What is a femtosecond laser cutting machine? In traditional applications where long-pulse lasers (microsecond, nanosecond, etc.) are used for material cutting or engraving, the primary interaction between the laser and the material is the conversion of laser energy into thermal effects. This process causes material melting and vaporization, enabling material removal. However, due to heat accumulation in this process, a large and intense heat-affected zone (HAZ) is formed. This heat-affected zone can lead to overheating deformation, melted edges, oxidation blackening, residue, and burrs in the processed material.
With the continuous development of laser technology and the increasing demand for higher processing quality, ultrafast laser processing technology is increasingly used in precision micromachining. Typically, ultrafast lasers refer to lasers with a pulse width of less than 10 picoseconds (ps). Among them, femtosecond lasers, which have even shorter pulse widths, are gradually being applied in laser processing.
A femtosecond laser is a laser technology that generates extremely short pulses, where “femtosecond” (femtosecond: 10⁻¹⁵ seconds) is a unit of time measurement. Femtosecond lasers are the shortest laser pulses that can be stably obtained and used in industrial applications.
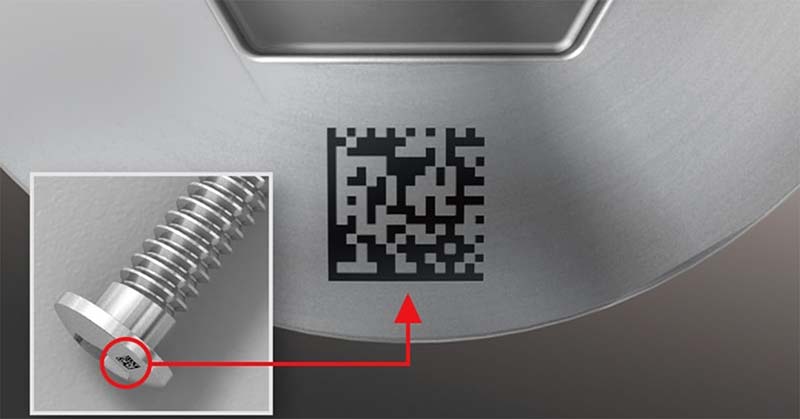
Why Use Femtosecond Laser Micromachining?
Femtosecond laser micromachining is highly favored for its exceptional precision and outstanding processing quality. Its ultrafast pulses and extremely small laser spot enable ultra-fine and highly intricate cutting, almost directly vaporizing the material without exerting any mechanical stress on the workpiece. Additionally, due to its extremely short pulse duration, the heat-affected zone (HAZ) is minimal, effectively preventing burr formation. This makes femtosecond laser micromachining an ideal choice for high-precision material processing, especially for applications requiring high-quality edges and intricate features.
Thermal Effects in Femtosecond Laser Material Processing
Femtosecond laser micromachining enables the finest and most intricate cutting. Due to its extremely short pulse duration, femtosecond lasers effectively suppress the formation of a heat-affected zone (HAZ) around the laser-affected area, ensuring high-quality material processing. This is because the pulse width of a femtosecond laser is shorter than the electron-phonon coupling time (1–100 ps) in the interaction between light and matter. As a result, most of the laser energy is absorbed by electrons and rapidly transferred to the lattice without significant heat diffusion losses. Consequently, heat diffusion around the femtosecond laser irradiation zone is minimal to the point of being negligible.
Additionally, femtosecond lasers possess ultra-high instantaneous pulse energy and high photon density, enabling nonlinear multiphoton absorption in materials.
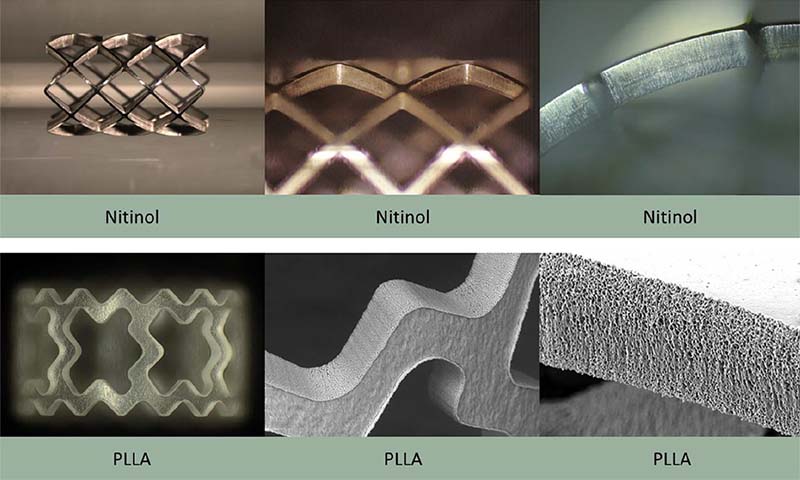
What is Femtosecond Laser Used for?
The ultrashort pulse width and extremely high peak power of femtosecond lasers can induce nonlinear absorption effects in materials, achieving a focal spot size much smaller than the diffraction limit, thus significantly enhancing the spatial resolution of machining. Additionally, because the pulse duration of femtosecond lasers is much shorter than the thermal relaxation time, no heat is generated during the processing—commonly referred to as “cold” processing. This allows femtosecond lasers to perform ultra-fine cutting, drilling, etching, and other operations on any material, directly avoiding issues such as overheating, cracking, oxidation, and melting caused by heat accumulation in long-pulse laser processing. This means that in femtosecond laser processing, there is almost no carbonization, slag, or residue.
- Surface micro-structuring:
Femtosecond lasers can precisely engrave micro- and nanoscale structures on the surface of materials, enabling superhydrophobic properties, optical control, and functional surface modification.
- Micronanodrilling:
Femtosecond lasers, with their ultrashort pulses and extremely high peak power, can achieve high-precision, small-aperture, and heat-affected-zone-free micro-and nano-drilling on materials such as metals, ceramics, and polymers.
- Brittle Material Processing:
Femtosecond laser cutting is used for materials like quartz glass, sapphire, ceramics, plastics, and thin films, allowing high-precision processing with ultrashort pulse lasers. Due to the ultrafast time scale of femtosecond lasers, the energy interaction time is extremely short, effectively reducing the heat-affected zone, and preventing material melting, thermal damage, and micro-crack formation, thereby significantly improving the processing quality.
- Biomaterials:
During femtosecond laser processing, an extremely minimal heat-affected zone (HAZ) is achieved, allowing high-precision processing without damaging surrounding materials. This is particularly suitable for processing heat-sensitive materials, such as polymers, glass, and biomaterials.
- Microelectronics:
In the fields of microelectronics and semiconductors, femtosecond lasers can precisely cut and drill holes, processing micro-holes with diameters smaller than 10 microns and achieving smooth, burr-free edges. This makes femtosecond lasers particularly suitable for manufacturing complex microstructures and nanostructures, enabling precise processing of small mechanical and electronic components like integrated circuits and micro-electromechanical systems (MEMS).
- Medical Materials:
Femtosecond laser processing allows for precise modification of medical materials with minimal heat damage. This technique is ideal for creating microstructures on implants, surgical tools, and medical equipment, ensuring high performance and biocompatibility.
- Optoelectronic Device Manufacturing:
In the manufacturing process of optoelectronic devices, precise processing of various small optical components is required. Femtosecond laser cutting machines are used to manufacture a variety of optoelectronic devices, such as lasers and LED lights. These devices require high-precision cutting and welding, and femtosecond laser cutting technology can meet these demands, improving production efficiency and product quality.
- Nanotechnology Applications:
Femtosecond laser cutting machines can be used to fabricate materials and devices at the nanoscale, such as nanowires and nanoparticles. These materials and devices possess unique physical and chemical properties and are widely used in fields such as energy, healthcare, and electronics.
Femtosecond laser processing offers high flexibility, enabling the creation of arbitrary three-dimensional structures both within and on the surface of materials. By utilizing femtosecond lasers to induce controlled phase transitions, directional etching of materials can be achieved.
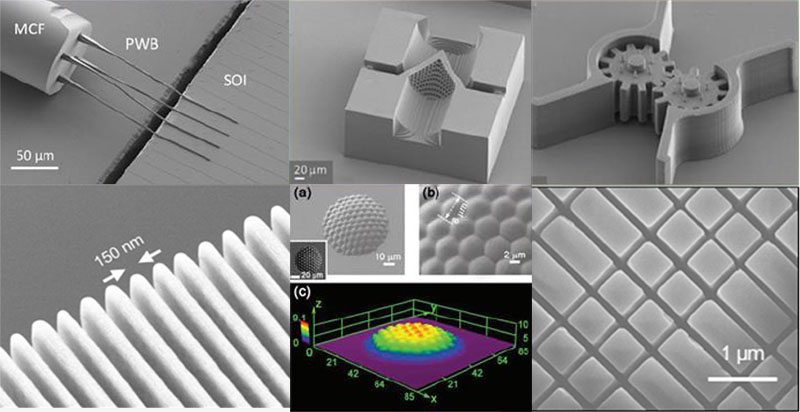
Femtosecond Laser Marker in Medical Device Manufacturing
Femtosecond laser marking and cutting machine demonstrate exceptional precision and stability in medical device manufacturing, especially for devices with high-precision requirements. For example, in the production of medical instruments such as endoscopes and microscopes, femtosecond laser technology can precisely cut optical components, ensuring that their quality and performance are optimized.
Moreover, this technology is widely used in the manufacturing of implants like artificial joints and coronary stents. These implants demand extremely high precision and stability, and femtosecond laser technology, with its ultrashort pulses and high energy density, can achieve micron-level and even nanometer-level processing accuracy. This makes it ideal for meeting the high precision and high contrast demands in medical device manufacturing.
Advantages of Femtosecond Laser Cutting Machines
- Ultra-High Precision:
Femtosecond lasers have extremely short pulse durations (femtosecond scale, i.e., 10^-15 seconds), allowing energy to be concentrated in a very small area to achieve micron and nanometer-level structures and patterns. By adjusting laser and processing parameters, various shapes and sizes of microstructures can be fabricated, such as gratings, micro-lens arrays, and micro-channels.
- Minimal Heat-Affected Zone:
Unlike traditional laser cutting, which can cause heat damage to the surrounding material due to thermal conduction, femtosecond lasers generate almost no heat impact due to their ultrashort pulse characteristics. This prevents material deformation, melting, or ablation, making it particularly suitable for processing heat-sensitive materials.
- Wide Material Compatibility:
Femtosecond lasers can process a variety of materials, including metals, ceramics, polymers, and biomaterials, with consistent cutting results across different materials. This is especially important in medical device manufacturing.
- High Surface Quality:
The surfaces after femtosecond laser cutting are extremely smooth, often requiring little to no subsequent polishing or treatment. This reduces processing steps and increases production efficiency.
- Complex Structure Processing Capability:
Femtosecond lasers can precisely process complex structures, such as curved surfaces, micro-holes, and micro-channels. This is crucial for manufacturing intricate implants like artificial joints and coronary stents.
- Environmentally Friendly and Safe:
Femtosecond laser cutting does not require the use of chemicals, nor does it produce harmful substances, effectively reducing environmental pollution. Additionally, its low energy consumption helps reduce production costs and enhances the company’s environmental image and sustainability.
- High Automation:
Femtosecond laser cutting machines can be automated and integrated with computer control systems, enabling efficient batch production and customized solutions, which flexibly meet the diverse needs of customers.
How much does a Femtosecond Laser Cutting Machine Cost?
The maintenance cost of a femtosecond laser cutting machine is higher than that of traditional laser cutters, but this is closely related to its high precision and advanced technology. Its core components, such as the laser and cutting head, require regular maintenance and calibration to ensure the machine remains in optimal working condition. Additionally, some consumables, like the laser module and optical components, need periodic replacement, which contributes to the higher maintenance costs.
However, the high maintenance cost of femtosecond laser cutting machines also brings significant returns. Its ultra-high cutting precision and efficiency greatly reduce material waste, enhance production efficiency, and lower the manufacturing cost of each unit. In the long term, this helps reduce overall operational costs.
To help users better manage maintenance costs, professional femtosecond laser cutting machine manufacturers (such as Dapeng Laser) typically offer comprehensive support, including detailed maintenance manuals, operator training, and 24/7 online after-sales service. These services not only assist users in correctly operating and maintaining the equipment but also maximize its lifespan, ensuring it remains in efficient and stable operation. Therefore, despite the higher maintenance cost, the production benefits and long-term economic advantages make femtosecond laser cutting machines an ideal choice for high-precision applications such as medical device and electronics manufacturing.
DPLaser Femtosecond Laser Solutions
Dapeng Laser’s femtosecond laser micro-cutting and marking system is the ideal choice for industrial-grade, high-precision material processing. Our experienced engineering team works closely with major research institutes across the country, sharing technical expertise to provide high-quality, customized solutions and products.
Femtosecond Laser Microprocessing System Customization Services:
- Offering high-precision, customized target positioning systems, complemented by specialized software.
- Integrating and synchronizing the femtosecond laser with the positioning system for efficient coordination.
- Providing user-friendly software interfaces that support various laser scanning and positioning systems.
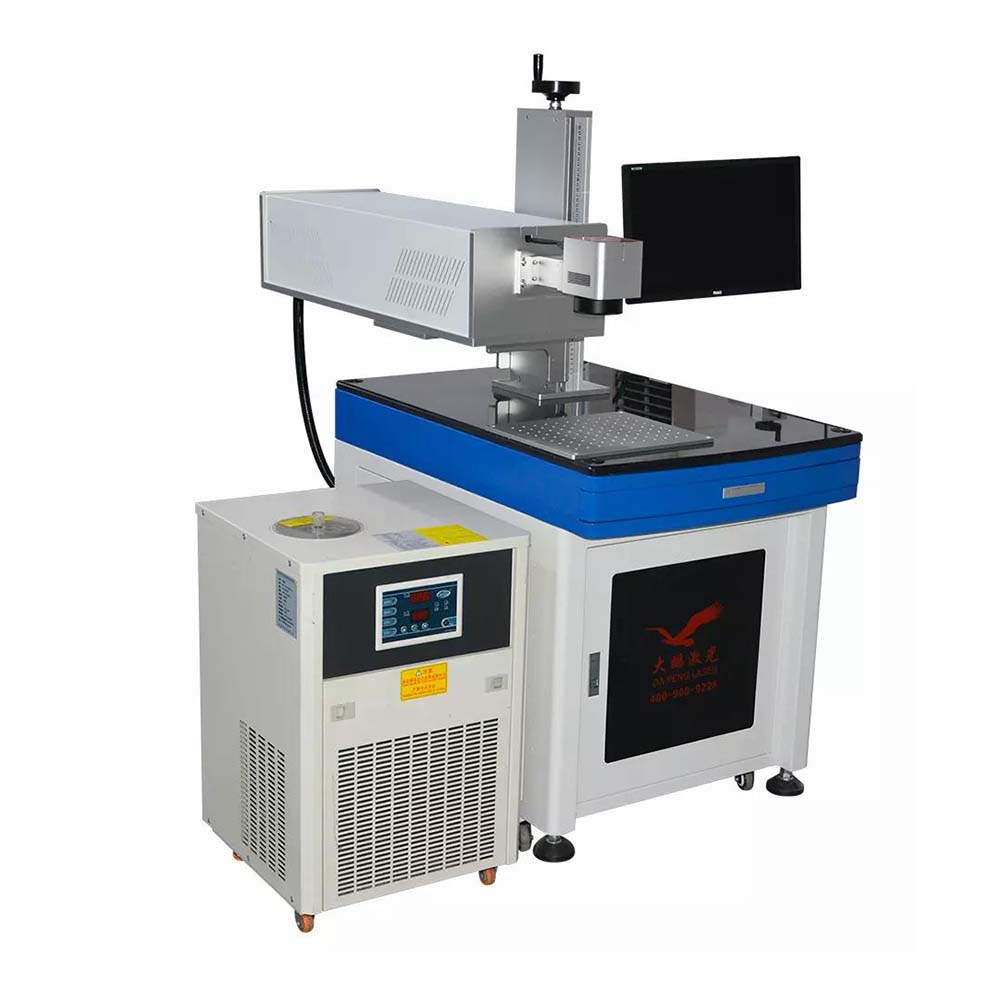
01 Precision Micro-Hole Forming Solutions
For ultra-fine manufacturing requirements of critical components in different fields, we provide efficient, precision hole-forming equipment capable of processing through holes, blind holes, special-shaped holes, micro-cavities, and cavities with high aspect ratios (>10:1), high circularity (>95%), and high accuracy (±3μm).
- Products are free of deformation, micro-cracks, and edge chipping. The surfaces and inner walls are neat, burr-free, and without carbonization.
- Controlled taper designs (inverted cone, no taper, and positive taper) to meet various application needs.
02 Carbonization-Free Cutting Solutions
Ideal for micro-engraving, marking, and cutting of flat, curved, and complex-shaped key components at the micron level.
- Achieve high-precision, high-efficiency, and high aspect-ratio (>100:1) cutting, scribing, and hole-making of materials like molten glass, wafers, PI films, etc.
- Features an extremely small heat-affected zone, with smooth, non-tapered, carbonization-free, and crack-free cutting profiles.
- Cut surfaces are smooth, burr-free, and edge-chipping-free, ensuring high-quality processing results.
Please provide details of the materials you need to process and your specific requirements. Based on this information, we will tailor a customized ultrafast laser micro processing solution that best suits your needs. Additionally, we will provide you with a competitive and affordable quote, ensuring both high performance and cost efficiency for your project. Last but not least, we have extensive experience in the design and manufacturing of ultrafast laser equipment for femtosecond laser glass cutting. In the field of femtosecond laser cutting, the most commonly processed materials include glass, quartz glass, Sapphire wafer, plastics, and thin films.