In the world of modern manufacturing and maintenance, laser cleaning of metal surfaces has emerged as a game-changing solution for precise, efficient, and eco-friendly surface cleaning. Laser cleaning machines can remove rust, paint, oxides, and other contaminants from metal surfaces without causing damage to the base material. Whether you’re looking to prepare a metal surface for welding, restore aged equipment, or maintain industrial components, laser metal cleaning offers unparalleled advantages over traditional cleaning methods.
The surfaces of metals are often subjected to corrosion from substances such as rust, dirt, and grease, which can severely impact the performance of components. Traditional rust removal methods generally fall into two categories: mechanical and chemical. Mechanical cleaning is straightforward but time-consuming and labor-intensive, often causing wear to the substrate. Chemical cleaning, while relatively simple to perform, generates waste liquids that can lead to environmental pollution. Both methods share common drawbacks, including complex operations, lengthy processing times, and the potential for secondary contamination.
To address these issues, laser cleaning technology has emerged and rapidly advanced. A laser cleaning machine for metal utilizes laser energy to cause the loose contamination layer on the metal surface to absorb energy, forming plasma and generating shock waves that break apart and detach rust and other pollutants. By precisely adjusting laser power, this method leverages the compositional differences between contaminants and the metal substrate, enabling efficient removal of rust, oxide layers, coatings, paint, and oil without damaging the substrate.
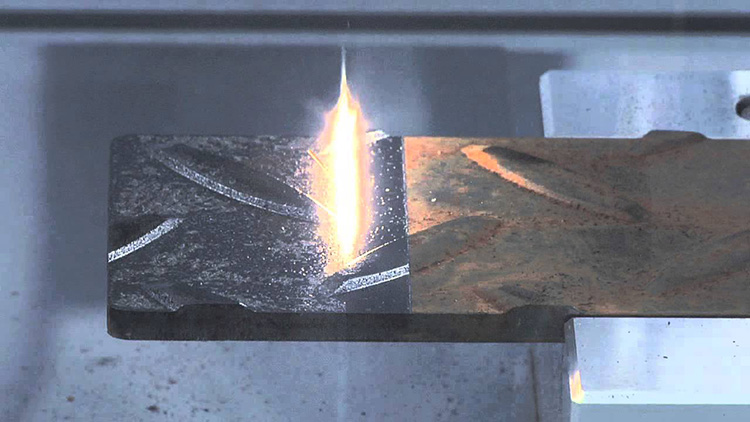
How Does Laser Cleaning Metal Work?
A laser metal cleaning machine primarily uses a high-energy laser beam to irradiate the surface of a metal, causing contaminants like dirt, rust, and oxides to instantly evaporate or decompose, thereby achieving effective cleaning. With its extremely high energy density and brief exposure time, the laser can remove unwanted substances in a fraction of a second without causing noticeable damage to the metal surface.
Every material has unique properties, including different molecular bonds and specific ablation thresholds. When removing unwanted layers from a surface, the energy delivered by the laser must exceed the ablation threshold of the target material. If there is a significant difference in ablation thresholds between materials, laser parameters can be adjusted to selectively remove the material with the lower ablation threshold while leaving other materials unaffected.
This non-contact cleaning method is highly efficient and precise, ensuring the integrity and quality of the metal substrate. It delivers excellent results for both large metal objects and intricate metal components, making it ideal for a wide range of industrial applications.
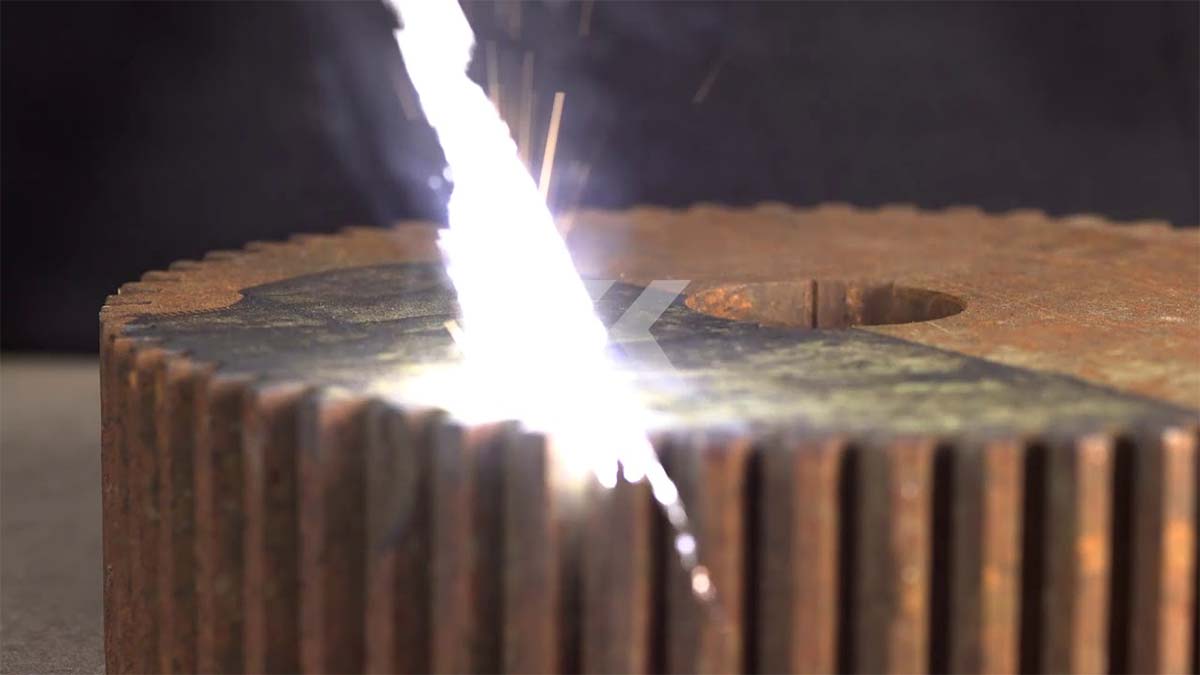
Does Laser Cleaning Damage Metal?
Laser cleaning is a non-contact cleaning method specifically designed to remove surface contaminants such as dirt, rust, and coatings from metals without damaging the underlying material. This is achieved by precisely controlling the laser’s energy output, targeting only surface impurities. Metals, with their excellent light-reflective properties, reflect most of the laser energy, minimizing the risk of thermal damage to the substrate.
Laser cleaning is versatile, effective on both large metal structures and delicate components. For instance, in microelectronics, laser cleaning is the only method capable of removing micron- or submicron-sized particles without damaging intricate structures, ensuring the performance and reliability of electronic components. Likewise, when applied to large metal objects, laser cleaning efficiently removes rust, paint, and grease while preserving the integrity of the metal.
This unique combination of precision and safety makes laser cleaning an ideal choice for a wide range of applications.
Advantages of Metal Laser Cleaning
High Efficiency
Laser cleaning removes dirt, rust, and oxides from metal surfaces quickly, significantly boosting productivity.
High Precision
The high energy density of the laser beam enables precise control of the cleaning area, making it ideal for treating intricate or complex surfaces.
Accurate Control
Laser technology allows precise targeting of specific areas or full cleaning of metal surfaces, such as rust removal from aluminum castings, making it especially useful for partial or intricate treatments.
Non-Contact Cleaning
As a non-contact method, laser cleaning avoids physical damage to the metal surface, preserving the integrity and quality of the substrate.
Environmentally Friendly
Laser cleaning produces no harmful waste, such as exhaust gases or wastewater, making it an eco-friendly cleaning solution.
Wide Application
Suitable for various metals, including steel, aluminum, and copper, as well as objects of different shapes and sizes.
Automation Compatibility
Laser cleaning system can be easily integrated into automated production lines for large-scale, efficient operations, enhancing overall productivity.

What Metals Can Be Laser Cleaned?
Steel and Stainless Steel
Laser cleaning is highly effective for removing rust, oxide layers, grease, and coatings from steel and stainless steel. It rapidly restores the original surface appearance without damaging the material.
Aluminum Alloys
Laser cleaning can remove oxides, paint, and coatings from aluminum, particularly in industries like aerospace and automotive. It efficiently cleans the surface without harming the substrate.
Carbon Steel
Laser cleaning is effective for removing rust and coatings from carbon steel surfaces, making it a popular choice for industrial equipment maintenance and cleaning.
Copper and Brass
Laser cleaning works well for removing light oxide layers and surface stains from copper and brass. This method is commonly used for cleaning electrical equipment and precision components.
Laser cleaning is especially effective on these metals because they have a high absorption rate for laser energy, allowing for efficient removal of surface contaminants without affecting the material’s integrity. Non-metal materials such as stone, ceramics, and certain plastics can also be cleaned with lasers, but the results may not be as efficient or effective as with metals.

Laser Cleaning of Metal Surfaces in Industry
1. Post-Welding Treatment
During welding, high temperatures can lead to the formation of oxide layers at the weld joints, which not only affect the quality of the weld but can also hide potential defects. Laser cleaning technology is highly effective in removing post-weld oxide scales, slag, and spatter. This process offers several benefits:
Improved Weld Defect Detection: Clean surfaces make it easier to detect welding defects, allowing for timely repairs.
Ensured Product Quality: Removal of residual welding debris ensures a smooth, clean surface, enhancing the aesthetic quality and overall finish of the product.
2. Pre-Welding Surface Preparation
Prior to welding, metal surfaces may be contaminated with oils, lubricants, black marks, or non-ferrous metal impurities. These contaminants can negatively affect the welding process, leading to issues like porosity or cracking in the weld. Laser cleaning effectively removes these impurities, ensuring:
High-Quality Welding: A clean surface helps form stable, smooth, and porosity-free welds, improving both the quality and durability of the welds.
Versatility for Different Materials: Whether working with steel or aluminum, laser cleaning provides consistent results, making it suitable for pre-welding preparation on various materials.
Laser cleaning in welding applications not only improves the efficiency of the process but also enhances the final product’s integrity and appearance, making it an essential tool in modern metalworking and fabrication.
3. Laser Cleaning of Rust On Metals
Laser cleaning is highly effective on various metals, including steel, stainless steel, aluminum, and copper, and can be applied to both large industrial components and smaller, intricate parts. With its ability to selectively target rust and oxides while leaving the metal surface intact, laser cleaning ensures a clean, smooth finish, improves corrosion resistance, and extends the lifespan of metal structures.
4. Automation in Production Lines
Laser cleaning technology is not only effective for small-area cleaning of individual parts but can also be integrated into automated production lines for large-scale, efficient cleaning operations. This capability is particularly beneficial in several industries:
Machinery Manufacturing: Laser cleaning is used to remove oil, carbon buildup, or old coatings from mechanical parts, ensuring smooth operation and enhancing product quality.
Automotive Industry: In automotive manufacturing, laser cleaning is applied before and after body welding to ensure high welding quality.
Precision Machinery Manufacturing: For tools and components that require high precision, laser cleaning effectively removes micro-level contaminants, ensuring the performance of the components.
Shipbuilding: Laser cleaning efficiently removes rust, oil, and other residues from ship hulls without damaging the material, ensuring the quality and durability of the vessel.
Integrating laser cleaning into automated production lines allows for high-volume, consistent, and efficient cleaning, making it a key technology in modern industrial processes.
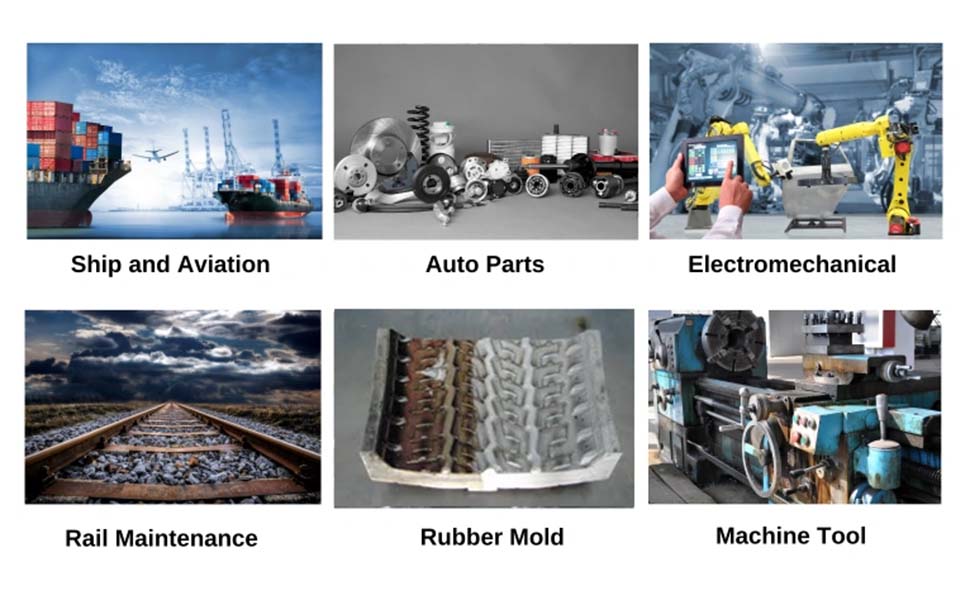
Pulse Laser Cleaning Machine for Metal
The pulse fiber laser cleaning machine is specifically designed for metal cleaning tasks such as rust removal, paint stripping, and oil stain elimination. It effectively handles challenges like metal corrosion, dust, and stubborn contaminants, making it ideal for applications in rust removal, paint and coating stripping, oil cleaning, adhesive removal, plating removal, surface roughening, and weld seam cleaning. Whether dealing with heavy rust layers, persistent grease, or intricate surface textures, this machine delivers exceptional results.
Equipped with advanced MOPA (Master Oscillator Power Amplifier) pulse fiber laser technology, it offers precise heat control, ensuring efficient and effective cleaning while maintaining the integrity of the metal surface. This innovation significantly enhances both cleaning accuracy and operational efficiency, achieving superior cleanliness and productivity.
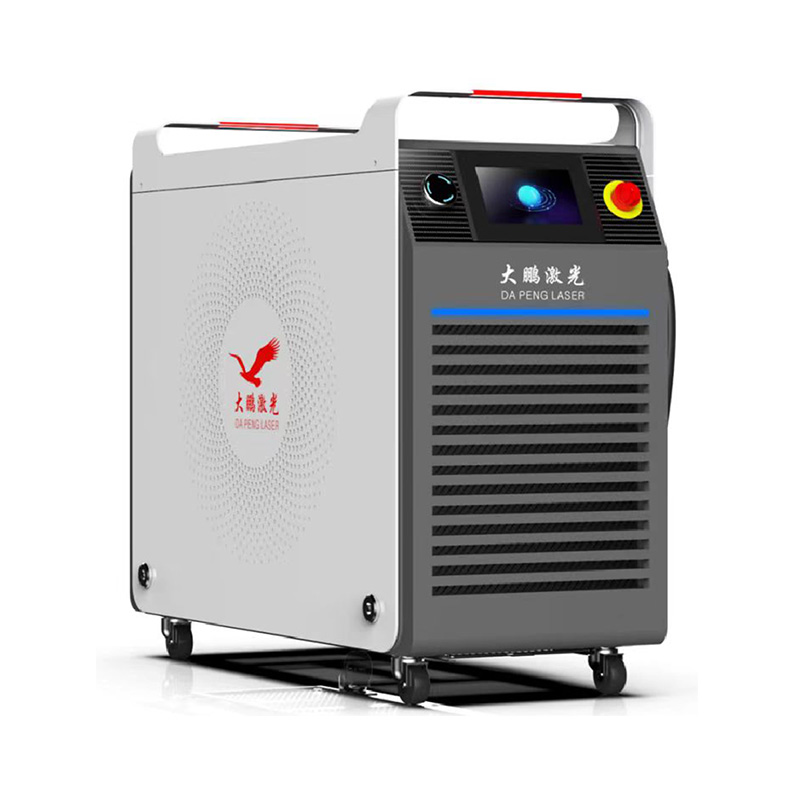
Key Features:
- Non-Contact Cleaning: Uses a laser beam to clean surfaces without damaging the substrate.
- Precision Cleaning: Enables selective cleaning of specific areas with exact dimensions and locations.
- Eco-Friendly: Requires no chemical solutions or consumables, ensuring a safe and environmentally friendly operation.
- User-Friendly Interface: Features a visual control system and simple operation; works seamlessly with a handheld cleaning gun.
- High Efficiency: Outperforms traditional methods in speed and cost-effectiveness, reducing time and labor requirements.
Metal Laser Cleaning Machine Price
As laser cleaner advances and becomes more widespread, the cost of metal laser cleaning machine is gradually decreasing, typically ranging from a few thousand to tens of thousands of dollars, depending on the machine’s configuration. To select a cost-effective laser cleaning machine, it’s essential to base the choice on specific cleaning needs and production requirements. Conducting thorough research on brands, models, and configurations ensures the selected machine meets operational demands while maximizing long-term productivity.
Steps to Choose the Best Laser Cleaning Machine
- Define Your Needs
Determine the material, size, contamination type, and cleaning frequency of your target objects. These factors will directly influence the required technical specifications of the machine.
- Evaluate Performance Parameters
Pay attention to key specifications such as laser power, scanning speed, and minimum focal spot diameter, as these significantly impact cleaning efficiency and effectiveness.
- Consider Additional Features
High-end models may offer features like automated loading/unloading systems or remote monitoring software. While these increase upfront costs, they can improve productivity and operational control in the long run.
- Compare Brands and Services
Different brands vary in quality and after-sales support. Check user reviews and seek expert advice to assess the cost-effectiveness and service reliability of various options.
- Request a Demo or Trial
Whenever possible, arrange for a live demonstration or trial run to experience the machine’s ease of operation and actual cleaning performance. You can also send a sample for free testing if direct trials are unavailable.
By following these steps, businesses can choose a laser cleaning machine that aligns with your budget and delivers optimal results for your specific cleaning applications.

Cost-Effective Metal Cleaning Solution
While some may perceive laser cleaning machines as expensive, they are a highly cost-effective choice for large-scale industrial production and long-term investment.
High Efficiency: Laser cleaning machines can process large volumes of metal components in significantly less time compared to traditional methods, reducing production downtime.
Exceptional Cleaning Results: Their precision ensures superior cleaning quality, leaving surfaces free from contaminants without damaging the substrate.
Reduced Labor Costs: Automation and ease of operation minimize the need for extensive manual labor, leading to long-term savings on workforce expenses.
For businesses seeking to improve productivity and achieve consistent cleaning results, investing in a laser metal cleaning machine provides a practical and efficient solution that delivers lasting benefits.
Conclusion:
Laser cleaning of rust on metals offers unmatched precision, efficiency, and eco-friendly benefits, making it a superior choice for modern surface cleaning needs. If you’re looking for a dependable and innovative solution, our pulsed laser cleaning machine for metal delivers exceptional performance tailored to your needs. Contact us today to learn more about how our laser cleaning systems can optimize your processes.