Laser cleaning is a process that involves directing a high-energy density laser beam onto the surface of a workpiece, causing contaminants, oxide layers, coatings, or other deposits on the surface to instantaneously melt, ablate, evaporate, or peel off due to the heat. This process cleans the workpiece surface without damaging the base material, making it an ideal choice for next-generation industrial cleaning technology. By focusing the laser through lenses and using a Q-switch, energy can be concentrated into a very small spatial and temporal range. Laser cleaning has significantly enhanced industrial cleaning needs, so what will affect laser cleaning of metal?

Advantages of Fiber Laser Cleaning
- Eco-friendly and Fast
Laser cleaning is a “green” cleaning method that does not require any chemical agents or cleaning fluids, resulting in no chemical reactions or pollution from the waste material. The process involves instantaneous heating and vaporization, making it very fast—usually completed within seconds to a few minutes. Traditional cleaning methods are time-consuming, often requiring soaking and repeated cleaning to achieve the desired results.
- Effectiveness
Conventional cleaning methods are often contact-based, applying mechanical force to the surface, which can damage the surface or leave residues that cause secondary pollution. Laser cleaning is non-abrasive, non-contact, and free of thermal effects, thus preserving the integrity of the base material.
- High Automation
Laser cleaning can be integrated with robotic arms and robots for remote operation, achieving automated cleaning, reducing labor costs, and minimizing human errors.
- Control Advantages
Lasers can be transmitted through optical fibers, allowing the laser beam to reach areas that are difficult for traditional methods to clean. Laser cleaning can remove various types of contaminants from different materials, achieving a level of cleanliness that conventional methods cannot. Moreover, it selectively cleans contaminants from surfaces without damaging the material.
- Cost and Labor Saving
Laser cleaning is fast and efficient, saving time. Although the initial investment in a laser cleaning system may be high, the system can be used long-term with low operating costs. Additionally, it easily enables automated operations.

Factors Affect Laser Cleaning Metal
Several factors affect the efficiency and effectiveness of laser cleaning metal surfaces:
1. Laser Power: 200W~500W laser cleaning machines typically offer high cleaning efficiency. However, this efficiency can be influenced by the thickness and hardness of the oxide layer on the weld surface. Thinner and softer oxide layers may be easier to remove, while thicker and harder oxide layers may require higher laser power.
2. Laser Parameters: Cleaning efficiency also depends on laser parameters, including pulse energy, frequency, and pulse width. Proper laser parameter settings can enhance cleaning efficiency.
2.1 Laser Wavelength: Different lasers such as Nd:YAG, fiber, or CO2 have varying advantages and disadvantages when cleaning different materials.
2.2 Laser Type: Fiber lasers, pulsed lasers, and continuous wave lasers are chosen based on the material to be cleaned, the thickness of the contaminants, and the required cleaning speed.
2.3 Power and Pulse Duration: Higher power and shorter pulse durations typically remove hard or stubborn deposits more effectively.
2.4 Pulse Repetition Rate: This determines the frequency of laser pulses. Higher repetition rates can speed up the cleaning process but may also increase heat buildup, potentially damaging the substrate. A balance must be struck between cleaning efficiency and substrate protection.
2.5 Energy Density: This dictates the amount of material ablated by each laser pulse. Higher fluency speeds up the cleaning process, but excessive fluency can lead to substrate overheating and damage. Optimizing fluency can effectively remove contaminants while protecting the substrate.
2.6 Spot Size: The size of the laser focus point determines the area that can be cleaned in one pass. The spot size is directly proportional to the focal length. During the adjustment of the parameters, you can choose the appropriate focal length according to the actual need to achieve the desired spot size.
3. Materials: Laser cleaning machines can clean various materials, including metals, plastics, rubber, ceramics, glass, and stone. Different materials require specific laser parameters and cleaning strategies, necessitating adjustments based on the actual situation. Some metal surfaces may have oxide layers or grease that need pre-treatment with other methods before laser cleaning.
4. Cleaning Head and Optical System: The quality and performance of the cleaning head and optical system in a laser cleaning machine impact cleaning efficiency. High-quality optical systems provide more precise laser focusing, enhancing cleaning effectiveness.
5. Cleaning Distance and Speed: The distance between the laser cleaning machine and the object, as well as the cleaning speed, also affect efficiency. Generally, positioning the laser closer to the weld and moving the beam at an appropriate speed can improve cleaning efficiency.
6. Size of the Cleaning Area: Laser cleaning systems need proper programming and adjustments to suit different cleaning area requirements. Cleaning complex geometric areas may require more time and technical expertise to achieve the same level of cleanliness.
Higher-speed, more efficient laser cleaning equipment typically comes with a higher price tag. These machines can handle larger workloads and reduce downtime, making them cost-effective in the long run. However, by thoroughly understanding the factors that influence laser cleaning efficiency and improving operational techniques, significant improvements in cleaning efficiency can also be achieved. This means that investing in expensive equipment may not be necessary to achieve high-efficiency cleaning.

Industrial Laser Cleaning Applications
Laser cleaner meets the needs for surface cleaning of various materials. In practical laser cleaning applications, continuous fiber lasers are used less frequently. However, for certain large steel structures, pipe, and other similar applications, continuous fiber lasers cleaning can be chosen due to the large volume and rapid heat dissipation of these structures, and the lower requirements for minimizing damage to the substrate.
New energy power battery | Lithium Battery Components: Cleaning of electrode sheets, electrode pillars, filling ports, cover plates, and blue film. |
Aerospace | Engine Parts: Pre-weld and post-weld cleaning of engine components, removal of paint and mold release agents from composite materials, aircraft skin stripping, and sealant removal. |
Molds | Molds: Paint, rust, and grease removal from tire molds, packaging molds, injection molds, seal ring molds, and food molds. |
3C industry | Electronics: Paint removal from circuit boards, wafer cleaning, phone case paint removal, and PVD coating fixture cleaning. Cleaning of fine particles and residues from precision electronic components, circuit boards, and semiconductor wafers. |
Automobile manufacturing/marine ships | Automotive: Pre-weld body cleaning, wheel cleaning, selective paint removal from the car body, silent tire cleaning, post-weld cleaning, and removal of paint and oil from parts. |
Petrochemical industry | Offshore Oil Platforms: Coating removal; paint, rust, grease, oil, and various types of dirt and grime removal from pipelines. |
Construction industry | Cultural Heritage and Construction: Cleaning of building walls and materials, rust removal from construction materials. |
Thermos cup | Household Items: Paint removal from the bottom and walls of thermos cups. |
Other industries | Metal Components: Cleaning of metal oil filters, filter tubes, stainless steel polishing; laser rust removal and oxide removal. |
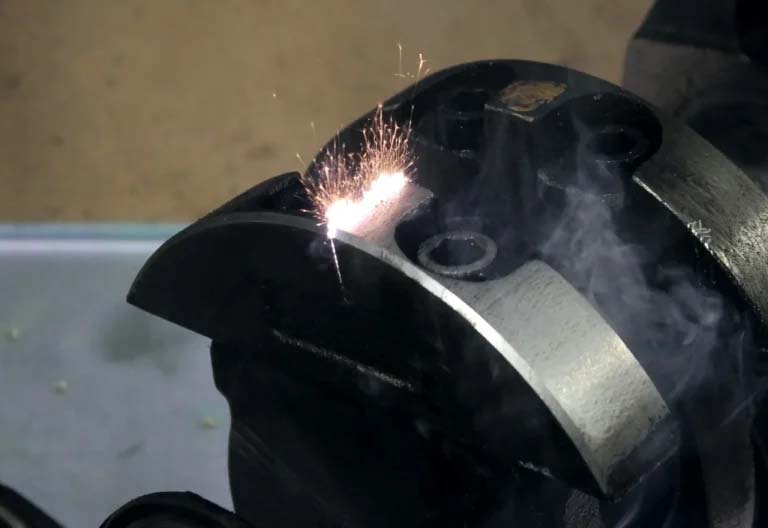
Can Fiber Laser Cleaning Machines be used for Paint Removal?
Due to the low absorption rate of fiber lasers by paint and the higher absorption rate by underlying metals, traditional fiber laser cleaning machines often have lower paint removal efficiency and can damage the substrate metal. However, Dapeng Laser’s fiber laser cleaning machines can still achieve good results for thin layers of paint.
Several factors affect the efficiency of laser paint removal, including laser power, laser energy density, scanning method and speed, defocus amount, beam quality, and whether the laser is continuous or pulsed. Each factor influences paint removal efficiency, and the optimal laser parameters must be selected based on different types of paint and substrate materials to achieve maximum efficiency.
Dapeng Laser has developed specialized laser cleaning system for paint removal, tailored to different types of paint. Through technological upgrades, Dapeng fiber laser cleaning significantly improves paint removal efficiency, meeting most paint removal application needs.
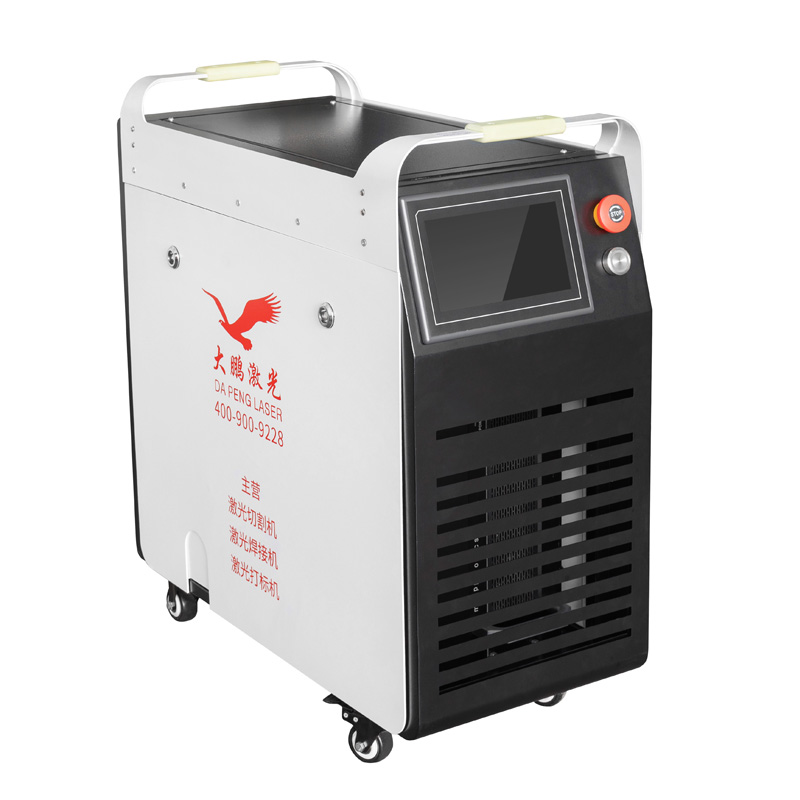
Summary, laser cleaning, with its non-damaging, efficient, and environmentally friendly characteristics, plays a significant role in various industries. By understanding the advantages of laser cleaning and what factors affect laser cleaning effectiveness, can help you achieve optimal results in practical applications. We hope the information provided in this article will offer you practical guidance and reference for the field of metal cleaning.