Ultrafast lasers, or ultrashort pulse lasers, have rapidly advanced in recent years, especially in glass cutting, where they have shown exceptional performance. Laser micromachining plays a key role in semiconductor chip manufacturing and packaging, as well as in the circuits that connect electronic components and PCBs. The production of high-resolution display also relies on micro laser cutting machine. It is the high precision, high efficiency and excellent performance of ultrashort pulsed lasers that are behind these applications, especially in areas such as glass micro cutting. Therefore, laser cutting not only promotes the precision and efficiency of electronic product manufacturing, but also provides innovative solutions for more demanding miniaturization and fine processing.
Ultrafast laser cutting is a non-contact machining method that completely eliminates the micro-crack and debris issues commonly associated with traditional cutting methods. Laser micro-cutting can be used to manufacture components with extremely complex shapes. Compared to traditional cutting or sawing, laser micro-cutting achieves extremely narrow cutting widths or kerf widths. Since residual stresses are almost never introduced into the glass during the laser cutting process, the edge strength after cutting is typically higher, and the surface quality is superior.
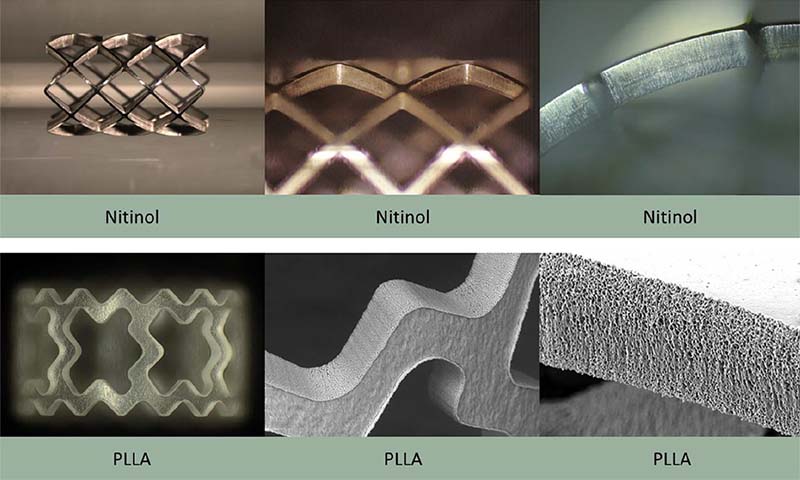
Advantages of Micro Laser Cutting Machine for Glass
Glass laser cutting technology has become an advanced solution in the glass cutting industry due to its ease of control and low pollution characteristics. When cutting at high speeds, it ensures clean, straight edges with excellent perpendicularity while significantly reducing internal damage. Particularly in high-precision cutting, picosecond ultrafast lasers offer a significant advantage due to their extremely narrow pulse widths. With their low heat diffusion properties, lasers complete the cut before heat can transfer to the surrounding material, effectively preventing thermal stress from damaging brittle materials, making it especially suitable for processing fragile materials like glass.
High Precision and Complex Shape Cutting
Ultrafast laser cutting technology guarantees that the processing does not affect surrounding materials, achieving “ultra-fine” machining results. With the increasing demand for complex curves and geometric shapes, especially in the smartphone manufacturing industry, ultrafast laser cutting technology is being widely used in high-end screen production due to its precision and efficiency, meeting the manufacturers’ needs for more intricate glass shapes.
Laser cutting in micromachining not only provides efficiency and precision but also ensures ultra-fine results during the processing, bringing revolutionary technological innovation to the glass cutting industry and pushing the sector toward higher precision and the ability to process more complex shapes.
Femtosecond Laser Glass Cutting
Femtosecond laser cutting technology, with its ultra-short pulse width and low thermal impact characteristics, has become a significant innovation in the field of glass cutting. Especially in the manufacturing of LCD screens, femtosecond lasers enable high-precision, low-damage cutting results. Traditional glass cutting methods often lead to micro-cracks, fragments, or irregular cutting edges. In contrast, femtosecond lasers, through precise control of pulses, can finely cut glass materials without inducing thermal effects. This non-contact cutting method not only enhances the cutting quality but also greatly improves production efficiency, meeting the demand for high-precision electronic products.
Glass Drilling
In glass drilling applications, femtosecond lasers also demonstrate exceptional performance. Traditional drilling methods can often cause glass cracks or surface damage, while femtosecond or picosecond lasers can precisely control pulse energy to quickly and accurately drill holes in glass, while minimizing the heat-affected zone. This avoids the cracks and deformations caused by thermal conduction. Whether it’s tiny diameters or complex-shaped holes, femtosecond lasers maintain high precision and quality throughout the process.
Glass Engraving
The use of femtosecond laser technology in glass engraving is becoming increasingly widespread. Compared to traditional engraving techniques, femtosecond lasers can achieve finer patterns and more complex markings. By heating the glass locally to its evaporation temperature in an extremely short period, the laser creates intricate designs or text, avoiding material deformation or damage caused by overheating. Femtosecond laser engraving is not only suitable for flat designs but also for micro and nano engraving on curved surfaces or ultra-thin glass.
Brittle Material Cutting
Femtosecond lasers also demonstrate unique advantages when cutting brittle materials. Traditional cutting techniques often lead to cracks and irregular cutting edges in brittle materials like glass, ceramics, or stone. However, femtosecond lasers, with their ultra-short pulse durations and low heat diffusion properties, can heat the material to its evaporation temperature and cut it in an extremely short time, preventing thermal stress caused by heat conduction. This ensures cutting precision and preserves the integrity of the material. This technology is particularly well-suited for high-precision cutting of brittle materials such as smartphone screens, automotive glass, and optical glass, significantly improving production efficiency while maintaining cutting quality.
Glass Laser Cutting Machine Price
The price can vary significantly based on the type of laser technology used (e.g., femtosecond, picosecond, or CO2 lasers). Femtosecond laser cutting machines, for example, tend to be higher in price due to their ultra-short pulse widths and superior precision, which are ideal for cutting delicate materials like glass, ceramics, and semiconductors. The cost of a glass laser cutting machine may also depend on additional features like automation, accessories, fixture, and the complexity of the control systems. While the initial investment can be substantial, the efficiency, precision, and reduced waste associated with ultrafast laser cutting often lead to long-term cost savings.
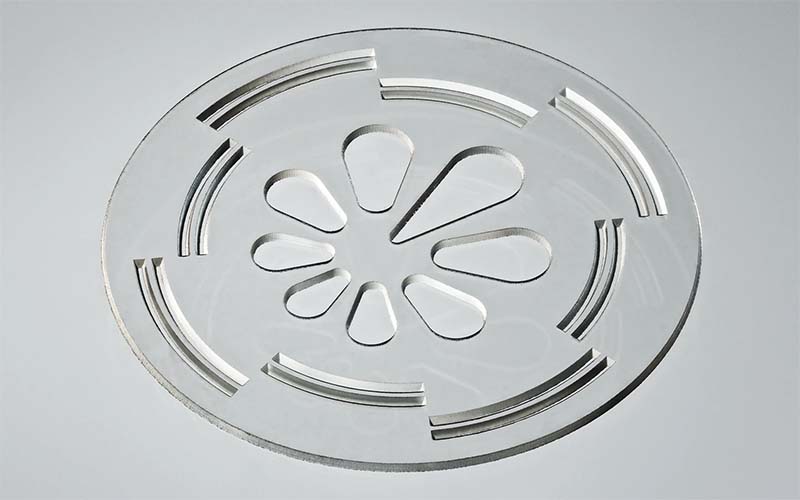
Femtosecond Laser Micromachining System
The femtosecond laser cutting machine utilizes femtosecond lasers as its core cutting tool, with laser pulse widths that are extremely short, typically in the femtosecond ((10^(-15)) seconds) range. These ultra-short pulses can heat materials to their evaporation temperature in an extremely brief period, enabling precise cutting without direct contact with the material. The high energy density and ultra-short pulse duration of femtosecond lasers ensure that they can perform precise cuts on materials such as metals, ceramics, glass, and polymers without creating a heat-affected zone.
Due to their ultra-short pulse width and exceptionally high peak power, femtosecond lasers enable high-precision micro-nano machining. Femtosecond laser micromachining offers advantages such as high processing accuracy, minimal thermal effects, low damage thresholds, and the ability to create true three-dimensional microstructures. In specific research applications, the precision of femtosecond laser processing can reach the nanometer level. For example, when machining non-metallic vascular stents, experiments have demonstrated that femtosecond laser cutting can achieve high-precision results. These precision capabilities make femtosecond laser cutting technology highly promising in fields such as precision manufacturing, biomedical applications, and micro-nano electronics.
Higher Precision: Femtosecond laser pulses have an extremely short duration, reaching the femtosecond scale (10^-15 seconds). This allows femtosecond lasers to achieve an extremely small heat-affected zone during the cutting process, thereby enhancing cutting precision and quality.
Reduced Material Damage: Due to the ultra-short pulse width and high energy density of femtosecond lasers, they can cut materials without significantly heating them, minimizing thermal damage to the material’s microstructure.
Suitability for a Wider Range of Materials: Femtosecond laser cutting technology can process materials with varying degrees of hardness, including those that are heat-sensitive or prone to deformation, such as glass, ceramics, and certain metal alloys.
Reduced Post-Processing: Since the edge quality produced by femtosecond laser cutting is generally high, there is often no need for additional polishing or cleaning steps. This reduces both production costs and time.
Micro-Nano Machining Capability: Femtosecond laser cutting technology has a significant advantage in the field of precision micro-nano machining, capable of achieving fine processing at the micrometer and even nanometer scale. This allows for the creation of intricate and highly detailed structures that would be challenging or impossible to achieve using traditional machining methods.
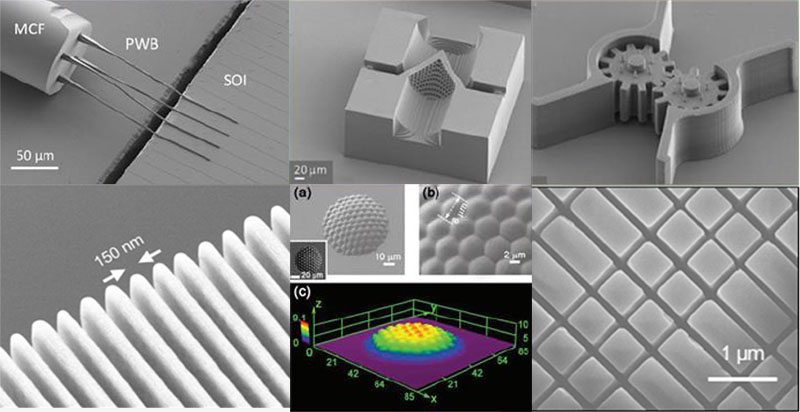
Dapeng Professional Femtosecond Laser Micromachining Machine
Femtosecond laser micromachining can be used for cutting, drilling, marking, texturing, removal, or surface engraving. It is one of the main methods used in micro-machining of transparent materials, with the structures produced (such as holes, grooves, or shapes) ranging from a few microns to a few millimeters. This technology is suitable for processing fine features in any type of material, including very hard and brittle substances. The DPLASER femtosecond laser engraving & cutting machine is ideal for small-batch micro-machining tasks. With advanced galvanometer scanners for high-speed scanning, it achieves rapid marking and cutting. The system can be customized based on specific application needs, offering various capacities to ensure versatility and adaptability to meet the demands of different users.
Applications of Femtosecond Laser Micromachining Systems
- Ultrafast laser ablation
- Cutting and drilling of brittle, fragile materials
- Touchscreen glass and ITO cutting
- Surface treatment and 3D structure creation
- Ultra-precise drilling and cutting
Materials Suitable for Laser Micromachining: Polymers, optical materials, metals, ceramics, glass and quartz, thin films, silicon, composite materials.
High Efficiency Cutting
Compared to traditional cutting equipment, the femtosecond laser cutting machine significantly improves work efficiency. With the high energy density and rapid pulse characteristics of femtosecond lasers, it can quickly complete material cutting, greatly reducing production cycles. Additionally, femtosecond laser cutting machines are often equipped with advanced CNC systems, supporting automated programming and efficient processing, further enhancing production efficiency.
Intelligent Operation
The operation interface of the femtosecond laser marking & cutting machine is highly user-friendly, allowing users to easily complete complex cutting tasks with simple operations. Modern femtosecond laser cutting machines also support remote control and IoT technologies, enabling users to monitor the cutting process in real-time through their phones or computers, adjust parameters, and perform remote operation and management.
Environmentally Friendly and Energy-Efficient
Femtosecond laser cutting machines do not emit harmful gases or waste liquids during operation, making their environmental impact minimal. Furthermore, with efficient energy utilization, these machines effectively reduce energy consumption, promoting green and sustainable production.
Wide Application
Due to their outstanding cutting performance and high efficiency, femtosecond laser cutting machines have been widely applied in industries such as display screens, semiconductor chips, MEMS/NEMS, nano-materials, biomaterials, and sapphire cutting and drilling. In these industries, femtosecond laser cutting machines, with their precision and efficiency, have become indispensable tools in both manufacturing and research and development processes.
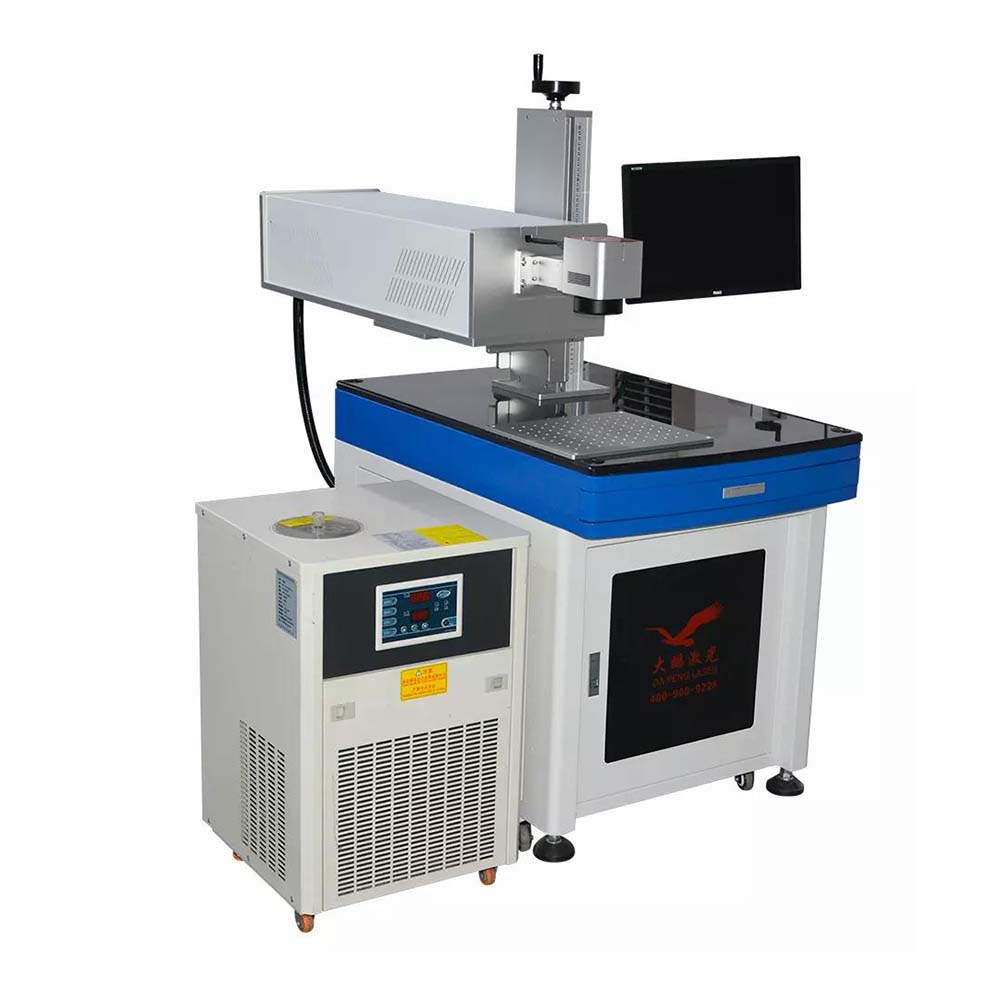
Infrared Picosecond Laser Cutting
Infrared picosecond laser cutting machines utilize lasers with infrared wavelengths and pulse durations in the picosecond range. Compared to nanosecond lasers, the main advantage of picosecond lasers lies in their shorter pulse widths, which enable them to transfer energy to the material in a shorter time, thus reducing the thermal impact on the material. This “cold processing” feature is crucial for preserving the physical and chemical properties of materials, especially in high-precision, high-quality applications. For example, in the production of high-end automotive windshields, picosecond laser cutting enables precise cutting of complex shapes while avoiding thermal damage to the glass, maintaining its original strength and transparency.
Infrared Femtosecond Laser Cutting
Infrared femtosecond laser cutting machines use lasers with infrared wavelengths and pulse durations in the femtosecond range. Femtosecond lasers are among the most advanced laser cutting technologies available, with the advantage of extreme short pulses and high energy. Femtosecond lasers can achieve precise cuts on glass without introducing any thermal impact. This “cold processing” technology is revolutionary for materials that are highly sensitive to heat. For instance, when producing solar panels, femtosecond lasers can cut silicon wafers without causing thermal damage, enhancing the efficiency and lifespan of the solar cells.
Both infrared picosecond and femtosecond laser cutting machines have unique advantages. Picosecond lasers are ideal for applications that require high precision and quality, while femtosecond lasers are perfect for processing materials that are extremely sensitive to thermal effects.
Summary
Micro laser cutting machine for glass using femtosecond lasers, with their ultra-short pulse widths, offer exceptional precision, minimal thermal impact, and the ability to preserve the material’s original properties, providing a revolutionary solution for precision machining. Their “cold processing” capability makes them especially suitable for cutting brittle materials like glass and ceramics, as well as thin films, semiconductors, and ultra-thin materials. These technologies have advanced high-end manufacturing and opened new opportunities in fields such as biomedical, microelectronics, solar energy, and precision instruments. Moving forward, femtosecond and picosecond laser cutting technologies will continue to deliver higher efficiency, precision, and cost-effective solutions, driving the progress of smarter and more sustainable manufacturing.