Laser welding has transformed the process of joining carbon steel, delivering unparalleled precision, speed, and efficiency over traditional methods. Capable of adapting to low, medium, and high-carbon steel, it ensures robust and reliable joints across various compositions. In this article, we explore the capabilities of carbon steel laser welding machines and how it meets diverse industrial needs.

Carbon steel, known for its moderate carbon content, excellent mechanical properties, low cost, and good weldability, has become the preferred material across various industries. With advancements in laser welding technology, carbon steel laser welding has become more efficient and precise. This technique not only enables deep penetration welding but also minimizes deformation, delivering more stable and uniform welds to meet the stringent standards of industrial production.
Benefits of Laser Welding Machine for Carbon Steel
- Wide Material Compatibility: Laser welding is suitable not only for low-carbon steel but also for refractory and dissimilar materials, enabling seamless combinations of various materials in industrial production.
- High Power Density: The focused laser delivers exceptionally high power density. With high-power laser welders, low-carbon steel can achieve a depth-to-width ratio of up to 5:1, enabling deeper welds in smaller areas and improving both quality and efficiency.
- Flexible Welding Angles: By adjusting the laser beam direction, welding can be performed at nearly any position or angle, even in hard-to-reach areas. This adaptability also accommodates complex shapes and large workpieces, broadening its applications.
- Fast and Efficient: Laser welding is 3–4 times faster than traditional methods, significantly boosting productivity, reducing processing time, and lowering manufacturing costs.
- High Precision and Minimal Heat Impact: The small laser spot minimizes heat-affected zones, preserving structural integrity and reducing deformation caused by overheating.
- Superior Weld Quality: The concentrated heat source creates narrow, stable weld seams, reducing defects like cracks and ensuring reliable joint quality.
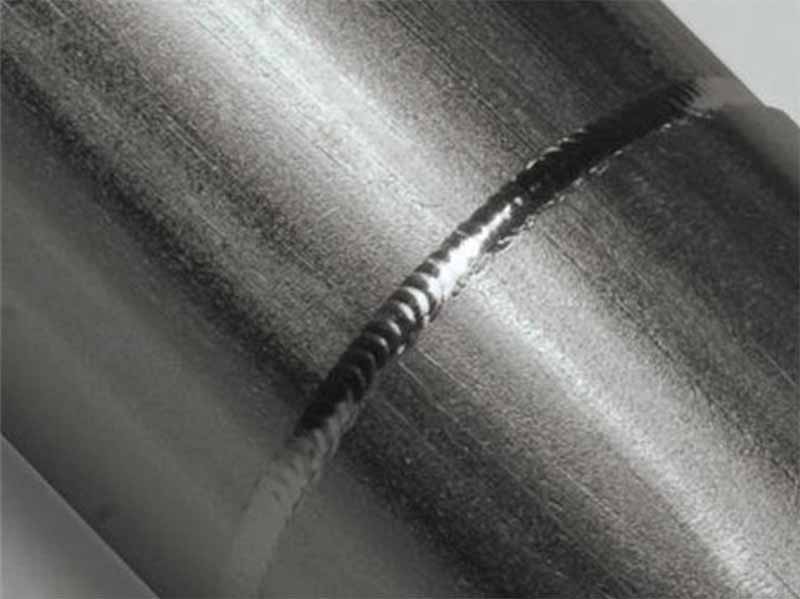
Can You Weld Steel with A Laser Welder?
Yes, laser welders can effectively weld various materials, including carbon steel. Carbon steel is categorized into three types based on carbon content: low-carbon steel (carbon content < 0.25%), medium-carbon steel (carbon content 0.25%–0.6%), and high-carbon steel (carbon content > 0.6%).
Laser Welding Low Carbon Steel
Low-carbon steel, also known as mild steel, has a carbon content below 0.25%. It is soft with low strength and hardness but exhibits excellent weldability, allowing most welding methods to achieve satisfactory results. Laser welding provides outstanding performance for low-carbon steel.
Laser Welding High Carbon Steel
However, when laser welding high carbon steel, certain challenges arise due to its material properties. High carbon content increases brittleness, leading to potential cracks during cooling, and is also a significant factor in welding deformation. To address these issues, laser welding high carbon steel requires preheating and post-weld treatments to reduce stress and minimize defects. For medium & high-carbon steel, preheating is especially recommended when the carbon content exceeds 0.25%, ensuring better weld quality and structural integrity.

Laser Welding Tips for Carbon Steels with Different Carbon Contents
- Laser welding delivers excellent results for carbon steel, but the impurity content plays a significant role in the overall welding quality. To ensure a high-quality weld, preheating is required when the carbon content exceeds 0.25%.
- When welding dissimilar carbon steels with varying carbon contents, it is recommended to slightly offset the welding torch toward the low-carbon side to ensure proper joint quality.
- Due to the rapid heating and cooling rates during laser welding, the sensitivity to welding cracks and defects increases with higher carbon content in the steel.
- Both medium–carbon steels and high-carbon steels, as well as alloy steels, can be successfully welded using laser welding. However, preheating and post-weld treatment are essential to relieve stress and prevent crack formation.
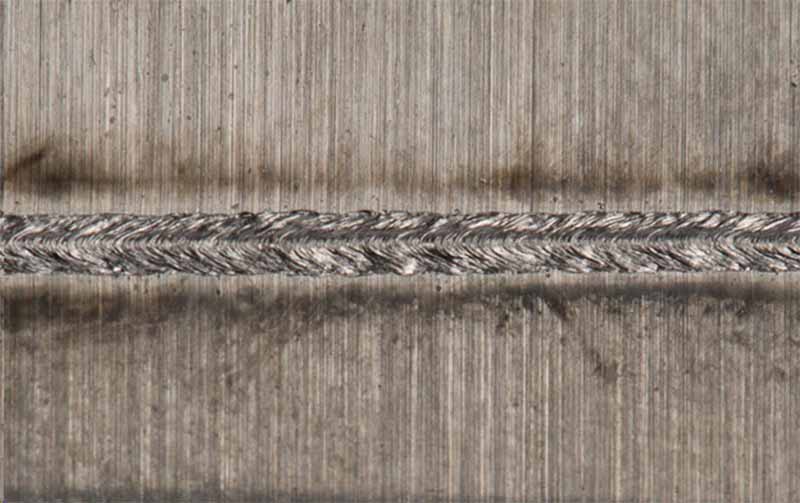
Is Laser Welding Carbon Steel as Strong as MIG Welding?
Yes, laser welding is as strong as MIG welding and produces welds with a cleaner and more aesthetically pleasing appearance.
What Is the Maximum Thickness for Laser Welding Machine Weld Carbon Steel?
A 3000W laser welder can typically weld carbon steel with a thickness of 4–6mm (approximately 1/4 inch) in a single pass, achieving full penetration.
What Gas Should Be Used for Laser Welding Carbon Steel?
For laser welding carbon steel, commonly used shielding gases include nitrogen and argon. The choice of gas or gas combinations depends on specific welding quality requirements and process efficiency.
3mm Carbon Steel Laser Welding
- Gas Shielding
Use shielding gas during fiber laser welding to protect the weld joint surface quality. Argon is commonly used, with a flow rate of 10–20 L/min to prevent oxidation.
- Surface Cleaning
Clean the carbon steel surface thoroughly before welding to reduce oxidation and impurities at the weld joint. Ensure the surface is free from oil, rust, and other contaminants by using acetone or alcohol for cleaning.
- Pre-treatment
Preheat the welding area if necessary to reduce stress during the welding process.
- Select Appropriate Welding Parameters
Adjust welding parameters based on material type and thickness to achieve optimal results.
- Laser Power: For 3mm thick carbon steel, a laser power of approximately 2000W is recommended.
- Welding Speed: Adjust according to material thickness and laser power; a common speed is around 10mm/s.
- Spot Diameter: Adjust the spot size using the focusing lens. For thin carbon steel sheets, a spot diameter of 0.2–0.5mm is typically suitable.
Perform multiple test runs to find the ideal combination of laser power, welding speed, and spot diameter.
- Welding Safety
Fiber laser welding involves high power, requiring strict safety measures to prevent harm to personnel and damage to equipment.
- Post-welding Treatment
After welding, perform deburring and surface treatments to improve the appearance and durability of the welded part. Common techniques include polishing, sandblasting, and coating, which remove splatter and oxidation layers and enhance corrosion resistance.

How to Laser Weld Dissimilar Metals: Carbon Steel and Stainless Steel
Carbon steel and stainless steel using laser welding is possible but challenging due to the differences in their material properties:
Thermal Expansion Coefficient: Carbon steel and stainless steel have different thermal expansion rates, leading to thermal stress and deformation during welding.
Melting Point Difference: Stainless steel has a slightly higher melting point than carbon steel, requiring precise laser power adjustments to control the molten pool temperature.
While laser welding can join these materials, their thermal and chemical property differences (e.g., thermal expansion coefficients) can cause issues such as unstable weld quality and crack formation. The following precautions can help improve stability and weld quality:
Material Pre-treatment:
Before welding, thoroughly clean the material surfaces to remove grease, rust, and other contaminants. This ensures a smooth and clean surface, reducing the risk of welding defects. Additionally, precisely control the gap between the materials to achieve a uniform and stable weld seam.
Welding Parameter Optimization:
Given the physical and chemical differences between the two materials, carefully adjust laser power, welding speed, and shielding gas flow. This minimizes heat input, preventing excessive heating that could cause material deformation or degradation.
Process Monitoring and Quality Control:
During welding, continuously monitor the weld seam to promptly identify and address issues such as cracks or porosity. Maintain proper welding temperatures and use appropriate shielding gas to ensure weld quality and process safety.
The Best Laser Welding Machine Carbon Steel
This handheld laser welding machine for carbon steel is a compact, portable, and highly efficient device designed for versatile welding applications. It supports multiple welding modes in a single machine, allowing for precise welding at any angle on any part of the workpiece. With its 5-in-1 metal welding capabilities —spot welding, seam welding, pulse welding, continuous welding, and repair welding—it meets a wide range of welding needs.
Lightweight and easy to carry, this portable laser welding machine offers a compact yet powerful solution, unlike traditional welders or complex robotic systems. It is perfectly suited for precise and demanding tasks in both outdoor and industrial environments.
This handheld laser welder is ideal for edge, butt, T-joint, corner, and lap joints. It is easy to operate, quickly to set up, and capable of delivering consistent, high-quality welds across a variety of materials and thicknesses. Whether you are a professional or a beginner, it’s a reliable choice. With shielding gas protection, it produces clean, high-quality welds that securely join two components.
Featuring fiber high electro-optical conversion efficiency, robust output power, excellent beam quality, and a compact, maintenance-free design, the fiber laser welding machine is cost-effective and efficient. Its continuous laser ensures smooth weld transitions, strong weld seams, and polished surfaces, eliminating the need for further grinding and saving both time and labor costs.

Features:
Intuitive User Interface
Equipped with a user-friendly touch screen, the machine ensures that users of all skill levels can quickly learn and operate it with ease.
Ergonomic Design
The welding gun features a lightweight, ergonomic design, weighing only 0.8 kg, specifically crafted for prolonged use without fatigue.
Advanced Laser Technology
Delivering faster and more precise results than TIG welding, this machine combines user-friendliness with efficiency.
Adjustable Welding Parameters
Easily adjustable settings allow users to tailor welding parameters to specific needs. With multiple pre-set configurations, users can quickly select and apply the most suitable parameters.
Six Welding Modes
From precision spot welding to continuous welding, six modes ensure the best performance and quality for every application.
Interchangeable Welding Nozzles
A variety of nozzle angles are available, enabling seamless welding for a wide range of product designs and requirements.
Compact and Robust Design
Built from high-quality metal, the machine is both durable and stable, requiring minimal maintenance. The compact design includes swivel wheels at the base, ensuring effortless mobility and easy repositioning.
Applications:
Laser welding machine is versatile and capable of welding a wide range of metals, including: Stainless Steel, Carbon Steel, Copper, Aluminum, and Galvanized Steel. Its adaptability makes it suitable for various industries and applications requiring precision and high-quality welding.

In conclusion, laser welding machine redefines efficiency and precision in metalworking, offering unmatched versatility and user convenience. Whether for industrial production or intricate custom projects, its innovative features and robust design ensure exceptional performance every time. Contact us today to customize a laser welding machine tailored to your welding projects. No matter the type of project or metal, we guarantee high-quality samples and carbon steel laser welder that meet your expectations.