In traditional material processing using long-pulse lasers, the primary interaction between the laser and the material relies on converting laser energy into heat, causing the material to melt and vaporize for removal. However, this process leads to significant heat accumulation, resulting in a large and intense heat-affected zone (HAZ). In precision machining applications, excessive heat can cause undesirable effects such as thermal deformation, molten edges, oxidation, discoloration, residue, and burrs. Ultrafast lasers, including nanosecond, picosecond, and femtosecond lasers, have revolutionized precision manufacturing with their ability to deliver extremely short and high-intensity pulses. Ultrafast laser manufacturing minimizes heat-affected zones (HAZ), enabling cleaner cuts, finer details, and minimal material damage.
Why use Ultrafast Lasers for Industrial Applications?
The ultra-short pulse width and ultra-high peak power of ultra-fast lasers can induce non-linear absorption effects in the material, obtaining a focal spot with a size much smaller than the diffraction limit, thus greatly enhancing the spatial resolution of processing. Therefore, picosecond femtosecond laser processing process without heat generation, commonly known as “cold” processing, can use ultra-fast laser on any material for ultra-fine cutting, punching, etching and other processing, can be directly avoided in the process of conventional long-pulse laser processing, material due to the accumulation of heat caused by overheating cracking, oxidation, melting and other phenomena.
Ultrafast lasers deliver light energy from a tightly focused femtosecond or picosecond laser in pulses that are directed to highly specific locations in the material. This process is realized by two- or multi-photon excitation and occurs on extremely short time scales, much faster than the exchange of thermal energy between electrons and lattice ions induced by optical excitation.
Ultrafast lasers, such as femtosecond lasers (fs), play a key role in applications requiring high precision, especially when working with brittle and hard transparent materials. These lasers are able to precisely process brittle materials without inducing excessive heat-affected regions, thus maintaining the structural integrity of the material.
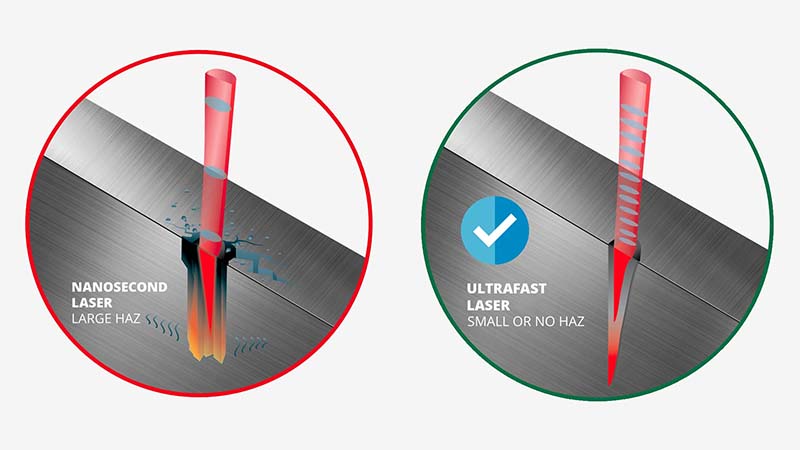
What Are Ultrafast Lasers Used For?
Nanosecond, Picosecond, and Femtosecond Ultrafast Laser Cutting Machines
In ultrafast laser processing, nanosecond (ns), picosecond (ps), and femtosecond (fs) refer to the time control units of the laser processing duration. Typically, laser processing involves delivering single-pulse energy to the material surface within an extremely short time frame. Through high-frequency repetition, this enables applications such as drilling, cutting, and marking.
Since 1 second = 10⁹ nanoseconds = 10¹² picoseconds = 10¹⁵ femtoseconds, laser processing equipment is often named based on these time scales.
Ultrafast laser cutting machines are particularly well-suited for materials such as glass, plastic films, heat-sensitive materials, and brittle substances due to their unique cutting capabilities. The ultra-short pulses of femtosecond or picosecond lasers minimize thermal effects, preventing heat from spreading through the material. This is crucial for materials like glass and plastic films, which are sensitive to thermal stress and can crack or deform when exposed to high temperatures.
For heat-sensitive materials, ultrafast lasers ensure precise cutting without causing unwanted thermal damage, preserving the integrity of the material. When cutting brittle materials like ceramics or glass, the laser’s ability to deliver high energy in extremely short bursts allows for fine, controlled cuts that prevent the material from fracturing or shattering.
In addition, ultrafast lasers can achieve fine, clean edges with minimal post-processing required, making them ideal for applications where high precision and high-quality finishes are critical. This makes ultrafast laser cutting an excellent choice for industries such as electronics, medical devices, and precision manufacturing.
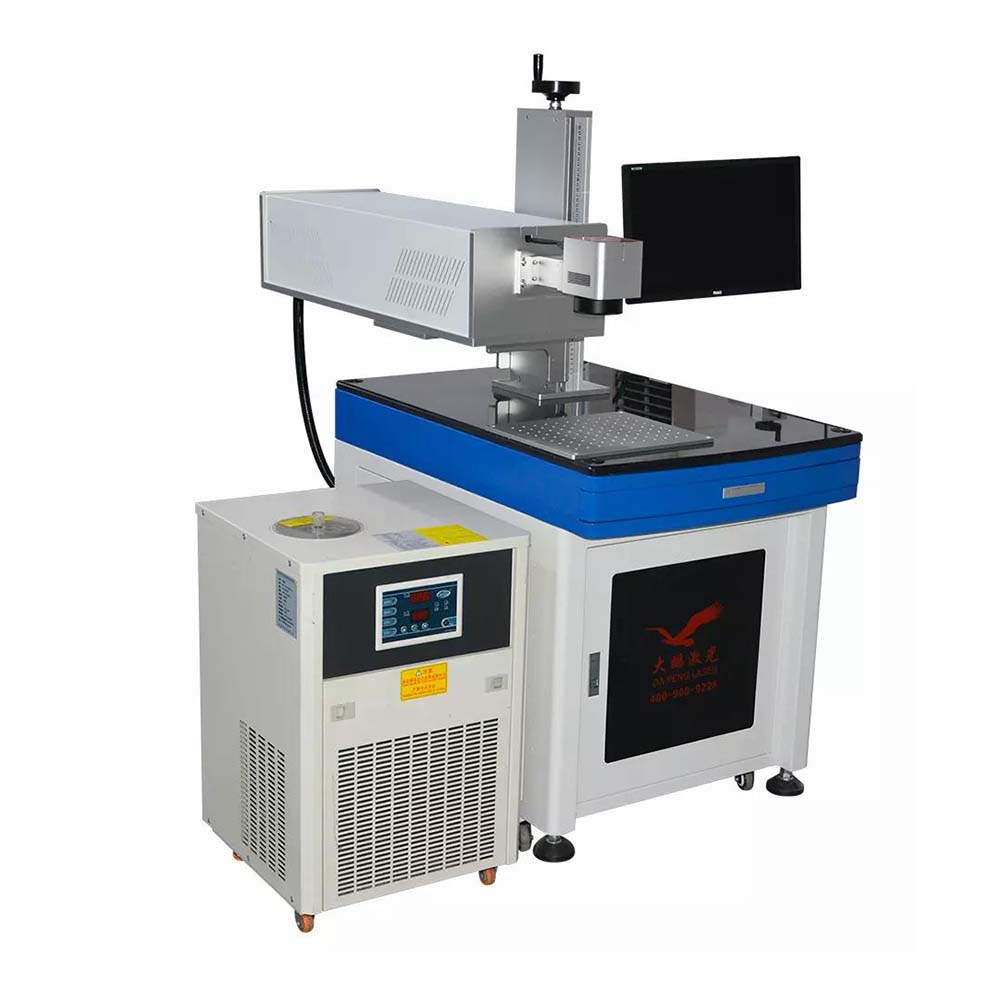
Picosecond, Femtosecond Pulsed Lasers for Material Micromachining
The shorter the processing time, the less time the laser interacts with the material surface, resulting in minimal thermal effects and improved processing quality. Depending on the material’s specific requirements, corresponding nanosecond, picosecond, or femtosecond laser equipment is chosen. For instance, a nanosecond UV laser cutting machine is commonly used for thin film processing, a picosecond UV laser cutting machine is ideal for brittle materials, and a femtosecond UV laser cutting machine is typically employed for processing conductive films, oxides, and similar materials (UV lasers refer to those with a wavelength of 355nm).
Femtosecond vs. picosecond laser material processing
Picosecond laser drilling is one of its common applications, where the laser efficiently creates holes through an impact drilling technique while ensuring uniformity. In addition to circuit boards, picosecond lasers can also perform high-quality drilling on materials such as plastic films, semiconductors, metal films, and sapphire.
Line ablation (removal of coatings) is another application of picosecond lasers in micromachining, capable of precisely removing coatings without or with minimal damage to the underlying material. Ablation can range from narrow lines a few microns wide to larger areas spanning several square centimeters. Since the coating thickness is typically much smaller than the ablation width, heat transfer along the edges of the coating is limited, allowing for processing with nanosecond laser pulses.
Femtosecond laser pulses, with their ultra-short duration, can efficiently remove material in very small areas while minimizing the thermal impact on the surrounding region. Precision laser cutting is one of the typical applications of femtosecond lasers, and their exceptional cold processing capabilities make them suitable for a variety of materials, such as metals, ceramics, glass, polymers, carbon fiber-reinforced composites (CFRP), and even organic tissues.
While femtosecond lasers are being applied in cutting, drilling, welding, marking, peeling, and repair, their use is still not widespread. On one hand, other types of lasers can achieve similar results in many situations; on the other hand, femtosecond lasers are more expensive than pulsed or continuous lasers.
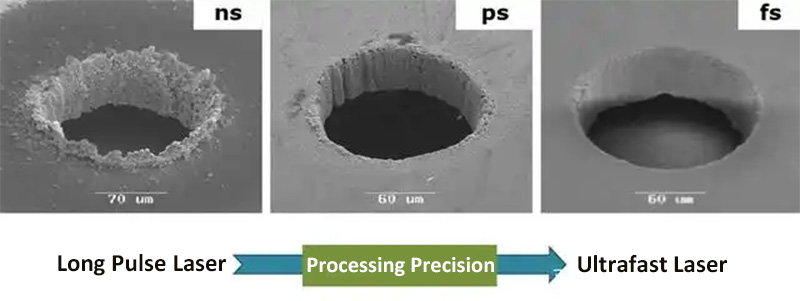
Micro-Nano Machining
Femtosecond laser technology can achieve sub-micron (less than 1 micron) processing precision, providing high-quality edge effects and extremely fine structures in the machining of metals, semiconductors, and composite materials. In the microelectronics and semiconductor fields, femtosecond lasers can perform high-precision cutting and drilling, creating smooth, burr-free microholes with diameters less than 10 microns. This capability makes them particularly suitable for manufacturing complex microstructures and nanostructures, such as integrated circuits, micro-electromechanical systems (MEMS), and functional metasurfaces. Additionally, femtosecond lasers can form tiny, complex circuit patterns through precision cutting and drilling, playing a key role in MEMS manufacturing for processing miniature mechanical and electronic components.
Non-Damaged Machining of Thermally Sensitive Brittle Materials
During femtosecond laser machining, an extremely weak or negligible heat-affected zone (HAZ) is achieved, allowing for high-precision machining without damaging the surrounding material. This makes it particularly suitable for processing thermally sensitive materials, such as polymers, glass, and biological materials.
Surface Microstructure Etching
In the medical field, femtosecond laser systems are widely used for manufacturing high-precision biosensors and microfluidic chips due to their exceptional processing accuracy and minimal thermal impact. These systems enable fine machining without damaging the material, ensuring the integrity and functionality of biological materials.
Industrial Picosecond and Femtosecond Laser Material Processing
Drilling
In circuit board design, ceramic substrates are gradually replacing traditional plastic substrates to improve thermal conductivity. During the manufacturing process, it is often necessary to drill up to hundreds of thousands of microholes with diameters ranging from 40-100μm in the substrate, while ensuring high precision in the drilling and protecting the thermal stability of the substrate.
Picosecond and femtosecond lasers, through impact drilling, can achieve uniform and high-quality hole processing, minimizing thermal input and its effect on the substrate. Furthermore, these laser technologies efficiently process materials such as plastic films, semiconductors, metal films, and sapphire to achieve precise drilling.
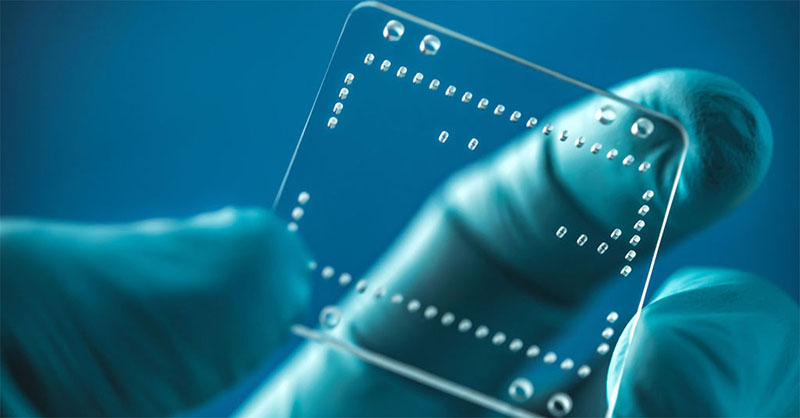
Laser Cutting
Ultrashort pulse laser ablation cutting, also known as ablative cutting, involves ablating the material layer by layer until it is completely cut through. This method provides extremely high cutting quality, making it particularly suitable for industrial applications that require exceptional precision.
Laser Marking
Ultrafast lasers perform exceptionally well in the field of laser marking, and they are widely used for surface processing of materials such as metals, plastics, and glass, particularly excelling in stainless steel color marking. With high pulse precision and energy control, ultrafast laser marking achieves fine, clear markings while minimizing thermal impact to avoid material deformation or damage. These markings offer excellent wear resistance and durability, along with aesthetic appeal and functionality, making them widely used in high-end manufacturing, electronic product identification, and optical component processing.
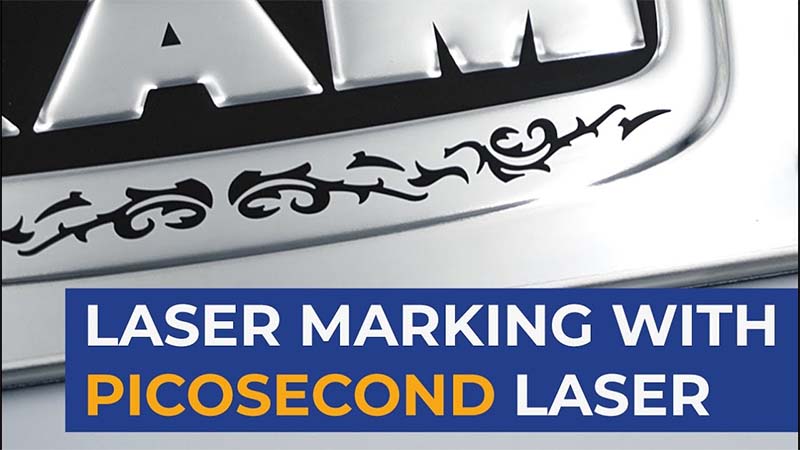
Coating Removal
Laser micromachining can also be used to precisely remove coatings without damaging or only lightly affecting the underlying material. Whether it is fine lines a few microns wide or large areas of coatings several square centimeters in size, lasers can efficiently remove them.
Nanosecond pulse width lasers are particularly suitable for this application due to their limited heat conduction properties.
By combining high average power lasers, square or rectangular optical fibers, and flat-top intensity distribution, laser surface ablation has found broad industrial applications. For example, ultrafast lasers can be used to remove coatings on thin-film solar cell glass and are widely applied in the automotive industry to remove anti-corrosion coatings in preparation for subsequent welding processes.
Surface Structuring
Surface structuring technology alters the physical properties of a material’s surface to achieve specific functions. For example, based on the lotus effect, laser processing can create hydrophobic microstructures on a material’s surface, causing water droplets to quickly roll off. By using ultrashort pulse lasers to create sub-micron level structures, precise surface regulation can be achieved.
The same technology can also be used to create hydrophilic surfaces or even larger structures. Surface structuring is widely used in industrial fields, such as designing microstructures on the inside surface of engine fuel tanks to reduce friction and wear, or forming microstructures on metal surfaces to enhance welding performance with plastics.
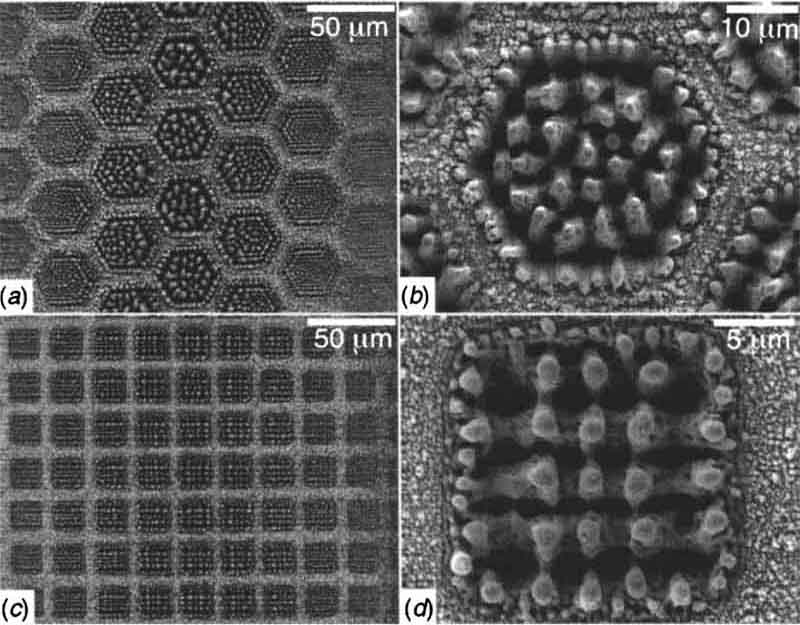
Carving and Molding
Carving and molding use laser ablation technology to create three-dimensional shapes. Although its scale may exceed traditional micromachining, its high precision demands place it within the realm of microprocessing.
Picosecond lasers are particularly suitable for processing polycrystalline diamond materials, which are extremely hard and commonly used in the manufacturing of milling cutter edges. Laser carving and molding can precisely cut polycrystalline diamond tools, especially in the creation of chip grooves and tooth structures on milling cutters.
Ceramic Welding
Welding ceramics has been a challenge in modern manufacturing, with traditional methods often unable to achieve reliable connections. Ultrafast lasers have become the only effective solution. Engineering ceramics, known for their excellent high-temperature resistance, are indispensable in demanding applications, but their joining technologies face significant challenges. Ultrafast lasers, with precise energy transfer, not only play a crucial role in additive manufacturing but also demonstrate high potential in ceramic welding, with successful cases of glass welding already achieved.
Scientists have developed an ultrafast pulsed laser welding technology that focuses light on the ceramic interface, inducing nonlinear absorption, which triggers localized melting instead of ablation, thereby achieving highly efficient welding. The key lies in the interaction between optical properties and the efficient coupling of laser energy. Ceramic components produced using this method exhibit excellent performance under high vacuum conditions, with shear strength comparable to metal-ceramic diffusion bonds.
The ultrafast laser glass micro-welding technique is based on the nonlinear absorption mechanism of ultrafast laser energy, enabling the plasma formation and subsequent reconfiguration of dissimilar materials at the microscopic scale of the bonding interface. Picosecond lasers have achieved a breakthrough in welding between metal and glass, while femtosecond laser pulses enable welding between glass-to-glass and glass-to-metal.
Ultrafast laser technology demonstrates unique advantages in welding transparent ceramics, as it can penetrate materials and join complex geometries, significantly expanding the welding volume and application scenarios. This makes it highly promising for use in harsh environmental equipment and optoelectronic product packaging.
Conclusion
Ultrafast laser applications are rapidly expanding, revolutionizing micro and precision manufacturing with their unmatched accuracy and minimal thermal impact. Their ability to perform micromachining, surface structuring, high-quality drilling, and welding with exceptional precision makes them indispensable for processing complex materials. By ensuring fine details, preserving material integrity, and enhancing processing efficiency, ultrafast lasers are set to play a pivotal role in advancing industrial manufacturing and driving future technological innovations.