The robot laser application we refer to is an automated production equipment that integrates laser technology and robotics. With the development of society and scientific progress, the application of industrial robots is increasing in both quantity and scope. Industrial robots can greatly liberate labor, improve labor efficiency, and enhance product competitiveness. Many countries are actively conducting research on laser robot technologies to take the initiative in future market competition. In the long term, the robotic applications in manufacturing has great development prospects.
Laser Welding
Laser welding is one of the most popular applications for robotic automation. An automated laser welding system is usually integrated using several components such as a fiber coupling system, a high power fiber-optic deliverable laser, a laser processing head, a six-axis robot arm and a laser table to improve the precision and quality of the weld.
Laser Cutting
Automated laser cutting offers exceptional opportunities to improve throughput, speed and consistency. The synergistic operation of the feeder and laser cutter enables repeated cuts of the same specification material, as well as greater flexibility to accommodate constant changes in size, width, part or quota. This flexibility allows the line to operate efficiently with varying demands, ensuring both cut quality and increased productivity.
Laser Marking
The robotic application of industrial laser marking ensures accurate and repeatable marking on all types of materials, enabling continuity and traceability of the production process. Companies can tightly integrate feeding and marking systems into their manufacturing or welding lines to improve product traceability. This highly automated laser marking system not only improves marking accuracy, but also provides an easier means of monitoring and managing the production process.
Benefit of Robot for Laser Applications
Robotic laser systems are characterized by precision, accuracy and high speed. Compared to traditional welding methods, laser applications can significantly improve the process, allowing for finer and more efficient production. While traditional methods may have a large acceptable margin of error, the precision and consistency of laser technology helps to improve product quality and reduce the rate of defects in production. This advanced laser automation system not only improves the accuracy of the manufacturing process, but also brings a more flexible and efficient production environment to the organization.
Laser robotics is a close integration of advanced robotics and laser processing, utilizing high-precision industrial robots to achieve more flexible laser processing tasks. The system supports online operation, which can be realized by users through the demonstration box, and also provides offline programming. The system generates a workpiece model by automatically inspecting the machined workpiece and further generates laser machining curves. In addition, it can directly utilize CAD data for processing, offering a wide range of application possibilities for laser surface treatment, drilling, welding, and mold repair processes. This comprehensive system is a breakthrough not only in terms of processing accuracy, but also in terms of flexibility and convenience in terms of operation and application areas.
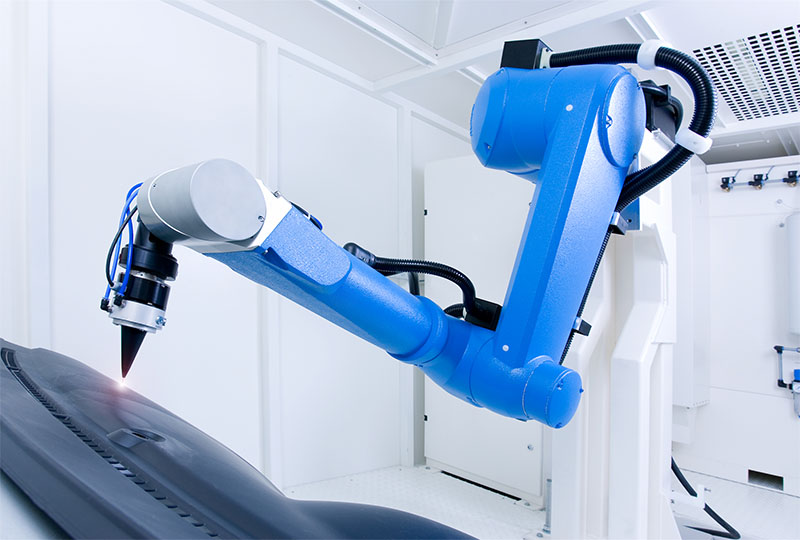
Robot Laser Application in Manufacturing
Laser Robots in Automotive Manufacturing
Robots laser application are widely utilized in the automotive manufacturing, where production processes are complex, primarily based on assembly lines, and the quality of welding procedures directly impacts overall vehicle manufacturing quality. In comparison to traditional welding techniques, laser processing robots exhibit outstanding technological advantages in welding.
Firstly, laser robots possess rapid and efficient welding speeds, coupled with exceptional accuracy. Secondly, the welding technology employed by laser processing robots produces smaller welding edges, providing more comprehensive protection for the automobile body. These features not only contribute to improving the quality of the welding process but also significantly enhance overall production efficiency.
Laser robots have a high degree of freedom, particularly excelling in industrial production scenarios that require dealing with complex spatial surfaces. Research results indicate that laser robots have the capability to achieve immediate and direct manufacturing in industrial production, offering reliable guarantees for the quality of the produced products. This flexibility and efficiency enable laser processing robots to achieve significant results when addressing highly complex production tasks, injecting new vitality into industrial manufacturing.
In the automotive manufacturing process, the application of robot laser welding technology not only contributes to enhancing production quality but also effectively ensures the quality and safety performance of the vehicle body. This advanced welding technology brings new development opportunities to the automotive industry, providing a more reliable and efficient solution for production manufacturing.
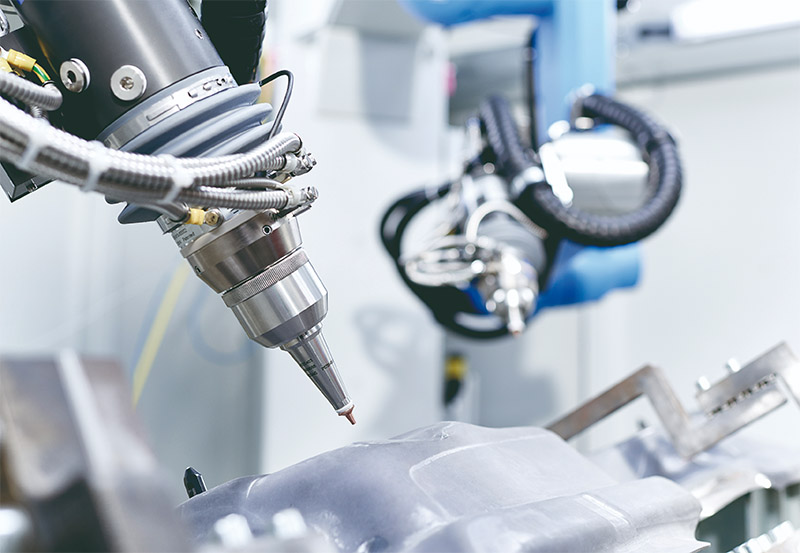
Laser Robots for Electronics Industry Manufacturing
In electronic manufacturing, laser welding robots can achieve precise and stable welding, ensuring the quality and reliability of electronic components. For example, laser welding robots can be used for the connection of electronic components, such as welding battery cells and circuit boards. Additionally, laser welding technology can meet the demand for small-scale connections in the manufacturing process of microelectronic devices, enhancing product performance and reliability.

Laser Robots for Metals Fabrication
In the field of metal fabrication, laser welding technology demonstrates its outstanding performance in achieving high-quality weld joints, providing products with excellent aesthetics and stable performance. Particularly in the welding of stainless steel products, laser welding robots play a crucial role and find widespread application in the manufacturing of kitchenware, medical instruments, and other products.
The laser welding technology is mainly manifested in its high precision and controllability, resulting in more uniform and flawless weld joints. This precision helps ensure the visual quality of the products, presenting a satisfying appearance. Simultaneously, due to the small heat-affected zone generated during the laser welding process, the performance of the products is more stable and reliable after welding.
Of particular note is the application of laser welding robots in the realm of stainless steel products, such as the manufacturing of kitchenware and medical instruments. This not only enhances the production efficiency of the products but also ensures their hygiene and durability. This advanced welding technology injects new productivity and competitiveness into the manufacturing of metal products, delivering high-quality, high-standard finished goods.
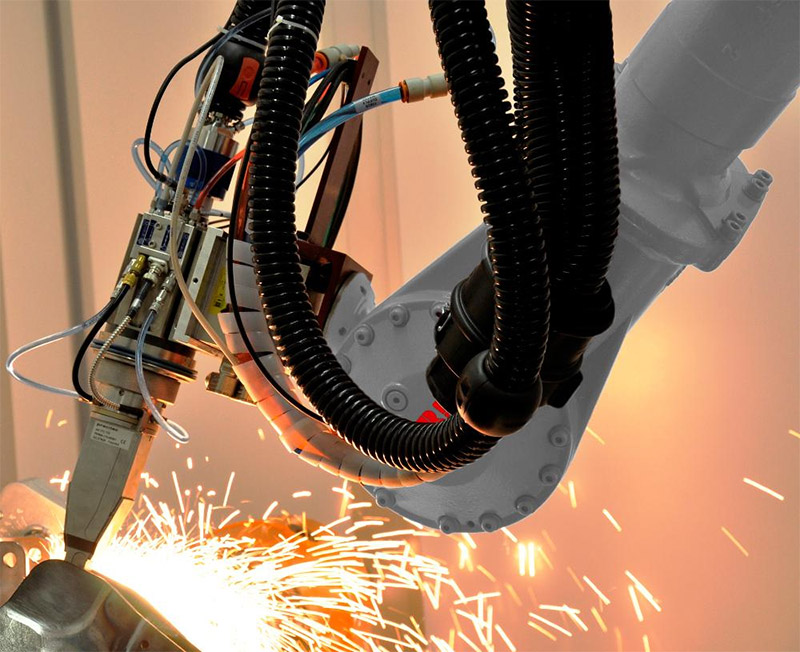
Robotic Welding Automation in Shipbuilding
In shipbuilding, laser welding robots play a crucial role in meeting the high standards for welding quality and efficiency. These robots achieve precise welding of ship components, reducing deformation and defects. This significantly improves the quality of weld joints, enhancing the overall reliability of ship structures. The shipbuilding industry, by using laser welding robots, aims to improve both welding efficiency and the quality of weld joints, positively impacting the overall performance and ensuring the safety and reliability of ships in challenging sea conditions.
Laser Robotic application for Petrochemical Industries
Laser welding robots play a key role in the petrochemical industry, covering the cutting and joining of equipment such as pipes, vessels and various steel structures. The efficiency and automation features of such robots make them ideal for joining pipes and vessels. Laser welding technology enables fast and reliable connections to be made in piping systems, improving the overall efficiency of the project. Meanwhile, for the manufacturing of steel structures and other equipment, laser welding robots are able to achieve high-precision welding during the production process, ensuring product quality and stability.
Laser welding robots bring significant advantages to the petrochemical industry with their high efficiency, automation and high precision, realizing significant savings in workload and significant improvement in work efficiency.
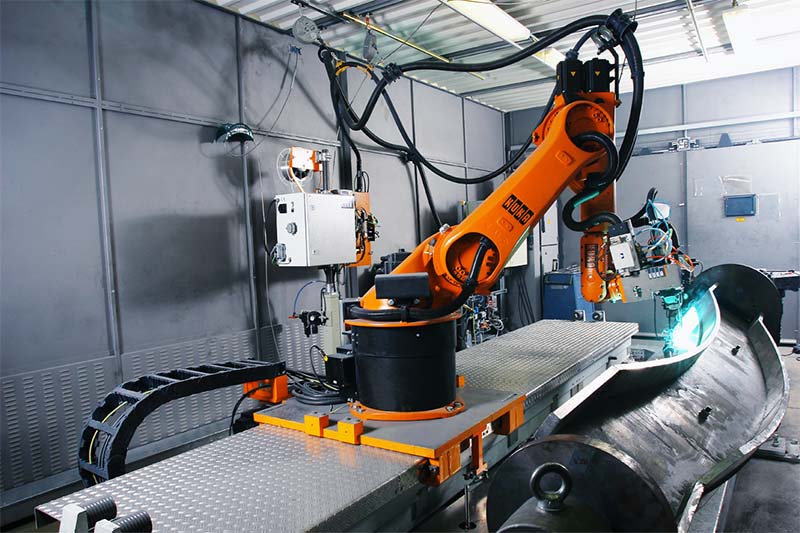
Parameters of Robotic Laser Systems
Matching Welding Speed with Quality: The choice of welding speed must be coordinated with welding quality. Excessive welding speed may lead to welding defects such as deviation, insufficient welding, and leakage. Conversely, too slow welding speed can affect product production efficiency. Therefore, welding speed, as a key indicator determining welding efficiency, needs to be fine-tuned while ensuring quality.
Rated Load of Robot Arm: This metric refers to the load that the end of a robot laser welding machine can bear. The rated load on the wrist directly affects its arm reach and the specifications of welded components, including the welding gun, cables, visual sensors, wire feeding tubes, and more. This consideration is crucial for ensuring the robot’s robust operation and adaptability to different welding conditions.
Axis and Flexibility: The number of axes affects the flexibility of the robot laser welding machine. The more axes it has, the more flexible the robot is, capable of handling a wider range of welded part specifications, expanding the scope of welding applications.
Arm Reach and Welding Radius: The arm reach of the robot laser welding machine reflects its welding radius. A longer arm reach corresponds to a larger welding radius, allowing the robot to handle larger welded part specifications. Users can choose the appropriate arm reach based on welding space, part specifications, and welding requirements.
Robot Weight: The weight of the robot laser welding machine varies with specifications. Weight is closely related to arm reach and welding range. Selecting a robot with the appropriate weight helps ensure its stability and reliability during operation.
Repeat Positioning Accuracy: The welding accuracy that the robot laser welding machine maintains during repetitive actions. Only a robot laser welding machine with high repeat positioning accuracy can ensure welding precision without deviation. Balancing welding quality and positioning accuracy is crucial while pursuing efficiency.
Movement Speed: The movement speed of the robot laser welding machine is a key indicator, requiring it to complete multiple small-distance multi-point positioning in a short time. To guarantee welding quality, it also needs to maintain high positioning accuracy (typically 0.25mm) and sufficient load capacity to adapt to variable welding conditions.
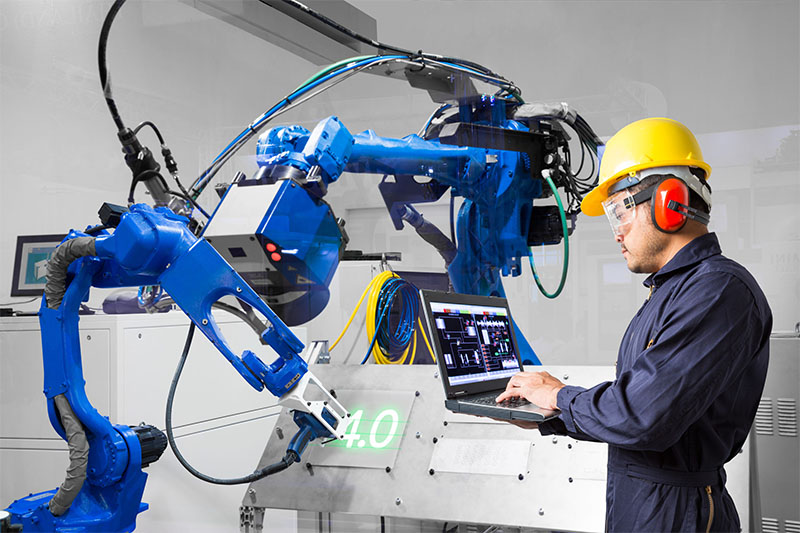
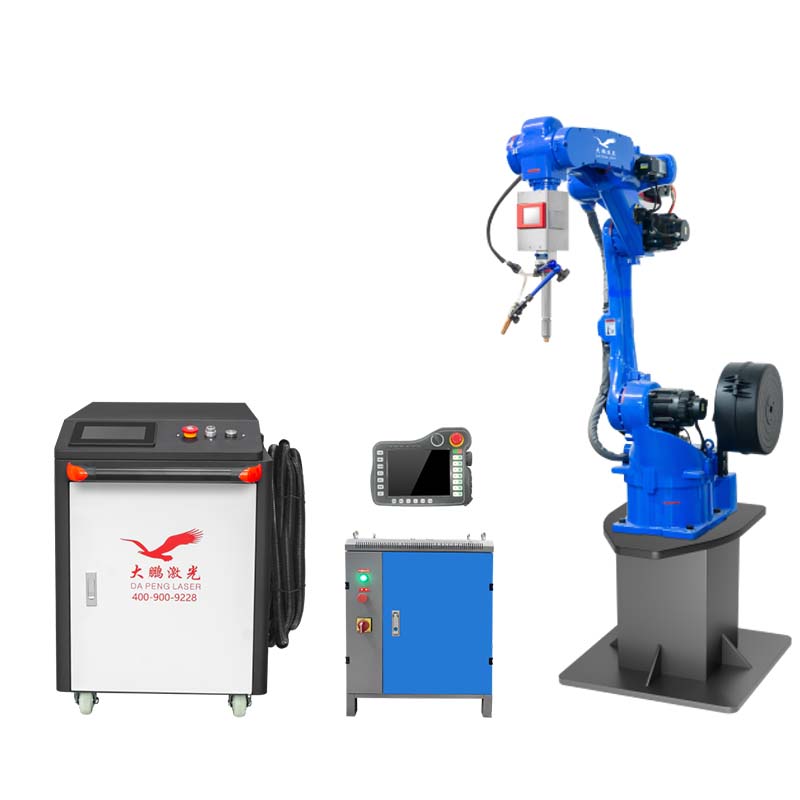
Overall, laser automation systems for manufacturing demonstrate outstanding potential applications in various fields. In processes such as manufacturing, welding, and cutting, laser robots bring a multitude of possibilities to the production process with their efficient, flexible, and precise characteristics. These laser robot systems not only enhance production efficiency but also provide the manufacturing industry with more innovation and impetus for sustainable development, marking the leading position of laser technology in industrial automation. In the future, with the continuous evolution of technology, laser robot automation systems will continue to bring more advanced and efficient solutions to the manufacturing industry, propelling industrial production towards a more intelligent, precise, and sustainable direction.