What is a CNC press brake machine? On the stage of modern manufacturing, CNC press brakes have captured attention with their efficient and precise metal processing capabilities. From the perspective of numerical control systems to the execution of bending processes, we will unveil the mysterious veil surrounding CNC press brake machines. Whether you are a professional in the manufacturing industry or simply intrigued by this technology, through this article, you will discover how CNC press brake machines achieve meticulous craftsmanship in metal shaping through advanced automation techniques.
How Does a CNC Press Brake Work?
Press brake machine consist of a frame, workbench, and clamping plate. The workbench is composed of a base and a pressure plate, with the base connected to the clamping plate through hinges. The base includes a seat shell, coil, and cover plate, with the coil placed in a recess of the seat shell, and the top of the recess covered by the cover plate. By applying electric current through the wires, the coil generates a magnetic force that exerts pressure on the pressure plate, achieving the clamping of thin plates between the pressure plate and the base. With electromagnetic force clamping, it can adapt to various workpiece requirements, including those with side walls, and the operation is simple.
Press brake machines are classified into manual bending machines, hydraulic bending machines, and CNC bending machines. Hydraulic bending machines can be further categorized based on synchronization: torsion axis synchronization, mechanical and hydraulic synchronization, and electro-hydraulic synchronization.
The main components of a CNC bending machine work in coordination to enable the efficient and precise bending of metal sheets.

Hydraulic System:
Hydraulic Pump: Usually driven by an electric motor, responsible for transmitting liquid (usually hydraulic fluid) pressure to the hydraulic cylinders to generate the force required to perform the bending of the plates.
Cylinders: Receive the pressure from the hydraulic pump and convert it into a linear movement that is used to push the backstop, move the table, or apply force to complete the bending operation.
Valves and Hoses: Used to control the flow of fluids and distribute pressure to ensure that the system responds flexibly and accurately to operational commands.
CNC Controller:
Operator Interface: Provides the operator with an intuitive interface for entering bending parameters, adjusting programs, and monitoring machine status.
Motion Control System: Controls the motion of each axis to ensure accurate and smooth bending.
PROGRAMMING FUNCTION: Allows the operator to define the bending parameters such as angle, position, etc. by entering the digitized bending program.
Backstop:
Motorized Backstop: In CNC bending machines, the backstop is usually motorized and can be precisely adjusted in position by the CNC controller to accommodate different workpiece sizes and shapes.
Molds:
Multi-station tooling: Some CNC bending machines are equipped with multi-station tooling that can accommodate different shapes and sizes of punches, making the machine more flexible.
Quick-change system: Some advanced CNC bending machines have a quick-change mold system to improve productivity.
Safety devices:
Guards and Light Curtains: Used to protect the operator from the moving parts of the machine, the guards can usually be opened for ease of operation.
Emergency stop button: In the event of an emergency, you can quickly cut off the power supply to the machine to ensure the safety of the operator.
Bending Accuracy of CNC Press Brake
In general, the precision requirements for CNC bending machines are as follows:
1. Wire feeding: ±0.2mm within a range of 300mm.
2. Bending angle: ±0.3 degrees.
3. Rotation angle of the rotary arm: ±0.3mm.
Precision sheet metal processing demands high requirements for part size accuracy and aesthetic surface finishes. The tolerance standard for bending dimensions is ±0.10mm.
During CNC press brake machine working, there may be some errors in bending accuracy, which can be attributed to various factors. Sometimes, it may be due to mechanical factors of the machine that result in insufficient bending accuracy. External factors such as bending tools, material thickness of the bent sheet, and even human-operational factors can also play a role. The following are factors that influence bending accuracy:
– Mechanical Factors: Mechanical issues within the machine can lead to deviations in bending accuracy.
– External Factors: Characteristics of bending tools and the thickness of the material being bent can impact precision.
– Human-operational Factors: The precision of bending can be affected by the skill and precision of the operator.
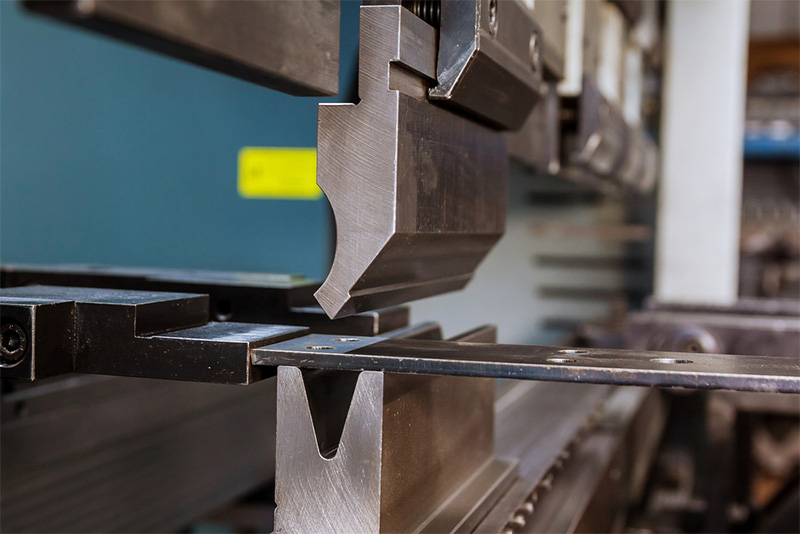
Part 1: Influencing Factors on CNC Bending Angle
A precision-controlled system utilizes computer programs to achieve accurate bending angles, with the range determined by preset parameters. While CNC press brake equipment typically allows for a bending angle range of 0 to 180 degrees, actual outcomes are affected by the following elements:
1. Material Thickness: The thickness of the material significantly impacts the achievable bending angle range on CNC press brake systems. Generally, thicker materials result in a reduced bending angle range.
2. Pressure: Bending angles are influenced by the pressure settings of the equipment. Insufficient pressure can hinder the attainment of larger bending angles.
3. Tooling: The type of tools employed in CNC bending systems plays a role in determining bending angles. Smaller tools generally facilitate larger bending angles.
Part 2: Control of Bending Angles
The regulation of bending angles in CNC bending systems is typically executed through computer programming. During program development, the following parameters must be established:
1. Material Thickness: The program requires knowledge of the material thickness to appropriately configure pressure and tooling.
2. Bending Position: Information about the material’s bending position is necessary to determine the tool’s placement and bending angle.
3. Desired Angle: The program relies on information about the desired bending angle to configure suitable pressure and tooling.
4. Tool Selection: Based on material thickness and desired angle, the program must choose suitable tools.
5. Sampling Interval: A sampling interval is established in the program to ensure stability and accuracy during the bending process.
Part 3: Bending Angle Deviation
In practical applications, deviations in bending angles may occur in CNC bending systems, influenced by factors such as the machine’s inherent precision, tool selection, and sampling interval. Typically, the deviation in bending angles on CNC bending systems can be kept within the range of 0.1-0.5 degrees. For applications requiring heightened bending accuracy, adjustments and optimizations tailored to the specific circumstances may be necessary.

How to improve the accuracy of CNC Bender?
Press Brake Machine Calibration: Regularly calibrate CNC metal press brake machines to ensure accurate positioning of each axis. This involves precise alignment of the transverse, longitudinal, and rotational axes to ensure the accuracy of workpieces during the bending process.
Tool Selection and Maintenance: Utilize high-quality bending dies and tools, ensuring their precise dimensions. Regularly inspect and maintain the tools to ensure the stability of their geometric shapes and sizes. Grind and trim tools to maintain the sharpness of their cutting edges.
Material Selection: Ensure the use of consistently high-quality metal materials and, whenever possible, adhere to standardized material specifications. This helps minimize the impact of material variations on bending results.
Parameter Settings: Carefully configure the process parameters of the CNC metal press brake machine, including bending force, bending speed, blackcap, and other relevant parameters. Adjusting these parameters can affect the accuracy of bending results.
Implement Advanced Control Systems: Consider upgrading to advanced CNC systems, if possible, to enhance control accuracy. These systems typically feature higher resolution and more advanced control algorithms, improving the performance of the press brake machine.
Operator Training: Provide thorough training for operators to ensure correct operation of the CNC metal bending machine. Skilled operators can better understand and apply process parameters, thereby improving bending accuracy.
Quality Control: Implement strict quality control procedures, including real-time inspection of workpieces during the bending process. Timely detection and correction of issues can enhance bending accuracy.
In summary, the bending angle range and accuracy of CNC press brake system depend on various factors mentioned above. Analysis and optimization should be performed based on specific application scenarios and material characteristics.
How to Operate a CNC Press Brake?
1. Power Connection: Ensure the machine is connected to a dedicated circuit capable of meeting its power requirements. The power supply should also be equipped with appropriate grounding and protective devices.
2. Workpiece Preparation: Place the workpiece to be bent correctly on the worktable, adjust fixtures and clamping plates to ensure secure fixation of the workpiece.
3. CNC Programming: Utilize the CNC system for programming, inputting bending process parameters, including bending angles and positions.
4. Selection of Bending Groove: Generally, choose a groove width approximately eight times the thickness of the plate. For instance, for bending a 4mm plate, select a groove width around 32.
5. Machine Startup: Initiate the hydraulic system and perform manual or unloaded operations, checking for any abnormal sounds or vibrations in the machine.
6. Automatic Bending: Input the CNC program and initiate the automatic bending process. The machine will automatically complete the bending task based on preset process parameters. Throughout the bending process, monitor the machine’s status and workpiece position in real-time through the CNC system display.
7. Inspection and Adjustment: After the first workpiece is completed, conduct an inspection to ensure that the bending results meet design requirements. If necessary, make minor adjustments to the CNC program to enhance bending accuracy based on actual conditions.

CNC press brake machines are indispensable tools in the metal processing industry. They are used to bend metal sheets into various shapes and angles with high precision and accuracy. These machines can handle different types of materials such as steel, aluminum, brass, and copper. Featuring high flexibility, accuracy, and repeatability, CNC press brake machines provide efficient and precise metal bending solutions for production and manufacturing needs.
What Are the Applications of Press Brake?
Aerospace Manufacturing:
In the aircraft manufacturing industry, hydraulic cnc press brake machines are employed for processing aircraft components such as wings, flaps, and fuselage shells. Due to the intricate curves and shapes often found in aircraft parts, the high precision and automation features of hydraulic press brake machines make them an ideal choice for manufacturing high-quality aircraft components.
Automotive Manufacturing:
In automotive manufacturing, hydraulic press brake machines are utilized for fabricating automotive body components such as doors, roofs, and floor panels. With precise control from CNC systems, hydraulic press brake machines ensure the accuracy and consistency of automotive parts, thereby enhancing production efficiency.
Shipbuilding:
Widely used in shipbuilding, CNC press brake machines play a crucial role in manufacturing ship structures and components. Given the typically large and complex metal sheets required for ship structures, the high force and spacious worktables of hydraulic press brake machines enable them to meet various demands in shipbuilding.
Electrical Manufacturing:
Metal press brake machines are employed in the production of components for the electrical industry, including casings, brackets, and panels. Given the high precision and aesthetic quality required for electrical components, the precise control offered by hydraulic press brake machines is vital in meeting these demands.
Mechanical Manufacturing:
In general mechanical manufacturing, metal bending machines can be used to produce various mechanical components such as machine tool beds, bases, and housings. They provide the capability to accurately bend a variety of metal sheets, catering to the diverse production needs of the mechanical industry.
Light Industry:
CNC bending system find widespread application in light industries such as the production of furniture, lighting fixtures, and signage. They fulfill the need for precise and efficient bending of various metal materials, offering a convenient solution for the manufacturing of light industry products.

Summary, hydraulic press brake machines stand at the forefront of precision and efficiency across diverse industries. Their ability to handle various materials, intricate shapes, and deliver consistent results underscores their significance in modern manufacturing. The accuracy and automation capabilities of industrial cnc press brake machine working, providing a reliable and versatile solution for meeting the evolving needs of industries worldwide. Whether shaping the wings of an aircraft, forming the automobile body, or crafting intricate components for machinery, hydraulic press brake machines play a vital role in shaping the future of precision metalworking.