In modern manufacturing, laser welding has become a widely adopted technology due to its precision, speed, and adaptability to complex materials. However, one of the most critical concerns for engineers and manufacturers alike is ensuring the strength and reliability of laser welds. This article will provide a professional explanation of how to increase welding strength, covering technical principles, welding quality control, and real application cases.
Features of Laser Welding
- Minimal Thermal Deformation
One of the most notable advantages of laser welding is its exceptionally low thermal deformation. Thanks to the laser beam’s ability to be precisely focused on a very small area, the heat input is minimal. This significantly reduces the risk of warping or structural distortion in the surrounding regions of the workpiece, helping maintain the geometric stability and dimensional consistency of welded components.
- High Processing Efficiency
Laser welding offers outstanding productivity due to its fast processing speed and high degree of automation. It is particularly well-suited for continuous, repetitive production tasks, enabling shorter production cycles and higher output per unit time. This makes it ideal for industrial-scale, mass manufacturing.
- Superior Weld Quality
Compared to traditional welding methods, laser welding typically produces finer, cleaner weld seams with smooth surfaces and minimal spatter, greatly reducing the need for post-processing. The resulting welds are strong and stable, meeting stringent reliability standards required in high-performance applications.
- Excellent Environmental Performance
The laser welding process generates less smoke, fumes, and waste gases, and offers higher energy efficiency, which collectively reduce environmental impact. Additionally, its precision minimizes material waste, contributing to more sustainable manufacturing.
- Long-Term Cost Efficiency
While the initial investment in laser welding equipment may be relatively high, its exceptional speed, precision, and weld durability greatly reduce downstream costs such as post-processing, maintenance, and rework. In large-scale production, laser welding delivers a clear advantage in overall cost control and long-term economic efficiency.
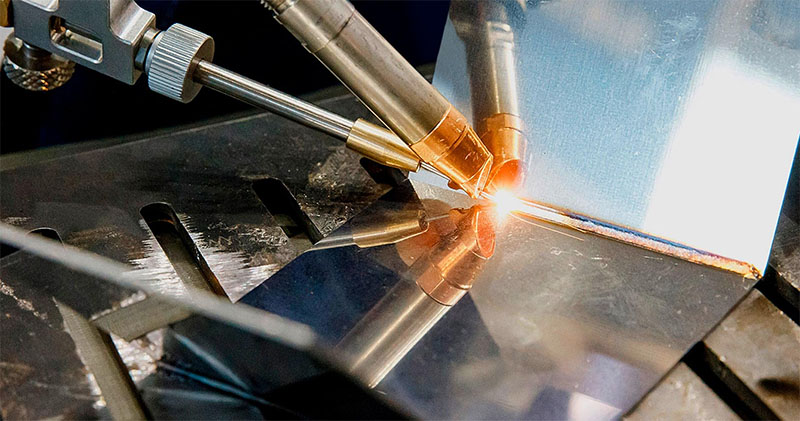
Factors Affecting the Strength of Laser Welding
Laser welding employs a high-energy-density laser beam directed at the surface of the workpiece, rapidly melting localized material to form a molten pool. Upon cooling, this results in a strong metallurgical bond between the materials. The strength of laser-welded joints is primarily influenced by the following factors:
1. High Energy Concentration
Laser beams can be tightly focused, delivering a high energy density within a very small area. This enables the formation of deep and narrow welds that promote effective metallurgical bonding, significantly enhancing the mechanical strength of the joint.
2. Narrow Heat-Affected Zone (HAZ)
Compared to traditional welding techniques, laser welding introduces less overall heat, resulting in a much narrower heat-affected zone—typically within 0.1 to 0.5 mm. This minimizes residual stresses and material deformation, helping maintain the structural integrity and strength of the welded component.
3. Favorable Metallurgical Reactions
The rapid heating and cooling rates characteristic of laser welding encourage the formation of fine, uniform grain structures within the weld zone. This microstructural refinement helps suppress defects such as porosity and cracking, thereby improving the strength and reliability of the welded joint.
Laser Welding Strength vs. Electric Arc Welding Strength
How strong is laser welding compared to electric arc welding? While both methods are widely used across various industries, they differ significantly in terms of heat input, weld precision, and mechanical performance.
Strength Performance of Laser Welding
Laser welding systems use highly focused laser beams—typically ranging from 1~10 kW in power—with energy densities exceeding 10⁶ W/cm². This allows the formation of deep, narrow welds with high aspect ratios. According to the American Welding Society (AWS), laser-welded joints can achieve tensile strengths in the range of 500–700 MPa, making them especially suitable for high-strength steels, aluminum alloys, and other demanding materials. For example, in the automotive industry, laser welds have demonstrated 20%–30% higher tensile strength compared to conventional arc welds.
Strength of Electric Arc Welding
Processes such as Shielded Metal Arc Welding (SMAW) and MIG/MAG welding rely on electric arcs to melt the base metal, typically delivering energy densities around 10³ W/cm². As a result, their weld strength usually falls within the 300–500 MPa range, depending on factors such as electrode type, filler material, and welding parameters.
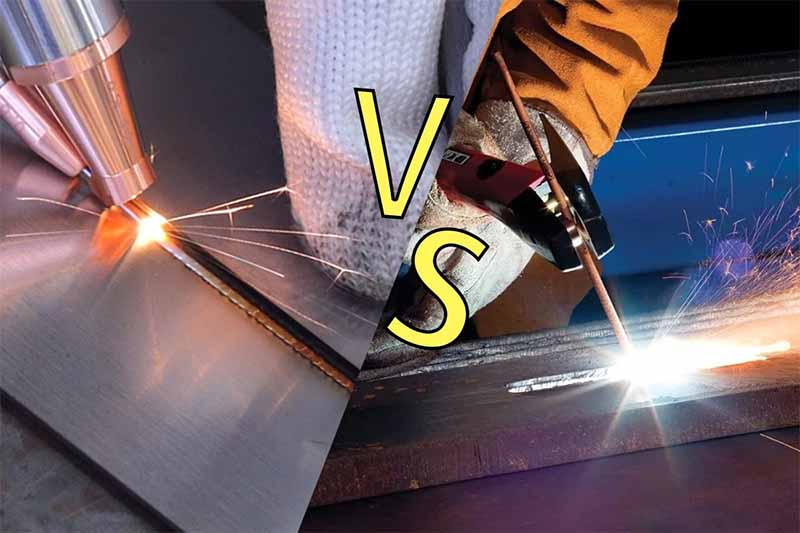
Is Laser Welding Stronger than MIG or TIG Welding?
The answer is yes. During the heating process, laser welding concentrates energy directly on the metal fusion zone, resulting in minimal thermal impact on the surrounding material. In contrast, MIG welding—and especially TIG welding—tends to introduce more heat into the heat-affected zone (HAZ), causing a wider spread of thermal energy. The more heat that dissipates into the HAZ, the greater the risk of microstructural changes and embrittlement in that area, particularly with heat-sensitive metals. In general, lower heat input leads to better weld joint quality and performance.
Speed
Laser welding operates at significantly higher speeds—approximately four times faster than TIG welding and about twice as fast as MIG welding. Its high energy density allows for rapid melting, making it especially efficient for welding thin metals.
Material Thickness
Laser welding is best suited for thin to medium-thickness sheets, but has limitations when it comes to welding thicker materials. On the other hand, arc welding techniques like MIG and TIG offer better adaptability for thicker sections. Therefore, weld strength depends not only on the welding method but also on the material type, thickness, and the specific application environment.
Application
In most thin-sheet metal applications, laser welding often outperforms traditional arc welding techniques due to its superior precision, strength, and weld quality. It is ideal for industries requiring high-quality joints, such as precision metal fabrication and parts manufacturing. Meanwhile, conventional arc welding remains widely used in sectors like automotive, construction, and machinery manufacturing, where high-volume production and cost efficiency are key considerations.
What Thickness Can Laser Welding for?
The thickness range that laser welding can effectively process generally varies from 0.1 mm up to about 8 mm, depending on the material type. Factors such as laser power, focal length, and spot size also significantly influence penetration capability. Below are typical average thicknesses that laser welding machines (with power around 1000 to 1500 watts) can weld for common materials:
Iron: 4–5 mm
Aluminum: 3–5 mm
Brass: 5–6 mm
Carbon Steel: 4–5 mm
Stainless Steel: 4–5 mm

How to Improve the Laser Welding Strength?
Material Compatibility:
Choosing filler materials that match the base metal is crucial for ensuring strong welds. Mismatched fillers can cause weak joints, cracking, or corrosion. Whether welding stainless steel, aluminum alloys, titanium alloys, or other materials, laser welding can achieve excellent joint strength. Laser welding machines can adapt to different metals by adjusting parameters such as laser power and pulse frequency to accommodate varying melting points, thermal conductivity, and other physical properties, ensuring a robust weld.
Surface Preparation:
Before welding, thoroughly clean the material surfaces to remove oils, contaminants, and oxides that could compromise weld strength and quality.
Optimizing Laser Welding Parameters:
Precisely controlling laser power, welding speed, and focal position ensures a stable welding process, minimizes thermal impact, and improves weld quality.
Securing the Workpiece:
Any vibration or movement during welding can negatively affect the weld formation. It is essential to firmly fix the workpiece on the welding table.
Controlling Welding Speed:
Longer interaction between the laser and the workpiece allows more complete welding. An appropriate welding speed helps distribute stress evenly across the weld, ensuring solid joints.
Use of Shielding Gases:
Applying suitable shielding gases like argon or nitrogen effectively removes oxides from the weld zone, protects the weld pool, and enhances weld strength.
Post-Weld Treatments:
Post-processing methods reduce residual stresses and structural defects in the weld, improving strength and toughness. Common treatments include annealing, aging, normalizing, tempering, and solution treatment.
Advanced Laser Welding Equipment:
Modern laser welding machines provide precise parameter control, increasing consistency and reducing defects. The growing use of automated and robotic welding systems in industry boosts productivity and ensures consistent weld quality.
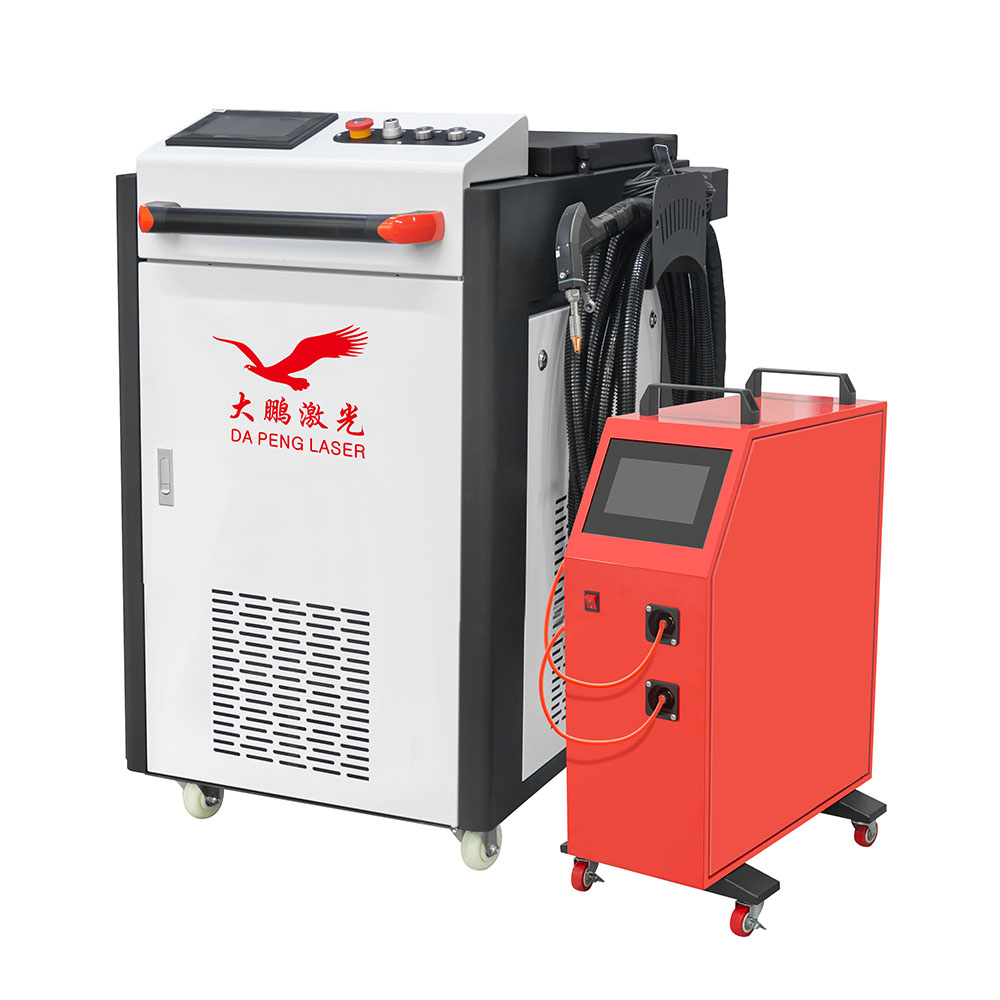
Welder Training:
Proper training ensures welders master best practices, safety standards, and advanced welding techniques. Companies should invest in continuous education to keep welders up to date with the latest technologies and operational methods.
Whether it is mold steel, carbon steel, stainless steel, or copper and copper alloys, aluminum alloys, magnesium alloys, and other metal materials, laser welding can achieve high-quality welds. This article aims to help readers better understand the high welding strength of laser welding machines, giving them greater confidence when selecting laser welding equipment.
With high power input and outstanding performance, laser welding machines are more powerful than MIG and TIG welding options. For manufacturers seeking to improve production and operational efficiency, it is a worthwhile investment. For superior laser welding solutions, Dapeng Laser offers laser welding machines with CE and SSG certified. By focusing on factors such as proper laser parameters, material preparation, and precise control of the welding condition, manufacturers can significantly enhance joint integrity. Understanding how to improve weld strength not only boosts product quality but also reduces defects and increases overall efficiency, making it a vital consideration in any laser welding process.