Choosing the right laser welding system is crucial for enhancing production efficiency. This guide compares automatic platform laser welding machines with robotic laser welding systems, highlighting the advantages of robotic laser welding and how they provide fully automated solutions for complex welding tasks.
As manufacturing demands flexibility and efficiency, automated welding technology is becoming more prevalent. Especially for small-batch, diverse production tasks, the variety of product specifications complicates standardized production. Companies often face challenges such as high initial investment and delayed returns during the automation upgrade process.
Laser welding robots are a crucial part of automation solutions, enhancing production line efficiency and weld quality with their high-speed operation, precise weld positioning, and stable performance. By adopting laser welding robots, manufacturers can effectively tackle challenges, ensure consistent weld quality, and lay a foundation for business development.
Robot welding system refers to using programmable mechanical tools (welding robots) to automatically complete welding tasks. These robots execute welding operations based on pre-programmed positions, orientations, and parameters. They are used for precision welding of sheet metal, hardware, and metal alloys, and are applied in industries such as automotive, aerospace, shipbuilding, power batteries, kitchenware, machinery manufacturing, and mechanical parts.

The Difference between Laser Welding vs Robotic Laser Welding
The difference between robotic welding and automatic welding is the degree of automation and flexibility.
Auto platform laser welding machines are designed for specific welding tasks with fixed mechanical structures and welding paths, making them suitable for high-volume production of identical or similar parts. These machines often require external human or robotic assistance for loading and unloading workpieces, which need to be secured and positioned using welding fixtures. Three- Axis desktop automatic laser welder is ideal for environments with stable and repetitive welding specifications.
In contrast, laser welding robotics offer high flexibility, adjusting their movements and welding parameters for various tasks. Comprising a robotic arm and a laser control system, they perform multi-angle and multi-directional welding operations. These best robotic welding systems can also be equipped with various accessories, such as vision systems, ground tracks, positioners, 3D workbenches, and wire feeders, to meet diverse welding needs. Their flexibility allows them to be used across different production lines, handling various shapes and sizes of workpieces, thus enhancing production line versatility.
1. Different Welding Methods
Platform automatic laser welding is fully autonomous, with the machine completing the welding process based on preset parameters. In contrast, robotic laser welding involves the use of a robotic arm to assist in welding the workpieces.
2. Different Application
Automated laser welding is suitable for large-scale, repetitive welding tasks, automating high-volume welding processes. Robotic laser welding is more flexible, ideal for smaller production runs, irregularly shaped parts, or products requiring frequent changes.
3. Different Welding Precision
Automated laser welding system achieves high precision due to its operation based on preset parameters on a workbench. Robotic laser welding is usually slightly less accurate due to the greater influence of the parameters of the robot arm and the environment.
Automated Laser Welding Machine
All welding parameters are controlled by the machine. Specific parameters can be adjusted when changing welding components.
Advantages: High production efficiency, stable welding quality, suitable for large-scale production, and cost-effective in terms of labor.
Disadvantages: High equipment and technology requirements, leading to high initial investment.
Application: Ideal for high-repeatability welding and large-scale production scenarios.
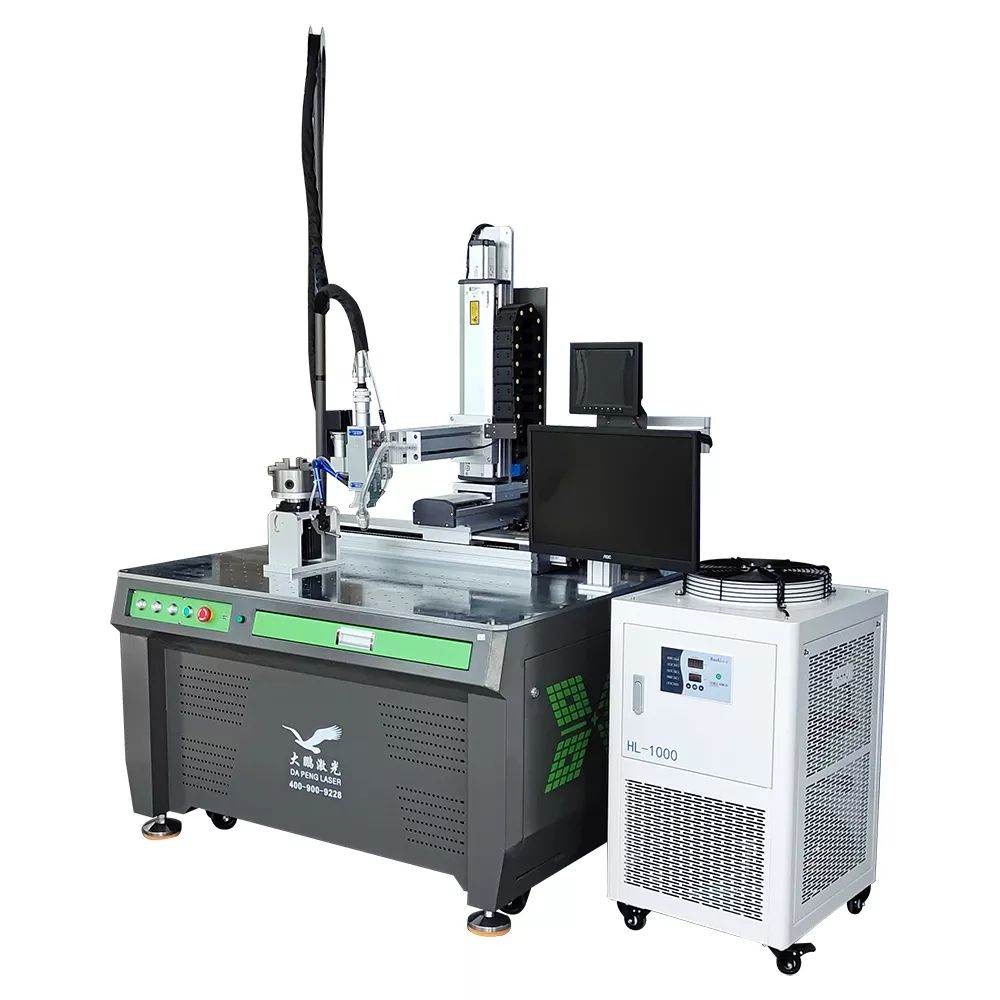
Robotic Laser Welding System
Automated welding is achieved through pre-programming in the robotic control system, supporting various welding paths and geometries.
Advantages: High flexibility, suitable for small-volume production, irregular shapes, or frequent changes, with relatively lower costs.
Disadvantages: Slightly lower welding precision and requires manual assistance.
Application: Best for diverse, small-scale welding tasks.
Items | Automatic platform Fiber laser welder | Robotic Arm Laser welding machine |
Axis | Standard 3-axis, 4-axis, 5-axis | Standard 6 axis + 3 axis (extended) |
Flexibility | Linkage cost is high and not flexible enough | Can realize more angle welding, wider application. |
Large workpiece | Gantry structure, suitable for high volume products with high consistency | Higher efficiency, the same table can weld multiple products allows for small batches with variable welding requirements |
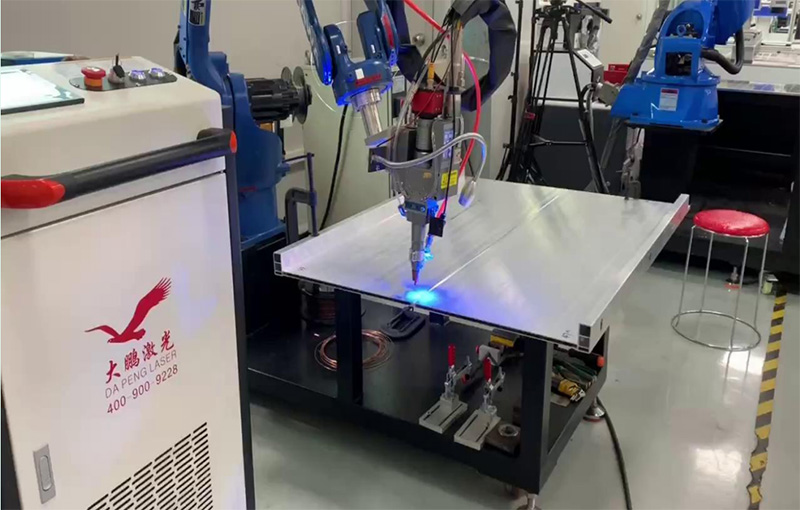
Advantages of Robotic Laser Welding
Suitable for Large Workspaces: Robotic intelligent operation offers flexibility and reliability, with six-axis movement enabling welding in any spatial orientation, not limited to flat surfaces.
Enhanced Weld Quality: Laser welding robots produce highly uniform and high-quality welds, thanks to precise path control and programmable welding modes, ensuring each weld meets optimal standards.
Increased Safety: Welding involves high temperatures and harmful radiation, posing safety risks to operators. Using welding robots removes workers from these hazardous environments, reducing the likelihood of workplace injuries.
High Flexibility: With user-friendly programming interfaces, laser welding robots are easy to adjust and reprogram, quickly adapting to new production tasks or design changes to meet diverse production needs.
Multi-Station Welding: Capable of dual or multi-station welding operations, saving fixture setup time and significantly boosting production efficiency.
Consistency: Robots provide excellent repeatability, ensuring consistent welding processes crucial for maintaining product quality.
Optimized Labor Resources: Introducing laser welding robots allows businesses to allocate skilled welders to more complex tasks while training non-specialists to operate robots, expanding welding production capacity.
Data Management and Analysis: Intelligent welding enables monitoring and recording of the welding process through data analysis, identifying issues and making adjustments to enhance efficiency and quality.
High Customization: Fixtures can be customized according to production needs.
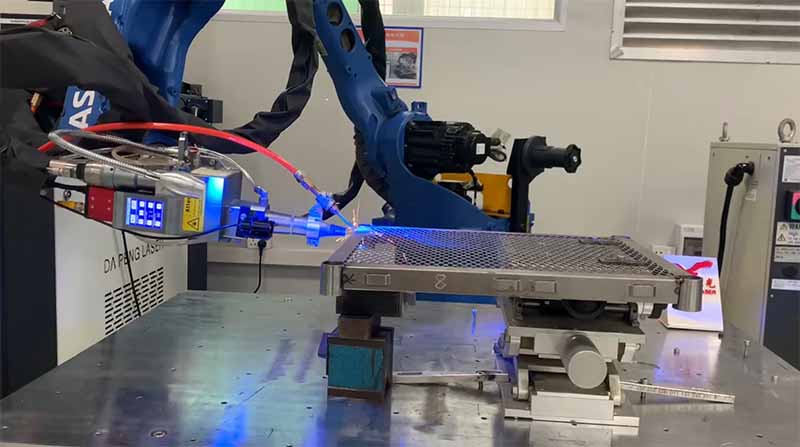
How Robot Laser Welding Improves Your Manufacturing?
1. Preparation
Select Equipment and Materials: Choose appropriate laser welding equipment, materials, and processes based on the characteristics of the parts to be welded.
Maintenance and Care: Perform regular maintenance on the robotic arm and laser welding system to ensure proper operation of both mechanical and electrical systems.
Comprehensive Check: Inspect the all component for any looseness, damage, or other abnormalities.
2. Programming Control
Offline Programming: Use specialized software to preset welding paths, speeds, and parameters, then upload them to the robot control system.
Online Programming: Program and adjust the robot directly through the control system.
Considerations: Ensure welding paths are continuous, control current and voltage appropriately, and meet welding quality standards.
3. Sensor Application
Real-Time Sensing: Collect welding environment data, such as weld seam position and shape, using sensors.
Dynamic Adjustment: Adjust the robot’s position and welding parameters based on sensor feedback to ensure weld seam accuracy.
4. Control System
Control Center: The control system manages the robot’s movements, welding parameters, and sensor data processing through programming instructions.
Advanced Algorithms: Employ advanced control algorithms and real-time operating systems for precise welding process control.
5. Quality Monitoring
Real-Time Monitoring: Continuously monitor weld seam dimensions, shape, and quality.
Fault Handling: If quality issues are detected, the robot can automatically stop welding and alert to prevent the production of defective products.

Laser Welding Robot Arm Parameters
1. Degrees of Freedom: Degrees of freedom refer to the number of independent movements a robotic arm can make in space. The more degrees of freedom, the greater the arm’s flexibility. For example, a six-axis laser welding robot has 6 degrees of freedom.
2. Maximum Reach: Maximum reach is the distance between the end-effector and the base when the robotic arm is fully extended. A larger maximum reach allows for a greater working range of the arm.
3. Work Space: The work envelope is the set of all points that the end-effector can reach while performing tasks. The size and shape of the work envelope directly impact the arm’s applicability.
4. Load-to-Weight Ratio: The load-to-weight ratio is the ratio of the maximum load the robotic arm can handle to its own weight. A higher ratio indicates stronger load-bearing capability.
5. Speed and Acceleration: Speed and acceleration are key indicators of the robotic arm’s movement characteristics. Acceleration affects the smoothness of movement and positioning accuracy.
6. Precision: Precision refers to the error between the target position and the actual position of the end-effector when performing tasks. Higher precision leads to better welding effect.
7. Repeatability: Repeatability is the consistency of the error in the end-effector’s position during multiple executions of the same task. Higher repeatability indicates better welding stability of the robotic arm.
8. Rigidity and Flexibility: Rigidity and flexibility refer to the arm’s deformation characteristics under external forces. A rigid arm maintains shape and position better, while a flexible arm adapts more effectively to irregular work environments.
Summarize
Automated platform laser welding system is a cost-effective solution for those on a low budget, offering the benefits of welding automation at a lower cost. With fewer integration requirements, the setup is quicker, allowing users to rapidly deploy the 3/4/5 axis automatic laser welding machine. Compared to manual welding, automated platform laser welding enhances production efficiency.
Fiber laser welding robots offer high automation levels and are suitable for complex and variable welding paths, commonly used in precision industries like automotive and aerospace. Although they involve higher equipment costs and require more investment, these systems provide faster returns by significantly shortening production cycles, increasing productivity, and reducing long-term operational costs.
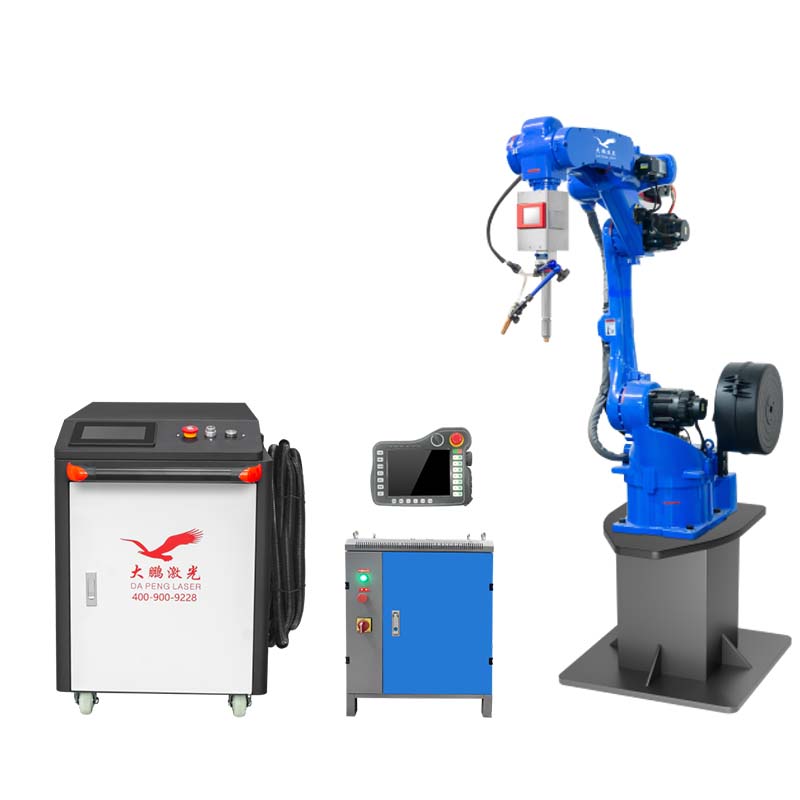
Understanding the difference between robotic welding and automatic welding can help you select the most effective solution for your production needs. Robotic laser welding systems use CNC technology to offer enhanced automation and flexibility, making them ideal for complex and varied tasks. By choosing the right system, you can achieve greater efficiency, precision, and productivity in your welding operations. Interested in learning more about robotic welding options? Let us know—we’re here to help you find the right laser welding robot solution for your business.