Glass is widely used in daily life, spanning applications such as automotive glass, architectural glass, photovoltaic solar glass, industrial substrates, display panels, and cover glass in the electronics industry. However, traditional glass cutting methods often struggle with the material’s brittleness, leading to issues like cracking, chipping, and fractures. In ultrafast laser precision machining, picosecond laser cutting machines for glass cutting have been widely used. This includes large-format glass cutting, glass engraving, micrometer-level glass drilling, 3D internal glass engraving, surface marking, and high-precision inspection of external dimensions.
The ultrafast laser cutting machine for glass stands out mainly due to its extremely high processing precision, ultra-fast speed, and excellent edge quality with virtually no chipping. It eliminates the need for rinsing, grinding, or polishing, requires no consumables, and significantly reduces manufacturing costs while catering to the complex demands of high-end glass processing.
Why Use Ultrafast Laser Cutting Glass?
Conventional long-pulse lasers, such as those with microsecond or nanosecond pulse durations, operate based on the principle of energy absorption by the material’s electrons through resonance, gradually melting or evaporating the material for removal. Due to the long duration of the laser pulse, which is much greater than the thermal diffusion time of the material, the energy transferred from electrons to ions is very high. This results in thermal diffusion that affects a larger area than the focal point, causing a significant volume around the laser focus to melt, leading to unclear edges and limited processing precision.
In contrast, ultrafast laser cutting is based on the interaction between the material and the laser within an extremely short pulse duration. The laser pulse is extremely brief, and the energy is rapidly converted into plasma to remove the material, avoiding thermal melting. Due to the minimal thermal diffusion, the heat-affected zone is virtually zero, no recast layers are formed, and the edges are sharp with high precision. Compared to traditional long-pulse lasers, ultrafast lasers significantly reduce thermal effects, making them ideal for high-precision microfabrication.
1. Ultrashort Pulses
Ultrafast lasers emit pulses with durations typically in the femtosecond (10–15 seconds) or picosecond (10–12 seconds) range. The ultrashort pulse duration allows for extremely high temporal resolution, enabling the study of transient phenomena such as ultrafast dynamics, molecular vibrations, and electron transfer processes.
2. High Peak Power
Despite their low average power, ultrafast lasers can achieve extraordinarily high peak power due to the concentration of energy within extremely short pulses. This high peak power is crucial for inducing nonlinear optical effects, such as multiphoton absorption and self-focusing, which are extensively used in applications like precision micromachining, biological imaging, and advanced spectroscopy.
3. Cold Ablation
Ultrafast lasers operate with such short pulse durations that they minimize heat diffusion into the surrounding material. This enables a “cold ablation” process, where material removal occurs with negligible thermal damage. This characteristic is particularly valuable in precision applications such as medical surgery, microelectronics fabrication, and delicate material processing, ensuring high accuracy and minimal collateral damage.
Laser Micromachining for Glass
In the precision manufacturing, laser cutting technology has become an indispensable tool for glass processing due to its non-contact nature, high precision, and efficiency. The “ultrashort pulse” technology, which utilizes extremely short pulse durations (nanoseconds, picoseconds, femtoseconds), not only significantly improves cutting quality but also reduces the heat-affected zone, opening up new possibilities for the production of high-precision, complex structures, and ultra-thin glass products.
Glass laser processing mainly includes 3 methods: laser cutting, laser drilling, and laser marking.
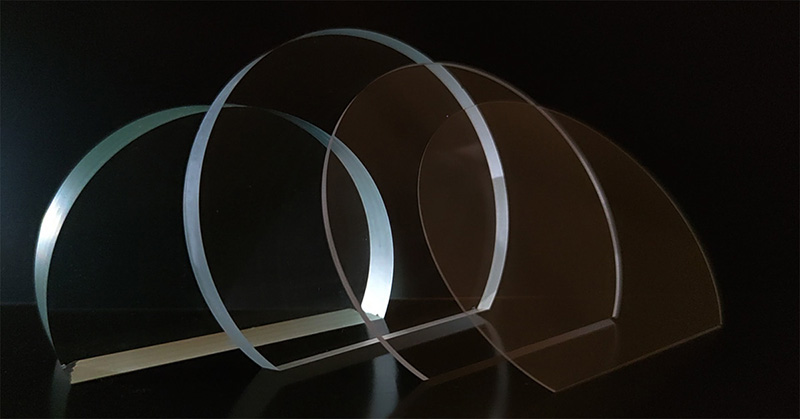
How Glass Laser Cutting Works
Glass ultrafast laser cutting utilizes ultrashort pulse lasers (such as femtosecond lasers) to focus extremely high energy density on the glass surface. This results in rapid local heating and evaporation, causing nonlinear optical effects in the glass under the laser pulse. These effects generate micro cracks and enable precise cutting. The cutting cross-section is composed of countless tiny perforations, and complete cutting of the glass is achieved through external stress. This method offers high precision, a low heat-affected zone, and no mechanical stress.
Application of Picosecond Laser Cutting for Glass
Laser glass cutting is widely used in industries such as household appliance glass, medical glass, display panels, and photovoltaic silicon wafers, with cutting thicknesses ranging from 0.1mm to 10mm. The cutting quality is stable and precise, with edge chipping less than 10μm, nearly invisible (micron-level). For cutting quartz glass, there are thickness limitations mainly due to the difficulty of cracking the material. Single-pass cutting can achieve a thickness of up to 6mm, while multiple passes can achieve a cutting thickness of 36mm, with cutting speeds ranging from 200-300mm/s.
Picosecond lasers have shown exceptional high precision and efficiency in LCD glass cutting. The picosecond laser pulse generates a high energy density, enabling fast and precise cuts while avoiding material damage caused by thermal effects and vibrations, which are common in traditional laser cutting. This ensures the quality and reliability of LCD glass.
Moreover, the extremely short pulse duration allows the material to evaporate quickly, significantly reducing energy loss. Compared to traditional lasers, picosecond lasers not only greatly improve cutting speed but also effectively reduce production costs. The efficient cutting process enhances production efficiency, opening up more possibilities for the development of LCD glass processing.
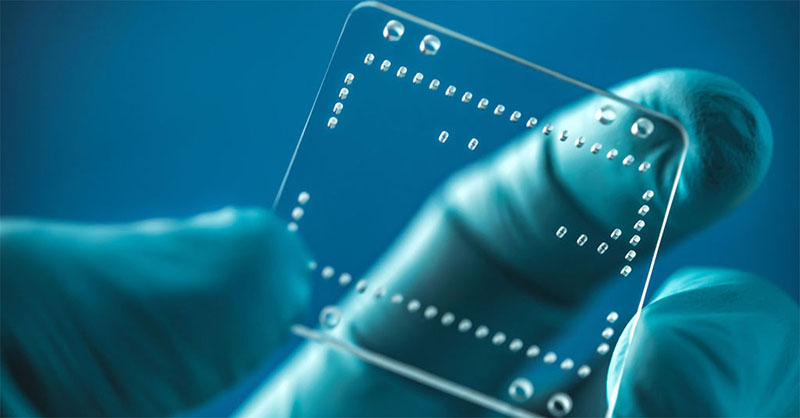
How Glass Picosecond Laser Drilling Works
Glass laser drilling works by focusing the laser beam into pulse energy, removing glass material point by point. During the process, the laser focus moves rapidly along a predefined path via a galvanometer, removing material layer by layer. The drilling progresses in a spiral pattern from bottom to top, with the laser focusing on the material’s lower surface and removing material from the bottom layer by layer until the glass is completely drilled or cut through.
Application of Laser Glass Drilling Machine
Laser glass drilling is widely used in fragile materials such as photovoltaic glass, household appliance glass, medical glass, and aerospace glass. It can process irregular and micro-sized holes. Compared to traditional mechanical processing, laser drilling offers advantages such as higher yield, greater precision, smaller edge chipping, and minimal taper. Picosecond laser drilling machines for glass support a wide range of hole diameters, with the smallest diameter reaching 0.04mm. They also provide fully automated line solutions suitable for large-scale production, enabling 7×24 hours of uninterrupted manufacturing.
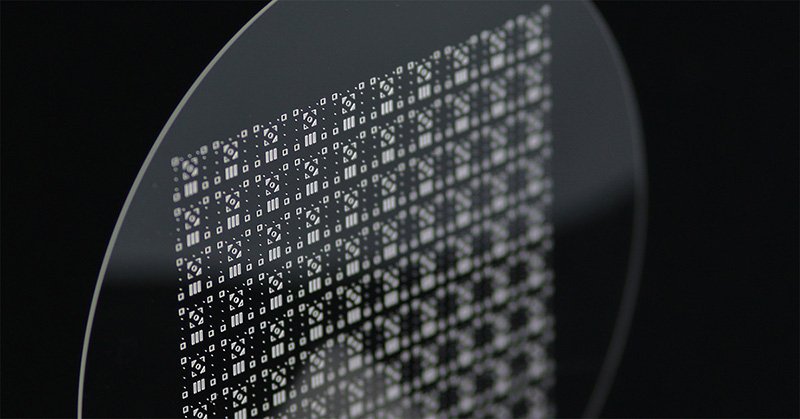
Glass Picosecond Laser Marking
Laser marking mainly includes surface engraving and internal engraving in glass.
- Surface Marking
Surface marking involves the laser emitting high-energy laser beams that are focused onto the glass surface. The energy density of the laser reaches the threshold that causes the surface material to instantly melt and vaporize. By controlling the path of the laser on the surface, the material is locally removed, forming the desired pattern. Picosecond laser surface marking has the advantage of a small heat-affected zone, preventing material thermal deformation and significantly reducing internal stress during the process.
Wear Resistance: The marking will not fade due to environmental factors (such as touch, temperature, etc.).
Anti-Counterfeiting: Once the pattern is formed, it is difficult to replicate or alter, providing strong anti-counterfeiting functionality.
For example, using UV picosecond lasers to mark QR codes on glass surfaces results in no noticeable bumps when touched, and the code points remain clear. Similarly, picosecond lasers have been widely applied in the semiconductor industry for QR code traceability.
- Laser Glass Internal Engraving
Internal glass engraving involves focusing the laser beam inside the glass. The high energy density laser pulses cause the glass interior to form micro cracks, ranging from microns to millimeters in size. These micro cracks scatter light and appear white. By controlling the laser path inside the glass, desired patterns are etched.
Laser Black Marking
Laser black marking is achieved by placing a stainless steel sheet beneath the glass and maintaining a tight connection. The laser is focused at the interface between the glass and the stainless steel, where the stainless steel releases carbon particles under high temperature and pressure. These particles adhere to the glass surface, forming a black mark.
Laser Color Marking
Laser color marking works by altering the refractive index within the glass to form a grating-like structure. This creates a dazzling color effect within the transparent, brittle material.
Micro-Structuring of Glass Surfaces
Laser processing technology can create fine microstructures on glass surfaces, such as tiny protrusions or indentations, with high efficiency and speed. For example, microstructures processed on the cover glass of solar energy devices can significantly reduce light reflection losses, thereby improving the photoelectric conversion efficiency of solar cells. On optical glass components, micro structuring can greatly enhance imaging uniformity and clarity, improving the overall quality of optical instruments. Additionally, micro channels created on glass surfaces enable precise injection and flow of micro fluids, widely applied in microfluidic technology.
Infrared Picosecond Laser Cutting Machine
The picosecond laser cutting machine has a wide range of applications, suitable not only for cutting conventional flat glass but also for processing various brittle materials such as specialty glass and glass-ceramic composites. It demonstrates significant potential in processing PCB, FPC, flexible glass, and ultra-thin glass. This technology is extensively applied in the production of high-precision glass panels, including smartphone screens, flat coated lenses, LCD material cutting, sapphire cutting, automotive central control glass, displacement screens, and glass components in the LED manufacturing industry. Additionally, picosecond laser cutting technology is used to fabricate complex shapes for automotive parts such as car windows, rearview mirrors, and dashboards.
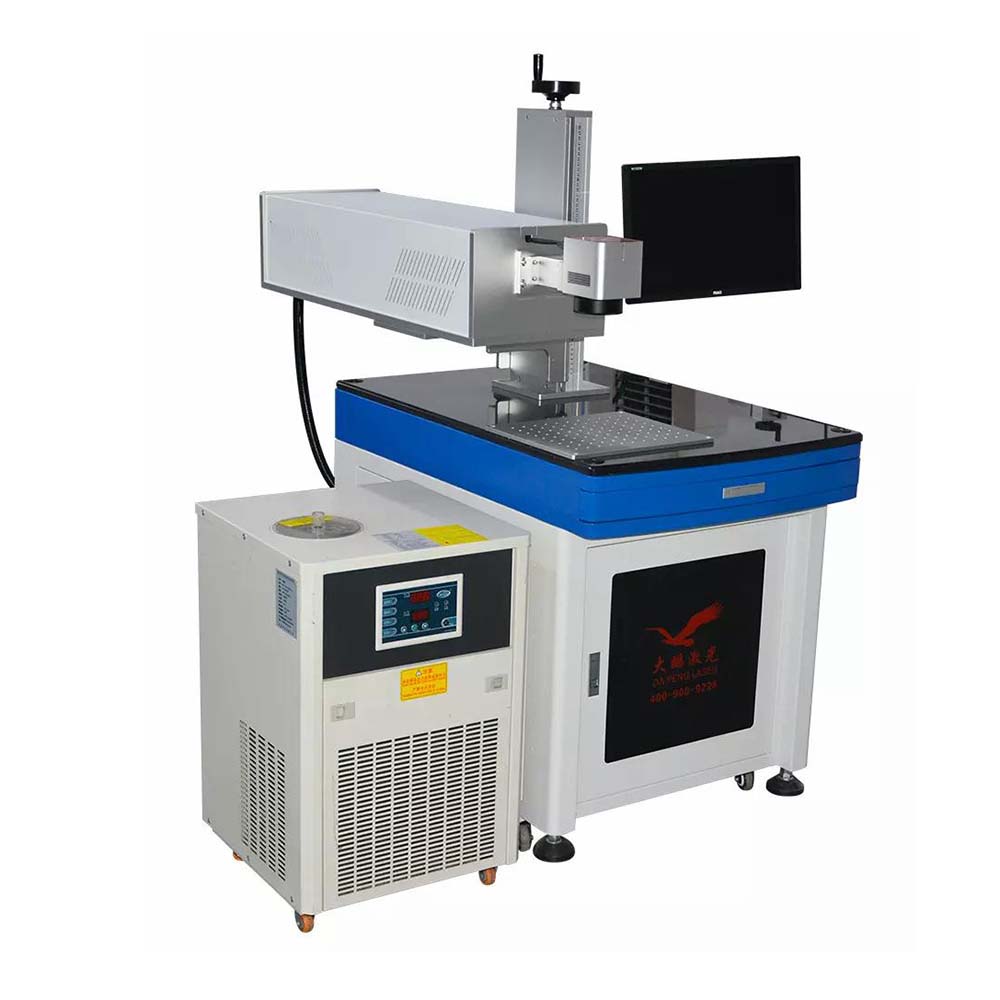
Dapeng Glass Laser Micro Drilling Machine
The Dapeng laser micro drilling machine employs advanced ultrafast laser technology to achieve smooth, crack-free drilling results. The edge chipping of drilled holes is controlled between 0.25~0.4 microns, making it particularly suitable for high-precision glass processing needs.
Advantages of Ultrafast Laser Cutting Machine
Ultrafast lasers exhibit excellent adaptability, particularly when processing brittle materials. This technology enables the flexible cutting of complex and irregular shapes that are difficult to achieve with traditional methods. The laser scribing and breaking process further enhances cutting edge quality and precision, with debris sizes typically smaller than 10μm, significantly reducing the time required for grinding and polishing.
In terms of performance, the equipment offers high processing efficiency, cutting 2mm thick glass at speeds of up to 800mm/s, greatly improving production efficiency.
- Cost-Effective, High Precision, and Minimal Surface Finish Requirements
- No melting or micro-cracks along the edges.
- High aspect ratio up to 1:100.
- Capable of producing extremely dense hole arrays.
- Zero taper
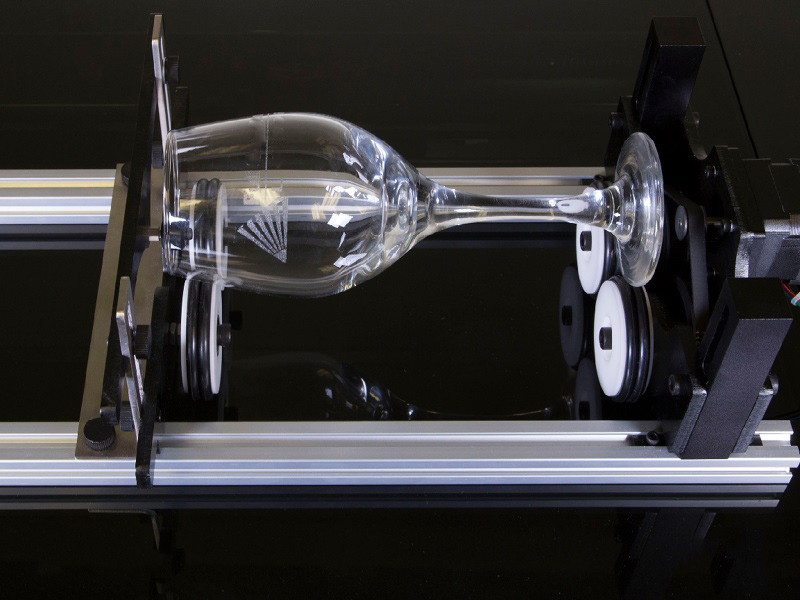
Comprehensive Glass Laser Micro Machining Solutions
DPLASER offers a full range of glass processing laser solutions, including cutting, marking, drilling, and engraving. With the continuous advancement of smart manufacturing, QR code traceability systems have been widely adopted across various industries. Dapeng provides specialized laser solutions for glass processing production lines. These systems can operate independently or integrate seamlessly into production lines, offering the advantages of low energy consumption and low operating costs.
In conclusion, ultrafast laser technology has revolutionized the way glass is processed, offering unmatched precision, efficiency, and versatility compared to traditional methods. From large format cutting to micro drilling and marking, ultrafast lasers enable manufacturers to meet the demanding requirements of modern industries with ease. With DPLASER ultrafast laser solutions and laser glass drilling machine, businesses can achieve superior quality and high-precision micromachining.