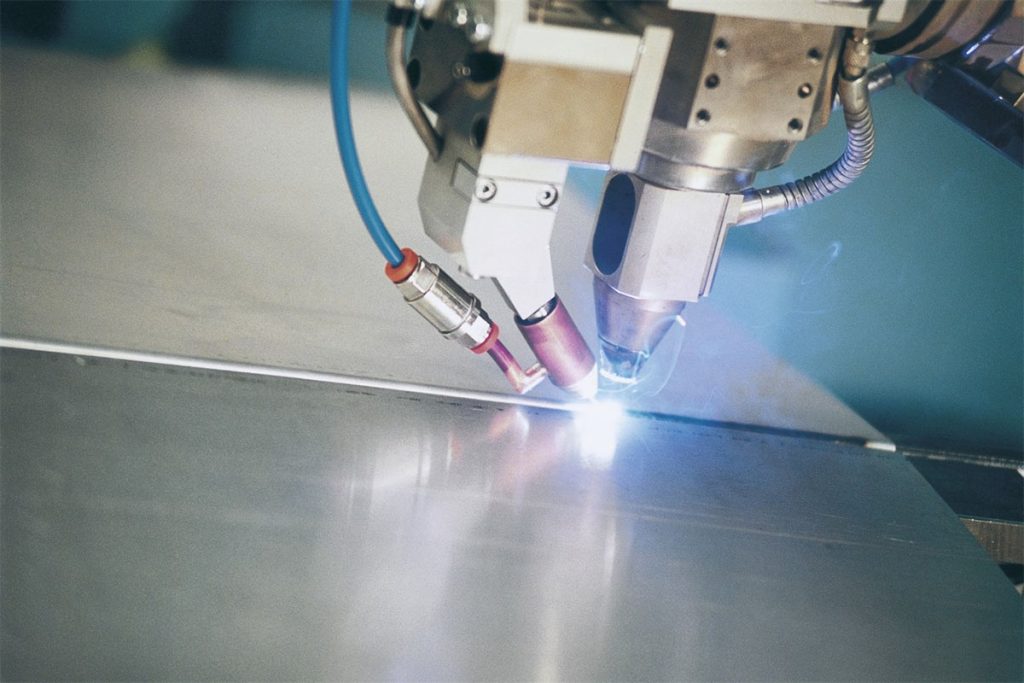
Laser Seam Welding
Laser seam welding refers to continuous welding on the surface of an object. When the welding points of spot welding are infinitely close to each other, laser spot welding becomes laser seam welding. It is a welding technique that uses a laser beam to form a continuous and highly precise weld along the seam or joint between two or more metal workpieces. This method offers high precision and control, allowing for consistent and accurate welding across the entire seam. The focused laser beam can weld thin and delicate materials without causing deformation or damage. Seam welding is generally slower than spot welding because it involves the continuous movement of the welding equipment along the joint.
This laser seam welding is widely used in the electrical manufacturing, electronics, and the production of aircraft and automotive components. It is particularly suited for welding tubular parts and structural components and plays a crucial role in container sealing and the production of various metal parts.
Laser welding machine is mainly for thin-walled materials, precision parts welding, by adjusting the parameters of the laser welding system can be realized spot welding, seam welding, stack welding, butt welding, and sealing welding and so on. Laser welding depth and width ratio is high, the width of the weld is small, the heat affected zone is small, the deformation is small, the welding speed is fast, the weld is flat, beautiful, no need to deal with the weld after welding or only simple treatment, the weld is of high quality, no air holes, it can be accurately controlled, the focusing point of light is small, the positioning accuracy is high, and it is easy to realize the automation.
Application of Laser Spot Welding
Spot welding is used across various industries, including automotive, aerospace, metal furniture, electronics, and construction. Automotive body components utilize different laser welding techniques, such as laser spot welding and laser seam welding.
Spot welding is ideal for high-volume production applications and is suitable for welding thin sheets. It is also used for manufacturing all types of metal sheet structures that require high mechanical strength. Additionally, spot welding is applied to various enclosures, cores, and housings.
Application of Laser Seam Welding Machine
The process is suitable for mass production applications such as batteries and the medical industry. Typical applications for laser seam welding include sensors, radar components, battery housings, thin film battery conductors, pacemaker housings and appliance housings.
Spot welding is used to make discrete welds at specific points, offering the advantages of speed and efficiency for parts that need to be welded in localized areas. Seam welding, on the other hand, involves continuous welding along the length of an overlapping sheet of metal, which is slower but provides a continuous and hermetically sealed weld, suitable for workpieces that need to maintain weld strength, gas tightness and water tightness over a long period of time. Therefore, depending on the application, the appropriate welding method can be selected to achieve the best results.
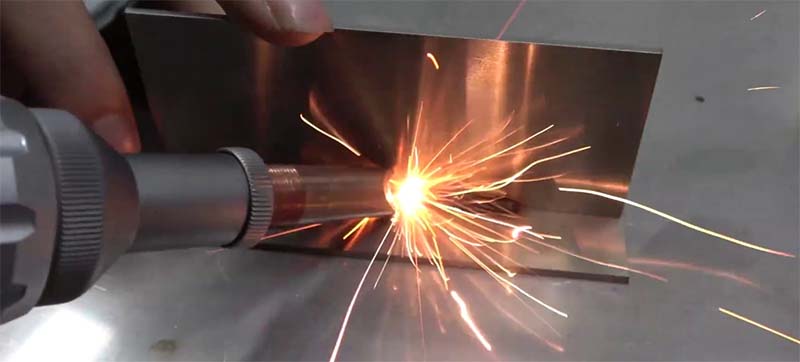
What is the Difference between Continuous Wave vs. Pulsed Laser Welding?
1. Continuous Laser Welding
Continuous mode laser welding involves continuously directing a laser beam onto the workpiece until the entire joint is welded. Its advantages include high welding speed, making it suitable for large areas and thicker workpieces, with a stable welding result. However, continuous mode requires a high power laser and may not achieve the same weld quality as pulsed continuous mode.
Continuous laser welding is a form of deep penetration welding with a high depth-to-width ratio, often exceeding 5:1, and it offers fast welding speeds with minimal thermal distortion. Most CW laser welding machines use high-power lasers with outputs above 500W, making them ideal for welding large, thick workpieces, such as sheet metal thicker than 2mm.
2. Pulsed Laser Welding
Pulsed mode laser welding involves the laser beam striking the weld point in periodic, short-duration pulses, generally lasting milliseconds, with very short intervals between pulses. The advantages of this mode include high weld quality, making it suitable for thinner workpieces that require precise welding and tiny components welding in the electronics industry.
Pulsed laser welding is primarily used for spot and seam welding of thin-walled metal materials up to 1mm thick. This process is thermal conduction-based, where the laser radiation heats the surface of the workpiece, and the heat is then conducted into the material. By controlling parameters such as pulse waveform, width, peak power, and repetition frequency, a good connection between the workpieces is achieved.
The advantages of pulsed continuous mode include high-quality welds, aesthetically pleasing joints, and reduced risk of deformation and porosity. It is widely used in industries such as 3C product enclosures, lithium batteries, electronic components, and mold repair.
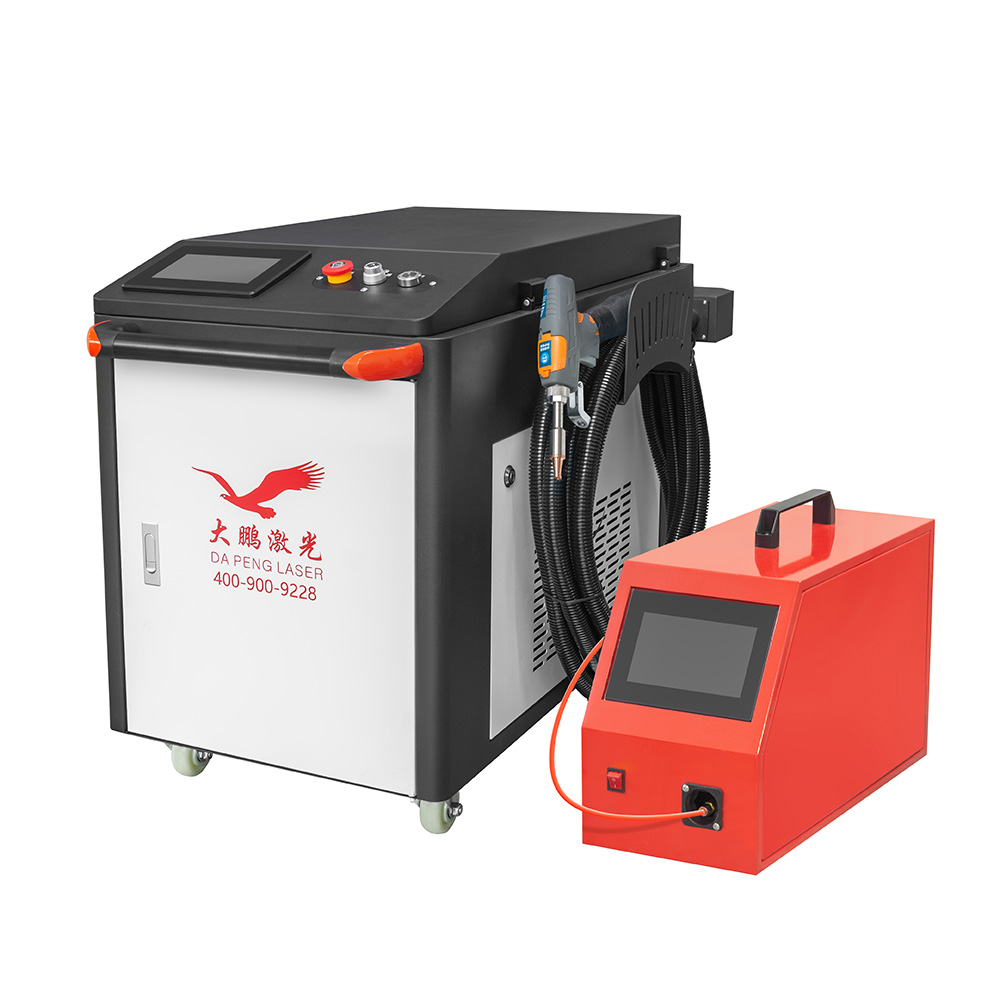
Why Choose DPLASER Laser Welding Machine
The 4-in-1 handheld laser welding machine consists of a fiber laser source, handheld laser gun, chiller, and 4-in-1 control system that allows you to perform the four tasks of laser welding, cutting, cleaning, and weld path cleaning with precision and efficiency.
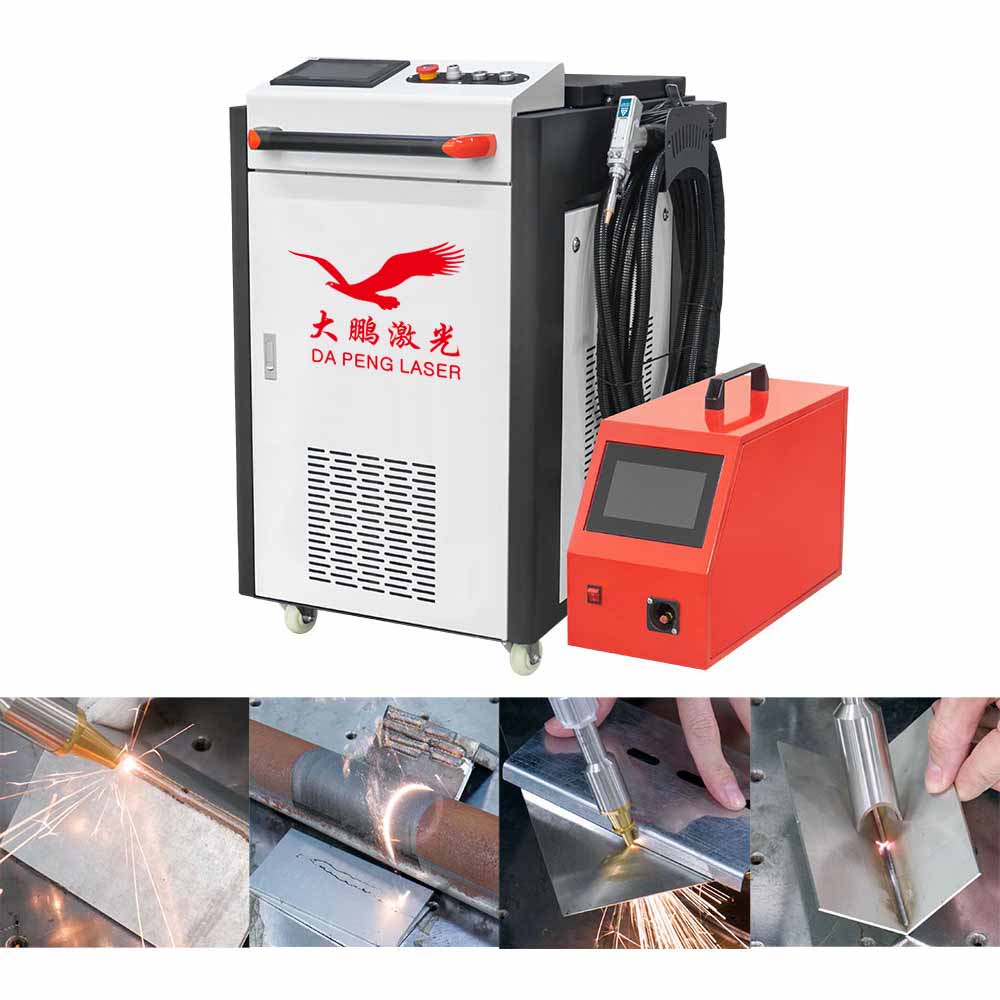
DPLASER handheld fiber laser welding machine produces high quality welds on a wide range of materials and thicknesses. The welds are smooth and beautiful, eliminating the need for secondary grinding or post-processing. This handheld metal laser welder has 5-in-1 metal welding capabilities including spot, seam, pulse, continuous and repair welding for a variety of welding needs.
Conclusion: By comparing laser seam welding vs spot welding, including their features and applications, you can gain a clearer understanding of each welding methods unique functions and suitable scenarios. Laser welding, with its high precision, minimal heat-affected zone, and excellent joint strength, offers the perfect welding solutions for modern manufacturing. We hope the information provided in this article helps you make a right decisions when choosing a welding method, optimizing production processes, and enhancing product quality.