Table of Contents
Robot laser welding machine is a kind welding equipment in modern industrial production. Compared with traditional welding system, robotic laser welding machines have many advantages, such as high precision, high efficiency, environmental protection, energy saving and high reliability. This article will introduce you to the many advantages of the best robotic welding systems in industrial applications.
Part 1: What are the Advantages and Disadvantages of Robotic Welding
At present, the research of robotic laser welding technology mainly focuses on high power lasers, high beam quality, high energy density laser devices, high efficiency power supply and automatic control technology. Robotic welding systems can help manufacturers and businesses simplify operations, reduce costs and increase production efficiency. Robots can also be a good solution to the shortage of qualified welders
1.1 Advantages of Robotic Welding
Robotic welding offers increased productivity, improved weld quality, enhanced safety, cost savings, flexibility, and the ability to collect and analyze valuable data. These advantages make it an attractive option for many manufacturing industries.
Increased productivity
Robots can work continuously without the need for breaks, resulting in higher productivity and increased throughput. They can also perform repetitive tasks with high precision and speed, reducing cycle times and improving overall efficiency.
Consistency and quality
Robotic welding ensures consistent weld quality as it follows programmed instructions with high accuracy. The robots can maintain a stable arc, consistent heat, and precise weld placement, resulting in stronger and more reliable welds. This reduces the likelihood of defects and the need for rework or repairs.
Improved safety
By using robots for laser welding tasks, human operators are removed from hazardous environments that involve exposure to high temperatures, fumes, and potentially dangerous welding operations. This improves workplace safety and reduces the risk of accidents and injuries.
Cost savings
While there are initial investments involved in setting up a robotic welding system, it can lead to long-term cost savings. Robots can work faster and more efficiently than humans, reducing labor costs. The consistent quality also reduces material waste and rework expenses. Moreover, robots can operate continuously, maximizing production time, and increasing overall profitability.
Flexibility and versatility
Robotic welding systems can be programmed to handle various welding applications and adapt to different production requirements. They can switch between different parts or welding configurations quickly and easily, allowing for greater flexibility in manufacturing processes. This versatility enables manufacturers to respond quickly to changing market demands and product variations.
High Automation & Intelligent
Compared with traditional welding, the biggest advantage of robotic laser welding technology is automation. The automatic fiber laser welding robot can be connected with a computer or an on-site controller to realize automatic and semi-automatic control.
Many robotic welding systems are equipped with advanced sensors and monitoring capabilities that allow for data collection during the welding process. This data can be analyzed to identify trends, optimize welding parameters, and improve overall process control.
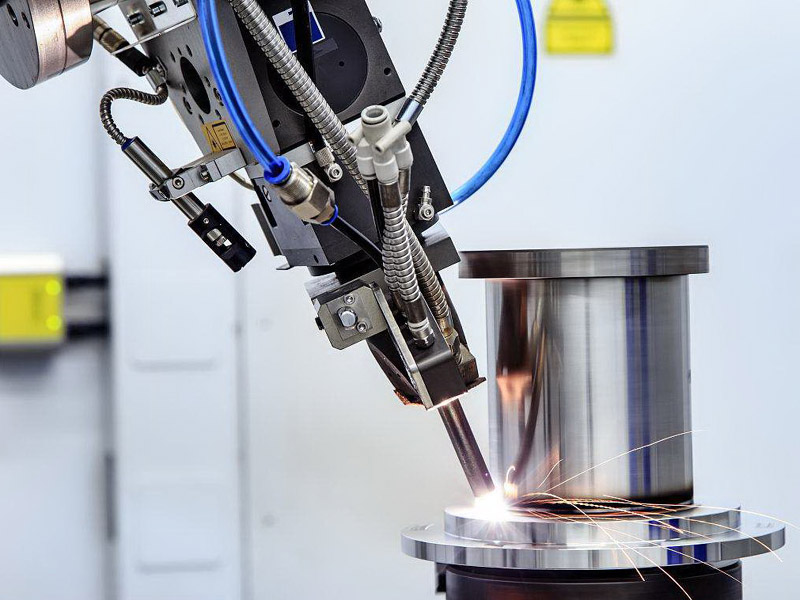
1.2 Disadvantages of Welding Robot
Complicated Setting
Before using the robot welding machine for welding, it is necessary to set and adjust the parameters of the robot welding machine according to the specific welding task, such as welding speed, welding current, welding time, welding distance, etc. If you need robotic welders to perform a variety of different manufacturing tasks, you need to configure specific parameters for each task, which takes some time. Modern robotic welding machines can achieve autonomous control by automatically adjusting welding parameters, but in most cases, manual parameter setting and adjustment are still required to ensure welding quality and efficiency.
Higher Initial Investment
One disadvantage of investing in robotic welding equipment is the high expenditure. Automated welding processes require a higher initial investment compared to manual welding processes. Manual welding may be more cost-effective, but you may still find it more expensive than automatic welding in the long run, and you will face labor costs, maintenance repairs, production waste costs, etc.
Part 2: What are the Components of a Robotic Laser Welding System?
The main components of the robot welding machine include robot system, laser system, welding head, control system and gas protection system, fixtures, etc. These parts cooperate with each other to complete the automatic welding and improve the welding quality and production efficiency. Knowing the main components of the robot welding machine can help you choose a welding machine that is more suitable for your production needs.
Robot System
The robot system is the core part of the robot welding machine. It usually uses a multi-joint robot arm as the basis, which has high speed, high precision and high flexibility. The robot system can be programmed and controlled by a computer or a dedicated controller to realize automated production.
Laser System
The laser system is another important part in the robot welding machine, which is used to provide the laser beam required for welding. The laser system mainly includes laser source, beam transmission system, beam focusing system and cooling system and other components. The quality and stability of the laser system have a very important influence on the welding quality.
Laser Welding Head
The welding head is the final part used by the robot welding machine for welding. It usually uses a hand-held or fixed welding head, which can be replaced according to different welding requirements. The welding head usually includes components such as a beam focuser, a gas shield, and a welding head.
Control System
The control system is an important part of the robot welding machine, which is used to realize the automatic control of the welding machine. The control system is usually composed of computer, PLC, electrical control system, etc., which can realize the monitoring and control of the automatic welding process and ensure the welding quality and production efficiency.
Gas Protection System
The gas protection system is the auxiliary equipment of the robot welding machine, which is used to provide shielding gas, protect the molten pool during welding, and prevent oxidation and pollution. Gas protection systems usually include gas cylinders, pressure reducers, flow meters, gas pipelines and other components.
Fixture and Clamping Equipment
The quality of the jig that holds the parts in place before welding is very important to the quality of the job done. The positioning of the parts needs to be highly repeatable and robust so that no movement occurs during the welding process. Welding robot manufacturers usually supply the bench, but not fixture provided.
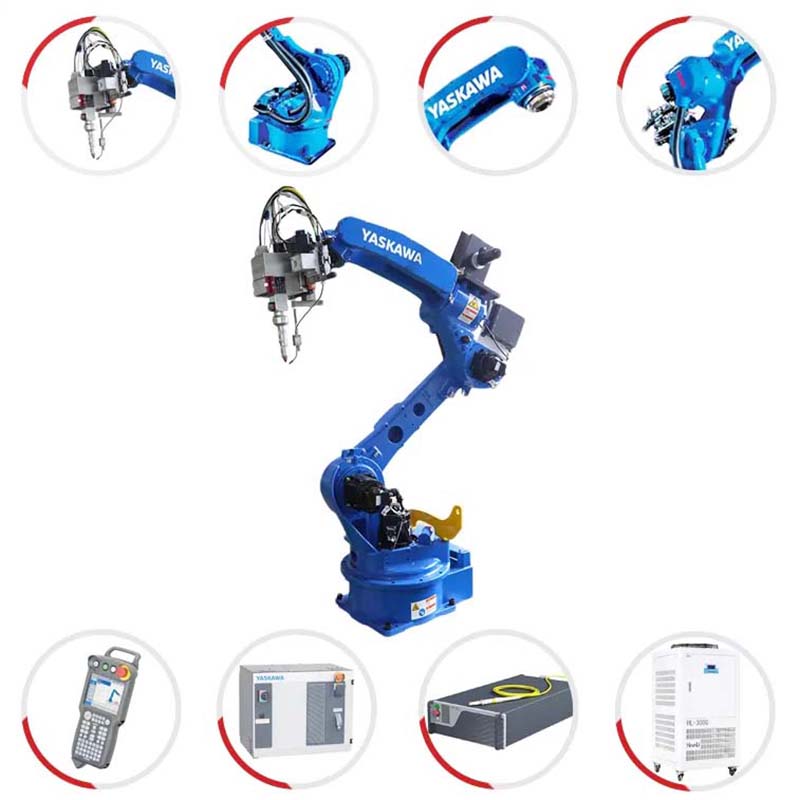
Part 3: How to Choose the Right Robotic Welding System
When choosing a laser robot welding machine, you need to focus on the following factors. These points will ensure that you get a high performance, high efficiency robotic welding system that fits your production business.
Welding Requirements
Consider the type of materials that need to be welded, the thickness of the metal, and the type of weld required (e.g. butt weld, lap weld, or fillet weld). Choose a robot laser welding machine that is appropriate for the specific welding requirements.
Laser Type
The two main types of lasers used in robot laser welding machines are CO2 and fiber. CO2 lasers are better suited to thicker materials, while fiber lasers are better suited to thinner materials and offer greater power efficiency.
Robot Type
Consider the size and reach of the robot arm, as well as the number of axes of movement. This will impact the maximum size of the components that can be welded and the complexity of the welds that can be performed.
Automation Requirements
Consider the level of automation required, including the need for automatic component loading and unloading. It may be necessary to assemble a complete robot welding system with other automation equipment.
Service and Support
Choose a reputable manufacturer that offers adequate customer service and support, including technical assistance, training, and maintenance and repair services.
Budget
Consider the budget available for purchasing and operating the robot laser welding machine, including the costs of maintenance and repair, consumables, and operator training.
By considering these factors, you can select a robot laser welding machine that is best suited for your specific welding needs and budget. Of course, you will not always have a deep understanding of all welding machines. Before purchasing, you can consult professional laser equipment manufacturer DPLASER at any time, and we will wholeheartedly provide you with suitable suggestions.
Part 4: Robotic Welding Applications
Due to its high quality and high productivity, robotic welding has become important in metal and heavy industry, especially in the automotive industry where spot and laser welding are mostly used. Secondly, robot welding technology is also commonly used in precision electronic components, aerospace aircraft parts, circuit board (PCB) welding, mechanical parts manufacturing, and welding of large steel structural parts in the construction industry.
4.1 Robotic Welding in Automotive Industry
Laser welding has become a trend in automotive production. The use of laser welding in automobile production line can not only reduce the weight of the car body, but also improve the quality, safety, efficiency and cost-effectiveness of the auto parts.
Body Welding:
The most common welding in automobile production is body welding, which is a complex welding process that requires high-precision and high-efficiency. The robot welding machine can quickly and accurately complete the body welding task through automatic control, effectively improving production efficiency and welding quality.
Engine Welding:
The auto engine is the core component of the automobile, and its welding quality affects the performance and safety of the automobile. The robot welding machine can achieve precise welding of engine parts through automatic control, improving welding quality and production efficiency.
Exhaust Pipe Welding:
The exhaust pipe is an important part of the rear of the car, which requires special welding techniques that are resistant to high temperatures and corrosion. The automatic robot welding machine can realize the precise welding of each part of the exhaust pipe, so as to ensure the performance and safety of the exhaust pipe.
Automobile Wheel Hub Welding:
Wheel hub is one of the key components of auto operation, and its welding quality is directly related to the driving safety and stability of the automobile. The robot welding machine can achieve high-precision and high-quality welding of the hub through automatic control, improving efficiency and welding quality.
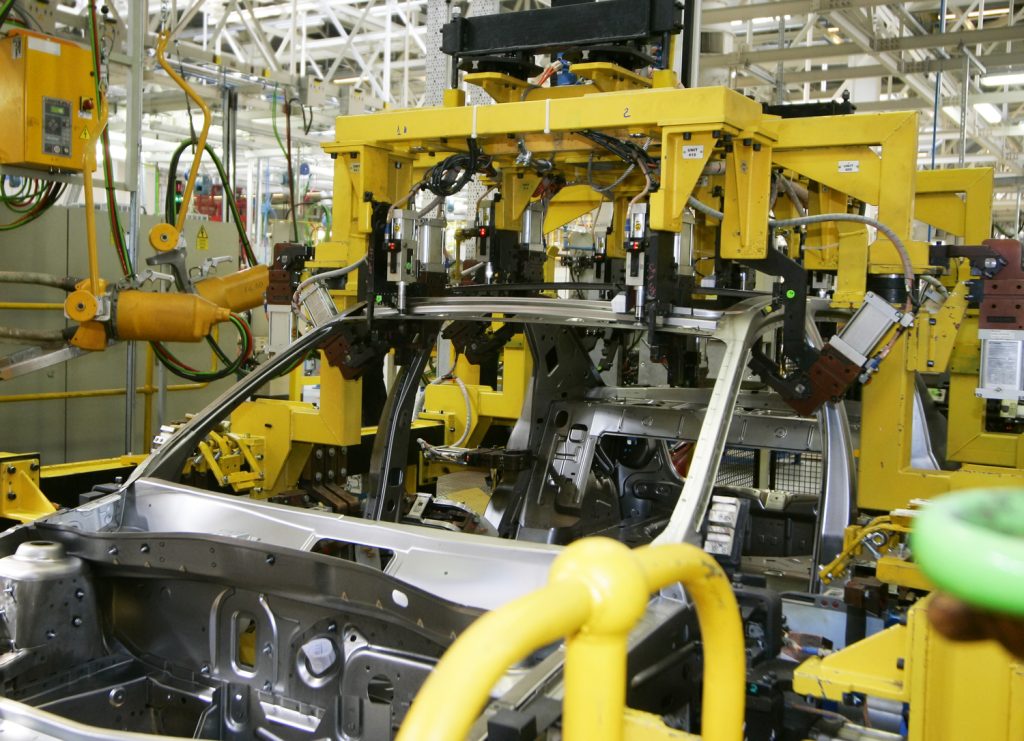
The above is the application of robot laser welding machine system for auto manufacturing. The laser welding machine adopts the intelligent robot. It collimates the parallel light through the collimating mirror and focuses on the work piece to perform welding. It can perform flexible transmission and non-contact welding on the welding precision parts that are difficult to access for large molds.
4.2 Robot Welding Machines for Jewelry Welding & Mark
Welding and soldering
Robot welding machines can be used to weld and solder various parts of a jewelry item, such as clasps, chains, and rings. The precision and accuracy of the robot ensure that the welds are strong and consistent.
Engraving and etching
Robot welding machines can also be used to engrave or etch patterns and designs onto jewelry items. This can be done with a laser or other cutting tool attached to the robot arm.
Overall, the use of robot welding machine in the jewelry industry can improve precision, quality, and efficiency.
The Bottom Line:
One of the most important advances in welding technology is robotic or automated welding. This article describes advantages of robotic vs. human welding in many application areas. With the continuous development of technology and the continuous expansion of application scenarios, robotic laser welding machines will be full of unlimited development space.